Carbide flat blanks are an important material used across several industries for machining and tooling applications. This guide provides a comprehensive overview of carbide flat blanks covering composition, properties, manufacturing, sizes, grades, standards, applications, suppliers, costs, pros and cons, and other key details.
Overview of Carbide Flat Blanks
Carbide flat blanks refer to pieces of carbide material shaped into flat squares, rectangles, or disks that serve as a starting workpiece for machining. Carbide’s high hardness, wear resistance, and strength make it an ideal material for cutting tools, dies, machine parts and other applications requiring durability under extreme conditions.
Carbide blanks allow machinists to grind, hone, and machine the carbide into a custom tool, mold, or die design. The machined carbide piece can then be attached to a tool body or base material. Having standardized carbide blanks available simplifies the manufacturing process compared to fabricating the carbide shape from scratch.
Carbide flats provide a uniform workpiece with tight tolerances on dimensions like thickness and flatness. Consistent blanks enable the creation of precision carbide tools and dies within fine specifications.
The main factors influencing the selection of a carbide flat blank include:
- Composition (binder type and carbide grains)
- Grade (hardness and toughness)
- Grain size
- Purity
- Tolerances
- Coatings
- Dimensions and thickness
- Surface finish
- Cost
This guide covers the key properties, specifications, and applications of carbide flat blanks. We’ve compiled the details into easy-to-find tables and sections to compare different blank options. Use the information below to select the optimal carbide flat blank for your manufacturing needs.
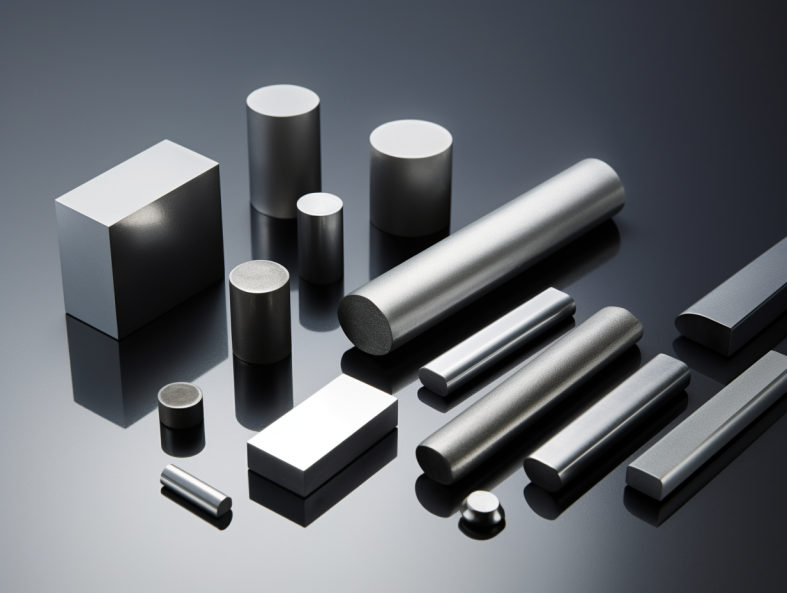
Composition of Carbide Flat Blanks
Carbide blanks consist of a carbide compound along with a metallic binder. Hard carbide grains provide wear resistance while the binder acts as a matrix to hold the grains together. The composition determines the ultimate properties and performance.
Carbide Compounds
Several carbide compounds are used to produce blanks. The most common are:
Carbide Type | Formula | Properties |
---|---|---|
Tungsten carbide | WC | Highest hardness and wear resistance |
Tantalum carbide | TaC | High hardness at high temperatures |
Titanium carbide | TiC | High strength and fracture toughness |
Silicon carbide | SiC | High thermal conductivity |
Tungsten carbide is most widely used due to its exceptional hardness, making it ideal for hard machining applications. Advanced grades may combine multiple carbide compounds to optimize properties.
Binders
The binder type affects strength, toughness, and high-temperature behavior. Common binders include:
Binder Type | Composition | Characteristics |
---|---|---|
Cobalt | Co | Most common, provides strength and toughness |
Nickel | Ni | Higher toughness than cobalt |
Chrome | Cr | Added for corrosion resistance |
Tantalum | Ta | Improves high temperature hardness |
Niobium | Nb | Increases fracture resistance |
Cobalt is the most popular binder material for its combination of strength, toughness, and corrosion resistance. Nickel binder is added when increased fracture toughness is needed. Other elements enhance specific qualities.
