Overview of H6 Carbide Rods
So, you’ve heard about H6 carbide rods and you’re curious about what makes them special, right? Well, you’re in the right place! H6 carbide rods are essential components in the manufacturing world, known for their exceptional hardness, wear resistance, and ability to withstand high temperatures. These rods are used in a variety of applications, from cutting tools to mechanical parts. Let’s dive into the nitty-gritty details and explore everything you need to know about H6 carbide rods.
What Exactly are H6 Carbide Rods?
H6 carbide rods are cylindrical rods made from tungsten carbide, often with additional metallic powders to enhance specific properties. Tungsten carbide is a compound formed by tungsten and carbon atoms. It’s as hard as nails—literally! The “H6” denotes a specific tolerance class, indicating precision and quality in the manufacturing process.
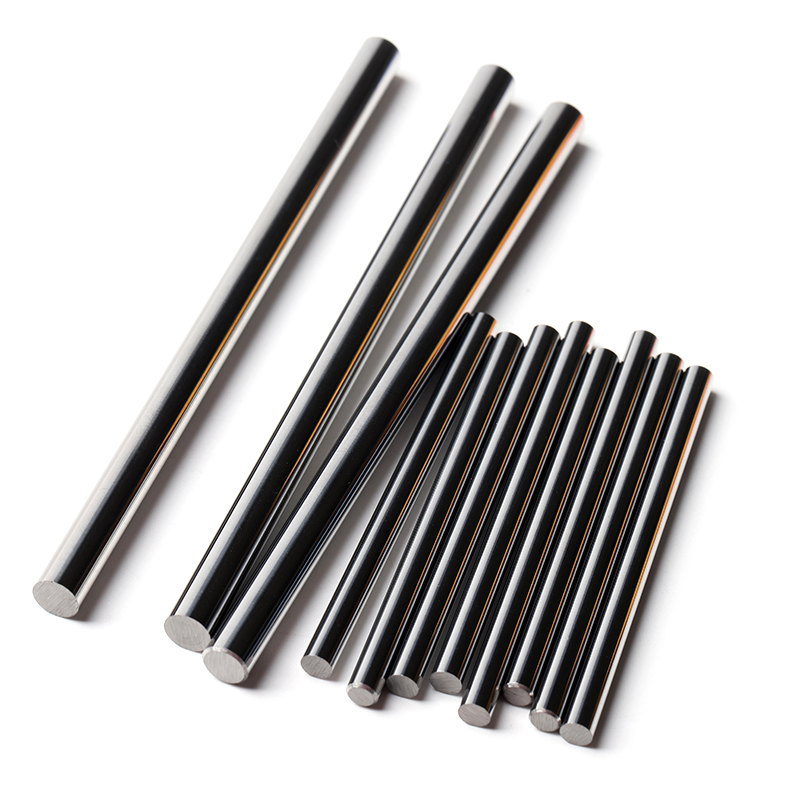
The Production Process of H6 Carbide Rods
Ever wondered how these rods are made? The production process involves several stages, each critical in ensuring the final product meets stringent quality standards. Here’s a breakdown of the steps:
- Powder Mixing: Different metal powders, including tungsten carbide and cobalt, are mixed to create a homogeneous blend.
- Pressing: The powder mixture is pressed into rod shapes under high pressure.
- Sintering: These pressed rods are heated in a sintering furnace, bonding the particles together and achieving the desired density and hardness.
- Grinding and Polishing: The rods are then ground and polished to achieve precise dimensions and a smooth finish.
- Inspection: Finally, each rod is inspected for quality assurance, ensuring they meet the H6 tolerance standards.
