When it comes to precision machining, indexable carbide inserts are a game-changer. These small yet powerful components have revolutionized the manufacturing world, allowing for efficient and precise cutting, turning, and milling. But what exactly are they, and how do you choose the right ones for your needs? Let’s dive into the world of indexable carbide inserts, exploring their types, applications, properties, and more.
Overview of Indexable Carbide Inserts
Indexable carbide inserts are replaceable cutting tools used in machining operations. They are typically made from carbide, a material known for its hardness and wear resistance. These inserts can be indexed, or rotated, to utilize multiple cutting edges before needing replacement, making them cost-effective and efficient.
Key Features:
- Material: Predominantly carbide
- Applications: Turning, milling, drilling, and more
- Benefits: High precision, multiple cutting edges, cost-effective
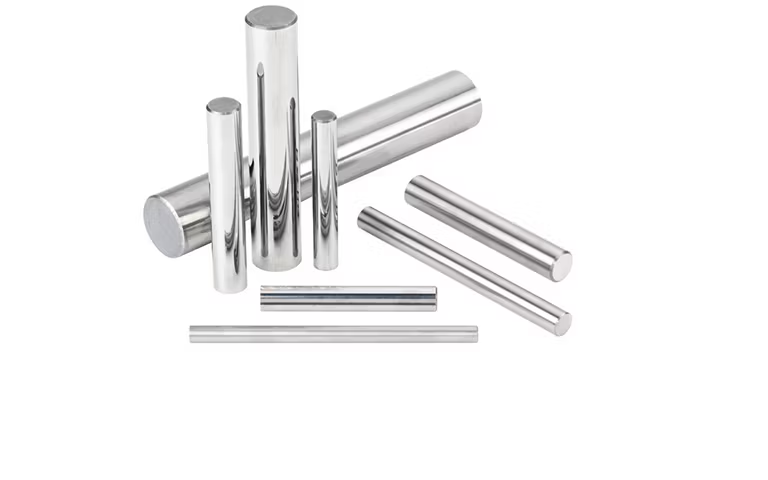
Types of Indexable Carbide Inserts
Indexable carbide inserts come in various shapes, sizes, and grades, each designed for specific applications. Here’s a detailed look at some of the most common types.
Common Shapes and Their Uses
Shape | Description | Applications |
---|---|---|
Triangle | Offers three cutting edges; versatile for various operations | General turning, facing |
Square | Four cutting edges; robust for heavy-duty operations | Roughing, general turning |
Round | Strong edge; reduces chipping and provides smooth finish | Contouring, profiling |
Diamond | Two or four cutting edges; ideal for precise and fine finishing | Finishing, threading |
Rectangle | Longer cutting edge; suitable for large depth cuts and interrupted cuts | Heavy turning, interrupted cuts |
Table of Indexable Carbide Inserts Applications
Application | Description |
---|---|
Turning | Precision cutting to shape the material’s surface |
Milling | Removing material from a workpiece to create a desired shape |
Drilling | Creating holes in the workpiece |
Threading | Cutting threads on a cylindrical surface |
Grooving | Cutting narrow slots or grooves in the material |
Material Properties of Indexable Carbide Inserts
Understanding the material properties of carbide inserts is crucial for selecting the right one for your application.
Table of Material Properties
Property | Description |
---|---|
Hardness | Ability to resist deformation and wear; measured in Vickers hardness (HV) |
Toughness | Ability to absorb energy and resist fracture |
Wear Resistance | Ability to resist wear during cutting operations |
Thermal Stability | Resistance to heat; crucial for high-speed machining |
Composition, Properties, and Characteristics
Carbide inserts are composed of a mix of tungsten carbide particles and a metallic binder, usually cobalt.
