Introduction
Definition of extruded carbide rod
An extruded carbide rod is a type of cylindrical component made from a carbide material. It is manufactured through a process known as extrusion, where the carbide material is forced through a die to create the desired shape and size. Extruded carbide rods are known for their high strength, durability, and resistance to wear and corrosion. They are commonly used in various industries such as automotive, aerospace, and machining, where they are utilized for applications such as cutting, drilling, and shaping hard materials. The unique properties of extruded carbide rods make them ideal for demanding and high-performance applications that require precision and reliability.
Applications of extruded carbide rod
Extruded carbide rod has a wide range of applications in various industries. One of the key applications of extruded carbide rod is in the manufacturing of cutting tools. Its high hardness and wear resistance make it an ideal material for producing durable and efficient cutting tools. Additionally, extruded carbide rod is used in the production of wear parts, such as punches and dies, due to its excellent strength and toughness. Moreover, it finds applications in the construction industry for drilling and mining operations. The versatility of extruded carbide rod makes it an essential component in many industrial processes.
Importance of extruded carbide rod in various industries
Extruded carbide rods play a crucial role in various industries due to their exceptional properties and versatility. These rods are widely used in the manufacturing sector for the production of cutting tools, such as drills, end mills, and reamers. The hardness and wear resistance of extruded carbide rods make them ideal for applications that require precision machining and long tool life. Additionally, these rods are also utilized in the automotive industry for the production of high-performance engine components, such as valve seats and pistons. The superior strength and thermal stability of extruded carbide rods make them capable of withstanding extreme conditions and ensuring reliable performance. Moreover, in the construction industry, these rods are used in the fabrication of wear-resistant parts for heavy machinery and equipment, enhancing their durability and efficiency. Overall, the importance of extruded carbide rods in various industries cannot be overstated, as they contribute significantly to the advancement and success of numerous manufacturing processes.
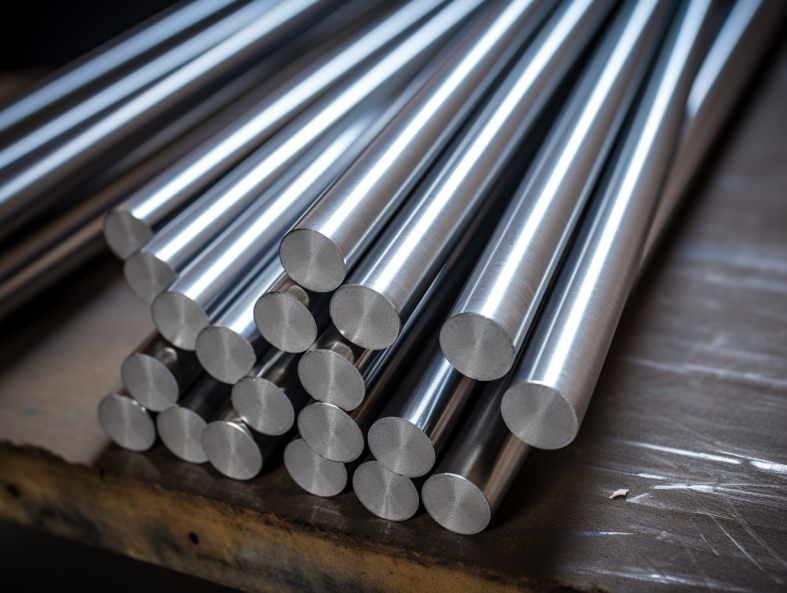
Manufacturing Process
Raw materials used in the manufacturing process
In the manufacturing process of extruded carbide rods, various raw materials are used. These materials include tungsten carbide powder, cobalt powder, and other additives. Tungsten carbide powder is the main component and provides the hardness and strength to the final product. Cobalt powder acts as a binder and helps in holding the tungsten carbide particles together. The use of specific additives enhances the performance and characteristics of the extruded carbide rods. The selection and quality of these raw materials play a crucial role in determining the overall quality and performance of the final product.
