Introduction
Have you ever thought about the environmental impact of the materials we use every day? If you’re here, you’re probably curious about how modern manufacturing can go green—and that’s where eco-friendly carbide manufacturing comes in. Carbide materials, celebrated for their toughness and wear resistance, are indispensable in industrial tools and components. But traditional manufacturing processes? They’ve got a bad rep for being energy-intensive and polluting.
The good news? Eco-friendly methods are transforming the industry. This guide dives deep into the green side of carbide manufacturing—covering the processes, materials, and applications while keeping things conversational and engaging. Let’s explore!
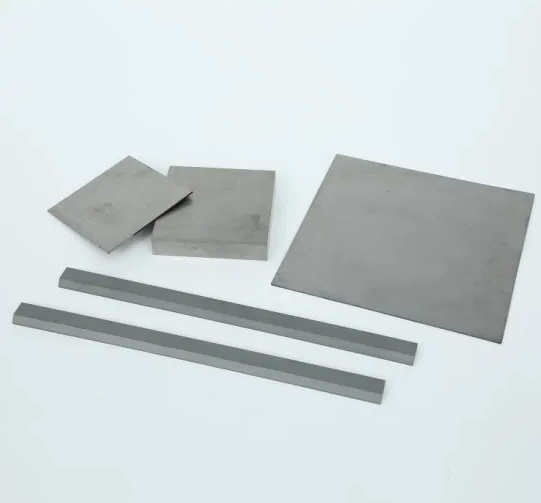
Types of Eco-Friendly Carbide Manufacturing
Methodology | Description |
---|---|
Recycling Carbide Scrap | Reclaiming used carbide materials to reduce waste and conserve resources. |
Additive Manufacturing | Using 3D printing techniques to minimize material usage and energy waste. |
Green Binder Systems | Employing non-toxic binders during production for cleaner outputs. |
Low-Emission Sintering | Reducing emissions by optimizing sintering processes with advanced technology. |
Bio-Based Lubricants | Utilizing biodegradable oils and coolants in machining processes. |
Closed-Loop Production Systems | Recycling byproducts like cobalt back into the manufacturing cycle. |
These innovative approaches aren’t just eco-friendly; they’re cost-effective and efficient. Let’s break it down further.
Raw Materials and Composition Analysis
When we talk about eco-friendly carbide manufacturing, the raw materials and their composition play a starring role. Traditional carbides are often made from tungsten carbide (WC) and cobalt (Co), but newer eco-friendly options focus on sustainable sourcing and alternatives.
- Recycled Tungsten Carbide: Extracted from old tools and components, reducing the need for virgin tungsten mining.
- Cobalt Alternatives: Exploring nickel or iron as binders to reduce reliance on cobalt, which is ethically and environmentally challenging to source.
- Nano-Scale Powders: Advanced powder technologies improve performance while using less material overall.
Specific Metal Powder Models
Powder Model | Composition | Characteristics |
---|---|---|
WC-6% Co | Tungsten carbide, 6% cobalt | High hardness, good toughness, versatile application. |
WC-10% Ni | Tungsten carbide, 10% nickel | Environmentally friendly, high corrosion resistance. |
WC-FeCr | Tungsten carbide, Fe-Cr binder | Cost-effective, sustainable alternative to cobalt. |
Sub-Micron WC | Ultrafine tungsten carbide | Extreme hardness, superior wear resistance. |
Nano WC-Ni | Nano tungsten carbide, nickel | Enhanced strength and toughness in compact designs. |
Recycled WC-Co | Reclaimed tungsten-carbide-cobalt | Sustainable, reduces raw material demand. |
WC-Cr3C2 | Tungsten carbide-chromium carbide | High thermal resistance, ideal for extreme conditions. |
TiC-Co | Titanium carbide, cobalt | Lightweight, strong, used in aerospace applications. |
WC-Ni-Fe | Tungsten carbide, nickel-iron | Excellent for eco-conscious construction tools. |
CrC-WC Blend | Chromium carbide, tungsten carbide | Outstanding wear resistance for demanding uses. |
These materials deliver top-notch performance while treading lightly on the planet.
Applications of Eco-Friendly Carbide Manufacturing
Industry | Applications |
---|---|
Aerospace | Turbine blades, fasteners, lightweight components. |
Automotive | Cutting tools, engine components, wear-resistant parts. |
Construction | Drill bits, saw blades, excavation tools. |
Medical | Surgical instruments, dental tools, prosthetics. |
Oil & Gas | Sealing rings, valves, pumps in harsh environments. |
Consumer Electronics | Precision molds, heat sinks, durable casings. |
Mining | Rock-cutting tools, heavy-duty drill bits. |
Carbide’s unique properties—from durability to resistance to extreme temperatures—make it a go-to material for these diverse industries.
