Overview
High-impact carbide brazed tip inserts are revolutionary tools that have transformed the landscape of machining and manufacturing. Renowned for their exceptional durability, hardness, and resistance to wear, these inserts are indispensable in a wide array of industrial applications. This article provides an in-depth exploration of high-impact carbide brazed tip inserts, covering their definition, working principles, usage guidelines, manufacturing process, market trends, and more. By understanding the intricate details of these cutting-edge tools, manufacturers can significantly enhance their operational efficiency and product quality.
Detailed Introduction
What Are High-Impact Carbide Brazed Tip Inserts?
High-impact carbide brazed tip inserts are specialized cutting tools that feature a carbide tip securely brazed onto a tool body. The carbide tip, typically composed of tungsten carbide particles bonded with a metallic binder such as cobalt, provides unmatched hardness and wear resistance. This combination makes the inserts ideal for high-stress machining operations, including cutting, milling, and drilling.
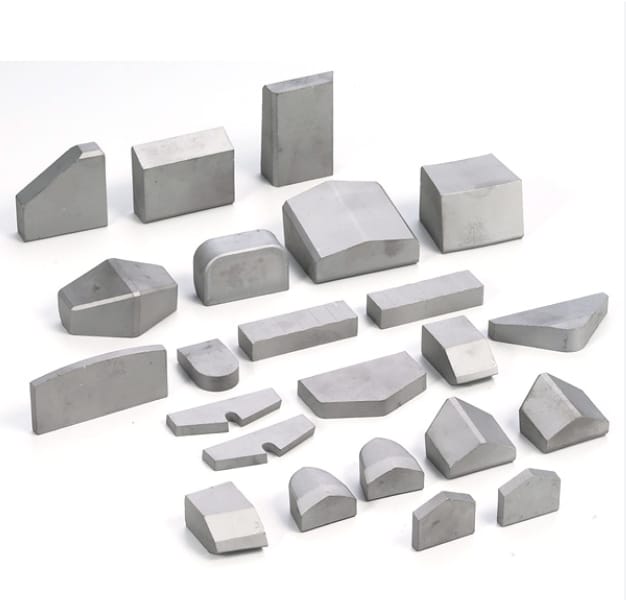
Working Principle
The exceptional performance of high-impact carbide brazed tip inserts is rooted in the superior properties of tungsten carbide. During cutting operations, the carbide tip maintains its sharpness and structural integrity even under extreme temperatures and pressures. The brazing process involves melting a filler metal to bond the carbide tip to the tool body, creating a robust and durable connection capable of withstanding the mechanical stresses of machining.
How to Use High-Impact Carbide Brazed Tip Inserts
- Selecting the Right Insert: Choose the appropriate carbide brazed tip insert based on the material to be machined and the specific application.
- Installation: Securely mount the insert in the tool holder, ensuring it is properly aligned.
- Adjusting Machining Parameters: Set cutting parameters such as speed, feed rate, and depth of cut according to the characteristics of the carbide brazed tip insert.
- Regular Maintenance: Regularly inspect and replace inserts to maintain optimal cutting efficiency and prevent damage to the workpiece.
Manufacturing Process
- Preparation: Clean and prepare carbide blanks to ensure a pristine surface for coating adhesion.
- Coating Application: Apply the selected coating using Physical Vapor Deposition (PVD) or Chemical Vapor Deposition (CVD) processes.
- Quality Control: Conduct rigorous testing to ensure coating thickness, adhesion, and uniformity meet stringent industry standards.
Market Trends
The demand for high-impact carbide brazed tip inserts continues to grow, driven by the need for efficient and durable cutting tools across various sectors. Key market trends include:
- Innovations in Coating Materials: Development of multi-layer and nanocomposite coatings to enhance performance.
- Increased Automation: Adoption of automated coating processes to ensure consistent quality and efficiency.
- Sustainability: Emphasis on eco-friendly coating processes and recyclable materials.
Product Specifications
The table below details the specifications and characteristics of various high-impact carbide brazed tip inserts.
Type | Composition | Properties | Features | Specifications | Size Range | Grade | Standards |
---|---|---|---|---|---|---|---|
Titanium Nitride (TiN) | Titanium + Nitrogen | High hardness, wear resistance | Low friction, golden color | ISO Certified | 10mm – 100mm | K10, K20, K30 | ISO 9001 |
Titanium Carbonitride (TiCN) | Titanium + Carbon + Nitrogen | Hard, tough, wear resistance | Improved hardness and toughness | Customizable | 5mm – 50mm | K05, K15 | ASTM B777 |
Aluminum Oxide (Al2O3) | Aluminum + Oxygen | High-temperature resistance | Chemically inert, white shade | Industry Specific | 20mm – 200mm | W10, W20 | DIN 9001 |
Multi-layer Coating | TiN + Al2O3 + TiCN | Combined advantages | Enhanced durability, multi-color | OEM Available | 2mm – 80mm | K40, K50 | ANSI B212 |
WC-Co (Tungsten Carbide-Cobalt) | Tungsten Carbide + Cobalt | High hardness, impact resistance | Wear-resistant, high-temperature | ISO Certified | 15mm – 150mm | YG6, YG8 | ISO 9001 |
Titanium Aluminum Nitride (TiAlN) | Titanium + Aluminum + Nitrogen | High hardness, oxidation resistance | Improved high-temperature stability | Customizable | 5mm – 100mm | K40, K50 | ASTM B777 |
Silicon Nitride (Si3N4) | Silicon + Nitrogen | High hardness, thermal stability | Wear-resistant, chemically inert | Industry Specific | 10mm – 80mm | N1, N2 | DIN 9001 |
Table 1: Specifications and Characteristics of High-Impact Carbide Brazed Tip Inserts
Applications
High-impact carbide brazed tip inserts are utilized in a wide variety of industries due to their exceptional performance. Below are some primary application fields:
- Metalworking: Milling, turning, and drilling tools.
