When it comes to precision and durability in machining, few materials can match the capabilities of tungsten carbide. Known for its hardness and resistance to wear, tungsten carbide is often used in applications where robustness and longevity are critical. One of the fascinating aspects of this material is the ability to grind tungsten carbide rods with holes. This article delves into the nitty-gritty of grinding tungsten carbide rod with hole, covering everything from metal powder models to applications, specifications, and supplier details.
Overview of Grinding Tungsten Carbide Rod with Hole
Tungsten carbide is a composite material made of tungsten and carbon. This material is renowned for its hardness, comparable to diamonds, and is used in various industrial applications. Grinding tungsten carbide rods with holes involves using specific grinding techniques and equipment to achieve the desired precision and finish.
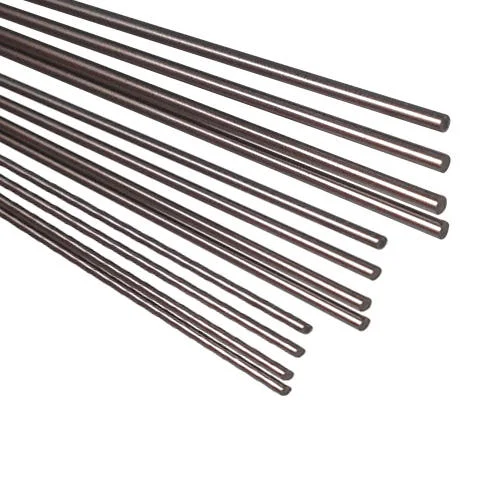
Composition and Properties of Tungsten Carbide Rod with Hole
To understand why tungsten carbide is so effective, let’s take a look at its composition and properties. This table provides a detailed breakdown of the key elements and characteristics of tungsten carbide rods with holes.
Composition and Properties Table
Element | Percentage | Property | Description |
---|---|---|---|
Tungsten (W) | 70-97% | Hardness | Extremely hard, high melting point, provides toughness. |
Carbon (C) | 3-30% | Abrasion Resistance | Enhances hardness and wear resistance. |
Cobalt (Co) | 0-10% | Binding Agent | Acts as a binder to give the material its toughness and shock resistance. |
Chromium (Cr) | 0-5% | Corrosion Resistance | Adds corrosion resistance and prevents oxidation. |
Nickel (Ni) | 0-5% | Strength and Durability | Improves toughness and durability. |
Vanadium (V) | 0-2% | Grain Growth Control | Controls grain growth to maintain the strength of the composite material. |
Production Process of Grinding Tungsten Carbide Rod with Hole
Grinding tungsten carbide rods with holes requires precision and expertise. The process typically involves the following steps:
- Material Selection: Choosing high-quality tungsten carbide rods.
- Pre-Grinding Preparation: Preparing the rods by cutting them to the required size and drilling the holes.
- Grinding: Using diamond grinding wheels to grind the rods to the precise dimensions.
- Finishing: Polishing the rods to achieve the desired surface finish and ensuring the holes are smooth and accurate.
- Quality Control: Inspecting the finished rods for any defects or inaccuracies.
Applications of Grinding Tungsten Carbide Rod with Hole
Tungsten carbide rods with holes are used in a variety of applications due to their unique properties. This table outlines some of the key applications and their benefits.
