Welcome to the ultimate guide on H6 polished tungsten carbide rods! Whether you’re in the field of manufacturing, engineering, or just have a keen interest in high-performance materials, you’re in the right place. We’ll dive deep into the world of these incredible rods, exploring everything from their properties to their applications, and providing a comprehensive comparison to help you make informed decisions. So, buckle up and let’s get started!
Overview of H6 Polished Tungsten Carbide Rods
Tungsten carbide rods are a staple in the manufacturing and engineering world due to their unparalleled hardness, strength, and wear resistance. When polished to an H6 tolerance, these rods offer exceptional precision and finish, making them ideal for a wide range of high-demand applications.
Key Features of H6 Polished Tungsten Carbide Rods:
- Unmatched Hardness: Tungsten carbide is one of the hardest materials known, second only to diamond.
- High Wear Resistance: These rods can withstand significant wear and tear, extending their lifespan in demanding environments.
- Precision Finish: The H6 polishing process ensures a smooth, precise surface finish.
- Versatility: Used in various applications, from cutting tools to wear parts.
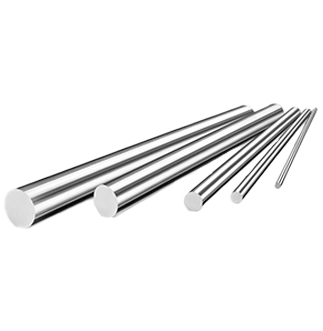
Types of H6 Polished Tungsten Carbide Rods
Let’s explore the different types of H6 polished tungsten carbide rods available on the market. Each type has unique properties tailored to specific applications.
Type | Description |
---|---|
WC-Co Rods | Tungsten carbide rods with cobalt binder, known for their toughness and impact resistance. |
WC-Ni Rods | Tungsten carbide rods with nickel binder, offering excellent corrosion resistance. |
WC-TiC Rods | Tungsten carbide rods with titanium carbide, enhancing wear resistance in abrasive environments. |
WC-TaC Rods | Tungsten carbide rods with tantalum carbide, providing superior high-temperature performance. |
Micrograin WC Rods | Fine-grained tungsten carbide rods, ideal for applications requiring high precision and smooth finishes. |
Ultrafine WC Rods | Ultrafine-grained tungsten carbide rods, offering excellent toughness and strength. |
WC-CoCr Rods | Tungsten carbide rods with cobalt-chromium binder, combining wear resistance with corrosion resistance. |
