Imagine a material so tough, it can shrug off scratches from a diamond and keep on functioning. That’s the remarkable world of tungsten carbide plates. These custom-made industrial workhorses find applications in a wide range of demanding environments, from the unforgiving depths of a mine shaft to the high-pressure world of metalworking.
This guide dives deep into the fascinating world of custom tungsten carbide plates. We’ll explore their unique characteristics, the vast array of applications they excel in, and the factors to consider when choosing the perfect plate for your specific needs. So, buckle up and get ready to discover the power of tungsten carbide!
Applications of Tungsten Carbide Plates
Tungsten carbide plates are the ultimate material for wear and tear resistance. Their exceptional hardness makes them ideal for applications where other materials would quickly succumb to friction and abrasion. Here’s a glimpse into some of the key industries that rely on custom tungsten carbide plates:
- Metalworking: Imagine a drill bit that can pierce through tough metals like steel or titanium without losing its edge. Tungsten carbide plates make this a reality. They are extensively used in cutting tools, dies, punches, and wear strips for various metalworking machinery. Their ability to maintain sharp edges translates to cleaner cuts, improved efficiency, and reduced downtime for tool changes.
- Mining and Construction: The harsh realities of mining and construction equipment demand materials that can withstand constant wear and tear. Tungsten carbide plates come to the rescue here as well. They are used in wear liners for chutes, crusher jaws, and drill bits, significantly extending the lifespan of these critical components. Their resistance to impact and abrasion ensures smooth operations and minimizes equipment replacements.
- Woodworking: Picture a router bit that carves intricate designs into hardwood without a hitch. Tungsten carbide plates make this possible. They are a popular choice for woodworking tools like router bits, planer blades, and saw tips. Their exceptional hardness allows for clean cuts, reduced chipping, and a longer tool life compared to traditional steel options.
- Oil and Gas Industry: Downhole drilling equipment used in the oil and gas industry encounters extreme pressure and harsh conditions. Tungsten carbide plates are a vital component in these applications. They are used in drill bits, downhole tools, and wear pads, ensuring equipment can operate reliably and efficiently in these demanding environments.
- Other Applications: The applications of custom tungsten carbide plates extend far beyond these core industries. They are also used in various sectors like:
- Aerospace: For wear-resistant parts in aircraft landing gear and engine components.
- Textiles: For cutting tools and wear strips in textile machinery.
- Recycling: For shredder blades and wear liners in recycling plants.
These are just a few examples, and the potential uses for custom tungsten carbide plates continue to grow as new applications emerge.
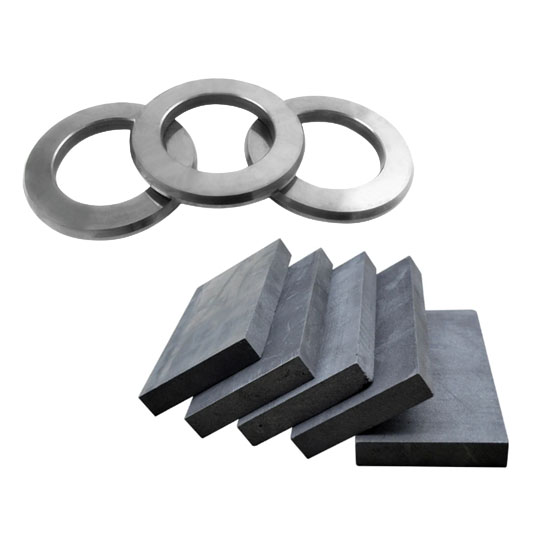
Characteristics of Tungsten Carbide Plates
Tungsten carbide’s exceptional properties make it a game-changer in industrial applications. Here’s a closer look at some of its key characteristics:
- Extreme Hardness: Tungsten carbide boasts a Rockwell hardness (HRA) that can reach up to 93, making it one of the hardest materials on Earth, second only to diamond. This exceptional hardness translates to unparalleled wear resistance, allowing these plates to withstand extreme friction and abrasion without succumbing to damage.
