When it comes to shaping the toughest materials on Earth, like tungsten carbide, conventional machining methods often fall short. Enter EDM (Electrical Discharge Machining) blocks carbide plates, a specialized technology that has revolutionized the way we shape and refine these incredibly hard and wear-resistant materials.
This comprehensive guide delves deep into the world of EDM blocks carbide plates, exploring their significance, the intricacies of the EDM process, diverse applications, and why choosing the right supplier is paramount for achieving exceptional results.
Unlocking the Power of Sparks: What is EDM Machining?
EDM, also known as spark machining or spark eroding, is a non-traditional machining process that utilizes controlled electrical discharges to remove material from a workpiece. Unlike conventional machining that relies on mechanical forces, EDM harnesses the power of precisely controlled electrical sparks to erode material with remarkable accuracy, even for the hardest materials like tungsten carbide.
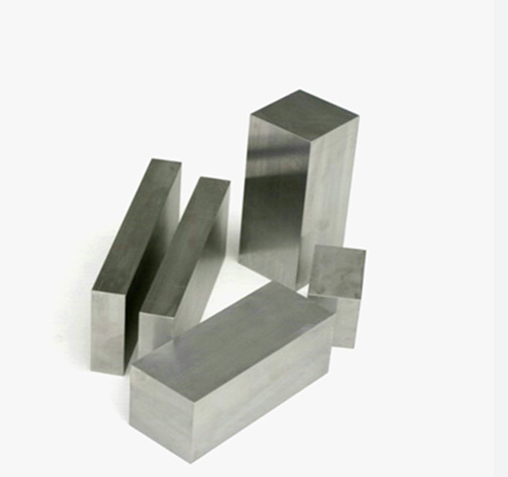
How EDM Blocks Carbide Plates: A Symphony of Precision
- The Setup: The EDM process begins with both the workpiece (in this case, the carbide plate) and the electrode (typically made of copper, graphite, or other conductive materials) submerged in a dielectric fluid, usually deionized water or oil.
- The Spark: A precisely controlled voltage is applied between the electrode and the workpiece, creating an electrical potential difference. As the electrode approaches the workpiece, the dielectric fluid breaks down, generating a spark.
- Material Removal: This high-energy spark, reaching temperatures exceeding 8,000°C (14,432°F), vaporizes a tiny amount of material from the workpiece’s surface, creating a small crater.
- Precision Movement: The electrode, guided by a CNC (Computer Numerical Control) system, follows a pre-programmed path, generating a series of controlled sparks that gradually erode the material, shaping the carbide plate with exceptional accuracy.
- Flushing and Cooling: The dielectric fluid plays a critical role in flushing away the eroded particles and cooling both the electrode and the workpiece, ensuring a clean and precise machining process.
Types of EDM Blocks Carbide Plates: Tailoring to Specific Needs
Type | Description | Applications |
---|---|---|
Solid Carbide Blocks | Made entirely of solid tungsten carbide, offering maximum hardness and wear resistance. | Ideal for high-wear applications like dies, punches, and cutting tools. |
Carbide-Tipped Blocks | Feature a layer of carbide brazed onto a less expensive substrate, like steel, providing a balance of cost and performance. | Suitable for applications requiring wear resistance in specific areas, like wear plates and cutting edges. |
Custom EDM Blocks | Engineered to meet specific dimensional and geometric requirements, offering tailored solutions for unique applications. | Used in a wide range of industries, including aerospace, medical, and automotive, for components with complex shapes and tight tolerances. |
Table 1: Types of EDM Blocks Carbide Plates
Where Precision Meets Durability: Applications of EDM Blocks Carbide Plates
- Aerospace: Intricate components for jet engines, turbine blades, and fuel system parts, requiring extreme precision, heat resistance, and wear resistance.
- Medical: Surgical instruments, dental burs, and implants, demanding biocompatibility, sharpness, and resistance to wear and corrosion.
- Automotive: Fuel injectors, engine components, and transmission parts, requiring high precision, durability, and resistance to high temperatures and pressures.
- Tool and Die Making: Dies, punches, and molds for shaping and forming other materials, requiring exceptional hardness, wear resistance, and dimensional accuracy.
- Electronics: Micro-components for semiconductors, connectors, and other electronic devices, demanding extreme precision and intricate geometries.
