When it comes to the world of industrial manufacturing, precision and durability are key. One such product that stands out in this regard is the grinding carbide strip. These essential components are pivotal in various machining processes, offering unmatched hardness and wear resistance. Whether you’re in the business of manufacturing cutting tools, molds, or any heavy-duty equipment, understanding grinding carbide strips and selecting the right manufacturer is crucial.
In this comprehensive guide, we’ll dive deep into the world of grinding carbide strips, exploring everything from their types and applications to material properties and how to choose the right manufacturer. Ready to get started? Let’s embark on this journey!
Overview of Grinding Carbide Strips
Grinding carbide strips are integral components used in a variety of industrial applications, known for their exceptional hardness and wear resistance. Typically made from tungsten carbide powder, these strips are used in the production of cutting tools, wear-resistant tools, and many other high-precision instruments.
These strips offer several benefits, including:
- Exceptional Hardness: Making them ideal for cutting and grinding applications.
- High Wear Resistance: Ensuring longevity and durability even under intense use.
- Versatility: Suitable for a wide range of industrial applications.
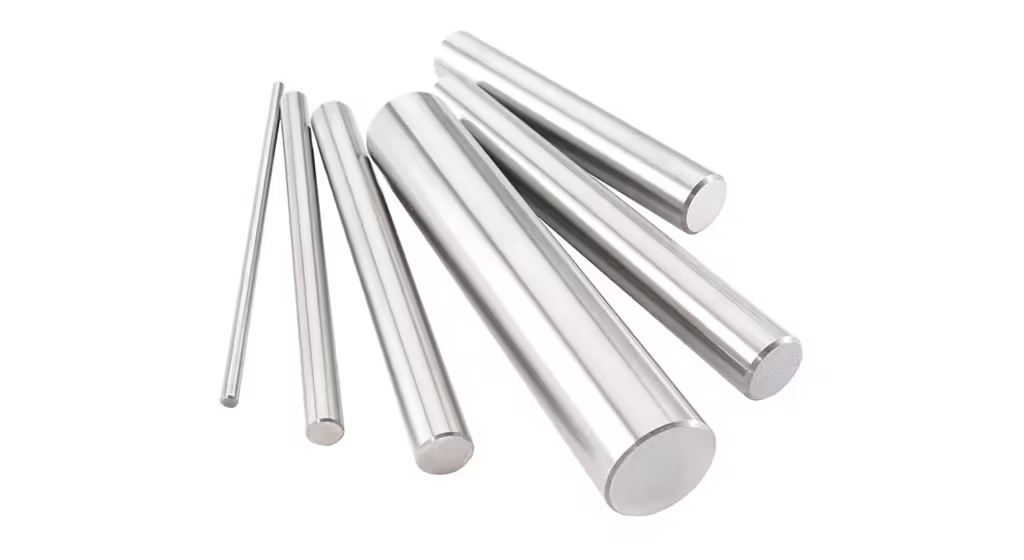
Types of Grinding Carbide Strips
Type | Description |
---|---|
Tungsten Carbide Strips | Made from tungsten carbide powder, known for high hardness and wear resistance. |
Cobalt-Bonded Strips | Carbide strips with a cobalt binder, offering enhanced toughness and wear resistance. |
Nickel-Bonded Strips | Utilize a nickel binder for improved corrosion resistance and toughness. |
Vanadium Carbide Strips | Contain vanadium, enhancing the hardness and heat resistance of the strips. |
Titanium Carbide Strips | Incorporate titanium for increased hardness and oxidation resistance. |
Multilayered Carbide Strips | Feature multiple layers of different carbides for tailored properties and enhanced performance. |
High-Precision Strips | Specifically manufactured for high-precision applications in the aerospace and automotive industries. |