WC-Mo Rods | Tungsten carbide rods with molybdenum, providing enhanced high-temperature stability. |
WC-VC Rods | Tungsten carbide rods with vanadium carbide, offering improved hardness and wear resistance. |
WC-NbC Rods | Tungsten carbide rods with niobium carbide, providing excellent high-temperature performance. |
Applications of H6 Polished Tungsten Carbide Rods
These rods are highly versatile and find applications in various industries. Here are some common uses:
Application | Description |
---|---|
Cutting Tools | Used in machining applications for cutting, drilling, and milling due to their hardness and precision. |
Wear Parts | Essential in industries where parts are subjected to significant wear and tear, such as mining and oil drilling. |
Aerospace | Utilized in components that require high strength-to-weight ratios and resistance to extreme conditions. |
Automotive | Employed in engine parts and other high-stress components due to their durability. |
Metalworking | Integral in tools and dies for shaping and forming metals. |
Electronics | Used in manufacturing of semiconductors and other electronic components. |
Medical Devices | Applied in surgical instruments and other medical devices requiring precision and durability. |
Renewable Energy | Important in the production of wind turbine components and other renewable energy equipment. |
Construction | Used in heavy machinery and tools for construction due to their robustness. |
Defense | Essential in the manufacture of armor-piercing ammunition and other defense-related equipment. |
Material Properties of H6 Polished Tungsten Carbide Rods
Understanding the material properties is crucial for selecting the right rod for your application. Here are some key properties:
Property | Description |
---|---|
Hardness | Typically ranges between 8.5-9 on the Mohs scale. |
Density | Around 15.63 g/cm³, depending on the composition. |
Tensile Strength | Typically 1500-2500 MPa. |
Young’s Modulus | Approximately 550-700 GPa. |
Fracture Toughness | Ranges from 8-30 MPa·m^1/2, depending on the specific grade. |
Thermal Conductivity | Around 85-110 W/m·K. |
Coefficient of Thermal Expansion | Approximately 4.5-6.5 µm/m·K. |
