Unleashing Efficiency: How Pointed Carbide Buttons are Revolutionizing Oil & Gas Operations
In the relentless pursuit of energy resources, the oil and gas industry demands equipment that can withstand extreme pressures, abrasive formations, and demanding drilling environments. Enter pointed carbide buttons, a specialized breed of wear-resistant components engineered to deliver exceptional penetration, durability, and performance in even the most challenging oil field applications.
This comprehensive guide delves into the world of pointed carbide buttons, exploring their unique advantages, applications, and selection criteria, empowering you with the knowledge to optimize drilling operations and maximize efficiency.
The Power of Precision: Why Choose Pointed Carbide Buttons?
Beyond Standard Wear Protection: The Advantages of a Targeted Approach
Pointed carbide buttons offer distinct advantages over other wear protection solutions in oil field applications:
- Enhanced Penetration: The sharp, pointed geometry concentrates cutting forces, enabling faster drilling rates and improved efficiency, especially in hard and abrasive formations.
- Reduced Friction and Torque: The pointed shape minimizes contact area with the wellbore, reducing friction and torque, which translates to lower energy consumption and extended drill bit life.
- Improved Hole Cleaning: The pointed buttons create a channeling effect that facilitates the removal of cuttings from the wellbore, preventing bit balling and ensuring optimal drilling performance.
- Versatility in Challenging Formations: Pointed buttons excel in a variety of formations, including hard rock, shale, and sandstone, making them a versatile choice for demanding drilling operations.
Understanding Pointed Carbide Button Design and Functionality
Anatomy of a Workhorse: Key Features and Their Impact
- Point Angle: The angle of the point influences penetration rate and wear resistance. Steeper angles offer faster penetration but may sacrifice some durability, while shallower angles provide a balance of penetration and wear life.
- Button Shape: While the pointed tip is the defining feature, the overall button shape can vary. Common shapes include conical, chisel, and spear-shaped, each optimized for specific drilling conditions.
- Carbide Grade: The grade of tungsten carbide used in the button dictates its hardness, toughness, and wear resistance. Selecting the appropriate grade is crucial for maximizing button life and performance.
- Attachment Method: Pointed carbide buttons are typically attached to drill bits or other drilling tools using brazing or welding techniques, ensuring a secure bond that can withstand the rigors of downhole environments.
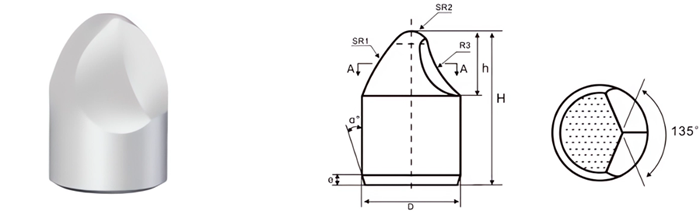
Product Information: A Closer Look at Pointed Carbide Buttons
Technical Specifications: Decoding the Details
Feature | Description |
---|---|
Type | Pointed Carbide Buttons for Oil Field Applications |
Composition | Tungsten Carbide (WC) with Cobalt (Co) or Nickel (Ni) binder |
Hardness (HV30) | Typically ranges from 1400 to 1800, depending on the carbide grade |
Transverse Rupture Strength (N/mm²) | Typically ranges from 1900 to 2600, depending on the carbide grade |
Impact Resistance | Excellent resistance to impact and shock loads encountered during drilling |
Sizes and Shapes | Available in a variety of standard and custom sizes and shapes, including conical, chisel, and spear-shaped |
Grades and Standards | Grades are available to meet specific industry standards, such as API (American Petroleum Institute) specifications for oil field drilling equipment |
Applications: Where Pointed Carbide Buttons Excel
Drilling Down to Specific Uses:
- Oil and Gas Exploration and Production: Drilling bits, core bits, hole openers, and other downhole tools used in drilling operations.
- Directional Drilling: Specialized drill bits and tools used to create deviated wellbores.
- Geothermal Drilling: Drilling equipment used to access geothermal energy resources.
