What is Cutting Speed?
Cutting speed is the rate at which the cutting edge of a tool moves relative to the workpiece surface. It is measured in surface feet per minute (SFM) or meters per minute (m/min). Cutting speed plays a crucial role in machining processes, affecting tool wear, surface finish, and productivity. Choosing the right cutting speed ensures efficient material removal while extending tool life.
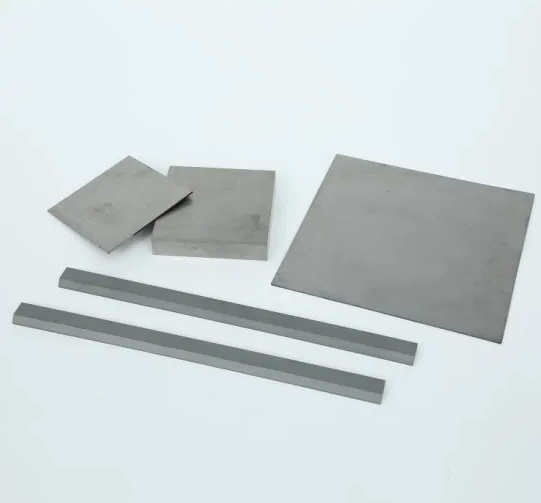
The Importance of Cutting Speed in CNC Machining, Milling, Turning, and Other Processes
Cutting speed directly impacts the efficiency and accuracy of CNC machining, milling, and turning operations. If the cutting speed is too low, the process becomes inefficient, leading to poor surface finishes and excessive tool wear. Conversely, excessively high cutting speeds can cause overheating, resulting in rapid tool degradation and workpiece damage. By optimizing cutting speed, manufacturers can achieve high precision, improved surface quality, and extended tool life.
Why Carbide Tools Require Higher Cutting Speeds?
Carbide tools are known for their hardness, wear resistance, and ability to withstand high temperatures. Unlike high-speed steel (HSS) tools, carbide tools require higher cutting speeds due to their superior heat resistance and toughness. Operating at higher speeds minimizes built-up edge formation, reduces cycle time, and enhances overall productivity.