Standard Carbide Strips | General-purpose strips used in a variety of applications. |
Customized Carbide Strips | Tailored to specific requirements of the application or machinery. |
Reinforced Carbide Strips | Have additional reinforcement for increased strength and durability. |
Applications of Grinding Carbide Strips
Application | Description |
---|---|
Cutting Tools Manufacturing | Used in the production of cutting tools like saw blades, drills, and milling cutters. |
Wear-Resistant Tools | Ideal for tools that experience high wear and tear, such as mining and drilling equipment. |
Mold Making | Essential in the creation of molds for casting and shaping materials. |
Aerospace Industry | Utilized in the manufacturing of high-precision components for aircraft. |
Automotive Industry | Used in the production of durable and precise automotive parts. |
Woodworking Tools | Perfect for tools used in woodworking due to their sharpness and durability. |
Metalworking | Employed in various metalworking applications for cutting and shaping metals. |
Oil and Gas Industry | Used in the harsh environments of oil and gas extraction and processing. |
Medical Equipment | Utilized in the production of precise and durable medical instruments and devices. |
Renewable Energy Sector | Applied in the creation of components for renewable energy systems, like wind turbines and solar panels. |
Material Properties of Grinding Carbide Strips
Property | Description |
---|---|
Hardness | Extremely high, often above 90 HRA (Rockwell Hardness Scale). |
Wear Resistance | Excellent, ensuring longevity even under severe conditions. |
Toughness | High, especially in cobalt or nickel-bonded strips, preventing breakage and chipping. |
Heat Resistance | Can withstand high temperatures without losing hardness, crucial for high-speed cutting applications. |
Corrosion Resistance | Nickel-bonded strips provide enhanced resistance to corrosion, suitable for harsh environments. |
Density | Generally ranges between 14.5 to 15.5 g/cm³, contributing to their stability and rigidity. |
Thermal Conductivity | Efficient heat dissipation, preventing overheating during use. |
Flexural Strength | High flexural strength, providing resilience against bending and deformation. |
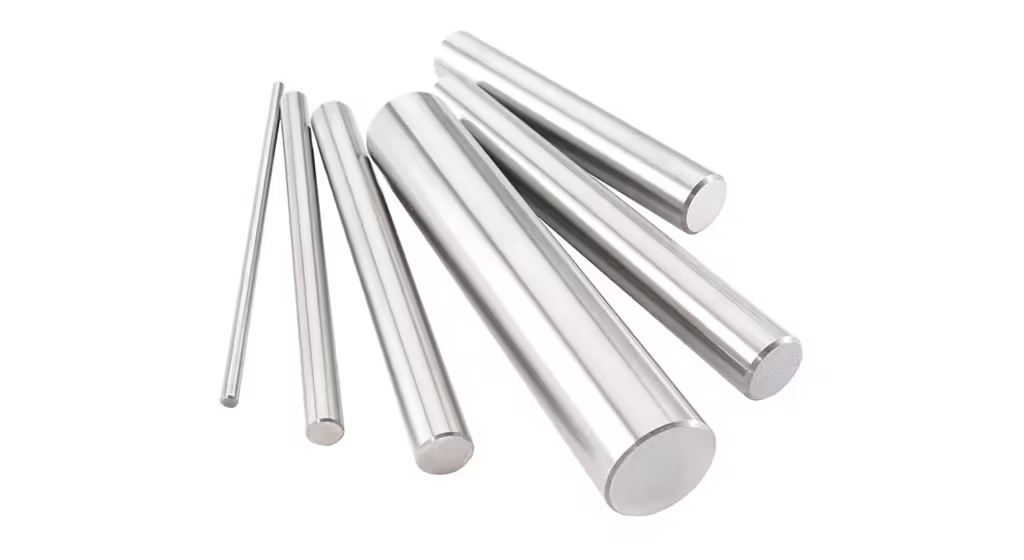
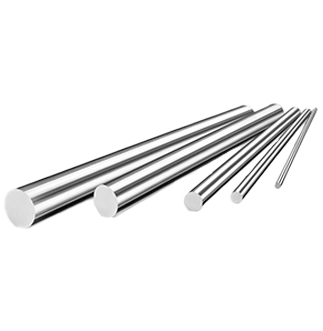
