Introduction: The Rise of Long-Lasting Carbide Brazed Tip Blades
In the world of cutting and material removal, achieving exceptional performance, precision, and tool life hinges on the cutting edge. Long-lasting carbide brazed tip blades have emerged as a game-changer, empowering industries worldwide to push the boundaries of what’s possible. This comprehensive guide delves into the intricacies of these remarkable blades, exploring their composition, manufacturing process, diverse applications, and the factors driving their growing adoption.
What are Long-Lasting Carbide Brazed Tip Blades?
A Fusion of Strength and Longevity: Where Tungsten Carbide Meets Precision Brazing
Long-lasting carbide brazed tip blades represent a pinnacle of material science and manufacturing ingenuity. They consist of two primary components:
- Tungsten Carbide Tips: The heart of the blade, meticulously engineered from tungsten carbide powder blended with a metallic binder (typically cobalt). These tips possess exceptional hardness, wear resistance, and hot hardness, making them ideal for demanding cutting applications.
- Steel Blade Body: Provides a robust and cost-effective base for the carbide tips. The blade body is typically made from high-quality alloy steel, offering a balance of strength, toughness, and machinability.
These components are permanently joined through a high-temperature brazing process, creating an inseparable bond that can withstand the extreme forces and temperatures encountered during cutting operations.
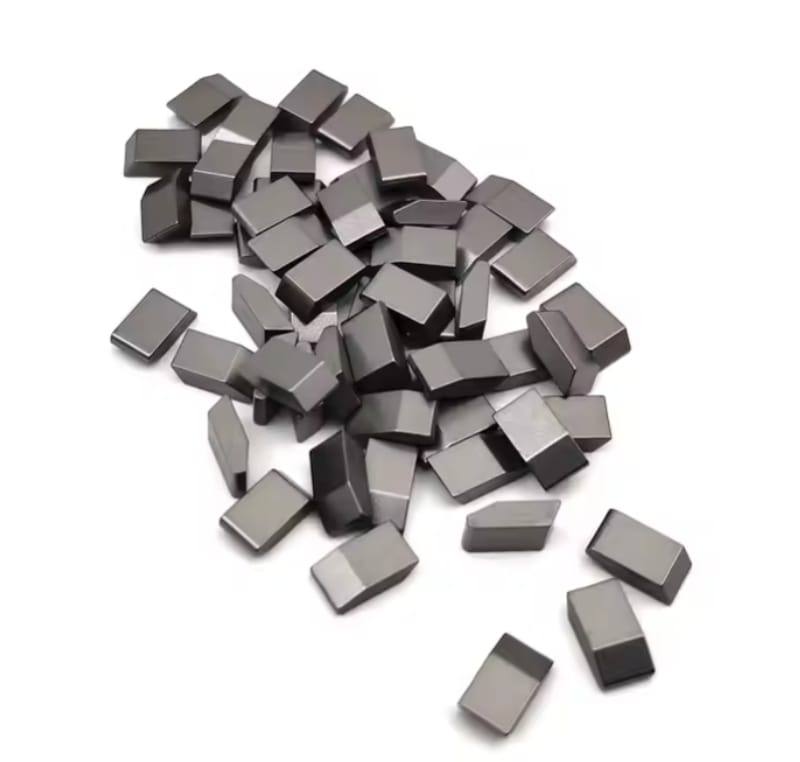
The Anatomy of Durability: Key Properties of Carbide Brazed Tip Blades
Table 1: Unveiling the Power Within – Properties of Long-Lasting Carbide Brazed Tip Blades
Property | Description | Benefits in Cutting Applications |
---|---|---|
High Hardness | Measures resistance to indentation and deformation. Tungsten carbide ranks among the hardest materials known, exceeding even hardened steel. | Enables blades to maintain sharpness and cutting edge integrity even when machining tough materials at high speeds. |
Exceptional Wear Resistance | Resists material loss due to abrasion, adhesion, and diffusion wear. | Significantly extends tool life, reducing downtime for blade changes and lowering overall cutting costs. |
High Hot Hardness | Retains hardness and strength at elevated temperatures, resisting softening and deformation. | Crucial for high-speed cutting operations where frictional heat can reach extreme levels. |
Good Fracture Resistance | Withstands impact loads and interrupted cutting conditions without chipping or breaking. | Ensures reliable performance and consistent results, even in challenging cutting environments. |
Chemical Inertness | Resists chemical reactions and corrosion from coolants, lubricants, and workpiece materials. | Extends tool life and prevents workpiece contamination, maintaining cutting efficiency and surface finish. |
Applications Across Industries: Where Precision Meets Versatility
Long-lasting carbide brazed tip blades find applications in a wide range of industries, including:
- Metalworking and Machining: Cutting, slotting, grooving, and parting off operations on various metals, including steel, stainless steel, cast iron, and aerospace alloys.
- Woodworking: Cutting, shaping, and sizing wood, plywood, and other wood-based composites, particularly in high-volume production environments.
- Plastics and Composites: Cutting, trimming, and deburring plastic parts, composite materials, and fiberglass components.