Table of Composition and Characteristics
Component | Properties | Characteristics |
---|---|---|
Tungsten Carbide (WC) | High hardness and wear resistance | Provides cutting edge strength |
Cobalt (Co) | Acts as a binder for tungsten carbide particles | Adds toughness and impact resistance |
Titanium Carbide (TiC) | Improves wear resistance and reduces built-up edge | Enhances thermal stability |
Tantalum Carbide (TaC) | Increases hardness and high-temperature performance | Used in high-speed machining applications |
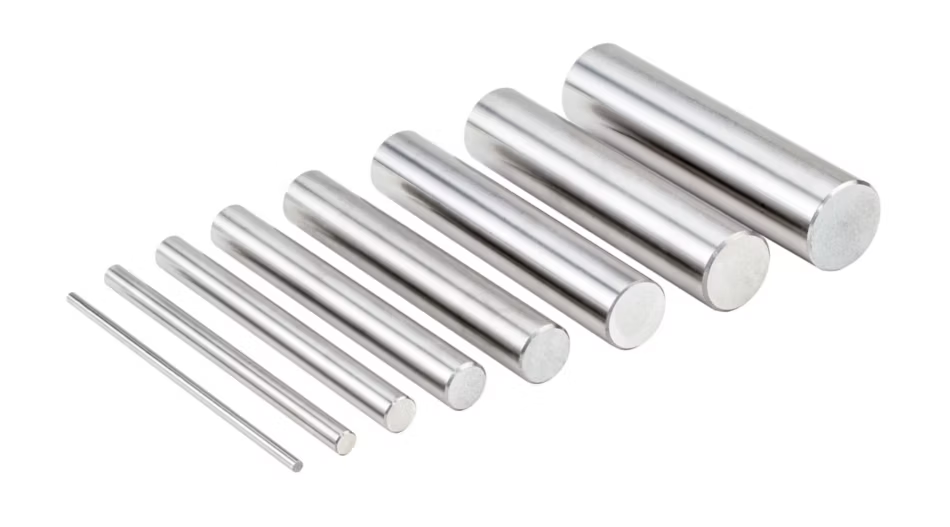
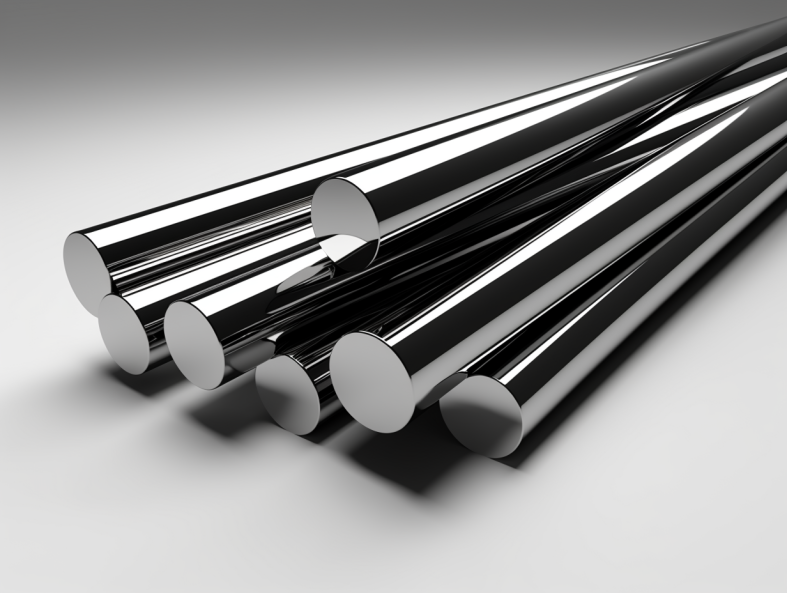