Extrusion process for carbide rod production
The extrusion process is a crucial step in the production of carbide rods. It involves forcing a carbide mixture through a die to create the desired shape and dimensions. The mixture, which typically consists of tungsten carbide powder and a binder material, is heated and then pushed through the die using a hydraulic press. The pressure applied during the extrusion process helps to compact the carbide particles and eliminate any voids or imperfections. This results in a dense and uniform carbide rod with excellent mechanical properties. The extruded carbide rod can then be further processed and treated to enhance its hardness, wear resistance, and other desirable characteristics. Overall, the extrusion process plays a vital role in producing high-quality carbide rods that are used in various industries such as manufacturing, mining, and aerospace.
Quality control measures during manufacturing
Quality control measures during manufacturing play a crucial role in ensuring the reliability and performance of extruded carbide rods. To meet the highest standards, rigorous inspections and tests are conducted at every stage of the manufacturing process. From the selection of raw materials to the final product, strict quality control protocols are implemented to identify any defects or deviations. Advanced technologies and equipment are utilized to measure dimensions, check for surface imperfections, and assess the material’s hardness and composition. Additionally, skilled technicians and engineers closely monitor the production line to detect any anomalies and take immediate corrective actions. By adhering to these stringent quality control measures, manufacturers can guarantee that each extruded carbide rod meets the required specifications and delivers exceptional performance in various industrial applications.
Properties of Extruded Carbide Rod
Hardness and wear resistance
The hardness and wear resistance of extruded carbide rods are key properties that make them highly desirable in various industries. These rods are specifically engineered to withstand extreme conditions and resist wear and tear, making them ideal for applications that require durability and longevity. The high hardness of extruded carbide rods allows them to maintain their shape and integrity even under heavy loads and high temperatures. Additionally, their exceptional wear resistance ensures minimal material loss and prolongs the lifespan of the rods, resulting in cost savings for businesses. With their superior hardness and wear resistance, extruded carbide rods are widely used in industries such as automotive, aerospace, and mining, where high-performance materials are essential for efficient and reliable operations.
High temperature resistance
Extruded carbide rods are known for their exceptional high temperature resistance. These rods are specifically designed to withstand extreme heat conditions, making them ideal for various industrial applications. The unique composition of the carbide material allows the rods to maintain their structural integrity even at elevated temperatures, ensuring reliable performance and longevity. Whether used in high-temperature furnaces, cutting tools, or other demanding environments, extruded carbide rods provide the durability and stability required for efficient and effective operations.
Chemical stability
Chemical stability is an important characteristic of extruded carbide rods. These rods are designed to withstand harsh chemical environments without undergoing any significant changes in their composition or structure. The high chemical stability of extruded carbide rods makes them suitable for various applications in industries such as aerospace, automotive, and manufacturing. Whether exposed to corrosive substances or extreme temperatures, these rods maintain their integrity and performance, ensuring reliable and long-lasting performance. This exceptional chemical stability sets extruded carbide rods apart from other materials and makes them a preferred choice for demanding applications.
Applications
Cutting tools
Extruded carbide rods are essential components in the manufacturing of cutting tools. These rods are made from a combination of tungsten carbide and cobalt, resulting in a material that is incredibly hard and wear-resistant. The extrusion process ensures that the rods have a uniform shape and size, making them ideal for use in various cutting applications. With their exceptional hardness and durability, extruded carbide rods provide excellent performance and longevity in cutting tools, allowing for precise and efficient cutting in a wide range of materials.
Milling and drilling applications
Extruded carbide rod is widely used in milling and drilling applications due to its exceptional hardness and durability. It is commonly used in the manufacturing industry for cutting, shaping, and drilling various materials such as metal, wood, and plastic. The high hardness of the carbide rod allows for efficient and precise machining, resulting in high-quality finished products. Additionally, the durability of the rod ensures long-lasting performance, reducing the need for frequent replacements. Whether it is for industrial applications or DIY projects, extruded carbide rod is a reliable choice for achieving accurate and efficient milling and drilling operations.