Finding the Right Partner: Comparing EDM Blocks Carbide Plate Suppliers
Supplier | Location | Price Range (per piece, approximate) | Specialties |
---|---|---|---|
TRUER | China | $100 – $2000+ (depending on size, complexity, and material grade) | Wide selection of carbide grades, custom geometries, rapid prototyping, competitive pricing. |
Kennametal | USA | $150 – $2500+ | Advanced materials, specialized coatings, technical expertise in demanding applications. |
Sandvik Coromant | Sweden | $120 – $2300+ | Wide range of standard and custom sizes, focus on tooling solutions, expertise in wear parts. |
Mitsubishi Materials | Japan | $180 – $2800+ | High-precision machining, advanced ceramics, complex geometries, focus on high-performance applications. |
Table 2: Comparing EDM Blocks Carbide Plate Suppliers
Weighing the Benefits and Limitations
Advantages of EDM Blocks Carbide Plates | Disadvantages of EDM Blocks Carbide Plates |
---|---|
Machining the “Unmachinable”: Enables the shaping of extremely hard and wear-resistant materials like tungsten carbide. | Slower Machining Speeds: Compared to conventional machining, EDM is a relatively slow process. |
Exceptional Precision and Accuracy: Achieves intricate geometries and tight tolerances, often in the micron range. | Limited to Conductive Materials: EDM can only be used on materials that conduct electricity. |
Minimal Tool Wear: The non-contact nature of EDM reduces tool wear, extending tool life. | Surface Recast Layer: The EDM process can create a thin recast layer on the machined surface, which may require additional finishing. |
Stress-Free Machining: The absence of mechanical forces minimizes stress on the workpiece, reducing the risk of distortion or cracking. | Cost Considerations: EDM equipment and consumables can be more expensive than conventional machining setups. |
Table 3: Advantages and Disadvantages of EDM Blocks Carbide Plates
Beyond the Sparks: Fascinating Facts about EDM
- Origins in Spark Erosion: The basic principles of EDM were first observed in the late 1700s, but it wasn’t until the mid-20th century that it evolved into a practical machining process.
- Micro-EDM for Tiny Wonders: Advancements in EDM technology have led to micro-EDM, capable of machining features at the micron and sub-micron level, enabling the creation of incredibly small and intricate components.
- Spark as a Tool: In EDM, the spark itself acts as the cutting tool, making it possible to machine complex shapes and cavities that would be impossible to create with traditional cutting tools.
Why Choose TRUER for Your EDM Blocks Carbide Plate Needs?
- Uncompromising Quality and Precision: We source only the highest quality carbide materials and utilize state-of-the-art EDM equipment to ensure exceptional precision and dimensional accuracy for your most demanding applications.
- Engineering Expertise and Collaboration: Our team of skilled engineers works closely with you to understand your specific requirements, providing expert guidance and tailored solutions to optimize your EDM machining processes.
- Wide Selection and Customization: We offer a comprehensive range of standard and custom EDM blocks carbide plates, catering to diverse industries and applications. Our capabilities include complex geometries, tight tolerances, and a variety of carbide grades to meet your specific needs.
- Competitive Pricing and Timely Delivery: We are committed to providing competitive pricing and efficient lead times, ensuring you receive the best value and on-time delivery for your EDM machining projects.
- Exceptional Customer Support: Our dedicated customer support team is always available to answer your questions, provide technical assistance, and ensure a seamless experience from initial inquiry to final delivery.
FAQs: Addressing Your EDM Blocks Carbide Plate Questions
1. What factors influence the cost of EDM blocks carbide plates?
Several factors impact the cost, including the size and complexity of the plate, the grade of carbide used, the required tolerances, the quantity ordered, and the complexity of the EDM machining process.
2. Can EDM blocks carbide plates be coated for enhanced performance?
Yes, various coatings, such as titanium nitride (TiN) or diamond-like carbon (DLC), can be applied to EDM blocks carbide plates to further enhance their wear resistance, lubricity, or corrosion resistance.
3. What are the typical lead times for custom EDM blocks carbide plates?
Lead times for custom plates vary depending on factors like the complexity of the design, the availability of the specific carbide grade, and the current production capacity. However, many suppliers, including TRUER, strive to provide competitive lead times to meet your project deadlines.
4. How do I choose the right electrode material for EDM machining carbide plates?
The choice of electrode material depends on factors like the desired machining speed, surface finish, accuracy requirements, and the type of carbide being machined. Common electrode materials include copper, graphite, and copper-tungsten alloys.
5. What are the key considerations for achieving optimal surface finishes in EDM machining carbide plates?
Achieving optimal surface finishes involves carefully selecting EDM parameters like pulse duration, current intensity, and electrode material. Additionally, using high-quality dielectric fluids and implementing proper flushing techniques are crucial for achieving smooth and defect-free surfaces.