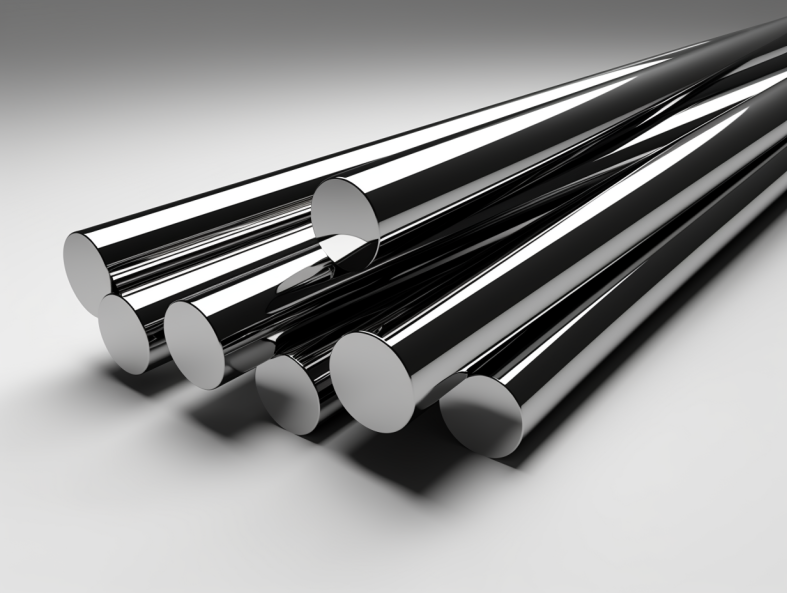
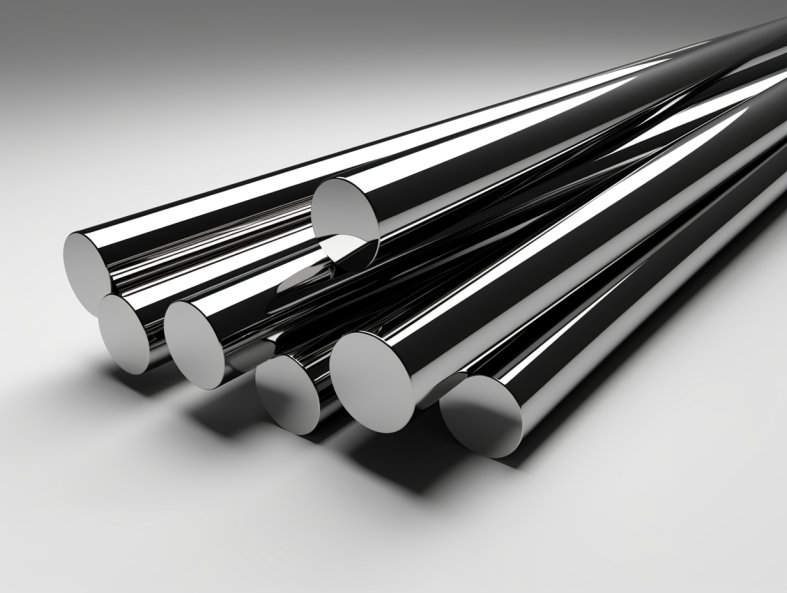
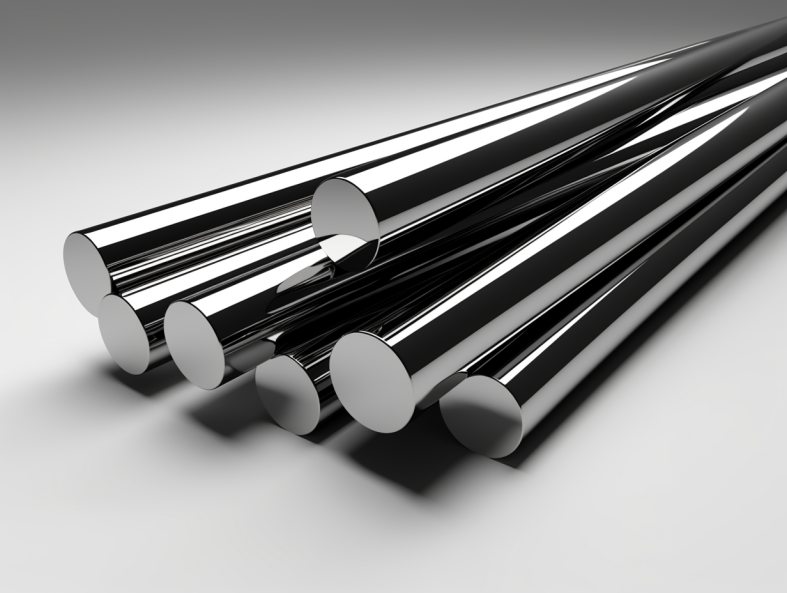
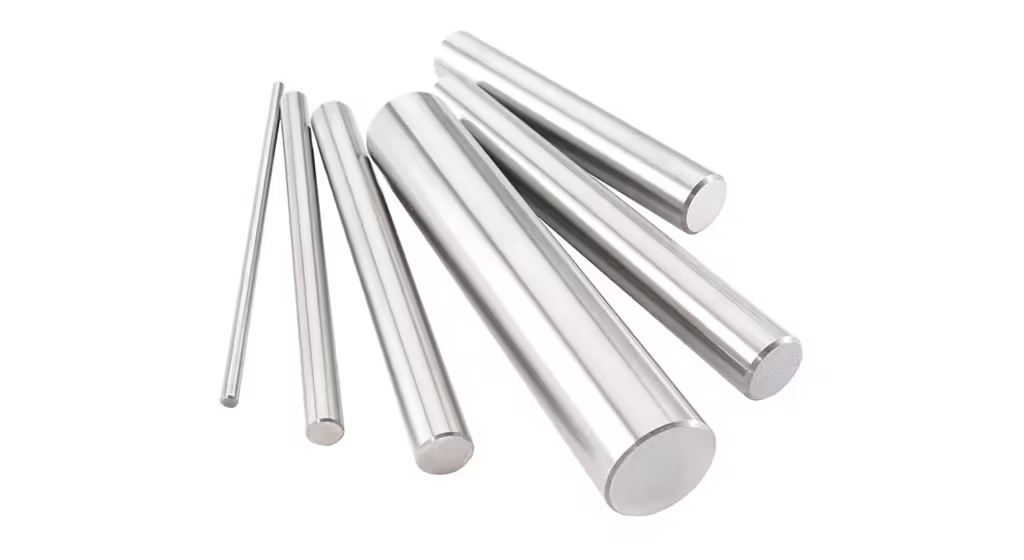
Hardness, Strength, and Wear Resistance
Choosing the right carbide insert involves understanding the balance between hardness, strength, and wear resistance.
Table of Hardness, Strength, and Wear Resistance
Grade | Hardness (HV) | Strength (MPa) | Wear Resistance |
---|---|---|---|
C1 | 1200 | 3000 | High |
C2 | 1500 | 3500 | Medium-High |
C3 | 1800 | 4000 | Medium |
C4 | 2100 | 4500 | Medium-Low |
C5 | 2400 | 5000 | Low |
Specifications, Sizes, Shape, Standards
The specifications of carbide inserts include their sizes, shapes, and adherence to industry standards.
Table of Specifications, Sizes, Shapes, and Standards
Specification | Size Range | Shape | Standards |
---|---|---|---|
ISO | Various (mm) | Triangle, Square, Round | ISO 1832 |
ANSI | Various (inches) | Diamond, Rectangle | ANSI B212.4 |
JIS | Various (mm) | Special shapes | JIS B 1163 |
DIN | Various (mm) | Various | DIN 4987 |
Suppliers and Pricing Details
Finding the right supplier and understanding pricing is crucial for procuring indexable carbide inserts.
