Manchester carbide inserts refer to a range of indexable carbide cutting inserts manufactured by various companies to suit different machining applications. This article provides an overview of carbide inserts, their properties, manufacturing methods, grades, styles, coatings and leading global suppliers.
Overview of manchester carbide inserts
Carbide inserts are cutting tools with a carbide tip brazed to a steel shank body. The carbide tips feature geometrically defined cutting edges that perform the actual material removal. Key attributes include:
- Extreme hardness for wear resistance
- Advanced substrate and coating combinations
- Precision indexable inserts for multi-edge use
- Designed for high productivity machining
Carbide inserts are available in a wide range of international and proprietary grades to suit different work materials, operating parameters and production demands. Custom geometries, chipbreakers, coatings and edge preparations further optimize performance.
Carbide Insert Components
Component | Role |
---|---|
Carbide substrate | Provides hardness for wear resistance during cutting |
Coating | Enhances lubricity, oxidation resistance and friction reduction |
Chipbreaker | Allows proper chip formation and flow across insert rake face |
Clamping area | Facilitates secure and precise seating on toolholder |
Carbide Insert Standards
International standards help define insert geometry, designation, selection and usage across manufacturers:
- ISO 1832 – Insert identification and coding
- ANSI B212.4 – Carbide insert dimensions and tolerances
- ISO 13399 – Toolholder interface dimensions
- Manufacturer standards – Grades, geometries, technical data
This enables interchangeability and consistent performance across carbide insert suppliers adhering to the standards.
Manufacturing Carbide Inserts
Producing precision carbide inserts involves carefully controlled powder metallurgy processes and state-of-the-art finishing steps:
1. Milling and Blending
Source powders are milled to desired particle sizes and intimately blended to achieve uniform distribution in the mixture.
2. Pressing
The feedstock is pressed into ‘green’ parts using dies machined to tight dimensional tolerances.
3. Sintering
Green inserts are consolidation to full density by heating below melting point to create durable cemented carbides.
4. Edge Preparation
The sintered part’s cutting edges are profiled using grinding or other methods to hone and prepare them for application.
5. Coating
Optional PVD, CVD or other coating processes are used to deposit wear-resistant layers over substrate.
Carbide grade composition, powder characteristics, pressing parameters, sintering method, edge treatment and coatings all determine product performance.
Grades of Carbide Inserts
Carbide inserts are produced in a wide range of compositions or ‘grades’ tailored to different work materials – steels, stainless steels, cast iron, aluminum alloys, titanium alloys, plastics and more.
Grade | Description | Key Elements | Hardness |
---|---|---|---|
Uncoated carbide | Base sintered micrograin or submicron tungsten or titanium carbide substrate without any coating | WC-Co <6% cobalt | 88-93 HRA |
PVD-coated | Physical vapor deposition applied 2-25 μm coatings like TiN, TiCN, TiAlN | Underlying mixed carbide | 92-94 HRA |
CVD-coated | Chemical vapor deposited 8-12 μm coatings including aluminum oxide | Fine grained tungsten carbide | 93+ HRA |
Cermet | Binderless nano-scale chromium carbide-nickel chrome | Cr3C2-NiCr | 88-92 HRA |
CBN/PCBN | Polycrystalline cubic boron nitride second hardest material known | CBN-ceramic binder | 90+ HRA |
Higher cobalt content allows fracture toughness while ultrafine grain tungsten carbide provides maximal hardness and heat resistance for more demanding applications on exotic alloys or hardened materials.
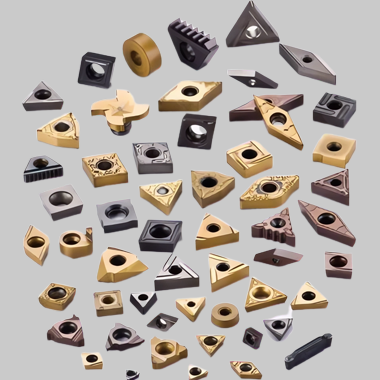
Coatings for Carbide Inserts
Coatings deposited over the carbide insert substrate lower cutting forces and temperatures while increasing lubricity and wear resistance. Common types include:
Coating | Description | Thickness | Key Properties |
---|---|---|---|
TiN | Titanium nitride | 2-4 μm | Gold color standard coating |
TiCN | Titanium carbonitride | 2-4 μm | Higher hardness and lubricity than TiN |
TiAlN | Titanium aluminum nitride | 4-25 μm | Oxidation resistance, high hot hardness |
Al2O3 | Aluminum oxide | 8-12 μm | Low friction, insulation, thermal shock resistance |
DLC | Diamond-like carbon | 1-5 μm | Extreme hardness, inertness, low friction |
Thicker coatings allow multiple regrinds while preserving insert integrity beneath. More advanced coatings like TiSiN, ZrN and TiAlCrN suit specific work materials in demanding environments.
