Carbide cutting tools are the unsung heroes in machining and metalworking. They’re tough, precise, and get the job done even under extreme conditions. But how do you optimize their efficiency? That’s what we’re here to uncover! This guide dives deep into carbide cutting efficiency, exploring raw materials, applications, manufacturing processes, and much more.
Understanding Carbide Cutting Efficiency
What is Carbide Cutting Efficiency?
Carbide cutting efficiency refers to the ability of carbide-based tools to cut through materials effectively, minimizing waste and maximizing output. It’s not just about sharpness—it’s about strength, durability, wear resistance, and the ability to handle high temperatures. Think of it like a chef’s knife: a sharper, stronger blade means cleaner cuts and longer use.
Why Does Carbide Matter in Cutting Tools?
Tungsten carbide, often the primary material, combines hardness and toughness in a way most metals can’t. Compared to traditional steel tools, carbide tools last longer, cut faster, and handle harsher conditions. It’s like switching from a butter knife to a samurai sword.
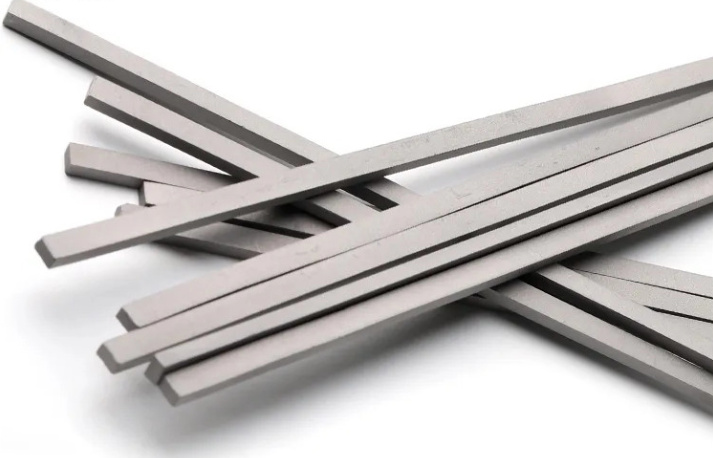
Raw Materials and Composition Analysis of Carbide Cutting Tools
Carbide cutting tools are a blend of metal powders and binders. Let’s break it down:
Material | Role in Composition | Properties |
---|---|---|
Tungsten Carbide (WC) | Core material, provides hardness | Extreme wear resistance, high strength |
Cobalt (Co) | Acts as a binder | Toughness, ductility |
Titanium Carbide (TiC) | Enhances wear resistance and temperature handling | Corrosion resistance |
Tantalum Carbide (TaC) | Adds heat resistance | Stability at high temperatures |
Nickel (Ni) | Alternative binder | Anti-corrosion, enhances flexibility |
Production Process Flow of Carbide Cutting Tools
- Powder Preparation: Mixing tungsten carbide, cobalt, and other powders to precise ratios.
- Compaction: The powders are pressed into molds to form a “green” compact.
- Sintering: High-temperature sintering fuses the particles together, creating the final hard material.
- Shaping and Grinding: Cutting tools are shaped to their final specifications with diamond abrasives.
- Coating (Optional): Advanced coatings like titanium nitride enhance performance and longevity.