- Water Well Drilling: Drill bits and tools used for water well construction.
Comparative Analysis: TRUER vs. the Competition
Market Leaders in Pointed Carbide Buttons:
Supplier | Location | Country | Price Range (per piece) | Specialties |
---|---|---|---|---|
TRUER | Shanghai, China | China | $15 – $60+ | Custom-engineered solutions, rapid prototyping, exceptional customer support |
Element Six | Global Headquarters: London, UK | UK | $20 – $75+ | Advanced material science, high-performance carbide grades |
Kennametal | Global Headquarters: Pittsburgh, PA | USA | $18 – $65+ | Wide range of standard and custom button designs, extensive industry experience |
Sandvik Coromant | Global Headquarters: Sandviken, Sweden | Sweden | $22 – $80+ | Innovative tooling solutions, focus on sustainability and performance optimization |
Note: Prices are approximate and can vary significantly based on button size, geometry, grade, quantity, and other factors.
Advantages and Limitations: A Balanced Perspective
Weighing the Pros and Cons of Pointed Carbide Buttons:
Advantages | Limitations |
---|---|
Superior penetration rates in hard and abrasive formations | Higher initial cost compared to some other wear protection solutions |
Reduced friction and torque, leading to lower energy consumption and extended drill bit life | May require specialized brazing or welding techniques for secure attachment |
Improved hole cleaning and reduced risk of bit balling | Not as versatile as some other button shapes for applications requiring a combination of cutting and scraping actions |
Beyond the Tip: Factors Influencing Pointed Button Performance
Optimizing Performance: Key Considerations
- Formation Properties: Understanding the specific characteristics of the formation being drilled, such as hardness, abrasiveness, and fracture toughness, is crucial for selecting the optimal button geometry and grade.
- Drilling Parameters: Factors like weight on bit (WOB), rotary speed (RPM), and drilling fluid properties can significantly influence button wear rates and overall drilling performance.
- Button Inspection and Replacement: Regular inspection of pointed carbide buttons is essential to identify wear or damage and ensure timely replacement, preventing costly downtime and potential drilling problems.
Why Choose TRUER?
Your Partner in Precision and Performance:
At TRUER, we’re not just manufacturing carbide buttons; we’re engineering solutions. Here’s why leading companies in the oil and gas industry trust TRUER:
- Unwavering Commitment to Quality: We use only the highest-grade tungsten carbide and employ rigorous quality control measures throughout our manufacturing process.
- Customization Expertise: Our team of engineers excels at designing and manufacturing custom pointed carbide button solutions tailored to your specific drilling challenges.
- Rapid Prototyping and Production: We understand the importance of speed in the oil field. Our streamlined processes enable us to deliver prototypes and production runs quickly and efficiently.
- Exceptional Customer Support: We’re with you every step of the way, providing expert technical guidance and support to ensure your success.
Frequently Asked Questions: Addressing Your Pointed Inquiries
1. How do I choose the right point angle for my pointed carbide buttons?
The optimal point angle depends on the balance you need between penetration rate and wear resistance. Steeper angles (e.g., 110 degrees) are better for soft formations, while shallower angles (e.g., 60 degrees) are more suitable for hard, abrasive formations.
2. What are the key factors that influence the lifespan of pointed carbide buttons?
Button lifespan is affected by factors such as carbide grade, formation properties, drilling parameters, and the quality of the attachment method.
3. Can TRUER provide pointed carbide buttons with wear-resistant coatings?
Yes, we offer a range of surface treatments and coatings that can further enhance the wear and corrosion resistance of our pointed carbide buttons.
4. What is the typical lead time for ordering custom pointed carbide buttons from TRUER?
Lead times for custom orders vary depending on the complexity of the design and the quantity required. Contact our sales team for a personalized quote and lead time estimate.For more information, please contact here.
5. Does TRUER offer technical support to help optimize drilling performance with your pointed carbide buttons?
Absolutely! Our team of technical experts is available to provide guidance on button selection, drilling parameter optimization, and troubleshooting any drilling challenges you may encounter.