Introduction: The Unsung Heroes of Wear Resistance
In a world demanding relentless performance and unwavering durability, high-quality tungsten carbide buttons emerge as unsung heroes, quietly powering industries ranging from mining and construction to oil and gas exploration. These small but mighty components, crafted from one of the hardest materials known to man, stand defiant against abrasion, impact, and extreme temperatures, ensuring the longevity and efficiency of countless tools and equipment.
This comprehensive guide delves into the world of high-quality tungsten carbide buttons, unraveling their exceptional properties, diverse applications, and the factors that set them apart as the ultimate solution for combating wear and maximizing performance in the most demanding industries.
What are High-Quality Tungsten Carbide Buttons?
Unveiling the Essence of Durability
High-quality tungsten carbide buttons are engineered components typically composed of tungsten carbide powder, meticulously blended with a binder metal, usually cobalt, and consolidated through a high-temperature sintering process. This intricate process yields an exceptionally hard and wear-resistant material, capable of withstanding the harshest operating conditions.
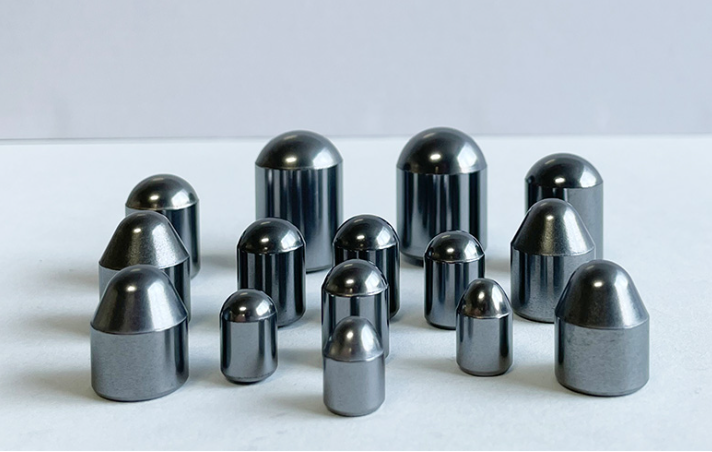
How Tungsten Carbide Buttons Work: A Symphony of Hardness and Toughness
The Science Behind Unwavering Performance
The remarkable performance of tungsten carbide buttons stems from the unique properties imparted by their constituent materials and the intricate sintering process:
- Tungsten Carbide: Renowned for its exceptional hardness, ranking a near-perfect 10 on the Mohs hardness scale, tungsten carbide provides the primary defense against abrasion, wear, and impact.
- Cobalt Binder: Acting as the bonding agent, cobalt enhances the toughness and impact resistance of the tungsten carbide matrix, preventing brittle fracture under high stress and impact loads.
- Sintering Process: The carefully controlled sintering process at temperatures exceeding 1400°C (2552°F) fuses the tungsten carbide particles and cobalt binder, creating a dense, homogeneous material with exceptional hardness and wear resistance.
Fabrication and Machining: Precision Engineering for Optimal Performance
Crafting Excellence from Powder to Part
The fabrication of high-quality tungsten carbide buttons involves a series of precision engineering steps:
- Powder Preparation: Finely ground tungsten carbide and cobalt powders are precisely blended in specific ratios to achieve the desired properties.
- Pressing: The blended powder is then compacted under high pressure in precisely shaped dies, forming the initial “green” button shape.
- Sintering: The green buttons undergo a high-temperature sintering process in controlled atmospheres, fusing the powders and creating the final dense, hard material.
- Finishing: After sintering, the buttons may undergo finishing operations such as grinding, lapping, or polishing to achieve the desired dimensions, surface finish, and tolerances.
Market Trends: A Growing Demand for Uncompromising Performance
Riding the Wave of Industrial Growth
The global market for tungsten carbide buttons is experiencing robust growth, driven by:
- Rising Demand from End-Use Industries: The increasing demand for wear-resistant components in industries such as mining, construction, oil and gas exploration, and agriculture is fueling market expansion.
- Technological Advancements: Innovations in powder metallurgy, sintering techniques, and finishing processes are leading to the development of tungsten carbide buttons with enhanced properties and performance characteristics.
- Focus on Sustainability: The extended lifespan and reduced maintenance requirements of tungsten carbide buttons align with the growing emphasis on sustainability and reducing environmental impact.
Tungsten Carbide Button Specifications: A Glimpse into Diversity
Navigating the Realm of Choices
High-quality tungsten carbide buttons are available in a wide array of grades, sizes, shapes, and configurations to meet the specific demands of diverse applications.
Feature | Description | Options and Variations |
---|---|---|
Grade | Dictates the hardness, toughness, and wear resistance | YG6, YG8, YG10, YG15, YG20 (increasing tungsten carbide content and hardness) |
Size | Determines the overall dimensions and application suitability | Diameters ranging from a few millimeters to several centimeters |
Shape | Influences the contact area, wear pattern, and application-specific performance | Round, hemispherical, conical, ballistic, custom shapes |
Configuration | Defines the attachment method and integration into tools or equipment | Plain, threaded, studded, brazed, welded |
Applications of High-Quality Tungsten Carbide Buttons: Where Durability Reigns Supreme
Conquering Wear in Every Industry
The exceptional wear resistance, impact resistance, and hardness of high-quality tungsten carbide buttons make them indispensable components in a wide range of applications:
- Mining and Construction: Protecting drilling bits, cutting tools, crusher wear parts, and other equipment from the abrasive forces of rock, ore, and concrete.