Properties of Carbide Flat Blanks
Carbide blank properties depend on the carbide grains, binder, manufacturing method, and other parameters. Here are the key characteristics considered when selecting a grade:
Property | Description | Factors |
---|---|---|
Hardness | Resistance to deforming, abrasion, cutting | Carbide type, grain size, binder |
Toughness | Ability to absorb impacts without fracturing | Binder type, grain size |
Strength | Maximum stress before failure | Carbide content, grain size |
Wear resistance | Resistance to sliding or rubbing wear | Hardness, grain size |
Thermal conductivity | Ability to conduct heat | Carbide type, purity |
Corrosion resistance | Resistance to environmental damage | Binder composition, coatings |
Hardness, wear resistance, and fracture toughness are critical for cutting tools and dies. Thermal conductivity is also important for removing heat from cutting edges. Specific grades balance these properties for an application.
Manufacturing of Carbide Flat Blanks
Carbide blank production involves carefully controlled processes to achieve precise material properties. Here are the key steps:
Manufacturing Stage | Description |
---|---|
Milling and blending | Measured quantities of carbide powder and binder are milled into a homogeneous mixture. |
Compacting | The powder is compacted into a “green” form using presses up to 4,000 psi. |
Sintering | Green forms are heated in a vacuum furnace to fuse grains via sintering. This densifies the structure. |
Grinding | The sintered blank is precision ground to tight tolerances on thickness, flatness, surface finish and dimensions. |
Edge preparation | Edges are chamfered, beveled, or rounded to protect cutting edges. |
Coating | PVD, CVD and other coatings are often applied to enhance wear resistance or lubricity. |
Final inspection | Detailed checks verify that the blanks meet all specifications. |
Precision at every step ensures the creation of a dense, uniform microstructure with controlled carbide grain size and consistent properties.
Grades of Carbide Flat Blanks
Grades categorize blanks by hardness, toughness, and high-temperature behavior according to standardized systems. The most common are:
Grade System | Details |
---|---|
C Grades | Two digit C system ranging from C1 to C8. Higher numbers indicate higher hardness and lower toughness. |
P Grades | Assigned based on composition and grain size. P01 is coarse while P50 is ultra-fine. |
M Grades | Developed for mining buttons. M10 is coarse while M40 has fine grains. |
K Grades | Denotes cobalt binder content from K05 to K40. Higher numbers have more cobalt. |
Within each system, the higher the number, the smaller the grain size and the harder and more wear resistant the grade. Hard grades cut faster but are britel. Tougher grades withstand shocks better.
Coating, binders, grain size, and other variables also affect grade properties. Custom or proprietary grades are available combining ideal attributes.
Grain Sizes of Carbide Blanks
Grain size refers to the average tungsten carbide particle size in the microstructure. It significantly influences blank properties and performance. Standard grain sizes are:
Grain Size | Micrometer Range | Characteristics |
---|---|---|
Ultra-fine | <0.5 μm | Highest hardness and wear resistance |
Submicron | 0.5 – 1 μm | Very hard with good strength |
Fine | 1 – 2 μm | Hard and strong for general use |
Medium | 2 – 4 μm | Tougher with higher impact resistance |
Coarse | 4 – 8 μm | Greatest toughness and fracture resistance |
Extra coarse | >8 μm | Best resistance to abusive impacts |
Finer grain sizes increase hardness and wear properties. Coarser grains improve toughness and ability to withstand forces without chipping. Ultra-fine and submicron grains are best for low force precision machining.
Dimensions of Carbide Flat Blanks
Carbide blanks are produced in standard sizes or cut to specified dimensions. Typical sizes are:
Shape | Common Dimensions | |
---|---|---|
Squares | 1/2″, 3/4″, 1″, 1-1/4″, 1-1/2″ | |
Rectangles | 1/2″ x 1″, 3/4″ x 1-1/2″, 1″ x 2″, 1-1/4″ x 3″ | |
Discs/Washers | 1/2″ OD x 1/4″ ID, 1″ OD x 1/2″ ID, 2″ OD x 1″ ID | |
Custom sizes | Up to 8” x 8” available |
Thickness is usually 1/8”, 1/4”, or 3/8”, with 1/8” and 1/4” being common. Precise tolerances on dimensions, parallelism, flatness, and squareness are maintained. Custom blank sizes are possible.
Surface Finishes of Carbide Blanks
The surface finish, measured in Ra or RMS values, affects application performance. Common surface finishes are:
Surface Finish | Ra Range (μin) | Typical Uses |
---|---|---|
As sintered | 50 – 80 | General purpose |
Ground | 30 – 50 | Close tolerance tooling |
Lapped | 5 – 20 | Precision tooling |
Polished | 1 – 10 | Mirror finishes |
EDM | 5 – 10 | Complex geometries |
A smooth surface finish improves performance by reducing friction and adhesion in materials like aluminum. Very fine polished finishes are used when surface reflectivity is needed.