- High Melting Point: Tungsten carbide has a melting point exceeding 3,400°C (6,130°F). This remarkable property makes it suitable for applications involving high heat and pressure, such as metalworking and downhole drilling.
- Excellent Strength: When it comes to sheer strength, tungsten carbide plates hold their own. They offer exceptional resistance to bending, breaking, and chipping, even under heavy loads and intense pressure.
- Corrosion Resistance: Tungsten carbide exhibits excellent resistance to corrosion from a variety of chemicals and compounds. This makes them ideal for use in harsh environments where other materials would quickly degrade.
While these characteristics paint a picture of near-invincibility, it’s important to remember that no material is perfect.
Disadvantages of Tungsten Carbide Plates
Here are some limitations to consider when working with custom tungsten carbide plates:
- Brittleness: While incredibly hard, tungsten carbide can be brittle. This means it may chip or crack if subjected to sudden impacts or extreme force.
- High Cost: The manufacturing process for tungsten carbide plates can be expensive. This translates to a higher cost per unit compared to some other materials.
- Heavier Weight: Tungsten carbide is a dense material, making the plates heavier compared to some alternatives. This might be a factor to consider in applications where weight is a critical concern.
- Machinability: While custom tungsten carbide plates offer exceptional performance, they can be challenging to machine compared to softer materials. Specialized tools and techniques are required to cut, drill, or shape these plates, adding to the overall production cost.
Choosing the Perfect Custom Tungsten Carbide Plate
Given the vast array of applications and the unique characteristics of tungsten carbide, selecting the perfect custom plate requires careful consideration. Here are some key factors to ponder:
- Application: Understanding the specific application and the type of wear and tear the plate will encounter is crucial. Different grades of tungsten carbide offer varying levels of hardness, toughness, and wear resistance. For instance, an application requiring high impact resistance might prioritize a tougher grade over an extremely hard one.
- Size and Shape: Custom tungsten carbide plates can be manufactured in various sizes and shapes to meet specific needs. Whether you require a rectangular plate for a wear liner or a complex geometric shape for a cutting tool, customization allows for a perfect fit.
- Grade Selection: Tungsten carbide comes in various grades, each formulated with a specific balance of properties. These grades are often denoted by a code like “Kxx” or “YGxx,” where “xx” represents the Cobalt content percentage. Higher cobalt content generally translates to increased toughness but slightly lower hardness. A knowledgeable supplier can guide you in selecting the optimal grade for your application.
- Surface Finish: The surface finish of the plate can also impact performance. A smoother finish might be preferred for cutting tools to minimize friction, while a textured finish might be suitable for wear liners to improve wear resistance.
Beyond the Basics: Exploring Advanced Considerations
For those seeking an even deeper dive into the world of custom tungsten carbide plates, here are some additional considerations:
- Composite Materials: Tungsten carbide can be combined with other materials like titanium or tantalum to create composite plates with tailored properties. These composites can offer advantages like improved toughness or higher thermal conductivity.
- Coatings: Tungsten carbide plates can be further enhanced with various coatings like titanium nitride or diamond-like carbon (DLC). These coatings can improve wear resistance, reduce friction, and even enhance corrosion resistance.
FAQs
Here are some frequently asked questions regarding custom tungsten carbide plates, presented in a clear and informative table format:
Question | Answer |
---|---|
What are the benefits of using custom tungsten carbide plates? | Exceptional wear resistance, high melting point, excellent strength, and good corrosion resistance. |
What are some drawbacks of custom tungsten carbide plates? | Brittleness, higher cost compared to some materials, heavier weight, and difficulty in machining. |
What are some typical applications for custom tungsten carbide plates? | Metalworking, mining and construction, woodworking, oil and gas industry, and various other industrial sectors. |
What factors should I consider when choosing a custom tungsten carbide plate? | Application, size and shape requirements, grade selection, and desired surface finish. |
Are there any advanced options for custom tungsten carbide plates? | Yes, composite materials and coatings can further enhance the properties of the plates for specific needs. |
By understanding the unique properties and considerations surrounding custom tungsten carbide plates, you can make informed decisions to leverage their exceptional strength and durability in your industrial endeavors.