Overview
Hardmetal carbide preforms are indispensable in various industries due to their exceptional hardness, wear resistance, and versatility. These preforms are crafted from a composite material that combines tungsten carbide with a metallic binder, typically cobalt, to create a product that can withstand extreme conditions. This article delves into the specifics of hardmetal carbide preform grades and standards, offering a comprehensive guide to understanding their properties, applications, and market trends.
Detailed Introduction
What is a Hardmetal Carbide Preform?
A hardmetal carbide preform, also known as a cemented carbide preform, is a pre-shaped component made from a mixture of tungsten carbide (WC) particles and a metallic binder such as cobalt (Co). The manufacturing process involves pressing and sintering the powder mixture to form a dense, solid piece with high hardness and wear resistance. These preforms are then machined or ground into the final shape required for specific industrial applications.
Working Principle of Hardmetal Carbide Preforms
The effectiveness of hardmetal carbide preforms lies in the properties of tungsten carbide and the binder metal. Tungsten carbide provides exceptional hardness and wear resistance, while the binder metal offers toughness and prevents brittleness. The sintering process, which involves heating the pressed powder mixture in a controlled environment, ensures that the carbide particles are bonded tightly together, resulting in a uniform and durable preform.
How to Use Hardmetal Carbide Preforms
Hardmetal carbide preforms are typically used in applications that require high precision and durability. The general steps for using these preforms include:
- Machining: Using diamond or carbide tools to machine the preform to the desired shape and size.
- Grinding: Precision grinding to achieve the exact dimensions and surface finish needed.
- Polishing: Polishing the surface to enhance performance and extend the lifespan of the component.
- Coating: Applying protective coatings to improve wear resistance and reduce friction in demanding applications.
Processing Hardmetal Carbide Preforms
The processing of hardmetal carbide preforms involves several critical steps:
- Design Specification: Defining the exact specifications, including dimensions, tolerances, and material composition.
- Powder Preparation: Mixing tungsten carbide powder with the chosen binder metal.
- Pressing: Compressing the mixture into the desired shape using high-pressure molds.
- Sintering: Heating the pressed preforms in a controlled environment to bond the carbide particles and binder metal.
- Finishing: Performing secondary operations such as grinding, polishing, and coating to meet final specifications.
Market Trends
The market for hardmetal carbide preforms is expanding rapidly, driven by the increasing demand for durable, high-performance tools and components. Key market trends include:
- Technological Advancements: Innovations in manufacturing processes and materials are enhancing the quality and capabilities of carbide preforms.
- Growing Industrialization: Industrial growth, especially in developing regions, is boosting the demand for high-quality, wear-resistant tools.
- Sustainability: The recyclability of tungsten carbide makes it an attractive option for environmentally conscious industries.
Product Specifications
To provide a comprehensive overview, here is a detailed table outlining the specifications and characteristics of various hardmetal carbide preform grades and standards.
Type | Composition | Attributes | Features | Specifications | Size Range | Grade | Standard |
---|---|---|---|---|---|---|---|
Standard Blanks | WC + Co | High hardness, wear-resistant | Uniform density | ISO certified | 10mm – 100mm | K10, K20, K30 | ISO 9001 |
Micro-grain Blanks | WC + Co + Additives | Ultra-fine grain, high toughness | Enhanced surface finish | Customizable | 5mm – 50mm | K05, K15 | ASTM B777 |
Wear Parts Blanks | WC + Ni | Corrosion-resistant, durable | High impact resistance | Industry-specific | 20mm – 200mm | W10, W20 | DIN 9001 |
Cutting Tool Blanks | WC + Co + TiC | Superior cutting edge retention | High precision machining | OEM available | 2mm – 80mm | K40, K50 | ANSI B212 |
Table 1: Specifications and Characteristics of Hardmetal Carbide Preforms
Applications
Hardmetal carbide preforms are utilized in a wide range of industries due to their exceptional properties. Here are some of the primary applications:
- Metalworking: Cutting tools, drills, and end mills.
- Mining: Wear-resistant parts for drilling and excavation equipment.
- Woodworking: Router bits, saw blades, and planing knives.
- Aerospace: Precision components subjected to high stress and wear.
- Automotive: Engine parts, valve seats, and fuel injector components.
- Oil and Gas: Drill bits, wear-resistant seals, and flow control components.
- Medical: Surgical instruments and dental tools.
- Construction: Concrete cutting and drilling tools.
List 1: Applications of Hardmetal Carbide Preforms
Comparative Analysis of Suppliers
To assist in choosing the right supplier, the following table compares various suppliers of hardmetal carbide preforms based on key criteria.