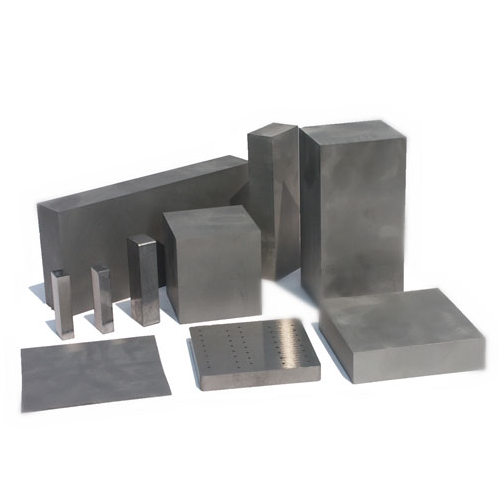
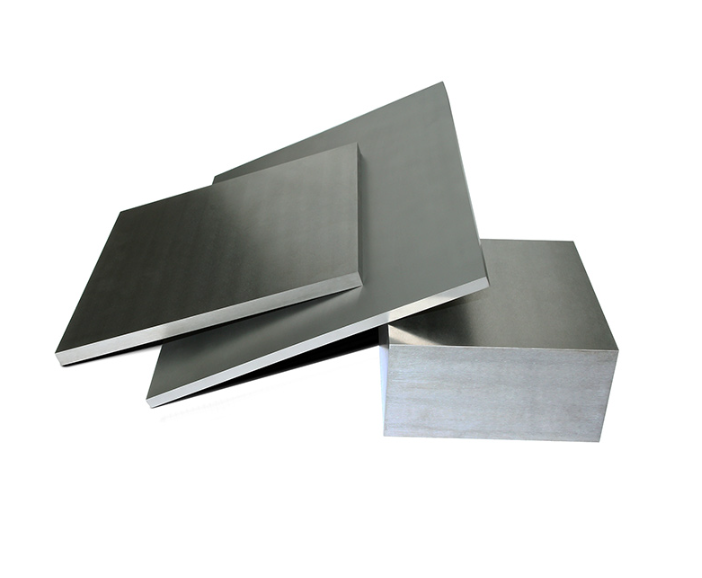
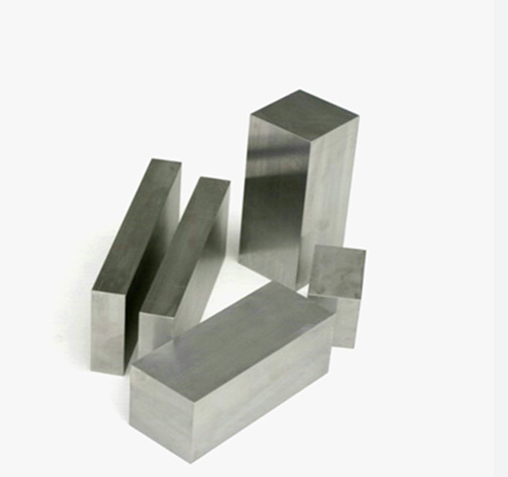
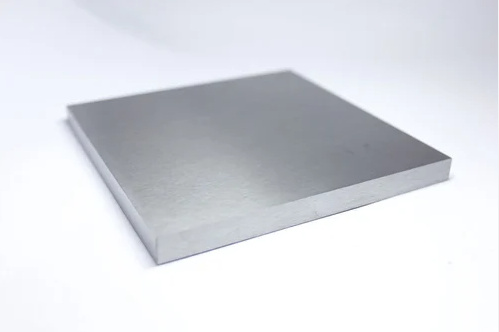
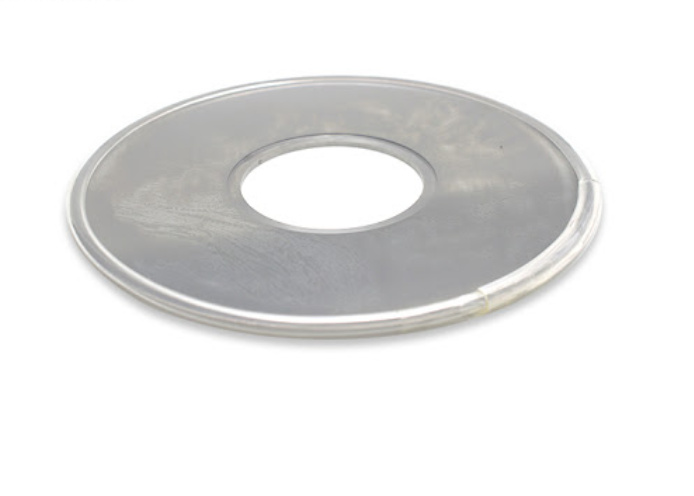
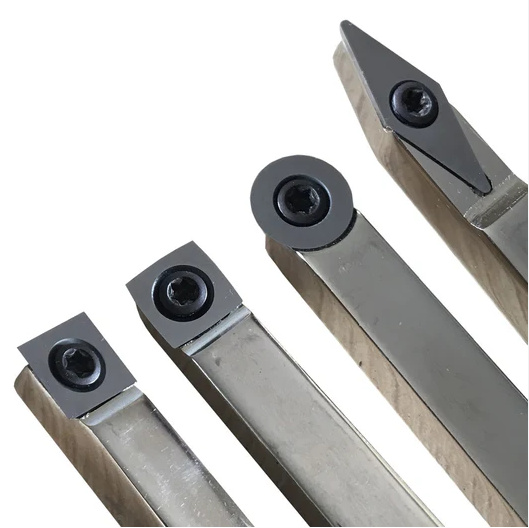
Production Process Flow
Eco-friendly carbide manufacturing simplifies and optimizes the traditional process. Here’s how:
- Raw Material Preparation:
- Recycling scrap carbide.
- Sourcing sustainably mined tungsten and alternative binders.
- Mixing:
- Combining metal powders (e.g., WC and Co) with eco-friendly binders.
- Compacting:
- Pressing powders into green (unfired) shapes using reduced-energy techniques.
- Sintering:
- Heating compacted parts in a controlled, low-emission furnace to achieve final density and strength.
- Finishing:
- Applying bio-based coolants during grinding and polishing to refine shapes and dimensions.
Material Properties of Eco-Friendly Carbide
Property | Range | Description |
---|---|---|
Hardness | 1200-2000 HV | Outstanding wear resistance and longevity. |
Density | 14.5-15.5 g/cm³ | Optimized weight for industrial applications. |
Toughness | 10-15 MPa•m½ | High fracture resistance, even under stress. |
Thermal Conductivity | 80-100 W/mK | Excellent heat dissipation in extreme conditions. |
Elastic Modulus | 500-700 GPa | Exceptional rigidity for precision applications. |
Specifications, Sizes, Shapes, and Standards
Parameter | Details |
---|---|
Shape | Round, square, hexagonal, custom geometries available. |
Size | From micro-sized (1mm) to large industrial parts (200mm). |