Table of Suppliers and Pricing
Supplier | Location | Price Range (per piece) | Specialties |
---|---|---|---|
Kennametal | USA | $10 – $50 | High-performance inserts, diverse shapes |
Sandvik Coromant | Sweden | $15 – $55 | Advanced coatings, custom solutions |
Seco Tools | Sweden | $12 – $45 | Comprehensive range, high precision |
Mitsubishi | Japan | $10 – $40 | Innovative materials, high durability |
Iscar | Israel | $14 – $50 | Versatile applications, robust performance |
How to Select the Right Indexable Carbide Inserts
Selecting the right indexable carbide inserts involves considering the material, application, and machining conditions.
Table on Selecting the Right Indexable Carbide Inserts
Factor | Considerations |
---|---|
Material | Type of workpiece material (steel, aluminum, etc.) |
Application | Type of machining operation (turning, milling, drilling) |
Machine Capability | Machine’s power, speed, and rigidity |
Insert Grade | Based on hardness, toughness, and wear resistance requirements |
Coating | Coated vs. uncoated inserts for different machining conditions |
Comparing Advantages and Limitations
Understanding the pros and cons of different carbide inserts can help make an informed decision.
Table Comparing Advantages and Limitations
Type | Advantages | Limitations |
---|---|---|
Uncoated Inserts | Cost-effective, suitable for low-speed operations | Limited wear resistance, not suitable for high speeds |
Coated Inserts | Enhanced wear resistance, suitable for high speeds | Higher cost, may require specific machining conditions |
Ceramic Inserts | Extremely hard, high-temperature performance | Brittle, not suitable for interrupted cuts |
CBN Inserts | Excellent for hard materials, long tool life | Expensive, limited to specific applications |
Specific Metal Powder Models
Here are some specific models of metal powders used in the production of carbide inserts, each with unique properties and applications.
Detailed Descriptions of Metal Powder Models
Model | Description | Applications |
---|---|---|
WC-10Co-4Cr | Tungsten Carbide with 10% Cobalt and 4% Chromium; excellent wear resistance | Aerospace, automotive components |
WC-12Co | Tungsten Carbide with 12% Cobalt; balanced toughness and hardness | General machining, heavy-duty cutting |
WC-6Ni | Tungsten Carbide with 6% Nickel; corrosion resistance, suitable for wet environments | Oil and gas, marine applications |
TiC-10WC-6Co | Titanium Carbide with 10% Tungsten Carbide and 6% Cobalt; enhanced hardness | Precision finishing, high-speed operations |
TaC-8WC-4Co | Tantalum Carbide with 8% Tungsten Carbide and 4% Cobalt; high-temperature performance | High-speed machining, aerospace |
NiCr-20TiC | Nickel-Chromium with 20% Titanium Carbide; excellent thermal stability | Automotive, high-temperature applications |