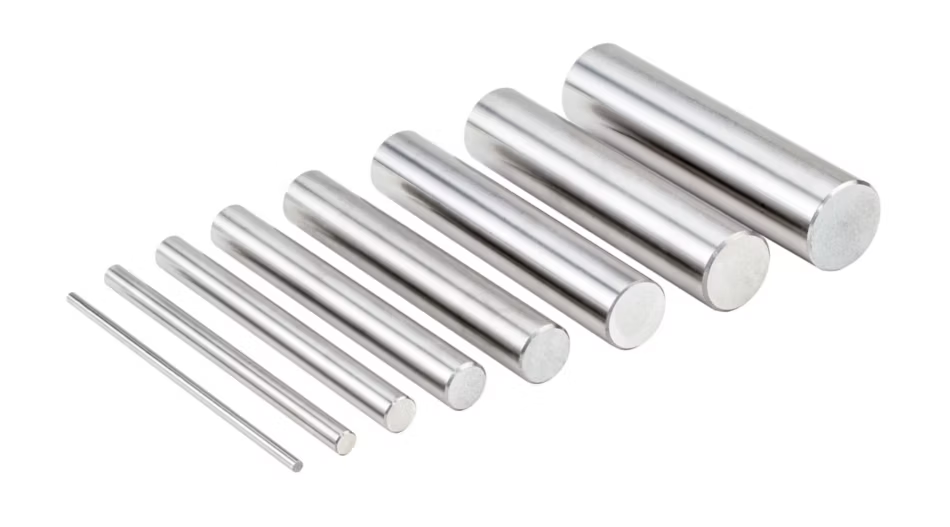
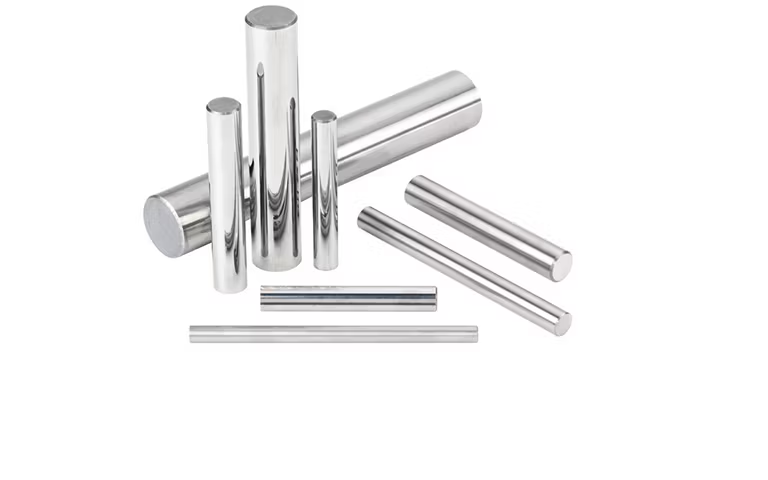
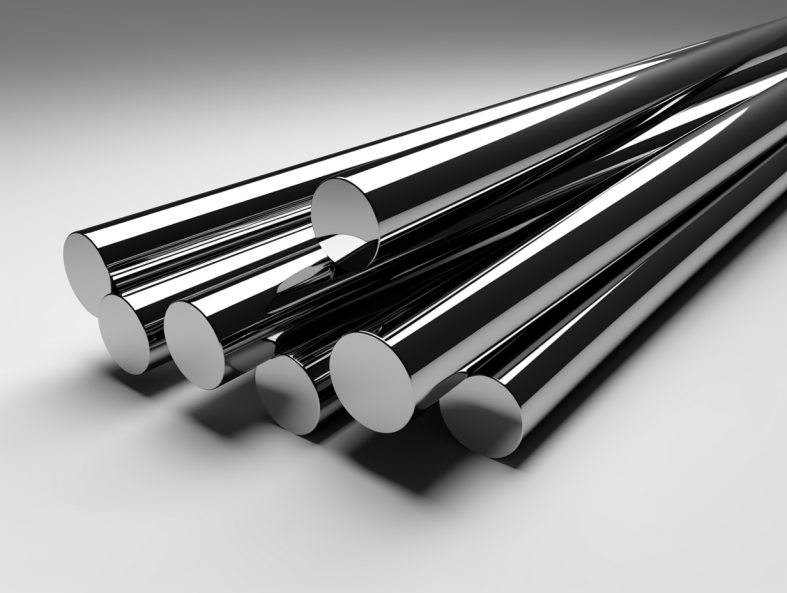
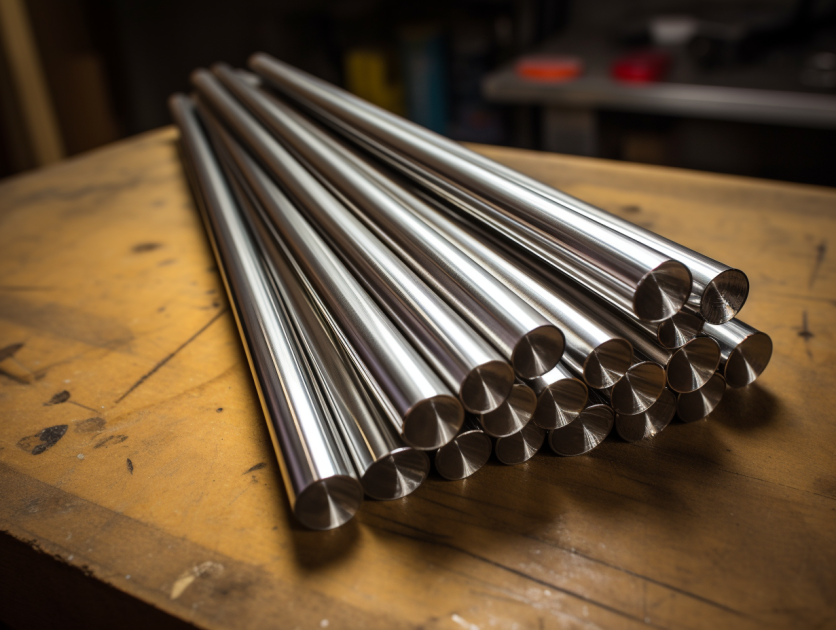
Composition and Characteristics of Grinding Carbide Strips
Model | Composition | Characteristics |
---|---|---|
WC-Co | Tungsten Carbide, Cobalt | High hardness, good toughness, suitable for general-purpose applications. |
WC-Ni | Tungsten Carbide, Nickel | Improved corrosion resistance, good toughness, ideal for harsh environments. |
WC-TiC | Tungsten Carbide, Titanium Carbide | Enhanced hardness and oxidation resistance, suitable for high-temperature use. |
WC-V | Tungsten Carbide, Vanadium | High heat resistance, increased hardness, used in high-performance applications. |
WC-TaC | Tungsten Carbide, Tantalum Carbide | Superior toughness and wear resistance, ideal for heavy-duty applications. |
WC-NbC | Tungsten Carbide, Niobium Carbide | Increased toughness and wear resistance, suitable for precision tools. |
WC-Mo | Tungsten Carbide, Molybdenum | Enhanced toughness, good wear resistance, used in demanding machining operations. |
WC-Cr3C2 | Tungsten Carbide, Chromium Carbide | Improved hardness and corrosion resistance, ideal for high-wear applications. |
WC-Re | Tungsten Carbide, Rhenium | High temperature stability, excellent wear resistance, used in aerospace industry. |
WC-B4C | Tungsten Carbide, Boron Carbide | Extreme hardness, high wear resistance, used in cutting and drilling tools. |
Hardness, Strength, and Wear Resistance
Property | Description |
---|---|
Hardness (HRA) | 90 – 95 |
Compressive Strength | 4000 – 6000 MPa |
Flexural Strength | 1500 – 2500 MPa |
Wear Resistance Index | 10 – 15 (scale based on ASTM standards) |
Fracture Toughness | 8 – 12 MPa·m^1/2 |
Thermal Expansion | 4.5 – 6.5 µm/m·°C (coefficient of thermal expansion) |
Thermal Conductivity | 80 – 120 W/m·K |
Density | 14.5 – 15.5 g/cm³ |
Specifications, Sizes, Shapes, and Standards
Specification | Size Range | Shape | Standard |
---|---|---|---|
Length | 100mm – 1500mm | Rectangular, Square, Custom | ISO 9001, ASTM B777 |
Width | 10mm – 300mm | Rectangular, Custom | ANSI B212.15, DIN 4999 |
Thickness | 2mm – 50mm | Rectangular, Custom | ISO 3327, ISO 513 |
Tolerances | ±0.05mm (length), ±0.02mm (width/thickness) | ISO 2768, ASME B46.1 | |