Applications of Carbide Cutting Tools
Industry | Application | Efficiency Boost |
---|---|---|
Aerospace | Cutting high-strength alloys | Precise cuts, reduced downtime |
Automotive | Machining engine components | Faster cycle times, extended tool life |
Medical | Manufacturing surgical instruments | Ultra-fine precision, minimal wear |
Oil and Gas | Drilling and pipeline manufacturing | Handles extreme environments |
General Engineering | Cutting, drilling, and shaping various metals | Versatility, reduced tool replacement |
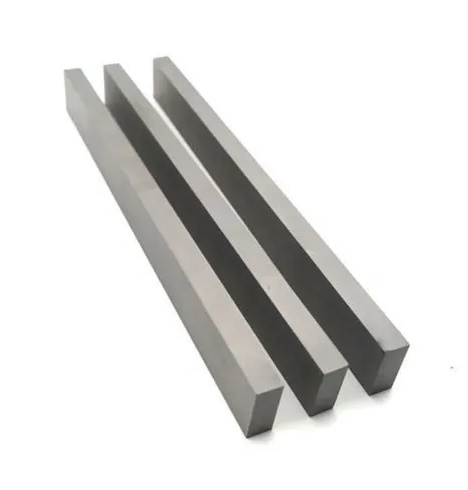
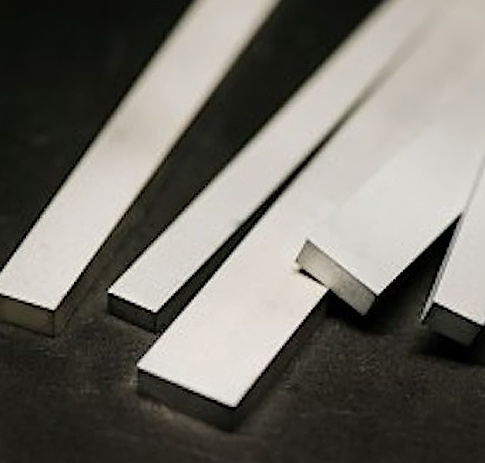
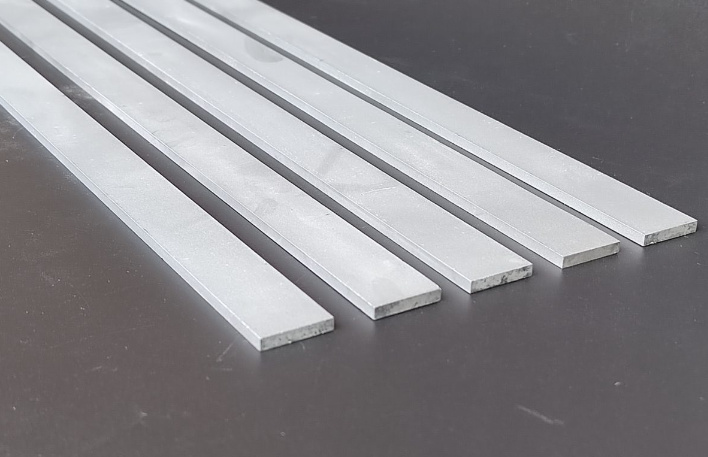
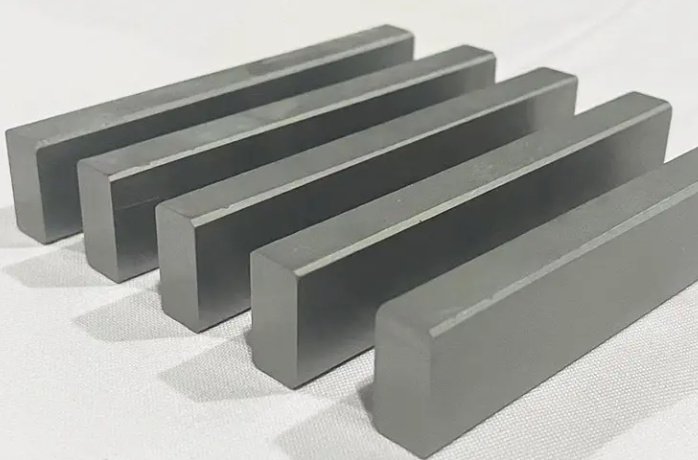
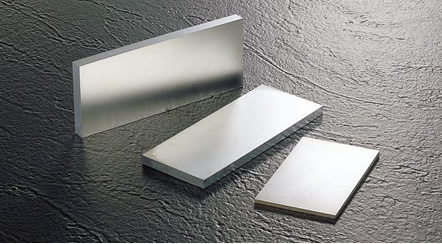
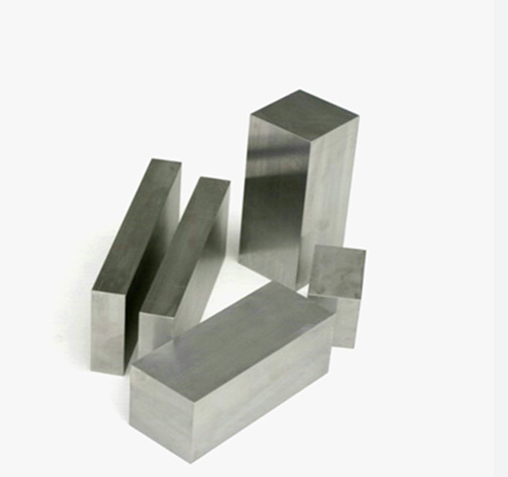
Material Properties of Carbide Cutting Tools
Property | Range | Impact on Efficiency |
---|---|---|
Hardness | 85–92 HRA | Higher hardness equals longer tool life |
Density | 14.5–15.1 g/cm³ | Indicates material compactness |
Transverse Rupture Strength | 2,000–3,000 MPa | Resistance to breaking under stress |
Thermal Conductivity | 84–105 W/mK | Heat dissipation during cutting |
Young’s Modulus | 550–700 GPa | Reflects material stiffness |
Top 10 Metal Powder Models for Carbide Tools
Here’s a closer look at specific metal powder models that power carbide tools:
- WC-10Co-4Cr: Excellent for high-impact applications.
