Introduction: Mastering the Art of Controlled Material Removal
In the realm of machining, where precision reigns supreme, inserts for parting and grooving turning stand as indispensable tools for achieving clean, accurate cuts. From separating finished components to creating intricate grooves, these specialized inserts empower machinists to shape metal with unparalleled control. This comprehensive guide delves into the intricacies of parting and grooving inserts, exploring their diverse applications, unraveling their design complexities, and equipping machinists with the knowledge to achieve exceptional results.
Parting and Grooving Inserts: Essential Tools for Precision Machining
What are Parting and Grooving Inserts?
Parting and grooving inserts are indexable cutting tools specifically engineered for creating narrow, deep cuts in turning operations. Unlike general-purpose turning inserts, these specialized tools feature geometries optimized for efficient chip evacuation and superior surface finish in confined spaces. While often used interchangeably, the terms “parting” and “grooving” denote distinct applications:
- Parting: Refers to completely separating a workpiece into two or more pieces.
- Grooving: Encompasses creating various types of grooves, such as O-ring grooves, snap ring grooves, and thread relief grooves.
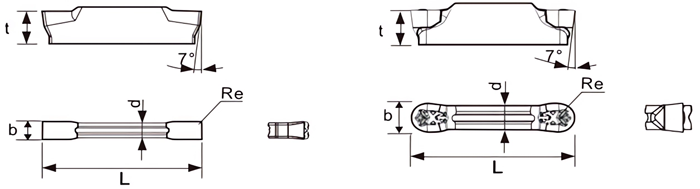
The Mechanics of Precision Cutting:
Parting and grooving inserts achieve their remarkable precision through a combination of factors:
- Sharp Cutting Edges: These inserts boast sharp, precisely ground cutting edges that efficiently shear material, minimizing cutting forces and reducing the risk of work hardening.
- Positive Rake Angles: Positive rake angles promote a slicing action, further reducing cutting forces and enhancing chip flow, crucial in narrow grooves where chip evacuation is paramount.
- Chipbreaker Geometries: Specialized chipbreakers, often featuring intricate geometries, effectively break chips into manageable sizes, preventing chip clogging and ensuring a smooth surface finish.
- Coolant Delivery: Many parting and grooving inserts incorporate internal coolant channels that direct coolant precisely to the cutting zone, enhancing chip evacuation, reducing heat generation, and extending tool life.
A World of Variety: Types of Parting and Grooving Inserts:
Navigating the diverse landscape of parting and grooving inserts can seem daunting, but understanding the key types empowers machinists to select the optimal tool for the task at hand:
- Full-Width Inserts: As the name suggests, these inserts span the entire width of the groove or parting cut. They offer high rigidity and are ideal for heavy-duty parting operations or creating wide grooves.
- Partial-Width Inserts: These inserts feature a cutting width narrower than the desired groove or parting width. They excel in creating narrow grooves, performing deep parting cuts, and machining delicate workpieces where rigidity is paramount.
- Double-Ended Inserts: Featuring cutting edges on both ends, these inserts offer exceptional economy, allowing for twice the cutting before indexing is required.
- Specialty Inserts: The world of parting and grooving inserts extends beyond the ordinary. Specialty inserts cater to specific applications, such as creating intricate profiles, machining difficult-to-cut materials, or producing ultra-fine surface finishes.
Deciphering the ISO Classification System: Matching Inserts to Materials:
Just like their threading counterparts, parting and grooving inserts adhere to the ISO classification system, providing a standardized framework for selecting the appropriate carbide grade based on the material being machined:
Application Group | Description |
---|---|
P | Designed for machining steel, steel castings, and materials known for producing long, continuous chips. |
M | Engineered to tackle the challenges of stainless steels, high-temperature alloys, and other materials that tend to be more difficult to machine, requiring enhanced heat and wear resistance. |
K | The go-to choice for taming cast iron, non-ferrous metals, and non-metallic materials, offering a balance of hardness and toughness to handle these diverse materials. |
The Importance of Tool Holding: A Solid Foundation for Success:
Achieving optimal results with parting and grooving inserts goes beyond selecting the right insert; it requires a robust and precise tool holding system:
- Rigidity is Key: Parting and grooving operations generate significant cutting forces, making rigidity paramount. Choose tool holders with minimal overhang and ensure a secure connection to the tool post or turret.
- Accurate Clamping: Proper insert clamping is crucial for preventing insert movement or chatter during machining. Utilize tool holders with secure clamping mechanisms and follow manufacturer recommendations for clamping torque.
- Coolant Delivery: Tool holders with internal coolant channels enhance chip evacuation and tool life, particularly in demanding applications.
Applications Across Industries: Where Precision Meets Versatility:
Parting and grooving inserts are the unsung heroes behind countless machined components across a wide range of industries:
- Automotive: From engine crankshafts and camshafts to transmission gears and axle components, these inserts play a vital role in creating precise grooves and separating finished parts, contributing to the performance and reliability of vehicles.
- Aerospace: The aerospace industry demands lightweight yet incredibly strong components. Parting and grooving inserts are instrumental in machining intricate grooves in landing gear components, turbine engine parts, and structural elements.