Electrical Conductivity | Low, similar to other ceramic materials. |
Chemical Resistance | Highly resistant to corrosion and chemical attack. |
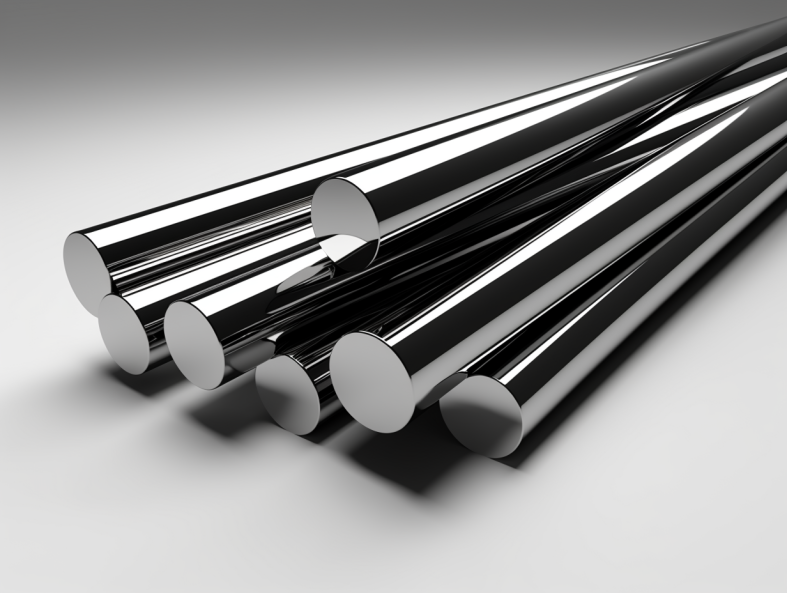
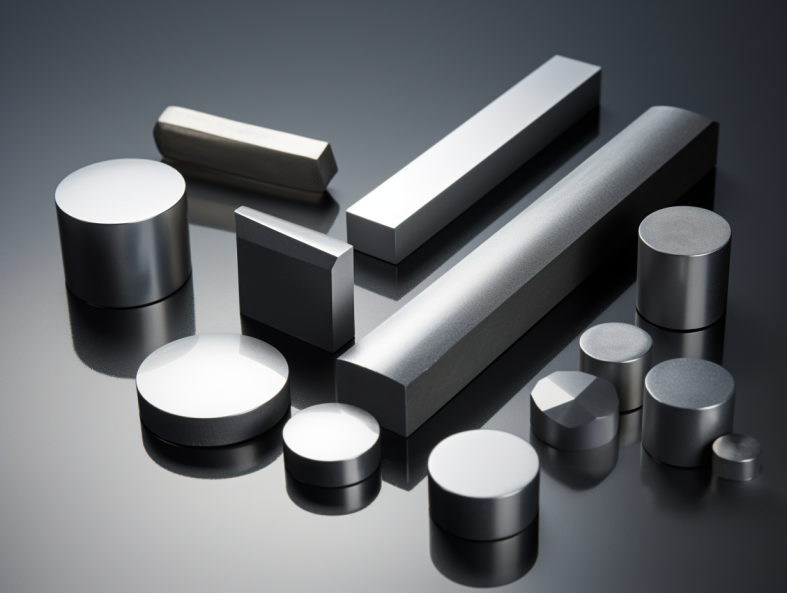
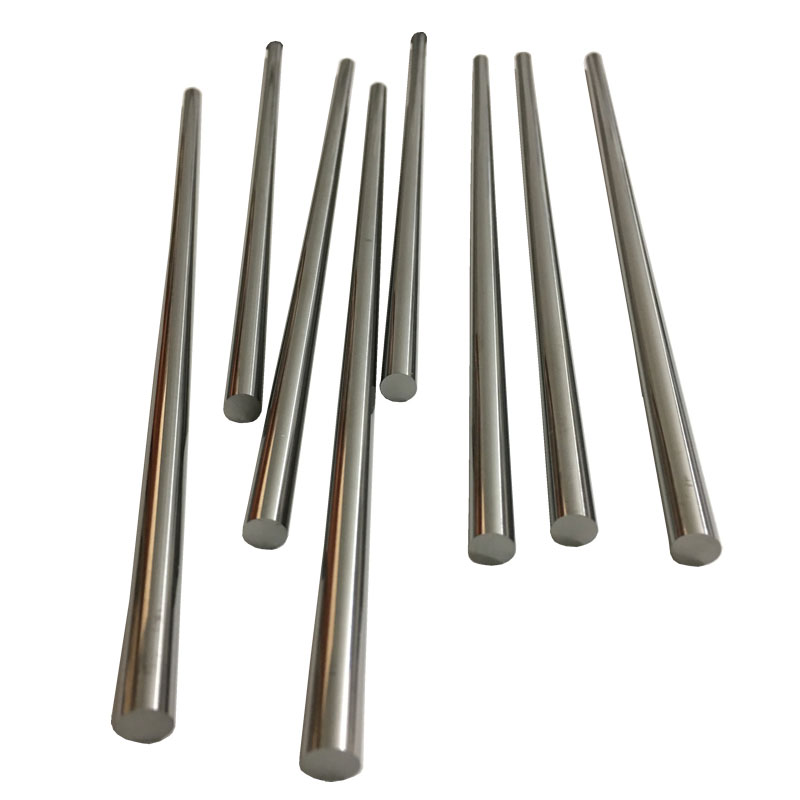
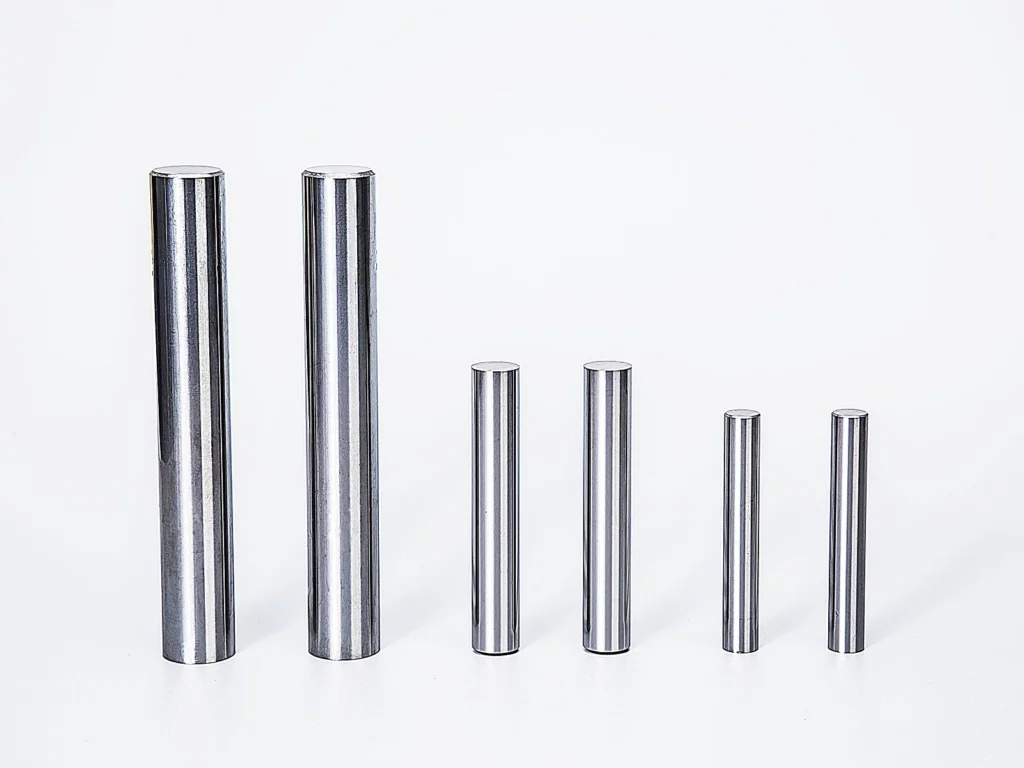
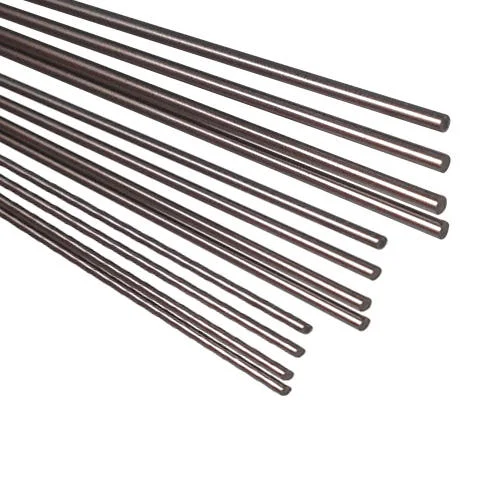
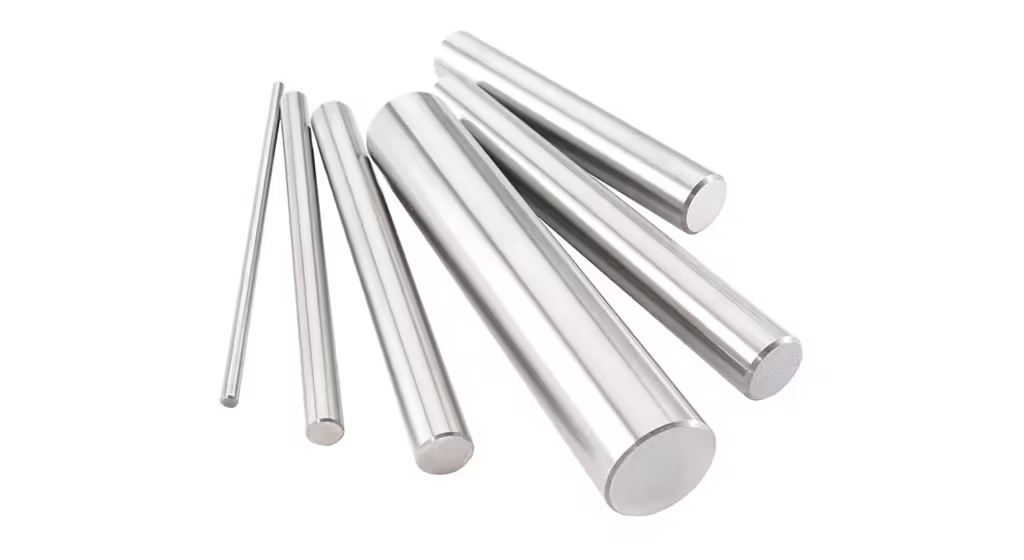
Composition, Properties, and Characteristics
Different grades of tungsten carbide rods have varied compositions and properties tailored for specific uses. Here’s a detailed breakdown:
Grade | Composition | Properties | Characteristics |
---|---|---|---|
WC-Co (6% Co) | 94% WC, 6% Co | High toughness, moderate wear resistance | General-purpose, suitable for impact applications |
WC-Co (10% Co) | 90% WC, 10% Co | Higher toughness, lower hardness | Better impact resistance, less brittle |
WC-Ni (6% Ni) | 94% WC, 6% Ni | Good corrosion resistance | Suitable for corrosive environments |
WC-TiC (10% TiC) | 90% WC, 10% TiC | Enhanced wear resistance | Ideal for abrasive environments |
WC-TaC (5% TaC) | 95% WC, 5% TaC | Excellent high-temperature stability | Suitable for high-temperature applications |
Micrograin WC | Sub-micron WC grains | High precision, smooth finish | Ideal for fine machining and cutting |
Ultrafine WC | Nano-sized WC grains | Superior toughness and strength | Best for precision tools and demanding applications |
WC-CoCr (8% CoCr) | 92% WC, 8% CoCr | Good wear and corrosion resistance | Balanced properties for tough environments |
WC-Mo (5% Mo) | 95% WC, 5% Mo | High-temperature stability | Suitable for hot environments |
WC-VC (3% VC) | 97% WC, 3% VC | Improved hardness and wear resistance | Excellent for heavy-duty applications |
Hardness, Strength, and Wear Resistance
These properties are vital when selecting tungsten carbide rods for specific applications. Here’s a comparative analysis:
Grade | Hardness (HRA) | Tensile Strength (MPa) | Wear Resistance |
---|---|---|---|
WC-Co (6% Co) | 89-92 | 1500-2000 | Moderate |
WC-Co (10% Co) | 87-89 | 1700-2500 | Lower hardness but higher toughness |
WC-Ni (6% Ni) | 88-91 | 1600-2100 | High |
WC-TiC (10% TiC) | 91-94 | 1400-1900 | Very high |
WC-TaC (5% TaC) | 90-92 | 1450-1950 | High |
Micrograin WC | 92-94 | 1300-1800 | High, excellent for precision work |