Recommended Cutting Speeds for Carbide Tools
The table below provides a general guideline for recommended cutting speeds when using carbide tools for different materials:
Material | Cutting Speed (SFM) | Cutting Speed (m/min) |
---|---|---|
Aluminum | 800 – 1500 | 244 – 457 |
Mild Steel | 250 – 600 | 76 – 183 |
Stainless Steel | 150 – 400 | 46 – 122 |
Cast Iron | 300 – 700 | 91 – 213 |
Titanium | 100 – 250 | 30 – 76 |
Nickel Alloys | 75 – 200 | 23 – 61 |
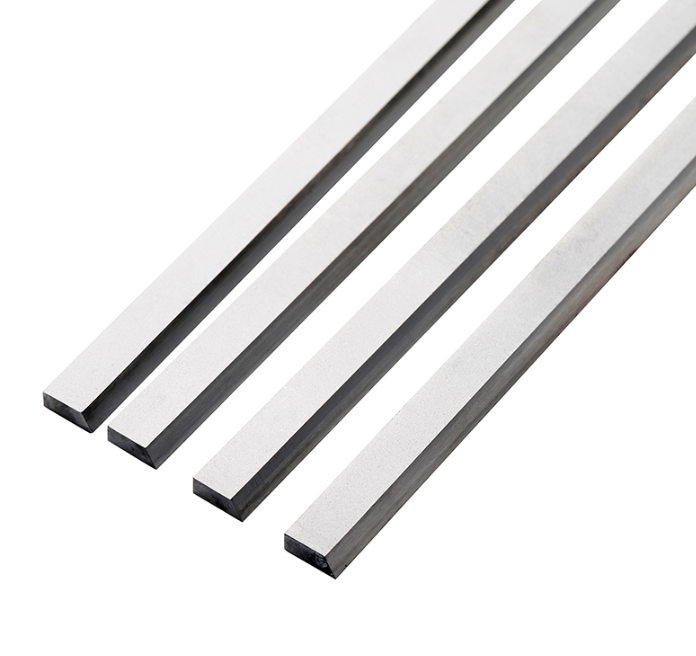
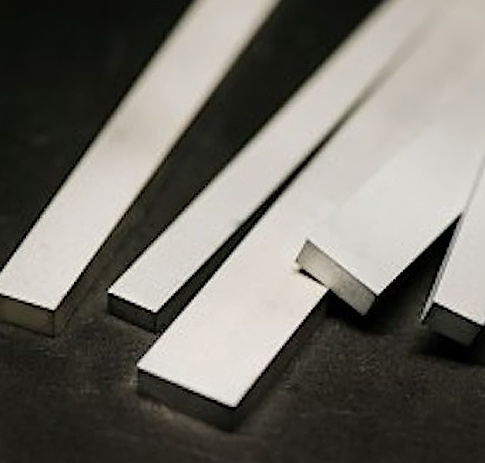
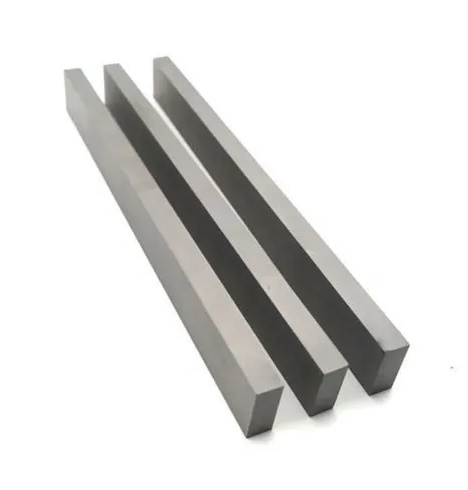
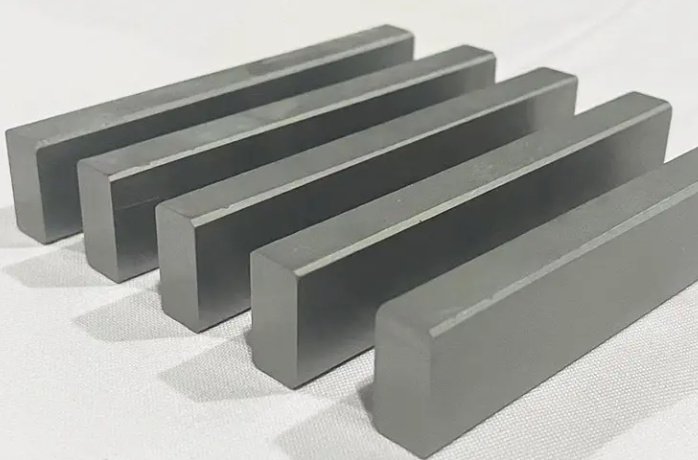
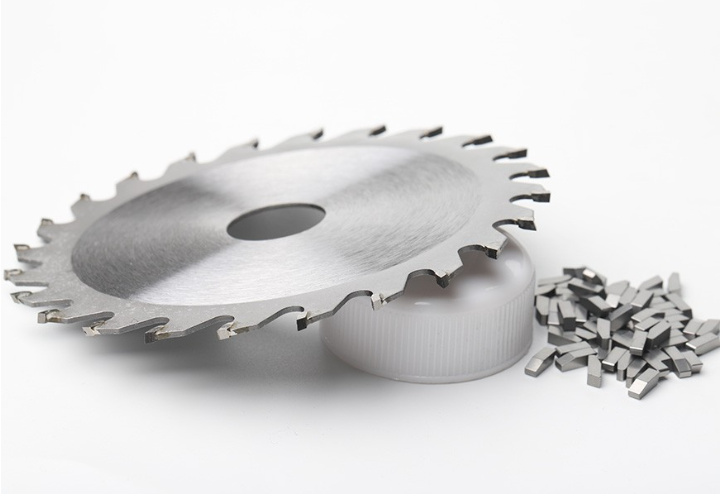
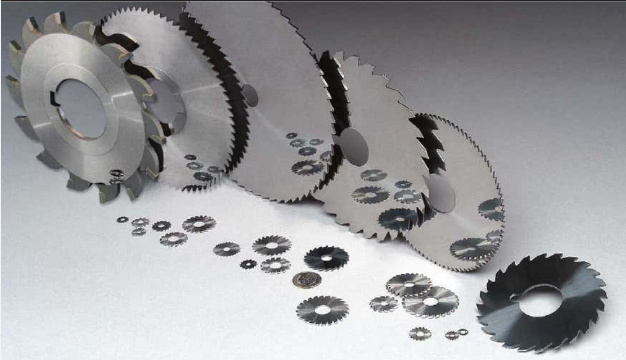
Factors Affecting Cutting Speed
Several factors influence the optimal cutting speed for carbide tools. The table below outlines key considerations:
Factor | Effect on Cutting Speed |
---|---|
Tool Material | Carbide tools operate at higher speeds than HSS tools. |
Workpiece Material | Harder materials require lower cutting speeds. |
Cutting Fluid | Enhances cooling and lubrication, allowing higher speeds. |
Tool Geometry | Sharp, well-designed cutting edges improve efficiency. |
Machine Stability | Rigid setups enable higher speeds without vibration. |
Depth of Cut | Deeper cuts require lower speeds to prevent tool damage. |
How to Calculate Cutting Speed for Carbide Tools?
