Imagine a world where drilling into granite countertops felt like butter, or where shaping razor-sharp tools was an everyday breeze. That’s the kind of world metric carbide rods help create. These unassuming metal sticks are the workhorses of countless industries, quietly enabling precision machining and shaping of some of the toughest materials around.
But what exactly are metric carbide rods, and how do they achieve such incredible feats? Buckle up, because we’re diving deep into the fascinating world of these industrial champions!
Introduction to Metric Carbide Rods
Metric carbide rods are essentially long, thin cylinders made from an incredibly hard material called tungsten carbide. Tungsten carbide is a ceramic compound known for its exceptional strength, hardness, and resistance to wear and tear. It’s no exaggeration to say that metric carbide rods are some of the toughest manufactured materials on the planet, easily surpassing the capabilities of even high-grade steel.
Here’s the secret sauce behind their strength: tungsten carbide isn’t just one material; it’s a composite. Imagine tiny, super-strong tungsten carbide crystals suspended in a metallic binder, like raisins in a powerful metal cookie dough. This combination creates a synergy of properties, resulting in a material that’s both incredibly hard and resistant to shattering.
But why “metric”? Unlike its imperial counterpart (measured in inches), metric carbide rods are sized based on the metric system, the globally preferred system for scientific measurement. This means their diameters are specified in millimeters (mm), making them a perfect fit for machinery and tooling designed around the metric system.
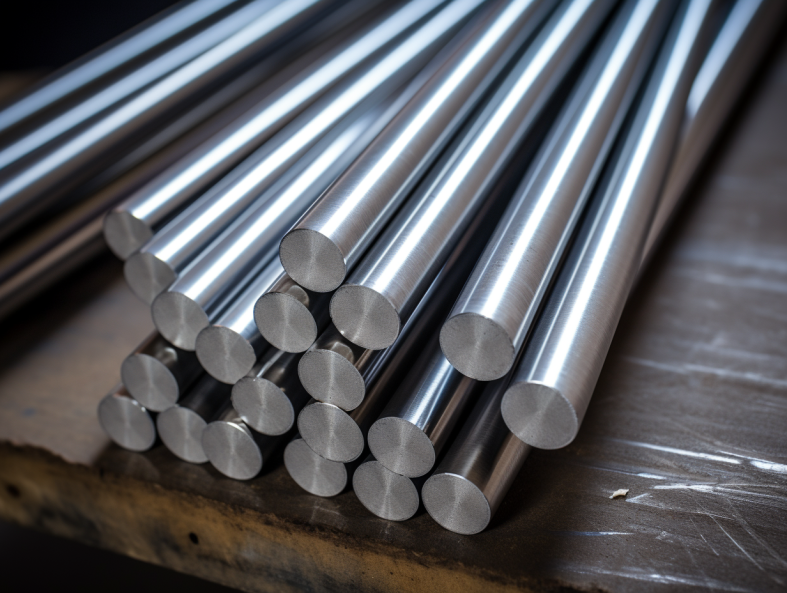
The Production Process of Metric Carbide Rods
Crafting these industrial marvels is no small feat. Here’s a glimpse into the remarkable journey of a metric carbide rod:
- Powder Power: The first step involves creating the essential ingredients – tungsten carbide powder and a metallic binder powder (usually cobalt). These powders are meticulously formulated to achieve the desired balance of properties in the final product.
- Mixing and Matching: The measured quantities of tungsten carbide and binder powder are precisely mixed to ensure a uniform distribution. Imagine tiny, super-strong tungsten carbide grains getting evenly coated with the metallic binder, like shaking a snow globe filled with pebbles and glitter.
- Compacting the Force: The mixed powder is then subjected to immense pressure in a specialized press. This intense squeezing forces the particles together, forming a dense and solid green compact, much like how a snowball becomes denser when packed tightly.
- Shaping Up: The green compact, still relatively weak, is then shaped into a long, cylindrical rod using various techniques like extrusion or pressing. Think of Play-Doh being squeezed through a mold to form a long, thin snake.
- The Heat is On: The shaped rod undergoes a high-temperature sintering process. Here, intense heat (often exceeding 1400°C) activates the binder, causing it to melt and fuse the tungsten carbide particles together. Imagine the Play-Doh snake being baked in an oven, transforming into a solid and permanent form.
- Grinding for Perfection: The sintered rod may undergo grinding to achieve the exact desired diameter and surface finish. This ensures precise dimensions and a smooth surface for optimal performance.
- Quality Check: Finally, the finished metric carbide rods undergo rigorous quality checks to ensure they meet the required specifications for strength, hardness, and dimensional accuracy.