Ultrafine WC | 93-95 | 1250-1750 | Very high, best for fine machining |
WC-CoCr (8% CoCr) | 90-93 | 1500-2100 | Balanced, good for tough environments |
WC-Mo (5% Mo) | 89-91 | 1600-2200 | High, suitable for high temperatures |
WC-VC (3% VC) | 91-93 | 1550-2050 | Very high, ideal for heavy-duty tasks |
Specifications, Sizes, Shapes, and Standards
When choosing tungsten carbide rods, it’s essential to consider their specifications, sizes, shapes, and the standards they adhere to.
Specification | Size Range | Shapes | Standards |
---|---|---|---|
Diameter | 1mm to 50mm | Round, square, hexagonal | ISO 9001, ASTM B777, JIS H 5201 |
Length | 50mm to 1000mm | Straight, twisted | ISO 2768, DIN 338, GB/T 18338 |
Tolerance | H6, H7, H8 | Solid, hollow | ANSI B94.19, EN 10204, MIL-STD-1388 |
Surface Finish | Polished, ground | Rod, bar, custom shapes | SAE J 437, ASME B94.11M, GB 3088 |
Coating Options | None, TiN, TiAlN, AlCrN | Coated or uncoated | ISO 21988, GOST 2216-76 |
Grade | Various (e.g., K10, K20) | – | ISO 3299, ANSI B212.12 |
Weight | Varies with size and composition | – | AISI M42, ASTM A681 |
Suppliers and Pricing Details
It’s crucial to know where to source these rods and what to expect in terms of pricing.
Supplier | Region | Price Range ($/kg) | Contact Information |
---|---|---|---|
ABC Materials | North America | 60-80 | www.abcmaterials.com, [email protected] |
Global Tungsten | Europe | 65-85 | www.globaltungsten.eu, [email protected] |
Asia Carbide | Asia | 50-70 | www.asiacarbide.com, [email protected] |
Tungsten Pro | North America | 70-90 | www.tungstenpro.com, [email protected] |
Euro Carbide | Europe | 75-95 | www.eurocarbide.com, [email protected] |
Orient Metals | Asia | 55-75 | www.orientmetals.com, [email protected] |
Precision Tools | North America | 80-100 | www.precisiontools.com, [email protected] |
Carbide Solutions | Europe | 60-80 | www.carbidesolutions.eu, [email protected] |
Pro Carbide | Asia | 50-80 | www.procarbide.com, [email protected] |
Elite Tungsten | North America | 70-85 | www.elitetungsten.com, [email protected] |
Selecting the Right H6 Polished Tungsten Carbide Rods
Choosing the right rods can be daunting. Here’s a guide to help you make the best decision:
Selection Criteria | Considerations |
---|---|
Application | Determine the specific application (e.g., cutting, drilling, wear parts). |
Material Properties | Consider the hardness, toughness, and wear resistance required for your application. |
Size and Shape | Ensure the rod’s size and shape match your equipment and project requirements. |
Coating Options | Decide if a coated rod (e.g., TiN, TiAlN) will provide additional benefits like increased lifespan. |
Supplier Reputation | Choose reputable suppliers known for quality and reliability. |
Budget | Balance cost with performance needs; higher initial costs may save money in the long run through durability. |
Industry Standards | Ensure the rods meet relevant industry standards and certifications. |
Delivery Time | Consider lead times and availability to meet your project deadlines. |
Advantages and Limitations of H6 Polished Tungsten Carbide Rods
Understanding the pros and cons can help you make an informed decision:
Advantages | Limitations |
---|---|
Superior Hardness | Brittle Nature: Can be prone to chipping or breaking under extreme impact. |
High Wear Resistance | High Cost: More expensive than other materials like steel. |
Precision Finish | Difficult to Machine: Requires specialized equipment for shaping and forming. |
Versatility | Heavy Weight: Higher density than some alternative materials. |
Excellent Temperature Stability | Limited Flexibility: Less flexible compared to softer materials. |
Corrosion Resistance | Complex Production Process: Manufacturing can be more complex and time-consuming. |
Longevity: Long-lasting in demanding applications. | Requires Skilled Handling: Handling and installation need expertise. |
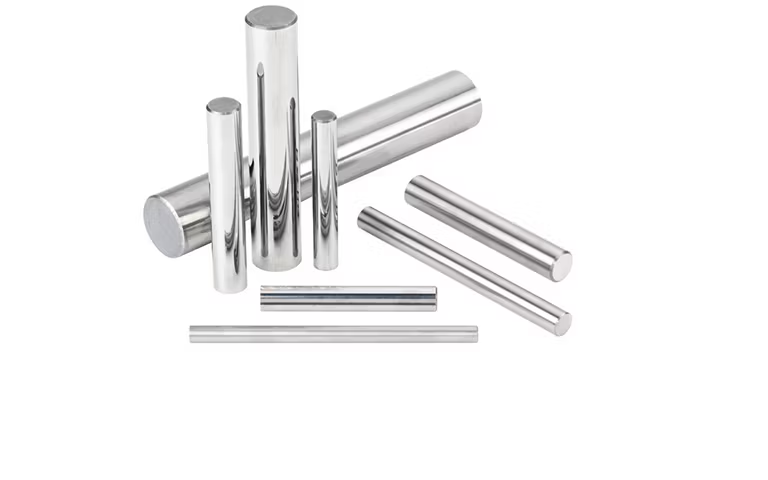
FAQ
What are H6 polished tungsten carbide rods used for?
H6 polished tungsten carbide rods are used in various applications, including cutting tools, wear parts, aerospace components, automotive parts, metalworking tools, electronics, medical devices, renewable energy equipment, construction tools, and defense-related equipment.
How are H6 polished tungsten carbide rods manufactured?