- Aerospace: Components in high-stress environments.
- Automotive Manufacturing: Engine parts, gear manufacturing.
- Medical Instruments: Surgical instruments, dental tools.
- Oil and Gas: Drilling tools, wear-resistant components.
- Woodworking: Cutting and shaping tools.
- Construction: Concrete and stone cutting tools.
List 1: Application Fields of High-Impact Carbide Brazed Tip Inserts
Comparison
To assist in selecting the right supplier, the table below compares TRUER with various suppliers of high-impact carbide brazed tip inserts.
Supplier | Location | Price Range (per piece) | Specialties |
---|---|---|---|
TRUER | China | $18 – $95 | High-impact, custom sizes, advanced coatings |
Kennametal | USA | $20 – $100 | Custom sizes, advanced coatings |
Sandvik | Sweden | $25 – $120 | High precision, multi-layer coatings |
ZCC Cutting Tools | China | $15 – $90 | Cost-effective, bulk orders |
Kyocera | Japan | $22 – $110 | High-quality, innovative materials |
Sumitomo Electric | Japan | $22 – $110 | Advanced coatings, micro-grain |
Table 2: Comparison of TRUER with Other Suppliers of High-Impact Carbide Brazed Tip Inserts
Pros and Cons
The table below compares the advantages and disadvantages of high-impact carbide brazed tip inserts.
Advantages | Disadvantages |
---|---|
Exceptional hardness | Higher cost |
Reduced friction and wear | Requires specialized equipment |
Improved heat resistance | Potential brittleness under heavy impact |
Longer tool life | Complex manufacturing process |
Enhanced cutting performance | Coating may peel off |
Table 3: Pros and Cons of High-Impact Carbide Brazed Tip Inserts
Related Topics
Different Types of Carbide Coatings
Understanding the various types of coatings available for carbide inserts is crucial for selecting the right one for your application. Common types include:
- TiN (Titanium Nitride): Known for high hardness and low friction.
- TiCN (Titanium Carbonitride): Offers higher hardness and toughness compared to TiN.
- Al2O3 (Aluminum Oxide): Provides excellent high-temperature resistance and chemical inertness.
- Multi-layer Coatings: Combine the advantages of different coatings to enhance overall performance.
Standards and Certifications
Ensuring that high-impact carbide brazed tip inserts meet industry standards and certifications is crucial for quality and reliability. Common standards include:
- ISO 9001: Ensures a consistent quality management system.
- ASTM B777: Specifies requirements for tungsten carbide materials.
- DIN 9001: German quality management system standard.
- ANSI B212: American cutting tool standards.
How to Choose the Right Supplier
Choosing the right supplier is critical for obtaining high-quality high-impact carbide brazed tip inserts. Key factors to consider include:
- Quality Assurance: Does the supplier provide products that meet industry standards and certifications?
- Customization Services: Can the supplier offer customized solutions based on specific customer needs?
- Price: Are the supplier’s prices competitive, and do their products offer good value for money?
- After-Sales Service: Does the supplier provide technical support and after-sales service to ensure customer satisfaction?
Why Choose TRUER
TRUER stands out as a premier supplier of high-impact carbide brazed tip inserts due to the following reasons:
- Unmatched Quality: TRUER’s inserts are manufactured to the highest standards, ensuring exceptional performance and durability.
- Advanced Coatings: Utilizing cutting-edge coating technologies, TRUER offers inserts with superior wear resistance and longevity.
- Customization: TRUER provides tailored solutions to meet the specific needs of different industries and applications.
- Competitive Pricing: TRUER offers high-quality products at competitive prices, ensuring excellent value for money.
- Comprehensive Support: TRUER provides extensive technical support and after-sales service to assist customers with any issues or questions.
FAQ
Q1: What are high-impact carbide brazed tip inserts?
A1: High-impact carbide brazed tip inserts are cutting tools featuring a carbide tip brazed onto a tool body, offering exceptional hardness and wear resistance.
Q2: What are the main applications of high-impact carbide brazed tip inserts?
A2: Main applications include metalworking, aerospace, automotive manufacturing, medical instruments, oil and gas, woodworking, and construction.
Q3: How do I choose the right high-impact carbide brazed tip insert?
A3: Selecting the right insert requires considering the material to be machined, specific application, coating type, and tool life.
Q4: What are the pros and cons of high-impact carbide brazed tip inserts?
A4: Advantages include exceptional hardness, reduced friction and wear, improved heat resistance, longer tool life, and enhanced cutting performance. Disadvantages include higher cost, need for specialized equipment, potential brittleness under heavy impact, complex manufacturing process, and possible coating peel-off.
Q5: How can I ensure the quality of high-impact carbide brazed tip inserts?
A5: Ensure the quality of high-impact carbide brazed tip inserts by selecting suppliers that meet industry standards and certifications, conducting regular inspections and maintenance, and using inserts that meet specifications and requirements.