Cutting speed can be calculated using the following formula:
V=π×D×N12V = \frac{\pi \times D \times N}{12} (for SFM)
V=π×D×N1000V = \frac{\pi \times D \times N}{1000} (for m/min)
Where:
- VV = Cutting speed
- DD = Workpiece or tool diameter (in inches or mm)
- NN = Spindle speed (RPM)
For example, if using a carbide end mill with a 1-inch diameter at 1000 RPM, the cutting speed is: V=3.14×1×100012=261.67 SFMV = \frac{3.14 \times 1 \times 1000}{12} = 261.67 \, SFM
Common Mistakes and How to Avoid Them
- Using Incorrect Cutting Speeds – Always refer to recommended values for specific materials.
- Ignoring Tool Wear – Regularly inspect tools to avoid premature failure.
- Poor Cooling and Lubrication – Use appropriate cutting fluids to manage heat buildup.
- Inconsistent Feed Rates – Maintain a steady feed rate to prevent uneven tool wear.
- Skipping Tool Coating Considerations – Use coated carbide tools for enhanced performance.
Specific Metal Powder Models for Carbide Tools
Below are specific metal powder models used in carbide tools and their applications:
Metal Powder Model | Composition & Features | Applications |
---|---|---|
WC-Co (Tungsten Carbide-Cobalt) | High hardness and toughness | General machining |
TiC (Titanium Carbide) | Wear-resistant, used in coatings | High-speed cutting |
TaC (Tantalum Carbide) | Heat-resistant, used in alloys | Aerospace machining |
NbC (Niobium Carbide) | Enhances wear resistance | Precision cutting |
VC (Vanadium Carbide) | Improves cutting edge retention | High-performance cutting tools |
Cr3C2 (Chromium Carbide) | Corrosion-resistant | Abrasive material machining |
Mo2C (Molybdenum Carbide) | Increases hardness | Heavy-duty applications |
ZrC (Zirconium Carbide) | High-temperature stability | High-speed operations |
HfC (Hafnium Carbide) | Excellent thermal resistance | Ultra-high-speed machining |
Al2O3-TiC (Alumina-Titanium Carbide) | Enhanced oxidation resistance | Hard turning operations |
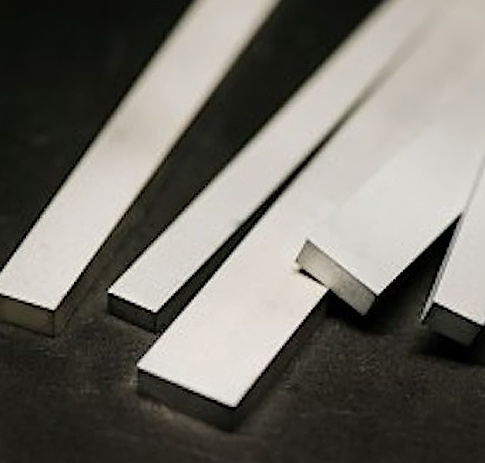
FAQ
Question | Answer |
---|---|
What happens if cutting speed is too low? | Poor surface finish, increased tool wear, and inefficient cutting. |
Can carbide tools cut hardened steel? | Yes, with proper coatings and high cutting speeds. |
How does cutting speed affect tool life? | Higher speeds reduce tool life if not optimized. |
Why use coolant with carbide tools? | Reduces heat buildup and prolongs tool life. |
What is the best cutting speed for aluminum? | 800-1500 SFM, depending on tool type. |