Key Specifications of H6 Carbide Rods
To truly understand H6 carbide rods, it’s crucial to look at their specifications. These specifications include composition, properties, characteristics, and more. Here’s a detailed table for your reference:
Specification | Description |
---|---|
Material Composition | Tungsten Carbide (WC) with Cobalt (Co) binder |
Hardness (HRA) | 89-92 |
Density (g/cm³) | 14.2-15.2 |
Tolerance Class | H6 |
Grain Size | Submicron to fine |
Flexural Strength (MPa) | 2800-3000 |
Thermal Conductivity (W/m·K) | 70-100 |
Melting Point (°C) | 2870 |
Applications of H6 Carbide Rods
These rods aren’t just for show—they have a wide range of applications due to their durability and resistance to wear. Let’s take a look at where they shine:
Application | Description |
---|---|
Cutting Tools | Used in drills, end mills, and reamers for their hardness and wear resistance. |
Industrial Machining | Essential for high-precision machining tasks in various industries. |
Mining Tools | Employed in mining equipment for their robustness and ability to cut through tough materials. |
Wear Parts | Utilized in components that are subjected to high wear and tear. |
Aerospace | Used in aerospace components for their high strength-to-weight ratio. |
Automotive | Critical in manufacturing automotive parts that require high precision. |
Medical Instruments | Employed in surgical instruments due to their biocompatibility and precision. |
Construction | Used in construction tools for their durability and resistance to extreme conditions. |
Jewelry | Sometimes used in high-end jewelry for their scratch resistance and unique finish. |
Electronics | Utilized in electronic devices for their thermal and electrical conductivity. |
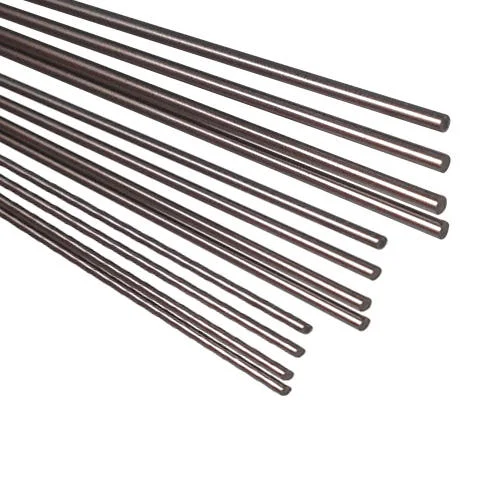
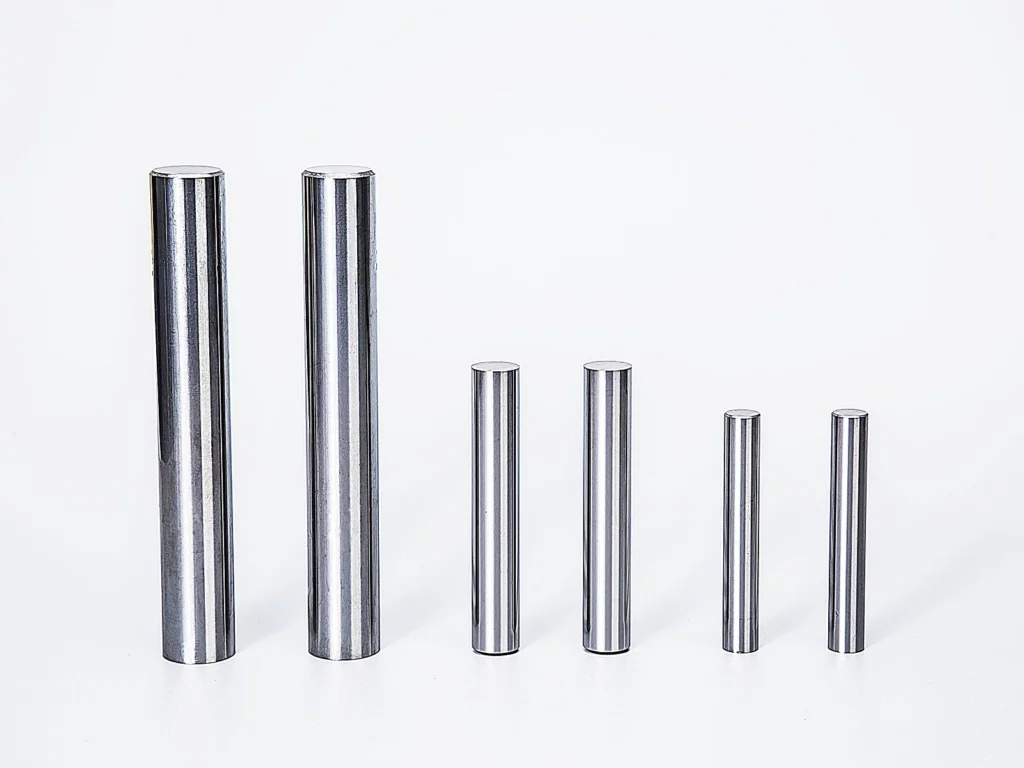
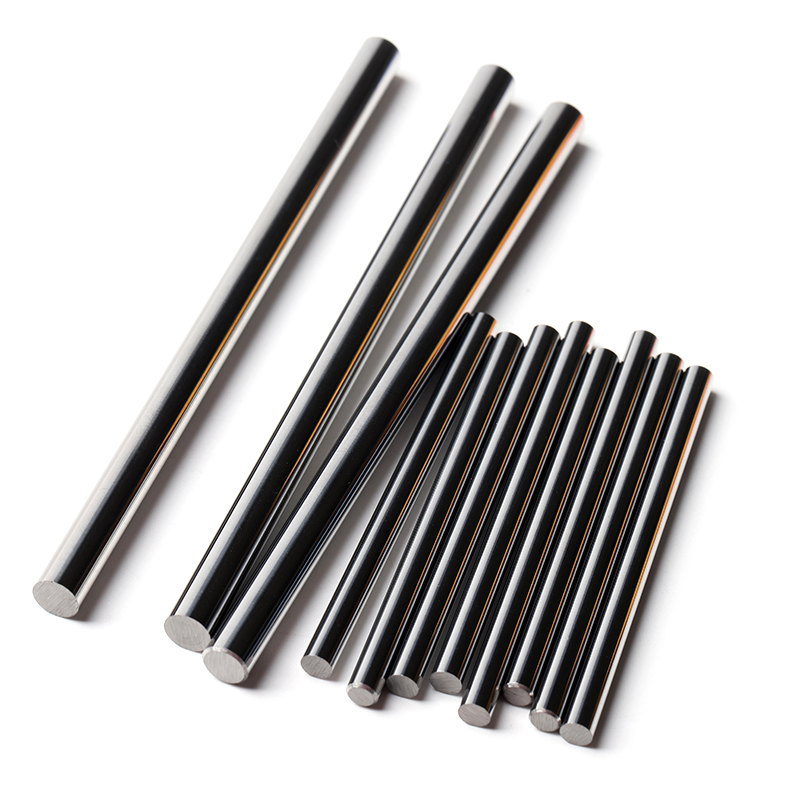
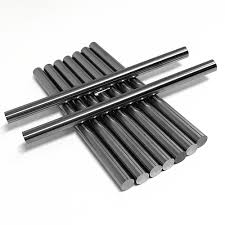
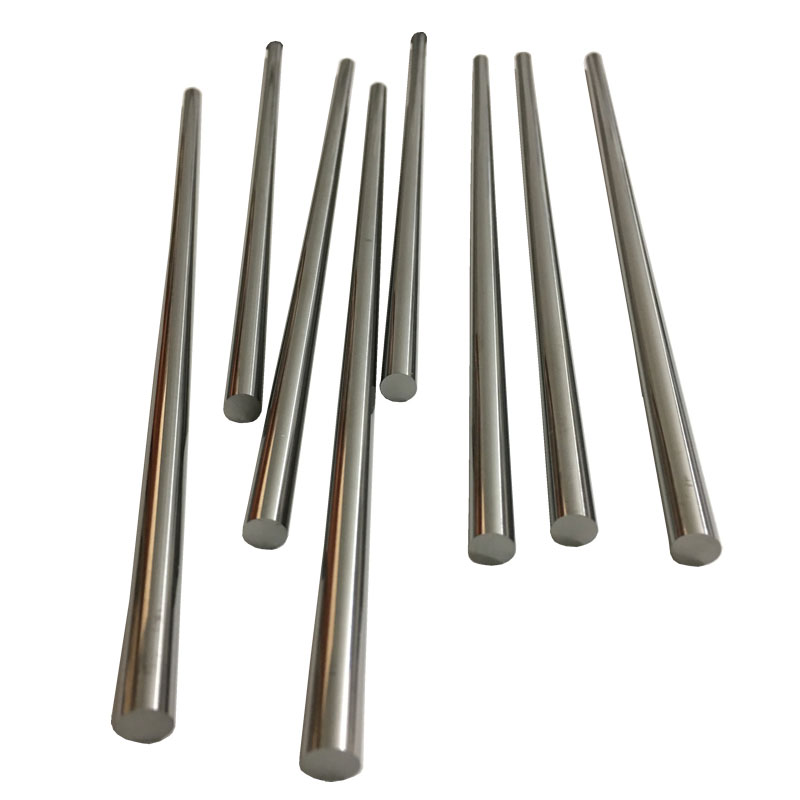
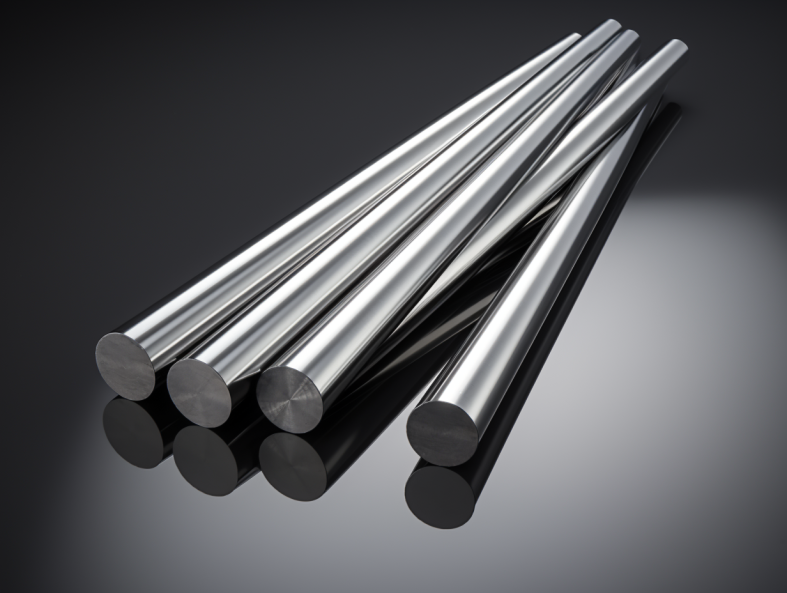
Types of Metal Powders Used in H6 Carbide Rods
Now, let’s delve into the specific metal powders that give H6 carbide rods their remarkable properties. Here are ten different metal powders commonly used:
- Tungsten Carbide (WC): The primary component, providing hardness and wear resistance.
- Cobalt (Co): Acts as a binder, enhancing toughness.
- Titanium Carbide (TiC): Improves hardness and oxidation resistance.
- Tantalum Carbide (TaC): Increases high-temperature strength and hardness.
- Nickel (Ni): Sometimes used as an alternative binder for improved corrosion resistance.
- Chromium Carbide (CrC): Adds corrosion resistance and wear resistance.
- Vanadium Carbide (VC): Enhances hardness and cutting edge retention.
- Molybdenum Carbide (MoC): Improves toughness and thermal conductivity.
- Hafnium Carbide (HfC): Provides high melting point and hardness.
- Niobium Carbide (NbC): Enhances wear resistance and strength at high temperatures.
Comparing H6 Carbide Rods to Other Grades
So, how do H6 carbide rods stack up against other grades? Let’s compare!