Supplier | Location | Price Range (per piece) | Specialties |
---|---|---|---|
Kennametal | USA | $20 – $100 | Custom sizes, quick delivery |
Sandvik | Sweden | $25 – $120 | High precision, ISO certified |
ZCC Cutting Tools | China | $15 – $90 | Low cost, bulk orders |
Sumitomo Electric | Japan | $22 – $110 | Advanced coatings, micro-grain |
TRUER | China | $18 – $95 | High-quality materials, advanced manufacturing |
Table 2: Comparative Analysis of Suppliers of Hardmetal Carbide Preforms
Advantages and Disadvantages
Here is a comprehensive comparison of the pros and cons of using hardmetal carbide preforms.
Advantages | Disadvantages |
---|---|
Exceptional hardness | High cost |
Wear and corrosion resistance | Difficult to machine without specialized equipment |
High temperature tolerance | Can be brittle under high impact |
Long lifespan | Requires precise manufacturing techniques |
Recyclable material | Can be more expensive than other materials |
Consistent performance in demanding applications | Limited flexibility in certain applications |
Table 3: Advantages and Disadvantages of Hardmetal Carbide Preforms
Related Content
Types of Hardmetal Carbide Grades
Understanding the different grades of hardmetal carbide is crucial for selecting the right preform for your application. Common grades include:
- K Grades: Typically used for cutting and wear-resistant applications.
- P Grades: Designed for applications requiring high toughness and impact resistance.
- M Grades: Balanced grades suitable for a wide range of applications.
Standards and Certifications
Ensuring that hardmetal carbide preforms meet industry standards and certifications is essential for quality and reliability. Common standards include:
- ISO 9001: Ensures consistent quality management systems.
- ASTM B777: Specifies the requirements for tungsten carbide materials.
- DIN 9001: German standard for quality management systems.
- ANSI B212: American standard for cutting tools.