These rods are manufactured through powder metallurgy, where tungsten carbide powder is mixed with a binder (like cobalt or nickel), compacted, and sintered at high temperatures to form a dense, solid rod. The rods are then polished to achieve an H6 tolerance.
What is the significance of the H6 tolerance in these rods?
H6 tolerance refers to the precision level of the rod’s diameter. It ensures a high level of accuracy and a smooth surface finish, which is crucial for applications requiring precise measurements and minimal friction.
How do I select the right tungsten carbide rod for my application?
Consider factors such as the specific application, required material properties (hardness, toughness, wear resistance), size and shape of the rod, coating options, supplier reputation, budget, industry standards, and delivery time.
What are the advantages of using tungsten carbide rods over other materials?
Tungsten carbide rods offer superior hardness, high wear resistance, excellent temperature stability, precision finish, versatility, and long lifespan compared to materials like steel or ceramics.
Can tungsten carbide rods be customized?
Yes, tungsten carbide rods can be customized in terms of size, shape, composition, and coatings to meet specific application requirements.
Are there any special handling or storage requirements for tungsten carbide rods?
Due to their brittleness, tungsten carbide rods should be handled with care to avoid chipping or breaking. They should be stored in a dry, cool place to prevent any potential corrosion, especially if they have not been coated.
How do tungsten carbide rods compare to steel rods?
Tungsten carbide rods are much harder and more wear-resistant than steel rods. They offer better performance in high-stress and high-temperature applications. However, they are also more expensive and can be more brittle compared to steel.
What is the typical lifespan of a tungsten carbide rod?
The lifespan of a tungsten carbide rod depends on the application and operating conditions but is generally much longer than that of steel or other materials due to its superior hardness and wear resistance.
Can tungsten carbide rods be recycled?
Yes, tungsten carbide rods can be recycled. The material can be reclaimed and reused in the production of new rods or other tungsten carbide products, making it an environmentally friendly option.