- Medical Devices: When precision and biocompatibility are paramount, these inserts excel in machining medical implants, surgical instruments, and diagnostic equipment, creating precise grooves and ensuring the integrity of critical components.
- Oil and Gas: Extracting and transporting oil and gas require robust equipment capable of withstanding extreme pressures and corrosive environments. Parting and grooving inserts contribute to the manufacturing of valves, pipes, and drilling equipment, ensuring reliable performance in demanding conditions.
- General Manufacturing: From simple shafts and gears to complex molds and dies, these versatile inserts find applications in countless manufacturing processes, enabling the creation of a wide array of components.
Weighing the Pros and Cons: Advantages and Limitations of Parting and Grooving Inserts:
Advantages | Limitations |
---|---|
Precision and Accuracy: Parting and grooving inserts excel at creating precise grooves and parting cuts with tight tolerances, meeting the stringent demands of various industries. | Tool Deflection: Due to the nature of the cut, parting and grooving operations are susceptible to tool deflection, particularly when using narrow inserts or machining deep grooves. Selecting rigid tool holders and optimizing cutting parameters is crucial. |
Excellent Surface Finish: Sharp cutting edges, positive rake angles, and effective chipbreakers contribute to achieving superior surface finishes, often eliminating the need for secondary finishing operations. | Chip Evacuation: Efficient chip evacuation is paramount, especially in deep grooves or when parting off large diameters. Proper chipbreaker selection, coolant delivery, and cutting parameter optimization are essential for preventing chip clogging. |
Versatility: Available in a wide range of sizes, geometries, and materials, parting and grooving inserts offer exceptional versatility in tackling diverse grooving and parting applications. | Tool Breakage: Parting and grooving inserts can be prone to breakage if subjected to excessive cutting forces, improper clamping, or if the insert is not properly supported. Choosing the right insert geometry, tool holder, and cutting parameters is crucial for maximizing tool life. |
Cost-Effectiveness: While the initial investment in parting and grooving inserts can be higher than some other tooling options, their extended tool life and ability to produce high-quality parts often result in lower overall machining costs. |
Frequently Asked Questions: Addressing Your Parting and Grooving Insert Queries:
1. How do I choose the right parting and grooving insert for my application?
Selecting the optimal insert involves considering several factors:
- Groove or Parting Width: Determine the required groove width or parting off diameter.
- Groove Depth: Specify the desired groove depth or parting off length.
- Material: Identify the material being machined, as different materials require inserts with specific carbide grades and coatings.
- Surface Finish Requirements: Define the required surface finish, as this will influence the choice of insert geometry and grade.
- Machine Tool Capabilities: Consider the capabilities of your lathe or turning center, including spindle speed, feed rate, and rigidity.
2. What are the key considerations for preventing tool deflection in parting and grooving operations?
Minimizing tool deflection is crucial for achieving accurate cuts and preventing tool breakage:
- Insert Width: Choose the widest insert possible that still meets the groove or parting width requirements.
- Tool Holder Rigidity: Select a tool holder with minimal overhang and ensure a secure connection to the tool post or turret.
- Cutting Parameters: Optimize cutting speeds, feed rates, and depths of cut to minimize cutting forces and reduce deflection.
- Workpiece Support: Provide adequate workpiece support, especially for long or slender parts, to minimize vibration and deflection.
3. How can I improve chip evacuation when performing deep grooving or parting off operations?
Efficient chip evacuation is essential for preventing chip clogging and ensuring a smooth surface finish:
- Chipbreaker Selection: Choose inserts with chipbreakers specifically designed for deep grooving or parting off operations.
- Coolant Delivery: Utilize tool holders with internal coolant channels and ensure adequate coolant flow and pressure.
- High-Pressure Coolant: Consider using high-pressure coolant systems for improved chip removal in challenging applications.
- Cutting Parameters: Optimize cutting speeds, feed rates, and depths of cut to promote favorable chip formation and evacuation.
4. What are the advantages of using coated parting and grooving inserts?
Coatings offer significant benefits in parting and grooving operations:
- Increased Wear Resistance: Coatings protect the insert from abrasive wear, extending tool life.
- Enhanced Hardness: Coatings increase surface hardness, allowing for higher cutting speeds and improved resistance to wear.
- Improved Lubricity: Some coatings exhibit lubricating properties, reducing friction and heat generation, leading to smoother cutting action and improved surface finish.
- Oxidation Resistance: Coatings can enhance the insert’s resistance to oxidation at elevated temperatures, particularly beneficial when machining at higher speeds or with difficult-to-cut materials.
5. How do I properly index a parting and grooving insert to expose a fresh cutting edge?
Indexing procedures may vary slightly depending on the insert design, so always refer to the manufacturer’s instructions:
- Loosen the Clamp: Use the provided wrench to loosen the insert clamp, taking care not to apply excessive force.
- Rotate or Replace the Insert: Rotate double-ended inserts to expose the fresh cutting edge. For single-ended inserts, replace the insert with a new one.
- Securely Clamp: Tighten the insert clamp securely, ensuring the insert is firmly seated and cannot move during machining.
- Verify Alignment: Before resuming machining operations, double-check the insert’s alignment to prevent any potential issues with groove or parting quality or tool breakage.
Want to buy a great quality Carbide Insert at the right price? Click here.