Coatings for Carbide Blanks
Applying coatings to blank surfaces improves properties like lubricity, wear resistance, corrosion protection, and insulating ability. Common carbide blank coatings include:
Coating | Composition | Benefits |
---|---|---|
TiN | Titanium nitride | General hardness, wear and corrosion resistance |
TiCN | Titanium carbon nitride | Hardness plus lubricity |
TiAlN | Titanium aluminum nitride | Oxidation resistance at high temperatures |
Diamond | DLC, CVD diamond | Low friction, high thermal conductivity |
Teflon | PTFE polymers | Friction and adhesion reduction |
Multiple layers of coatings are often combined to enhance specific characteristics. Custom coatings can provide optimized performance for the application.
Applications of Carbide Flat Blanks
The unique properties of carbide make it suitable for the following applications:
Industry | Applications |
---|---|
Metalworking | Cutting and forming dies, punches, tooling |
Woodworking | Cutters, saw tips, router bits |
Plastics | Injection molds, extrusion dies |
Automotive | Forming dies, gages, fixtures |
Aerospace | Cutting tools, wear parts, molds |
Medical | Surgical instruments, dental tools |
Electronics | Wafer machining, wire drawing dies |
Carbide’s hardness at high temperatures is critical for metal cutting and forming where tool life is essential. The corrosion resistance benefits plastic injection molds and electronic component manufacturing.
Different carbide grades balance toughness and hardness for these applications based on the forces, speeds, and environment involved.
How to Select Carbide Grades and Grain Size
Choosing the right carbide grade and grain size depends on the application and operating conditions, including:
- Hardness of work material – Harder materials require finer grains and higher hardness to cut and machine efficiently. Ultra-fine grain carbides are best suited for hardened tool steels, ceramic and composite materials.
- Cutting speed – Higher speeds generate more heat and require grades resistant to thermal softening. Fine and submicron carbides have higher hot hardness.
- Impact forces – Applications with vibration or impact loads need tougher grades with medium and coarse grains to resist fracture and chipping.
- Precision – Finer carbide grains and tighter tolerances allow manufacturing parts within tighter specifications.
- Environment – Corrosive conditions may require upgraded binders or coatings for oxidation and chemical resistance.
Consulting application engineers from suppliers is recommended to match the carbide blank properties to the operating conditions. This ensures optimal performance and productivity.
Standards for Carbide Flat Blanks
International and national organizations publish standards governing carbide blank specifications, quality, and testing. The main standards bodies are:
- ISO – International Organization for Standardization
- ANSI – American National Standards Institute
- ASTM – American Society for Testing and Materials
- JIS – Japanese Industrial Standards
Relevant carbide blank standards include:
- ISO 1832 – Structured carbide grades
- ANSI B212.4-1986 – Carbide hardness testing
- JIS R 1601 – Classification and grain size
- ASTM B865 – Testing methods
Reputable manufacturers test carbide blanks according to these standards to validate grade, hardness uniformity, grain size, and other properties.
Suppliers of Carbide Flat Blanks
There are many industry suppliers offering a range of carbide blanks. Some of the top global manufacturers are:
Company | Headquarters | Grades | Coatings | Services |
---|---|---|---|---|
Sandvik | Sweden | C, P, M, K | TiCN, AlTiN | Custom blanks |
Kennametal | United States | KC, LC | TiN, TiCN | Technical support |
Ceratizit | Luxembourg | CC, NN | TiAlN, DLC | Carbide recycling |
Kyocera | Japan | Micrograin, coarse | TiCN, TiN | Custom engineering |
Mitsubishi | Japan | Ultra-fine to coarse | TiAIN, CVD Diamond | Custom sizes |
Smaller regional suppliers are also available. Working with an experienced carbide supplier ensures getting the optimal grade and blank for specific needs. They also offer additional services like custom machining and coatings.