Styles of Carbide Inserts
Carbide inserts come in hundreds of standardized and custom geometries to suit different applications and machining methods. Common styles include:
Style | Description | Key Attributes |
---|---|---|
Round insert | Circular disc shape | Positive geometry, multipurpose |
Square insert | Square shape, often with clipped corners | Added edge security, prevented rotation |
Triangle insert | Equilateral triangle | Greatest number of cutting edges |
Rhombic | Diamond shape | Added strength and edge security |
Other regular shapes | Pentagon, hexagon, octagon shaped inserts | Indexability, specific edge configurations |
Irregular shapes | Specialty geometries | Complex forms like gear profile cutters |
nn addition to simple geometric styles, inserts may features chipbreakers, coolant holes or channels, Irregular shapes offer engineered geometries with complex cutting edge profiles to suit niche applications in aerospace, power generation, oil and gas industries.
Sizes of Carbide Inserts
Carbide inserts range from minute sizes for Swiss-type CNC lathe work to large indexable inserts for rough boring, milling and grooving operations. Standard inscribed circle dimensions include:
Inscribed Circle Size | Typical Applications |
---|---|
1/16″, 1.5 mm | Swiss-type turning, small bores |
3/16″, 3/8″, 5 mm | Finish boring, turning |
1/2″, 5/8″, 3/4″ | Turning, profiling, planing |
1″ and above | Rough boring, peripheral milling |
Larger carbide inserts allow greater metal removal rates increased productivity for roughing cuts before switching to smaller sizes for semifinishing and finishing passes. Specific edge lengths, corner radii, thickness and features are engineered for desired results.
Leading Carbide Insert Manufacturers
Major carbide insert brands catering to Manchester and global markets include:
ISCAR
Founded: 1952 in Israel
Headquarters: Migdal Tefen, Israel
- Carbide grades: High micrograin and submicron substrates plus BARC ION iTAS TiAlN, ZrN coatings
- Markets served: Automotive, aerospace, die mold, general machining
- Brands: ISCAR, Ingersoll, TaeguTec metalworking tools
Kennametal
Founded: 1938
Headquarters: Pittsburgh, Pennsylvania USA
- Carbide grades: Beyond grades with nano-scale tungsten carbides and proprietary top layers
- Markets served: Energy, transportation, general engineering
- Brands: Kennametal, WIDIA, Hanita cutting tools
Korloy
Founded: 1977 Headquarters: Chungcheongbuk-do, South Korea
- Carbide grades: Tri-Tech sharpness with three-tier substrate, coatings and top layers
- Markets served: Automotive, die and mold
- Brands: Korloy, Addison, Mirae, CrownCUT carbide inserts
Kyocera Unimerco
Founded: 1959 Headquarters: Ann Arbor, Michigan USA
- Carbide grades: Ultra-fine grain carbide grades plus advanced coating technology
- Markets served: Aerospace, automotive, medical, mold and die
- Brands: Kyocera, plus seven merged companies
Mitsubishi Materials
Founded: 1970
Headquarters: Tokyo, Japan
- Carbide grades: Ultra-smooth NHS micrograin substrates, Miracle coating technology
- Markets served: Automotive, die mold
- Brands: Mitsubishi carbide inserts and cutting tools
Sandvik Coromant
Founded: 1942 Headquarters: Stockholm, Sweden
- Carbide grades: CoroTurn wisker-reinforced grades like GC4330 for stainless steels
- Markets served: Aerospace, automotive, general machining
- Brands: Sandvik Coromant round tools for turning
Tungaloy
Founded: 1968 Headquarters: Arlington Heights, Illinois USA
- Carbide grades: Micrograin MC and Nanograde NM hard part turning
- Markets served: Die mold, automotive, medical
- Brands: Tungaloy round cutting tools for industry
Walter Tools
Founded: 1919 Headquarters: Tübingen, Germany
- Carbide grades: Duratomic ultra-fine grain with nano-structured Twin Adaptive coating
- Markets served: Automotive, aviation, power engineering
- Brands: Walter Tools metalworking and cutting tools
These plus other manufacturers offer wide selections of carbide insert grades, geometries, sizes and customizable specifications to suit all types of machining in Manchester area manufacturing environments.