Grade | Hardness (HRA) | Density (g/cm³) | Applications | Advantages | Limitations |
---|---|---|---|---|---|
H6 | 89-92 | 14.2-15.2 | Cutting tools, machining, wear parts | High precision, excellent wear resistance | Can be more expensive due to precision |
H5 | 87-90 | 14.0-15.0 | General machining, mining tools | Good wear resistance, slightly less costly | Slightly lower precision |
H7 | 90-93 | 14.3-15.3 | High-precision machining, aerospace | Superior hardness, very high wear resistance | Can be brittle under extreme stress |
H10 | 86-89 | 13.8-14.8 | Industrial tools, construction | Cost-effective, good general-purpose properties | Lower precision compared to H6 and H7 |
Specifications, Sizes, Grades, and Standards of H6 Carbide Rods
When it comes to H6 carbide rods, one size doesn’t fit all. They come in various sizes and grades, meeting different standards. Here’s a detailed table:
Specification | Details |
---|---|
Diameter (mm) | 1-25 |
Length (mm) | 50-330 |
Grade | K10, K20, K30 |
Standard | ISO, ASTM, DIN |
Finish | Ground, polished |
Tolerance | H6 |
Suppliers and Pricing Details for H6 Carbide Rods
Finding the right supplier is crucial. Here are some well-known suppliers along with pricing details:
Supplier | Location | Price (per kg) | Minimum Order Quantity | Lead Time |
---|---|---|---|---|
Kennametal | USA | $75-$100 | 5 kg | 2-4 weeks |
Sandvik | Sweden | $80-$105 | 10 kg | 3-5 weeks |
Zhuzhou Cemented Carbide | China | $60-$90 | 20 kg | 4-6 weeks |
Mitsubishi Materials | Japan | $85-$110 | 5 kg | 2-4 weeks |
Ceratizit | Luxembourg | $70-$95 | 10 kg | 3-5 weeks |
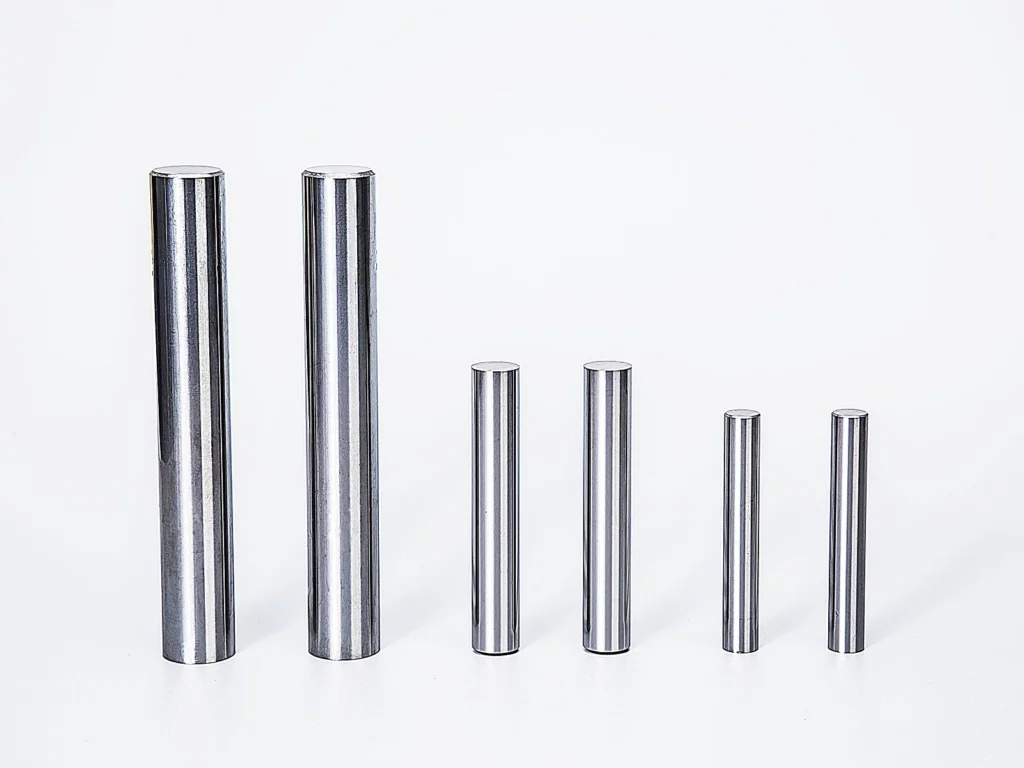
Pros and Cons of H6 Carbide Rods
Every product has its strengths and weaknesses. Let’s weigh the pros and cons of H6 carbide rods.
Advantages | Disadvantages |
---|---|
Exceptional hardness | Can be more expensive |
High wear resistance | May be brittle under extreme conditions |
Excellent thermal conductivity | Requires precise manufacturing processes |
Long lifespan in demanding applications | Slightly heavier compared to some alternatives |
FAQs
Question | Answer |
---|---|
What are H6 carbide rods used for? | They are used in cutting tools, industrial machining, mining tools, and more. |
Why are they called H6? | The “H6” denotes a specific tolerance class, indicating high precision and quality. |
What is the main material in H6 carbide rods? | Tungsten carbide, often with a cobalt binder. |
How are H6 carbide rods made? | Through a process of powder mixing, pressing, sintering, grinding, and polishing. |
What are the advantages of using H6 carbide rods? | High hardness, wear resistance, and excellent thermal conductivity. |