Applications Table
Application | Industry | Benefits |
---|---|---|
Cutting Tools | Manufacturing | High precision, long-lasting, and efficient cutting performance. |
Wear Parts | Mining and Drilling | Exceptional wear resistance, reducing downtime and maintenance costs. |
Molds and Dies | Automotive and Aerospace | Durable and able to withstand high pressures and temperatures. |
Medical Instruments | Medical | High precision and biocompatibility for surgical instruments and implants. |
Precision Machining Components | Engineering | Ensures accuracy and longevity in various engineering applications. |
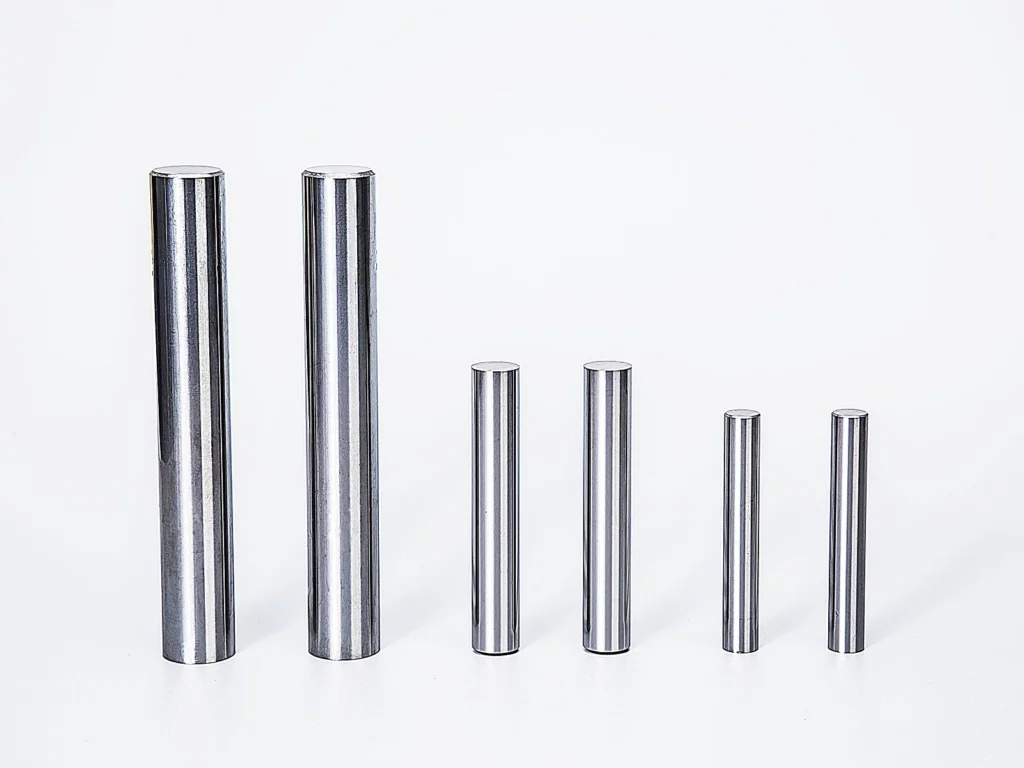
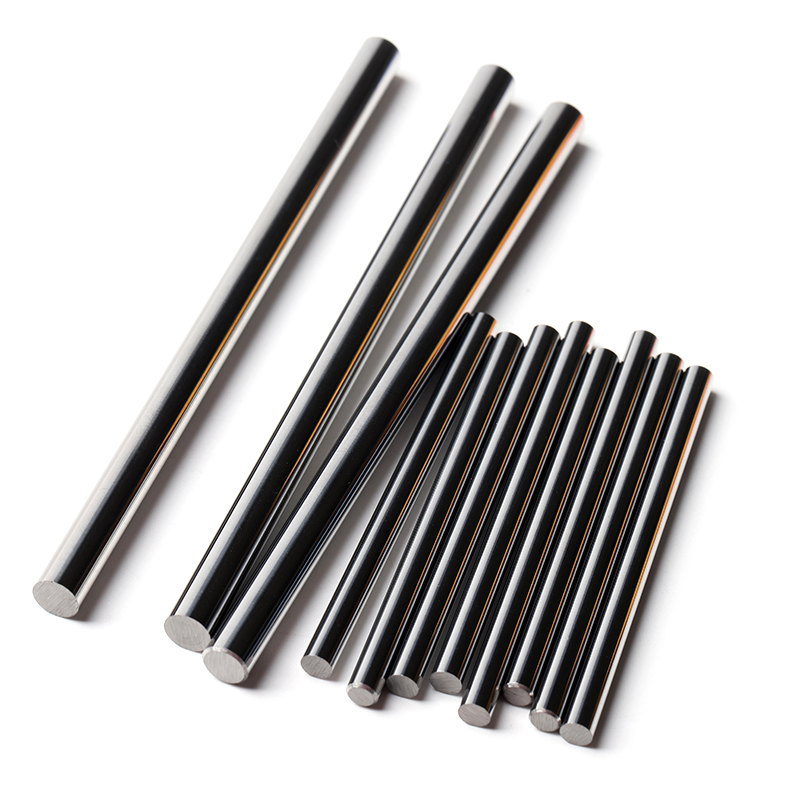
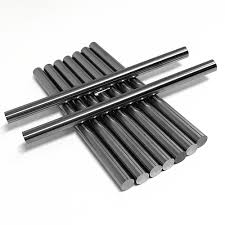
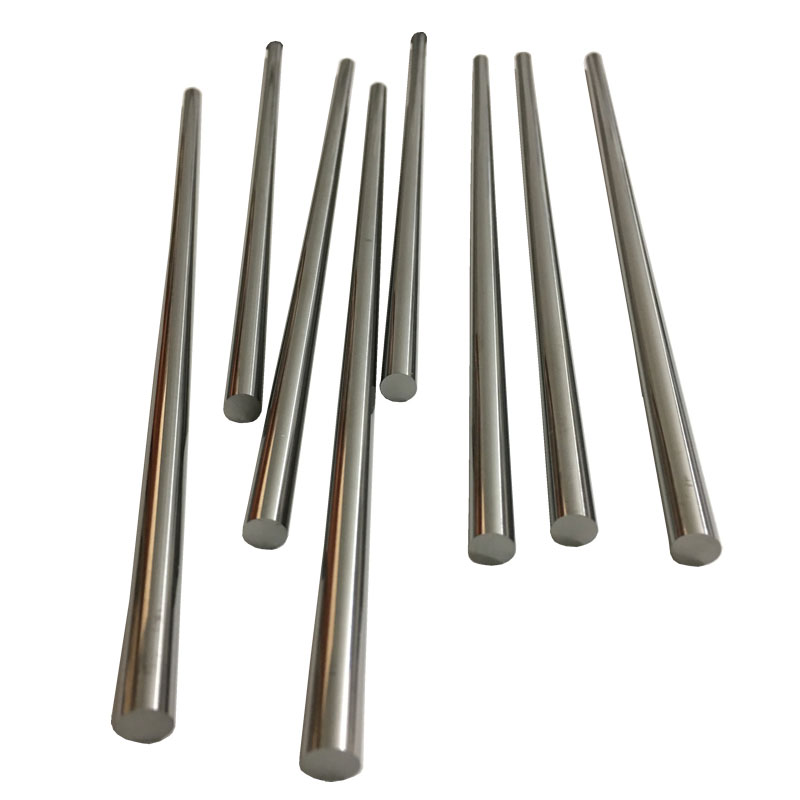
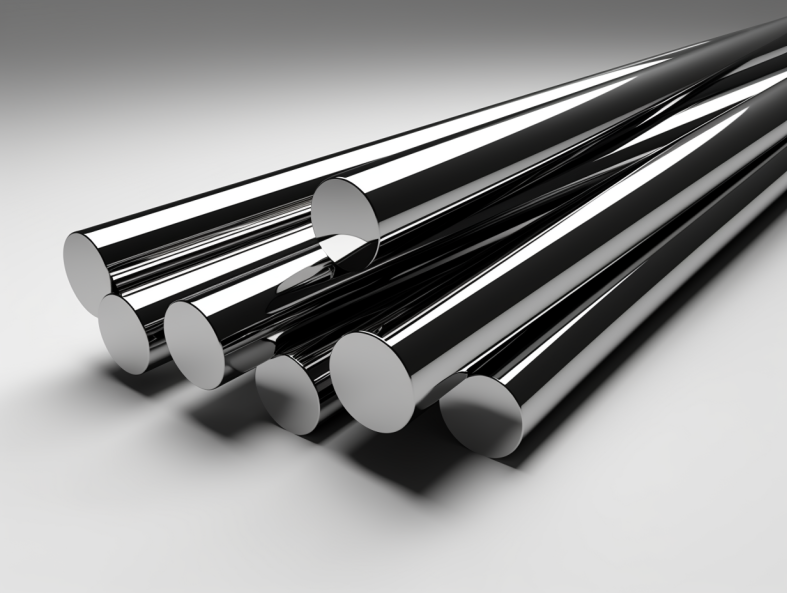
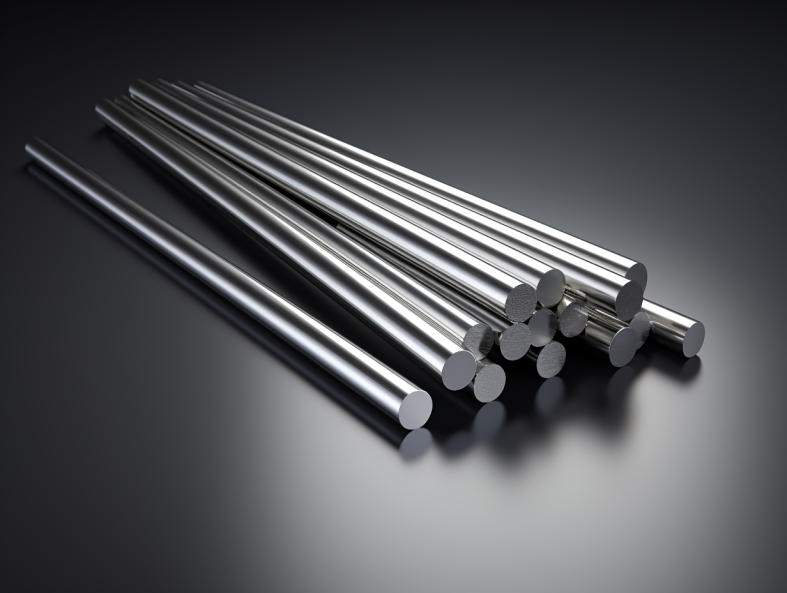
Specifications, Sizes, Grades, and Standards
Tungsten carbide rods with holes come in various specifications, sizes, grades, and standards. This table provides an overview of the available options.
Specifications Table
Specification | Details |
---|---|
Diameter | Ranges from 1mm to 50mm |