Carbide Insert Styles Comparison
Parameter | Round Insert | Square Insert | Triangular Insert |
---|---|---|---|
Edge security | Fair | Good | Good |
Indexability | 2-8 edges | 2-8 edges | 3-6 edges |
Application fit | General purpose | Added strength | Maximum edges |
Replaceable tips | Brazed | Clamped | Clamped |
Relative cost | Low | Moderate | High |
Choose style based on rigidity required, max number of usable cutting edges and operating parameters. Coolant delivery method also impacts selection.
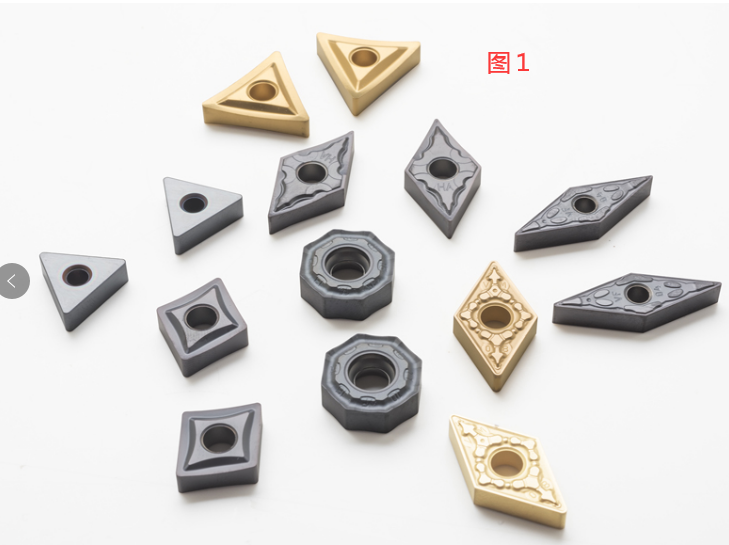
Carbide vs. Other Tool Materials
Carbide vs. High Speed Steel
Carbide inserts last 10-20X longer tool life than HSS tools. Much higher hot hardness and wear resistance. However, carbide more brittle with less strength and shock resistance versus tougher HSS.
Carbide vs. Ceramics
Silicon nitride ceramics approach diamond in hardness but are chemically inert unlike diamond. Ceramics more temperature sensitive with lower impact strength. Costlier than carbide inserts.
Carbide vs. cBN/PCBN
Polycrystalline CBN second hardest material exhibits thermal stability for high speed machining of irons/steels. More expensive than carbide inserts but lower wear rates at extreme parameters.
Carbide vs. Diamond
Natural and polycrystalline diamond have much higher hardness than carbide with lower friction and high heat conductivity. However, carbide tougher for interrupted cuts. Diamond costly and reacts with ferrous materials.
No universally best insert material exists. Carbide strikes optimal balance of wear resistance and transverse rupture strength across the widest range of applications from roughing to finishing. Advanced carbide grades continue pushing performance barriers matching or exceeding exotic cutting tool materials.
FAQ
Q: What carbide grade is suitable for machining stainless steel or other alloys?
A: For austenitic or duplex stainless steels, consider coated grades with medium cobalt content like 10% cobalt. Avoid ultrafine grades as lower cobalt offers better shock resistance.
Q: How are carbide coating properties matched to workpiece materials?
A: Hard coatings like TiAlN sustain high temperatures when machining nickel alloys. Low-friction coatings help on composites and sticky alloys. Specialized coatings continue expanding work material compatibility.
Q: When are ground versus molded chipbreaker geometries used?
A: Ground chipbreakers allow precise edge profiles but are costlier. Molded geometries easier to mass produce through pressing but less defined. Both work with proper selection.
Q: What are recommended insert handling practices?
A: Always wear gloves when handling to prevent skin oils transfer. Use proper insert boxes with separated compartments to avoid contact or edge damage during storage. Reject chipped or compromised inserts.
Q: When to use carbide inserts versus replaceable carbide tip tooling?
A: Inserts quickly index to fresh cutting edges. Replaceable tips allow custom shank configurations. Choice depends on setup flexibility required and ability to precisely position inserts.