Wear parts in various industries
Wear parts in various industries play a crucial role in ensuring the efficiency and longevity of machinery and equipment. One such important component is the extruded carbide rod. This specially designed rod, made from high-quality carbide materials, offers exceptional wear resistance and durability. It is widely used in industries such as automotive, aerospace, mining, and manufacturing, where the demand for reliable and long-lasting wear parts is paramount. The extruded carbide rod is known for its exceptional hardness, toughness, and resistance to heat, making it ideal for applications that require high levels of strength and performance. With its superior properties, the extruded carbide rod is an indispensable component in the production of cutting tools, punches, dies, and wear parts that can withstand the most demanding operating conditions. Its ability to resist wear and provide excellent precision and stability makes it a preferred choice among professionals in various industries.
Advantages of Extruded Carbide Rod
Longer tool life
The extruded carbide rod offers a significant advantage in terms of longer tool life. With its superior hardness and wear resistance, this rod is designed to withstand high-speed machining operations and heavy cutting conditions. The unique composition of the carbide material ensures minimal tool wear, resulting in extended tool life and reduced downtime for tool replacements. Additionally, the extruded carbide rod exhibits excellent thermal stability, allowing it to maintain its performance even in high-temperature environments. This makes it an ideal choice for industries that require precision and durability in their cutting tools, such as automotive, aerospace, and manufacturing sectors.
Higher cutting speeds
Extruded carbide rods offer significant advantages when it comes to higher cutting speeds. The unique composition and structure of these rods allow for increased heat resistance and improved hardness, ensuring that they can withstand the extreme conditions of high-speed machining. This enables manufacturers to achieve faster cutting rates, resulting in increased productivity and reduced production time. Additionally, the exceptional wear resistance of extruded carbide rods ensures a longer tool life, reducing the need for frequent tool changes and enhancing overall cost-effectiveness. With their ability to handle higher cutting speeds, extruded carbide rods are a valuable tool for industries that require efficient and precise machining processes.
Improved productivity
Improved productivity is a key goal for many industries, and the use of extruded carbide rods can greatly contribute to achieving this objective. These rods are known for their exceptional hardness, wear resistance, and durability, making them ideal for applications that require high precision and long-lasting performance. By incorporating extruded carbide rods into manufacturing processes, companies can enhance their productivity by reducing downtime, increasing cutting speeds, and improving tool life. With their superior strength and reliability, extruded carbide rods enable faster and more efficient production, resulting in higher output and reduced costs. Whether it’s in the automotive, aerospace, or machining industry, the adoption of extruded carbide rods can lead to significant improvements in productivity, ultimately driving business success.
Conclusion
Summary of the key points
The extruded carbide rod is a highly durable and versatile material used in various industries. It is made by compressing tungsten carbide powder into a rod shape and then subjecting it to a high-temperature extrusion process. This process results in a dense and uniform structure, giving the rod exceptional strength and wear resistance. The extruded carbide rod is commonly used in cutting tools, such as drills and end mills, due to its excellent hardness and ability to withstand high temperatures. Additionally, it is also used in the manufacturing of wear parts, such as dies and punches, as well as in the production of wire drawing dies. Overall, the extruded carbide rod is a crucial component in many industrial applications, providing superior performance and longevity.
Future prospects of extruded carbide rod
The future prospects of extruded carbide rod look promising. With advancements in technology and increasing demand for high-performance materials, extruded carbide rod is expected to play a vital role in various industries. Its exceptional hardness, resistance to wear and corrosion, and high temperature stability make it an ideal choice for applications in cutting tools, dies, and molds. Moreover, the versatility of extruded carbide rod allows for customization and adaptation to specific requirements, further enhancing its potential in the market. As industries continue to seek innovative solutions for improved productivity and efficiency, the demand for extruded carbide rod is projected to grow. With ongoing research and development, we can expect to see further improvements in its properties and performance, making it even more valuable in the future.
Importance of using high-quality carbide rods
High-quality carbide rods are of utmost importance in various industries. These rods offer exceptional durability, strength, and wear resistance, making them essential for applications that require cutting, drilling, milling, and shaping hard materials. By using high-quality carbide rods, manufacturers can ensure precision and efficiency in their processes, resulting in superior quality products. Moreover, these rods also contribute to cost savings as they have a longer lifespan and require less frequent replacement. Therefore, it is crucial for industries to prioritize the use of high-quality carbide rods to maximize productivity and maintain a competitive edge in the market.