- Oil and Gas Exploration: Enhancing the durability and longevity of drilling tools, downhole motors, and other equipment operating in harsh, abrasive environments.
- Agriculture and Forestry: Reinforcing tillage tools, ground engaging equipment, and harvesting machinery for extended service life in abrasive soils and demanding conditions.
- Metalworking and Machining: Providing wear-resistant surfaces for dies, punches, cutting tools, and other components subjected to high stress and abrasion.
- Other Industries: Finding applications in industries such as chemical processing, power generation, and pulp and paper, wherever wear resistance and durability are paramount.
Comparing Suppliers: Navigating the Landscape of Quality and Value
Making Informed Decisions for Optimal Sourcing
Supplier | Location | Price Range (per piece) | Specialties |
---|---|---|---|
TRUER | China | $2.50 – $35+ | Customized tungsten carbide products, competitive pricing |
Element Six | Global | $5 – $50+ | Advanced materials and engineered solutions |
Kennametal | Global | $3 – $40+ | Metal cutting tools, wear-resistant solutions |
Note: Prices are approximate and can vary based on grade, size, quantity, and other factors. It’s always recommended to contact suppliers directly for accurate pricing and availability.
Advantages and Limitations: A Balanced Perspective
Weighing the Pros and Cons for Informed Decision-Making
Advantages | Limitations |
---|---|
Exceptional Wear Resistance: Unmatched resistance to abrasive wear, extending tool and equipment life | High Initial Cost: Can be more expensive than alternative materials upfront |
High Hardness: Maintains sharpness and cutting efficiency over extended periods | Brittleness: Can be prone to chipping or fracture under high impact or shock loads |
Impact Resistance: Withstands moderate to high impact forces, depending on grade and design | Machining Challenges: Requires specialized machining techniques and equipment due to hardness |
High-Temperature Performance: Retains hardness and properties at elevated temperatures | Limited Ductility: Not suitable for applications requiring significant bending or deformation |
The Intricacies of Tungsten Carbide: Beyond the Buttons
Exploring the Wider World of a Remarkable Material
While this guide has focused on tungsten carbide buttons, it’s essential to recognize that tungsten carbide’s versatility extends far beyond these small but mighty components. This remarkable material finds applications in:
- Cutting Tools: From drill bits and end mills to saw blades and router bits, tungsten carbide’s hardness and wear resistance are revolutionizing cutting tool performance.
- Wear Parts: Nozzles, dies, bearings, seals, and countless other components subjected to wear benefit from the exceptional durability of tungsten carbide.
- Jewelry: Known for its scratch resistance and enduring shine, tungsten carbide has emerged as a popular choice for wedding bands and other jewelry.
Why Choose TRUER for High-Quality Tungsten Carbide Buttons?
Partnering with Excellence for Unrivaled Performance
At TRUER, we’re not just suppliers of high-quality tungsten carbide buttons; we’re your dedicated partners in achieving unparalleled performance and exceeding industry standards. Here’s why discerning customers choose us:
- Uncompromising Quality: We utilize stringent quality control measures throughout our production process, ensuring that our tungsten carbide buttons consistently meet the highest standards of performance and reliability.
- Tailored Solutions: We understand that your needs are unique. Our team of experts works closely with you to understand your specific application requirements and provide customized solutions tailored to your exact specifications.
- Competitive Pricing: We strive to offer competitive pricing without compromising on quality, ensuring that you receive the best possible value for your investment.
- Exceptional Customer Service: Our commitment to customer satisfaction is unwavering. We’re always available to answer your questions, provide technical support, and ensure that your experience with us is exceptional from start to finish.
Frequently Asked Questions: Addressing Your Tungsten Carbide Button Queries
Q1: What factors influence the price of tungsten carbide buttons?
A1: Several factors influence pricing, including the grade of tungsten carbide (higher tungsten carbide content generally translates to higher cost), the size and complexity of the button, the quantity ordered, and the supplier’s pricing policies.
Q2: How do I choose the right grade of tungsten carbide button for my application?
A2: The optimal grade depends on the specific application requirements, including the type of material being processed, the operating conditions (temperature, pressure, impact), and the desired wear resistance. Consulting with a knowledgeable supplier like TRUER can help you make the best selection.
Q3: Can tungsten carbide buttons be repaired or refurbished?
A3: While tungsten carbide is extremely hard and wear-resistant, it can experience wear and tear over time. In some cases, depending on the extent of wear, buttons can be refurbished through grinding or other specialized processes. However, if the wear is significant, replacement is often the most cost-effective solution.
Q4: What are the safety considerations when working with tungsten carbide buttons?
A4: Tungsten carbide is extremely hard and can shatter or chip if dropped or struck sharply. When handling or installing tungsten carbide buttons, it’s crucial to wear appropriate personal protective equipment (PPE), including safety glasses and gloves.
Q5: What is the lifespan of a tungsten carbide button?
A5: The lifespan of a tungsten carbide button varies significantly depending on factors such as the grade of tungsten carbide, the operating conditions, the application itself, and the maintenance practices. In some cases, buttons can last for thousands of hours of operation, while in other demanding applications, their lifespan may be shorter.