Hole Diameter | Typically ranges from 0.5mm to 20mm |
Length | Can be customized, commonly between 50mm to 500mm |
Grades | Various grades including YG6, YG8, YG10, YG15, etc. |
Standards | ISO, ASTM, JIS standards |
Surface Finish | Ground, polished, or unpolished |
Tolerance | High precision tolerances typically within ±0.005mm |
Density | 14.5 – 15.1 g/cm³ |
Suppliers and Pricing Details
Finding the right supplier for tungsten carbide rods with holes is crucial. This table lists some key suppliers and provides an overview of their pricing.
Suppliers and Pricing Table
Supplier | Location | Pricing | Contact Details |
---|---|---|---|
XYZ Tungsten Carbide Co. | USA | $50 – $200 per rod, depending on size | [email protected] |
ABC Metals | Germany | €40 – €180 per rod, depending on size | [email protected] |
Tungsten Experts Ltd. | China | ¥300 – ¥1500 per rod, depending on size | [email protected] |
Global Carbide Solutions | UK | £45 – £190 per rod, depending on size | [email protected] |
Industrial Carbide Inc. | Canada | CAD $55 – CAD $210 per rod, depending on size | [email protected] |
Comparing Pros and Cons of Tungsten Carbide Rod with Hole
When considering tungsten carbide rods with holes, it’s essential to weigh the advantages and limitations. This table highlights the pros and cons.
Pros and Cons Table
Aspect | Pros | Cons |
---|---|---|
Hardness | Extremely hard, second only to diamonds | Can be brittle under extreme stress |
Wear Resistance | High resistance to wear and tear | Difficult to machine |
Precision | Can be ground to very tight tolerances | Requires specialized equipment and expertise |
Durability | Long-lasting in various industrial applications | Higher initial cost compared to other materials |
Versatility | Used in a wide range of industries | Limited flexibility once manufactured |
Corrosion Resistance | Resists oxidation and corrosion in harsh environments | May require specific treatments for certain applications |
Key Metal Powder Models for Tungsten Carbide Rods with Holes
Selecting the right metal powder model is crucial for the performance and longevity of tungsten carbide rods with holes. Here are ten specific models with their descriptions:
- YG6: Contains 6% cobalt and offers excellent hardness and wear resistance. Ideal for general machining.