Surface Finish | Ra 0.2 – 0.8 µm | ISO 4287, ISO 1302 |
Suppliers and Pricing Details
Supplier | Location | Product Range | Pricing (USD) |
---|---|---|---|
Kennametal | USA | Full range of carbide strips | $50 – $300 per piece |
Sandvik Coromant | Sweden | High-performance carbide strips | $70 – $350 per piece |
Zhuzhou Cemented Carbide | China | Standard and custom strips | $30 – $250 per piece |
Ceratizit | Luxembourg | Wide range of carbide products | $60 – $320 per piece |
Sumitomo Electric | Japan | Precision carbide strips | $80 – $400 per piece |
Guhring | Germany | High-quality carbide strips | $55 – $300 per piece |
OSG Corporation | Japan | Specialized carbide strips | $75 – $350 per piece |
Seco Tools | Sweden | Various carbide strips | $65 – $310 per piece |
ISCAR | Israel | Full range of carbide products | $70 – $330 per piece |
Walter AG | Germany | High-precision carbide strips | $85 – $380 per piece |
How to Select the Right Grinding Carbide Strips
Criteria | Considerations |
---|---|
Application | Ensure the strip material matches the specific requirements of the application (e.g., high wear resistance for cutting tools). |
Material Composition | Choose based on the required hardness, toughness, and corrosion resistance. |
Manufacturer Reputation | Look for manufacturers with a proven track record of quality and reliability. |
Cost | Balance cost with the required performance and longevity. |
Customization Options | Some manufacturers offer customization to meet specific needs. |
Standards Compliance | Ensure the strips meet industry standards and certifications. |
Supplier Location | Consider logistics and shipping times from the supplier’s location. |
Technical Support | Availability of technical support and customer service. |
Comparing Advantages and Limitations
Parameter | Tungsten Carbide Strips | Cobalt-Bonded Strips | Nickel-Bonded Strips |
---|---|---|---|
Hardness | Very high | High | Moderate |
Wear Resistance | Excellent | Very good | Good |
Toughness | Moderate | High | High |
Corrosion Resistance | Moderate | Moderate | High |
Cost | Moderate to high | Moderate | High |
Heat Resistance | High | Moderate to high | Moderate |