The entire process is a marvel of material science and engineering, transforming raw materials into a powerhouse of industrial capability.
Selection of Metric Carbide Rods
Not all metric carbide rods are created equal. Choosing the right one depends on the specific application. Here are some key factors to consider:
- Grade: Metric carbide comes in various grades, each formulated with a specific binder content and tungsten carbide grain size. Higher binder content often translates to better toughness but slightly lower hardness, while the opposite holds true for lower binder content. Matching the grade to the task is crucial. For example, a high-impact application like chiseling might favor a tougher grade, while a high-precision cutting application might prioritize a harder grade.
- Diameter and Length: Metric carbide rods come in a wide range of diameters and lengths to suit various machining and tooling needs. A delicate engraving job might require a thin rod with a small diameter, whereas a heavy-duty grooving operation might call for a thicker and longer rod.
- Surface Finish: The surface finish of the rod can also impact performance. A smoother finish can provide better chip clearance and reduce friction during cutting, while a rougher finish might be preferred for applications requiring a stronger grip on a tool insert.
- Manufacturer Reputation: When it comes to mission-critical applications, opting for reputable manufacturers with proven quality control processes is essential. Look for brands known for consistent performance and reliable product specifications.
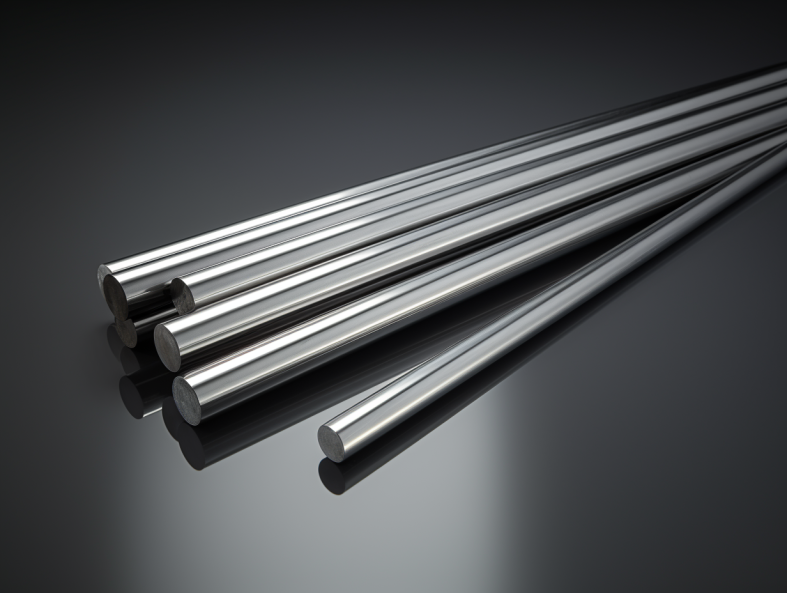
Understanding Grade Options
Metric carbide grades are often denoted by a code consisting of numbers and letters. Delving a little deeper, here’s a breakdown of what this code signifies:
- The first two numbers: These represent the Rockwell C hardness (HRC) of the material. For instance, a metric carbide rod labeled “10K” would have a hardness of around 100 HRC. Generally, higher numbers indicate greater hardness and better wear resistance, ideal for tasks like machining hardened steel or abrasive materials.
- The letter: This typically denotes the binder content. The most common letter you’ll encounter is “K,” signifying cobalt as the primary binder. A higher percentage of “K” translates to increased toughness but slightly lower hardness. Other letters like “F” or “G” might indicate different binder compositions used for specialized applications.
Choosing the Right Diameter and Length
Just like Goldilocks searching for the perfect bed, selecting the ideal diameter and length for your metric carbide rod is crucial. Here’s a breakdown of what to consider:
- Diameter: Think about the tool or application you’ll be using the rod for. A small, delicate engraving tool might require a thin rod (perhaps 1-2 mm in diameter) for intricate detail work. Conversely, a heavy-duty grooving operation on a large lathe might necessitate a thicker rod (think 10-20 mm or more) to handle the increased forces involved.
- Length: The length of the rod is equally important. Consider the depth of material you need to machine or the overall size of the tool you’re creating. For instance, a deep hole drilling operation would require a longer rod compared to a shallow countersinking application.
A Smooth Operator or a Grippy Friend?
The surface finish of your metric carbide rod, while seemingly subtle, can significantly impact performance. Here’s how to choose the right finish for the job:
- Smooth Operator: A smooth finish, achieved through grinding or polishing, offers several advantages. It allows for better chip clearance during cutting, reducing friction and heat buildup. This is particularly beneficial for high-speed machining applications or when working with materials that tend to stick to the tool, like aluminum or some plastics.