- Paper and Packaging: Cutting and slitting paper, cardboard, and other packaging materials with precision and efficiency.
- Food Processing: Slicing, dicing, and portioning food products with high sanitation and durability requirements.
Navigating the Market: Comparing Leading Suppliers
Table 2: A Global Perspective – Leading Suppliers of Long-Lasting Carbide Brazed Tip Blades
Supplier | Location | Price Range (USD/Blade – Approximate) | Specialties |
---|---|---|---|
TRUER | China | $10 – $100+ | Cost-effective solutions, wide range of blade sizes and geometries, focus on quality and customer satisfaction |
Sandvik Coromant | Sweden | $15 – $150+ | Wide range of grades and geometries, advanced coatings, technical expertise |
Kennametal | USA | $12 – $120+ | High-performance grades, custom tooling solutions, application support |
Iscar | Israel | $14 – $140+ | Innovative geometries, specialized coatings, focus on productivity enhancement |
Seco Tools | Sweden | $16 – $160+ | Comprehensive product range, digital machining solutions, sustainability focus |
Note: Prices are approximate and vary significantly based on blade size, grade, geometry, coating, quantity, and market conditions.
Advantages and Limitations: A Balanced View of Performance
Table 3: Weighing the Pros and Cons – Advantages and Limitations of Long-Lasting Carbide Brazed Tip Blades
Advantages | Limitations |
---|---|
Exceptional Tool Life: Significantly outlasts conventional steel blades, reducing downtime for blade changes and lowering operating costs. | Higher Initial Cost: Carbide brazed tip blades typically command a higher upfront cost compared to steel blades. |
Increased Cutting Speeds and Feeds: Enables faster cutting rates, boosting productivity and reducing cycle times. | Brittle Nature: Susceptible to chipping or breakage under extreme impact loads or improper cutting parameters. |
Improved Cut Quality: Produces smoother, more precise cuts, reducing the need for secondary finishing operations. | Requires Specialized Grinding: Sharpening and reconditioning require specialized grinding wheels and techniques. |
Enhanced Dimensional Accuracy: Maintains tight tolerances and dimensional stability, even at elevated temperatures. | Limited Application in Certain Materials: Not ideal for cutting very soft or gummy materials that can cause edge buildup. |
Beyond the Blade: Factors Influencing Performance and Tool Life
Maximizing the performance and longevity of long-lasting carbide brazed tip blades involves considering several crucial factors:
- Grade Selection: Choosing the appropriate carbide grade based on the workpiece material, cutting conditions, and desired tool life.
- Geometry Optimization: Selecting the optimal blade geometry (e.g., rake angle, clearance angle, tooth profile) to control chip formation, heat generation, and cutting forces.
- Coating Technology: Applying specialized coatings (e.g., TiN, TiAlN, CVD diamond) to enhance wear resistance, reduce friction, and improve tool life in specific applications.
- Cutting Parameters: Optimizing cutting speed, feed rate, and depth of cut to balance productivity with tool life and surface finish requirements.
- Coolant Selection and Application: Using appropriate coolants and lubrication strategies to control heat, reduce friction, and improve chip evacuation.
Why Choose TRUER for Your Carbide Brazed Tip Blade Needs?
TRUER has emerged as a leading provider of high-quality, cost-effective carbide brazed tip blades, offering:
- Unwavering Commitment to Quality: TRUER utilizes premium carbide grades, advanced brazing technologies, and stringent quality control measures throughout the manufacturing process to ensure consistent performance and reliability.
- Competitive Pricing: TRUER’s efficient operations and customer-centric approach enable them to offer competitive pricing without compromising quality.
- Wide Range of Options: TRUER provides a comprehensive selection of blade sizes, geometries, and coatings to meet diverse cutting application requirements.
- Customer Focus: TRUER is dedicated to providing exceptional customer service, technical support, and timely delivery to ensure customer satisfaction.
FAQs: Addressing Your Carbide Brazed Tip Blade Queries
1. How do I choose the right carbide grade for my application?
Grade selection depends on factors like workpiece material hardness, cutting speed, feed rate, and desired tool life. Consulting supplier catalogs, machining data, or seeking expert advice is recommended.
2. What are the benefits of using coated carbide brazed tip blades?
Coatings enhance wear resistance, reduce friction, improve chip flow, and increase tool life, especially in demanding applications involving high temperatures or abrasive materials.
3. How do I prevent chipping or breakage of carbide brazed tip blades?
Using appropriate cutting parameters, ensuring proper tool holding and workholding, and avoiding sudden impacts or interruptions during cutting can help prevent blade damage.
4. Can carbide brazed tip blades be sharpened and reconditioned?
Yes, they can be sharpened multiple times using specialized grinding wheels and techniques. However, it’s crucial to maintain the original blade geometry and avoid overheating during grinding.
5. What are the latest advancements in carbide brazed tip blade technology?
Advancements include the development of new carbide grades with improved toughness and wear resistance, innovative coatings with enhanced performance characteristics, and optimized blade geometries for specific applications