Typical Applications | Cutting tools, wear-resistant tools, molds | General machining, wear parts, cutting tools | Corrosive environments, high-precision tools |
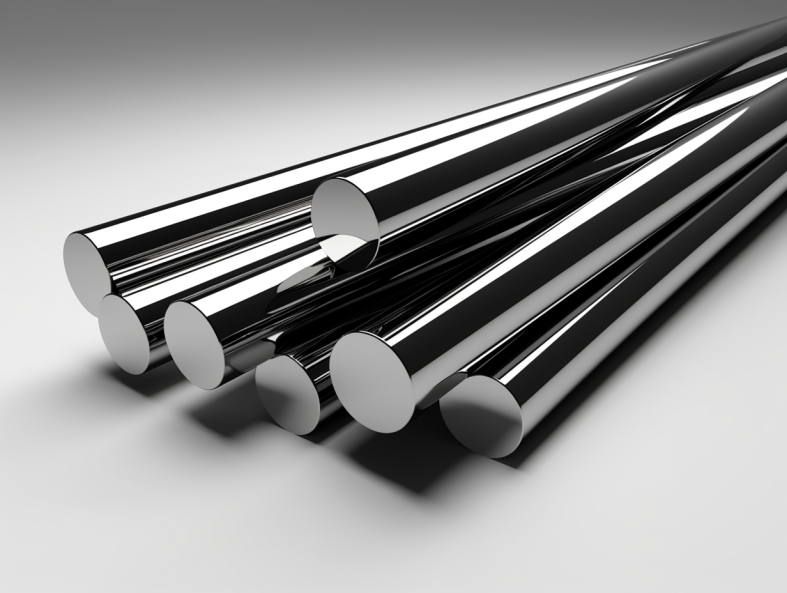
FAQs
Question | Answer |
---|---|
What are grinding carbide strips? | Grinding carbide strips are hard, wear-resistant components used in various machining and cutting applications. |
Why is tungsten carbide used in grinding strips? | Tungsten carbide offers exceptional hardness and wear resistance, making it ideal for high-stress applications. |
How do I choose the right carbide strip manufacturer? | Consider factors like application requirements, material composition, manufacturer reputation, and cost. |
What are the benefits of cobalt-bonded carbide strips? | Cobalt-bonded strips offer high toughness and wear resistance, suitable for general machining and cutting tools. |
Are there custom options available for carbide strips? | Yes, many manufacturers offer customized carbide strips to meet specific application needs. |
What industries use grinding carbide strips? | Industries like aerospace, automotive, woodworking, metalworking, oil and gas, and medical equipment utilize these strips. |
How are carbide strips priced? | Pricing varies based on material composition, size, and manufacturer, typically ranging from $30 to $400 per piece. |
What standards should carbide strips comply with? | Look for compliance with standards such as ISO 9001, ASTM B777, ANSI B212.15, and others relevant to your application. |
Can carbide strips withstand high temperatures? | Yes, especially those made from tungsten carbide and other heat-resistant materials. |
What is the lead time for carbide strip orders? | Lead time varies by manufacturer and order size, generally ranging from a few days to several weeks. |
Choosing the right grinding carbide strips and manufacturers is pivotal for ensuring the quality and efficiency of your industrial applications. By understanding the types, applications, material properties, and selection criteria, you can make an informed decision that aligns with your specific needs. Whether you’re looking for high-precision strips for aerospace or durable strips for heavy-duty mining tools, this guide provides the comprehensive information you need to navigate the complex world of grinding carbide strips.