Standards | ISO, ASTM, DIN-compliant for universal compatibility. |
Surface Finish | Polished, ground, or unpolished depending on application. |
Choosing Eco-Friendly Carbide Manufacturing: Key Factors
Factor | Considerations |
---|---|
Environmental Impact | Recycling percentage, emission control measures. |
Performance Requirements | Hardness, wear resistance, thermal stability. |
Cost | Initial material cost versus lifecycle savings. |
Certification Standards | ISO, ASTM compliance for quality assurance. |
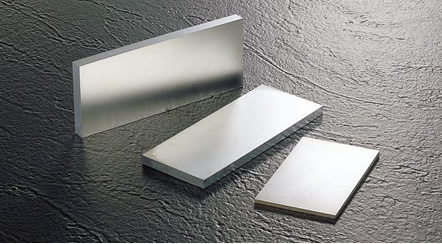
Comparison of Advantages and Limitations
Aspect | Advantages | Limitations |
---|---|---|
Recycling | Reduces waste, conserves raw materials. | May involve slightly higher initial costs. |
Green Binders | Non-toxic, environmentally safe. | Limited availability in certain regions. |
Low-Emission Processes | Reduces carbon footprint. | May require advanced infrastructure. |
Alternative Binders | Safer than cobalt. | Lower toughness compared to traditional cobalt. |
FAQs
Question | Answer |
---|---|
What is eco-friendly carbide? | Carbide manufactured with sustainable processes and recycled materials. |
Why is cobalt-free carbide important? | Reduces environmental and ethical concerns linked to cobalt mining. |
How durable is eco-friendly carbide? | Comparable to traditional carbide, with high hardness and wear resistance. |
Can eco-friendly carbide reduce costs? | Yes, through recycling and longer-lasting tools. |
Are there industry certifications? | Look for ISO and ASTM certifications for quality and sustainability. |