- YG8: With 8% cobalt, this model provides a balance between hardness and toughness, suitable for mining and drilling applications.
- YG10: Contains 10% cobalt, enhancing toughness. Used for cutting tools requiring high precision.
- YG15: Offers 15% cobalt for increased toughness and durability. Perfect for heavy-duty cutting and wear parts.
- YW1: A versatile grade with tungsten carbide and cobalt, providing good wear resistance and toughness.
- YW2: Similar to YW1 but with slightly higher cobalt content for improved toughness.
- K10: Fine-grained tungsten carbide ideal for precision machining and cutting tools.
- K20: Offers a balance between hardness and toughness, used in metal forming and cutting.
- C2: Known for its general-purpose applications, providing good wear resistance and impact strength.
- C3: Similar to C2 but with higher wear resistance, used for non-ferrous and non-metallic materials.
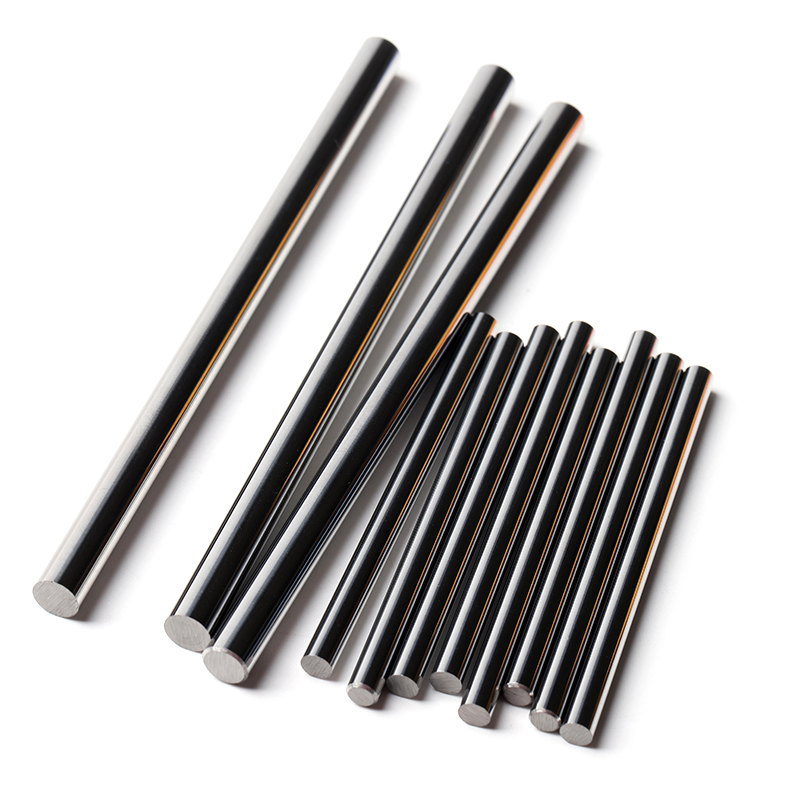
FAQ
Here are some frequently asked questions regarding tungsten carbide rods with holes:
Question | Answer |
---|---|
What is tungsten carbide? | Tungsten carbide is a composite material made of tungsten and carbon, known for its hardness and durability. |
Why use tungsten carbide rods with holes? | They offer high precision, wear resistance, and durability, making them ideal for various industrial applications. |
How are the holes in tungsten carbide rods made? | The holes are typically drilled using specialized equipment before the grinding process. |
What industries use tungsten carbide rods with holes? | They are used in manufacturing, mining, automotive, aerospace, medical, and engineering industries. |
What are the common grades of tungsten carbide? | Common grades include YG6, YG8, YG10, YG15, YW1, YW2, K10, K20, C2, and C3. |
How to select the right tungsten carbide rod? | Consider the application requirements such as hardness, toughness, wear resistance, and the specific grades suitable for those needs. |
What are the challenges in grinding tungsten carbide rods with holes? | The material’s hardness makes it difficult to machine, requiring specialized equipment and expertise. |