- Grippy Friend: A rougher finish, achieved by techniques like sandblasting or etching, might be preferable in certain situations. For instance, if you’re using the metric carbide rod as an insert for a brazed tool, a slightly rougher finish can provide a better grip for the brazing material. This ensures a strong and secure bond between the rod and the tool body.
Manufacturer Reputation: Why Brand Matters
When it comes to metric carbide rods, especially for critical applications, choosing a reputable manufacturer is paramount. Here’s why:
- Consistent Quality: Renowned manufacturers implement stringent quality control procedures throughout the production process. This ensures that each metric carbide rod they produce meets their stated specifications for hardness, toughness, and dimensional accuracy. This consistency is vital for predictable performance and reliable results.
- Technical Support: Reputable brands often provide excellent technical support. Their experienced staff can answer your questions about grade selection, recommend the right product for your specific needs, and offer valuable insights into using their metric carbide rods effectively.
- Innovation and Development: Leading manufacturers are constantly innovating and developing new grades and formulations of metric carbide to cater to ever-evolving industrial demands. By choosing a reputable brand, you gain access to these advancements and can benefit from the latest material science breakthroughs.
Remember, the right metric carbide rod can be the difference between a smooth, efficient machining operation and a frustrating, time-consuming one. By carefully considering the factors outlined above, you can ensure you select the perfect rod for your specific needs.
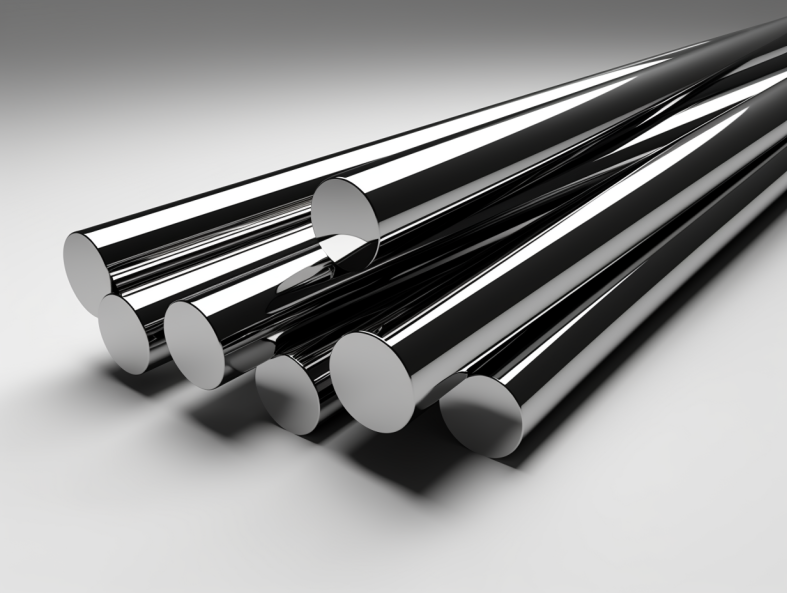
Applications of Metric Carbide Rods
Metric carbide rods are the workhorses of countless industries, playing a vital role in various metalworking and machining applications. Here are some key examples:
- Cutting Tools (Continued): …and turning inserts. These tools, tipped with brazed or mechanically clamped metric carbide inserts, can machine a wide range of materials, from soft aluminum to ultra-hard steels and even exotic alloys. Their exceptional hardness and wear resistance allow for faster cutting speeds, cleaner cuts, and longer tool life compared to traditional high-speed steel tools.
- Die Making and Punches: Metric carbide rods are instrumental in creating dies and punches used in stamping, punching, and blanking operations. These components require immense strength and resistance to deformation to withstand the high pressures involved in shaping sheet metal. Metric carbide rods, especially those formulated for high toughness, are perfectly suited for this task, ensuring precise and durable die and punch creation.
- Wear Parts and Abrasion Resistance: Whenever an application involves enduring friction and wear, metric carbide rods come to the rescue. They are commonly used in wear parts like wear strips, guides, and nozzles that are constantly exposed to abrasive materials. Their exceptional wear resistance significantly extends the lifespan of these components, reducing downtime and maintenance costs.
- Medical Devices and Implants: Due to their biocompatibility and exceptional strength, metric carbide rods are finding increasing applications in the medical field. Specifically formulated grades are used to manufacture surgical instruments, orthopedic implants, and other medical devices that require a combination of strength, wear resistance, and corrosion resistance.