Why Choose TRUER
Choosing TRUER for your hardmetal carbide preforms offers several advantages:
- High-Quality Materials: We use only the highest-grade raw materials for superior performance and durability.
- Advanced Manufacturing: Our state-of-the-art facilities and technologies ensure precision and consistency.
- Extensive Experience: Our years of industry expertise enable us to provide valuable insights and solutions.
- Customer Support: Our dedicated team is always ready to assist with any inquiries or technical support.
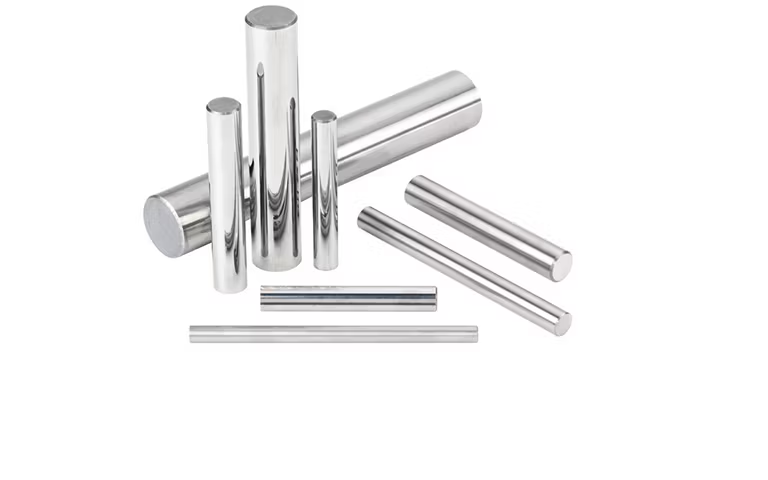
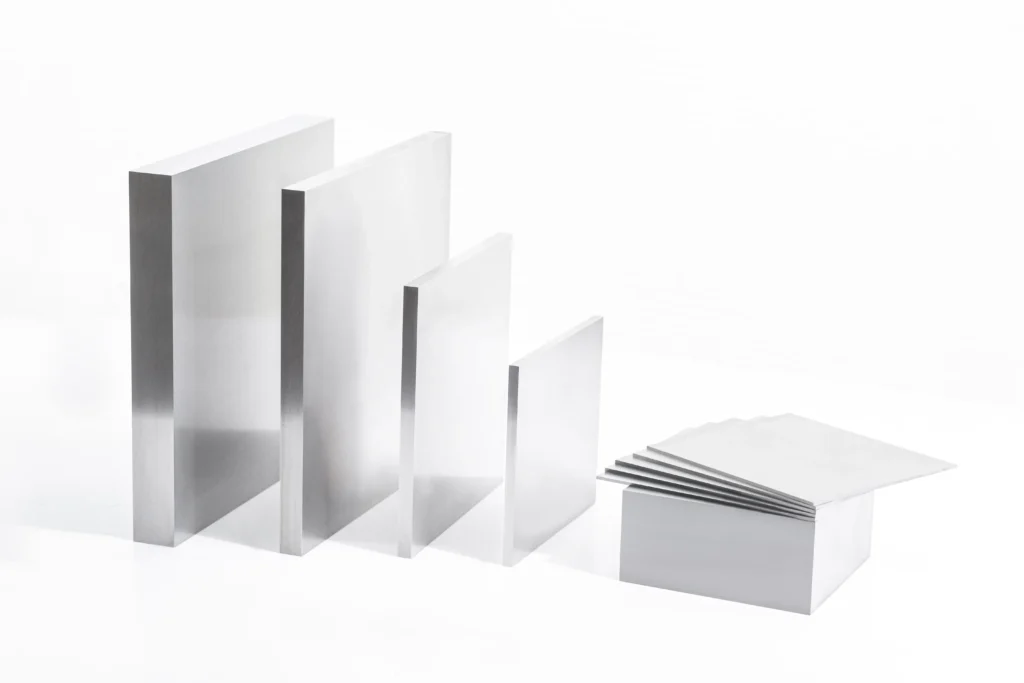
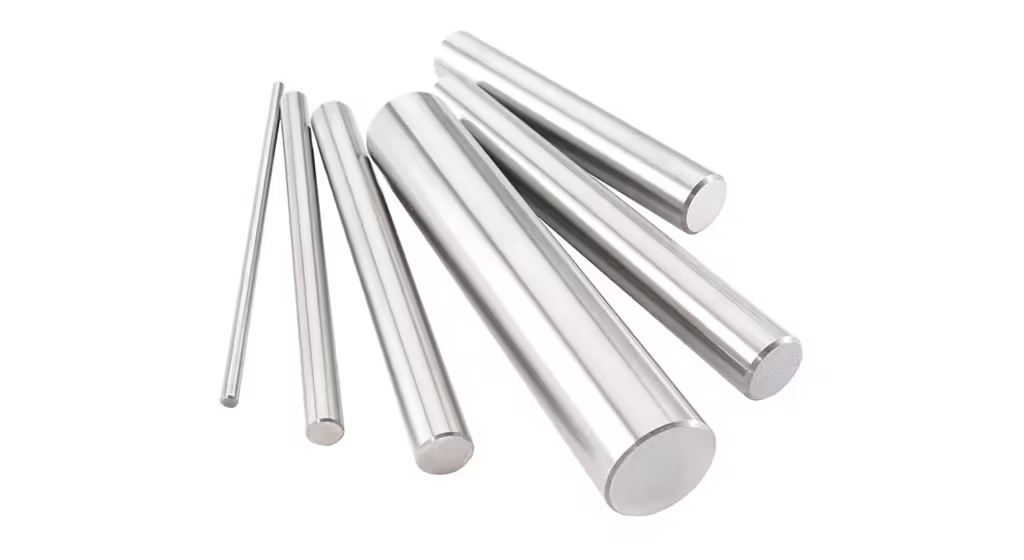
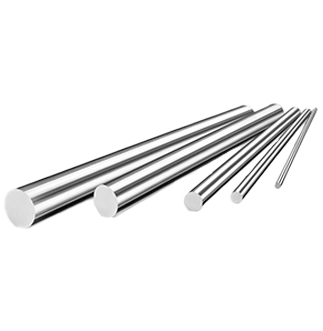
FAQ
Here are some frequently asked questions to address common concerns and provide additional information about our hardmetal carbide preforms.
Q1: What is the typical lead time for orders?
A1: The lead time varies based on order size and customization requirements. Standard orders are usually processed within 2-4 weeks, while custom orders may take longer.
Q2: Can I request specific sizes and shapes?
A2: Yes, we offer customization services to meet your unique needs. Contact our sales team with your specifications, and we will provide a tailored solution.
Q3: How do you ensure the quality of the preforms?
A3: Our hardmetal carbide preforms undergo stringent quality control checks at every production stage. We also provide material certifications and test reports upon request.
Q4: What payment methods are accepted?
A4: We accept various payment methods, including bank transfers, credit cards, and PayPal. Please contact our billing department for more details.
Q5: Do you provide technical support for machining carbide preforms?
A5: Yes, our technical team is available to provide guidance and support for machining and processing our carbide preforms. We can offer recommendations on tools, techniques, and best practices to ensure optimal results.