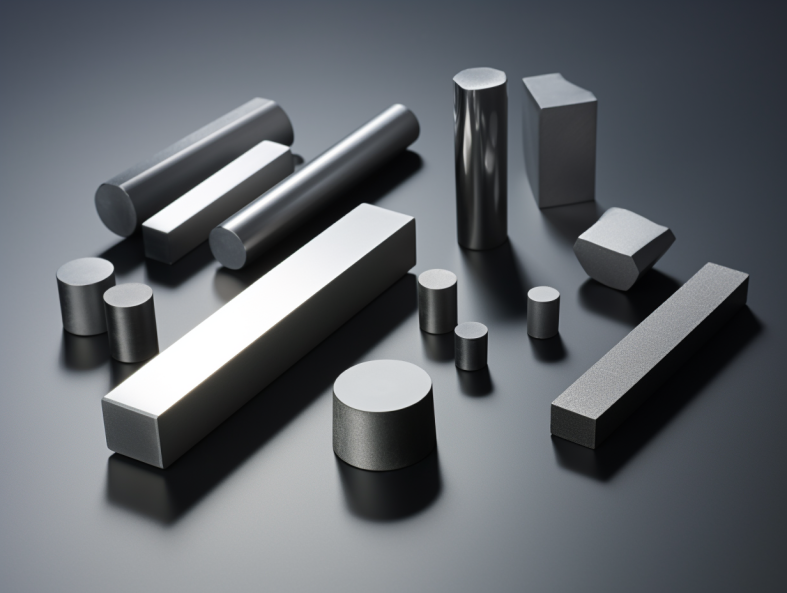
Costs of Carbide Blanks
Carbide flat blanks range from $5 to $50 per pound depending on size, grade, tolerances, and quantity:
- Grades – Finer grainsubmicron and ultra-fine grades are more expensive than coarse grades. Custom grades with high cobalt content also cost more.
- Quantity – Per piece costs range from $1 to $4 for common sizes. Bulk discounts apply for orders over 10-20 pieces.
- Tooling – Blanks within 0.0005” tolerances are more expensive than standard 0.001” to 0.002” tolerance blanks.
- Coatings – Coated blanks command around a 10-20% premium over uncoated. Multiple or exotic coatings increase cost.
- Size – Larger blanks and custom blank sizes often have higher associated tooling costs.
Getting quote from several suppliers is recommended to find the best balance of quality and cost for an application.
Pros and Cons of Carbide Flat Blanks
Advantages:
- Extreme hardness for wear resistance
- Maintains strength and cutting ability at high temperatures
- Resists corrosion and chemical damage
- Enables machining of very hard or abrasive materials
- Consistent properties for precision components
- Simplifies manufacturing of complex geometries
- Wide range of grades balance toughness and hardness
- Coatings improve specific characteristics
- Available in standard and custom sizes and geometries
Limitations:
- More expensive than tool steel or HSS blanks
- Brittle with risk of chipping from impacts
- Requires diamond grinding due to hardness
- Heavier than other tool materials
- Difficult to machine complex internal features
- Coatings may delaminate under extreme forces
- Grain pull-out can occur with poor carbide quality
- Special handling required to avoid cracking
FAQs
Q: What are the most commonly used carbide grades?
A: For general machining, the C2, C4, and C6 grades offer a good balance. K10 and K20 with cobalt binders are also popular. For high wear applications, submicron P grades excel while tough C8 to C10 are good for intermittent cuts.
Q: When should coatings vs. uncoated blanks be used?
A: Coatings improve wear protection and lubricity. They are recommended for abrasive or gummy materials like carbon steel, aluminum, and wood. For short run jobs, uncoated blanks are generally used.
Q: How are custom carbide blanks made?
A: Custom blanks are usually ground to size from standard geometry blanks. EDMed blanks allow complex ID shapes but have higher associated costs. Miniature blanks use special processes and quality checks.
Q: What causes microchipping on carbide blanks?
A: Fractures form from impact damage, grinding stresses or heat checks from overheating. Proper handling, conservative grinding parameters and inspection for cracks minimize chipping risk.
Q: Can carbide blanks be repaired or recoated?
A: Recoating or resharpening blanks is possible in some cases. Repairs are limited for damaged blanks but may be an option over replacement.
Q: What are the main advantages of carbide over HSS tool blanks?
A: Carbide maintains hardness and cutting ability at much higher temperatures than HSS allowing faster speeds. Carbide has superior wear resistance for longer life on abrasive materials.
Conclusion
Carbide’s unique properties make it an essential material for durable cutting, machining and forming applications across industries. Carbide flat blanks provide the foundation for creating optimized custom tools and components to enhance manufacturing productivity.
Choosing the appropriate grade and grain size matched to operating conditions is key to maximizing blank performance. Consulting technical experts is recommended when selecting blanks for an application.
Coatings, specialty grades and fine grain sizes expand carbide’s capabilities for the most demanding uses. As newer binders and ultra-fine grain technologies emerge, carbide blanks will continue improving manufacturing processes requiring precision, speed and resistance to extreme environments.