- Aerospace and Defense: The demanding world of aerospace and defense relies heavily on high-performance materials. Metric carbide rods play a crucial role here, used in components like landing gear, jet engine parts, and even in the shaping of rocket engine nozzles. Their ability to withstand extreme temperatures, resist wear, and maintain structural integrity makes them irreplaceable in these critical applications.
Exploring Unexpected Uses of Metric Carbide Rods
Metric carbide rods aren’t limited to just industrial applications. Their unique properties have led to some fascinating and unexpected uses:
- Jewelry Making: Believe it or not, some jewelry makers utilize thin metric carbide rods for creating intricate engraving tools used for personalizing rings, pendants, and other ornaments. The fine detail achievable with these sharp and wear-resistant tools allows for exquisite craftsmanship.
- Art and Sculpture: Some sculptors have begun experimenting with metric carbide rods for creating unique and durable sculptures. The ability to precisely shape the rod and its exceptional hardness allows for the creation of sharp edges, intricate details, and a unique aesthetic that is difficult to achieve with traditional materials.
- Extreme Sports and Recreation: The exceptional wear resistance of metric carbide has even found its way into the world of extreme sports. Some ice skates incorporate small metric carbide inserts in their blades for superior edge retention and extended life, allowing skaters to perform at their peak for longer durations.
These are just a few examples of how metric carbide rods are pushing the boundaries of what’s possible in various industries and applications. As material science continues to evolve, we can expect to see even more innovative and unexpected uses for these remarkable industrial workhorses.
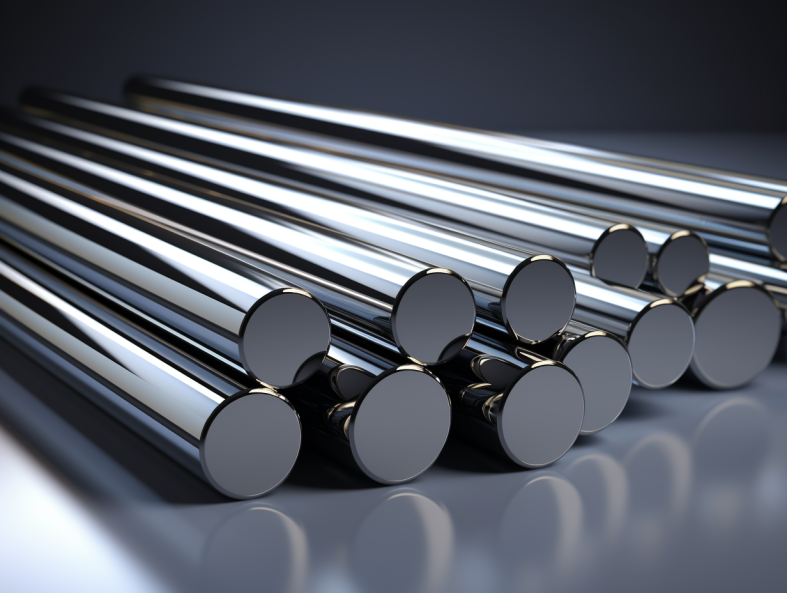
Advantages and Disadvantages of Metric Carbide Rods
Metric carbide rods offer a plethora of advantages that make them invaluable in countless applications. However, it’s important to consider their limitations as well:
Advantages:
- Exceptional Hardness and Wear Resistance: Metric carbide is one of the hardest materials commercially available, significantly surpassing even high-grade steel. This translates to superior wear resistance, allowing metric carbide tools to last longer and maintain sharp cutting edges for extended periods.
- High-Speed Machining: Due to their hardness and heat resistance, metric carbide rods enable machining operations at significantly higher speeds compared to traditional tools. This translates to increased productivity and faster turnaround times in manufacturing environments.
- Precision Machining: The rigidity and dimensional stability of metric carbide rods contribute to precise machining capabilities. This allows for the creation of parts with tight tolerances and intricate details, essential for various high-precision applications.
- Versatility: Metric carbide comes in a wide range of grades and formulations, each tailored for specific requirements. This versatility makes them suitable for machining a diverse array of materials, from soft aluminum to exotic alloys and even some composite materials.
Disadvantages:
- High Cost: Compared to traditional high-speed steel tools, metric carbide rods can be significantly more expensive. The upfront cost can be a deterrent for some applications, particularly for low-volume or hobbyist use.
- Brittleness: While incredibly hard, metric carbide can be somewhat brittle. This means they can chip or fracture if subjected to excessive impact or shock loads. Proper handling and tool selection are crucial to avoid breakage.