- WC-6Co-1Cr: Balances wear resistance and toughness.
- WC-17Co: Known for its superior hardness and longevity.
- WC-12Ni: Offers corrosion resistance for challenging environments.
- WC-20TiC: Great for high-speed machining tasks.
- WC-5Mo-4Co: Performs exceptionally in abrasive conditions.
- WC-8TaC-2Co: Ideal for aerospace-grade alloys.
- WC-15Co-2TiC: Provides enhanced thermal resistance.
- WC-9Co-1Ni: Combines toughness and flexibility.
- WC-25Cr3C2: Preferred for heavy-duty industrial tasks.
Choosing Carbide Cutting Efficiency
Factor | Consideration | Tip |
---|---|---|
Tool Type | Drill, end mill, insert, etc. | Match the tool to the material |
Material Composition | WC, Co, TiC ratios | Balance hardness and toughness |
Coating Options | TiN, TiCN, Al2O3 | Use coatings for high-temperature jobs |
Supplier Reputation | Established vs new suppliers | Prioritize quality and consistency |
Budget | Initial cost vs long-term savings | Invest in durable, high-quality tools |
Comparing Advantages and Limitations
Aspect | Advantages | Limitations |
---|---|---|
Durability | Long-lasting, resists wear | Higher upfront cost |
Precision | Cleaner, more accurate cuts | Requires expertise for best use |
Versatility | Works across materials, including alloys | Not ideal for softer materials |
Heat Resistance | Performs well at high temperatures | May need specialized coatings for extreme jobs |
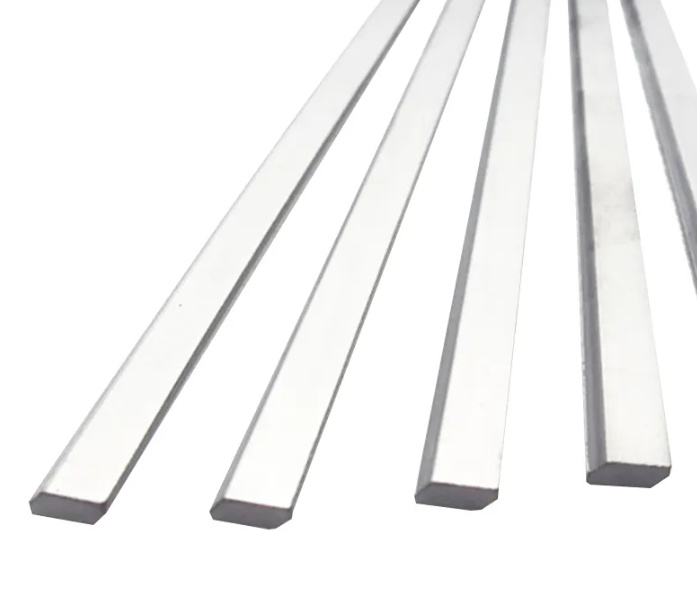
FAQs
Question | Answer |
---|---|
What makes carbide tools efficient? | Their hardness, durability, and ability to handle heat and wear during cutting. |
Are carbide tools better than steel tools? | Yes, they last longer, cut faster, and can handle tougher materials. |
How do I maintain carbide tools? | Regular cleaning, proper storage, and periodic sharpening ensure longevity. |
Can I use carbide tools on all materials? | They’re best for hard materials; softer materials may not benefit as much. |