Cr3C2-25NiCr | Chromium Carbide with 25% Nickel-Chromium; superior wear and corrosion resistance | Industrial machinery, cutting tools |
Mo2C-5Co | Molybdenum Carbide with 5% Cobalt; high strength and hardness | Heavy-duty cutting, mining tools |
VC-10WC-5Co | Vanadium Carbide with 10% Tungsten Carbide and 5% Cobalt; high wear resistance | Tool and die, high-precision machining |
WC-8Co-2TaC | Tungsten Carbide with 8% Cobalt and 2% Tantalum Carbide; balanced performance | General purpose, aerospace, automotive |
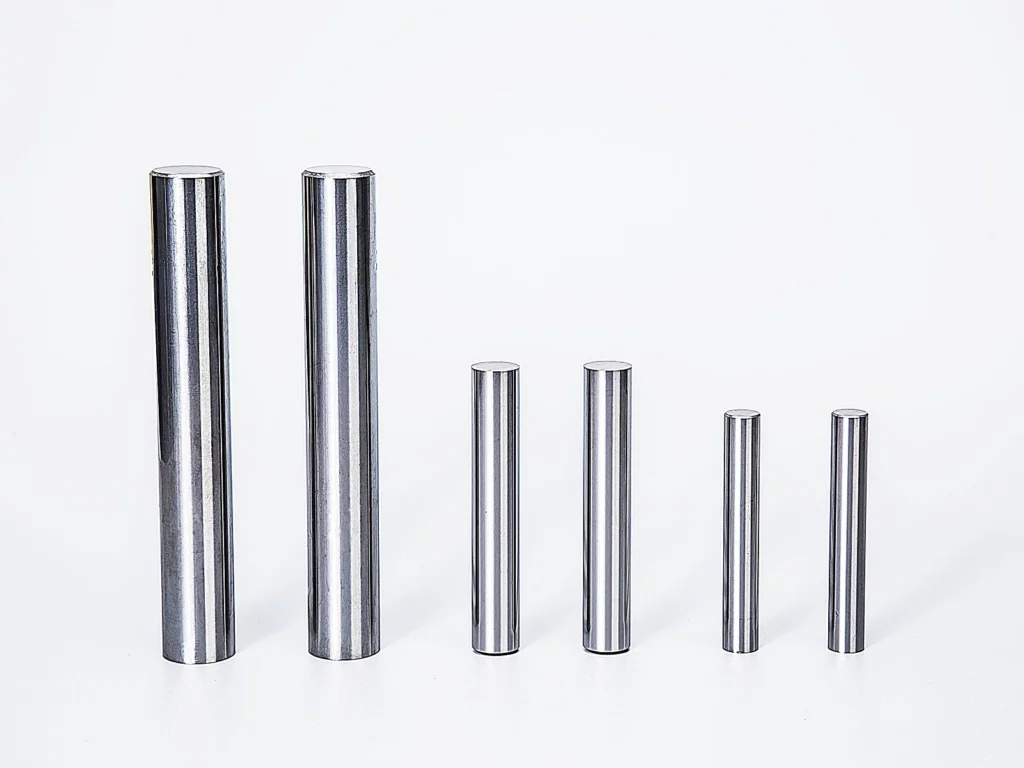
FAQ
Question | Answer |
---|---|
What are indexable carbide inserts used for? | They are used for various machining operations like turning, milling, drilling, and threading. |
How do I choose the right carbide insert? | Consider the workpiece material, machining operation, machine capability, insert grade, and coating. |
What are the benefits of using indexable inserts? | They offer multiple cutting edges, high precision, cost-effectiveness, and reduced downtime. |
What materials are carbide inserts made from? | Primarily tungsten carbide, often with cobalt, titanium carbide, tantalum carbide, and other additives. |
Are coated inserts better than uncoated? | Coated inserts offer enhanced wear resistance and are suitable for high-speed operations but are more expensive. |
Can carbide inserts be re-sharpened? | No, once all cutting edges are worn out, they need to be replaced. |
What is the typical lifespan of a carbide insert? | It depends on the application and material but generally ranges from several hours to several days of continuous use. |
How are carbide inserts attached to tool holders? | They are typically clamped or screwed onto the tool holder, allowing for easy replacement. |
What is the significance of insert grades? | Insert grades determine the balance between hardness, toughness, and wear resistance, impacting performance in specific applications. |
Where can I buy indexable carbide inserts? | Various suppliers like Kennametal, Sandvik Coromant, Seco Tools, Mitsubishi, and Iscar offer a wide range of inserts. |
Conclusion
Choosing the right indexable carbide insert can significantly impact the efficiency and precision of your machining operations. By understanding the types, applications, material properties, and other critical factors, you can make an informed decision that suits your specific needs. Whether you’re a seasoned professional or a beginner, this comprehensive guide provides the insights and information necessary to navigate the world of indexable carbide inserts with confidence.
I hope this comprehensive guide provides the detailed and engaging content you need. If you have any specific requirements or additional points you’d like to include, feel free to let me know!