- Heat Sensitivity: Although metric carbide exhibits good heat resistance, prolonged exposure to extremely high temperatures can cause the material to lose some of its strength and hardness. This needs to be considered when selecting metric carbide tools for applications involving high heat generation, such as high-speed cutting of some steels.
- Limited Applications for Soft Materials: While metric carbide excels at machining hard materials, it might not be the most cost-effective option for very soft materials like wood or plastics. Traditional high-speed steel or even carbon steel tools might be better suited for such applications.
Making the Right Choice
The decision to use metric carbide rods boils down to a careful evaluation of your specific needs. Consider the following factors:
- Material to be Machined: The hardness and abrasiveness of the material you’ll be working with are primary considerations. For tough materials, metric carbide is the clear winner. For softer materials, alternative tool materials might be more economical.
- Required Level of Precision: If tight tolerances and intricate details are crucial, the dimensional stability and rigidity of metric carbide make them a compelling choice.
- Production Volume and Budget: For high-volume production runs, the extended tool life and faster machining speeds offered by metric carbide can justify the higher upfront cost. For low-volume or hobbyist applications, traditional tool materials might be more budget-friendly.
- Application Requirements: Consider factors like impact resistance and heat generation. If your application involves high shock loads or extreme temperatures, alternative tool materials with better impact resistance or higher heat tolerance might be necessary.
By carefully weighing the advantages and disadvantages of metric carbide rods in the context of your specific application, you can make an informed decision that optimizes both performance and cost-effectiveness.
The Future of Metric Carbide Rods
The world of metric carbide rods is constantly evolving. Here are some exciting trends shaping the future of this remarkable material:
- Advanced Material Science: Researchers are continually developing new formulations and grain structures for metric carbide. These advancements aim to achieve even higher hardness, improved toughness, and better thermal properties, further expanding the capabilities of metric carbide rods.
- Nanotechnology Integration: The incorporation of nanoparticles into the metric carbide matrix is a promising area of research. This could lead to the development of metric carbide rods with superior wear resistance, improved strength, and even self-lubricating properties.
- Sustainable Manufacturing: The focus on eco-friendly practices is driving innovation in the production of metric carbide rods. Manufacturers are exploring ways to reduce the environmental impact of the manufacturing process, such as using recycled materials or developing more energy-efficient production techniques.
- 3D Printing of Carbide Composites: The emergence of 3D printing technologies opens exciting possibilities for creating custom-designed metric carbide tools with complex geometries. This could revolutionize the way cutting tools are designed and manufactured.
As these advancements unfold, metric carbide rods are poised to play an even more significant role in shaping the future of manufacturing and beyond. Their exceptional properties, combined with ongoing innovation, ensure that these unassuming rods will continue to be the unsung heroes of countless industries for years to come.
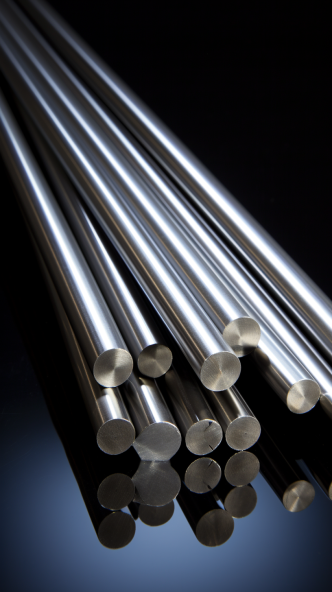
FAQ
Q: What is the difference between metric and imperial carbide rods?
A: The primary difference lies in the measurement system used. Metric carbide rods are sized in millimeters (mm), while imperial carbide rods are sized in inches. They offer the same material properties and benefits, but their dimensions cater to different tooling and machinery standards.
Q: Can I use metric carbide rods for drilling into concrete?
A: While metric carbide is incredibly hard, it’s not generally recommended for drilling concrete. Concrete is an abrasive material that can cause rapid wear on the rod. Specialized drill bits designed for concrete are a better choice for this application.
Q: How do I store metric carbide rods safely?
A: To prevent chipping or breakage, store metric carbide rods in a secure container with padding to prevent them from banging against each other. You can also use protective caps on the ends of the rods for added safety.
Q: Where can I buy metric carbide rods?
A: Metric carbide rods can be purchased from various industrial tool suppliers, both online and in physical stores. Reputable manufacturers and distributors often offer a wide selection of grades, sizes, and lengths to suit your specific needs.
Q: Are there any safety precautions to consider when using metric carbide rods?
A: Always wear appropriate safety gear, including eye protection, gloves, and proper respiratory protection when working with metric carbide rods. Be mindful of the potential for flying debris during machining operations.