In the realm of industrial manufacturing and engineering, where precision and durability reign supreme, custom carbide strips have emerged as indispensable components. These versatile tools, meticulously crafted to meet specific application requirements, offer unparalleled performance in wear resistance, cutting efficiency, and structural integrity. This comprehensive guide delves into the world of custom carbide strips, exploring their intricacies, applications, and the advantages of partnering with a trusted manufacturer like TRUER.
What are Custom Carbide Strips?
Custom carbide strips are precision-engineered components made from cemented carbide, a composite material renowned for its exceptional hardness and wear resistance. Unlike standard, off-the-shelf carbide strips, custom variants are tailored to meet unique specifications, encompassing a wide range of geometries, sizes, grades, and surface finishes.
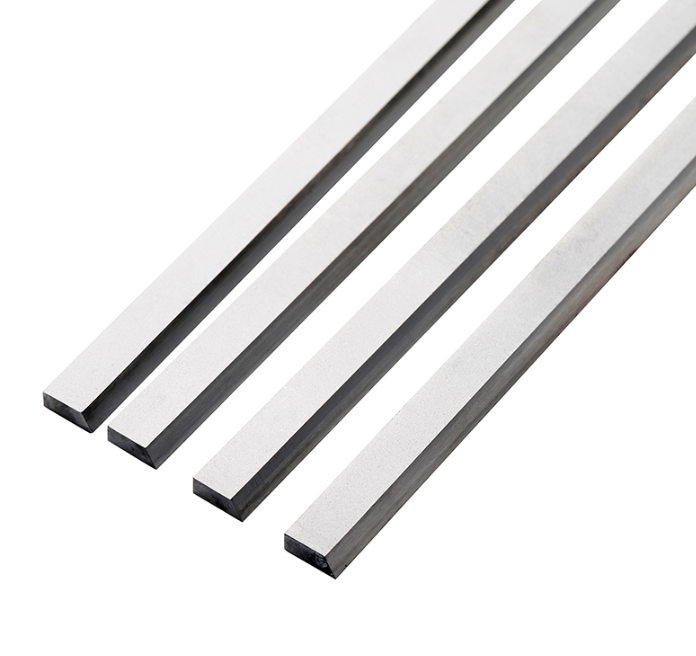
Unlocking the Power of Customization: How it Works
The process of creating custom carbide strips begins with a thorough understanding of the application requirements. This involves close collaboration between the customer and the carbide manufacturer, considering factors such as:
- Application: The specific task the strip will perform, such as wear resistance, cutting, or forming.
- Material Being Processed: The hardness, abrasiveness, and other properties of the material the strip will interact with.
- Operating Conditions: Temperature, pressure, speed, and environmental factors that may influence performance.
- Desired Geometry: Dimensions, shape, tolerances, and any required features like grooves, chamfers, or holes.
- Carbide Grade: Selection of the optimal carbide grade based on hardness, toughness, and wear resistance requirements.
Once the specifications are finalized, the manufacturing process typically involves:
- Powder Metallurgy: Blending, pressing, and sintering of tungsten carbide powder and binder metals to create the desired shape.
- Precision Machining: Using specialized techniques like grinding, lapping, and EDM to achieve the required tolerances and surface finish.
- Quality Control: Rigorous inspection processes ensure that each custom carbide strip meets the specified quality standards.
Navigating the Carbide Strip Universe: Types and Grades
Custom carbide strips are available in a wide array of grades, each formulated to excel in specific applications:
Carbide Grade | Typical Composition | Properties | Common Applications |
---|---|---|---|
K01 | WC-Co (Fine grain) | High toughness, moderate wear resistance | Impact-resistant wear parts, stamping dies, rock drilling tools |
K20 | WC-Co (Medium grain) | Balanced toughness and wear resistance | Wear strips, guides, bushings, drawing dies |
P10 | WC-Co (Fine-medium grain) | Good wear resistance, moderate toughness | Cutting tools for steel and stainless steel, wear parts for abrasive conditions |
P20 | WC-Co (Medium-coarse grain) | High wear resistance, good toughness | Precision cutting tools, wear strips for high-load applications |
M20 | WC-Co (Medium grain) | High wear resistance, moderate toughness | Cutting tools for aluminum and non-ferrous metals, wear parts for abrasive non-metals |
Table 1: Common Carbide Grades for Custom Strips
Applications Across Industries: Where Precision Meets Performance
The versatility of custom carbide strips has led to their widespread adoption in diverse industries, including:
- Metalworking and Machining: Cutting tools, wear parts, forming dies, and guide rails for precision machining operations.
- Oil and Gas: Downhole drilling tools, wear rings, valve components, and seals for demanding oilfield environments.
- Aerospace: Engine components, structural parts, and tooling for high-performance aircraft and spacecraft.
- Automotive: Cutting tools, engine parts, transmission components, and wear-resistant parts for demanding automotive applications.
- Packaging: Cutting blades, sealing jaws, and wear parts for high-speed packaging machinery.
- Textiles: Yarn guides, cutting blades, and wear parts for textile manufacturing equipment.
Weighing the Advantages and Limitations
Advantages of Custom Carbide Strips:
- Tailored Performance: Optimized for specific applications, maximizing efficiency and service life.
- Enhanced Durability: Exceptional wear resistance and hardness, extending component lifespan.
- Increased Precision: Tight tolerances and precise geometries ensure accuracy and repeatability.
- Versatility: Suitable for a wide range of applications and industries.
Limitations:
- Higher Initial Cost: Custom designs typically involve higher upfront costs compared to standard options.
- Longer Lead Times: Customization may require additional design and manufacturing time.
- Limited Availability: Not all suppliers offer custom carbide strip manufacturing.
Table 3: Advantages and Limitations of Custom Carbide Strips
The TRUER Advantage: Why Choose Us?
- Uncompromising Quality: We use only the highest quality carbide materials and adhere to stringent quality control measures.
- Engineering Expertise: Our team of experienced engineers provides expert guidance throughout the design and manufacturing process.
- Advanced Manufacturing: We leverage state-of-the-art equipment and technologies to create complex geometries and achieve tight tolerances.
- Customer-Centric Approach: We are committed to understanding your unique needs and delivering solutions that exceed expectations.
FAQs: Addressing Your Custom Carbide Strip Queries
1. What is the minimum order quantity for custom carbide strips?
We strive to accommodate our customers’ needs, and while we have minimum order values, we can discuss your specific requirements to find a suitable solution.
2. What is the typical lead time for custom carbide strip orders?
Lead times vary depending on the complexity of the design and current production capacity. However, we strive to provide realistic lead times and keep our customers informed throughout the process.
3. Can you provide material certifications for your carbide strips?
Yes, we provide material certifications and test reports upon request to ensure traceability and compliance with industry standards.
4. What types of surface finishes are available for custom carbide strips?
We offer a range of surface finishes, including polished, ground, lapped, and textured surfaces, to meet specific application requirements.
5. Do you offer coating services for custom carbide strips?
Yes, we offer a variety of coatings, such as TiN, TiCN, and DLC, to further enhance wear resistance, lubricity, or other properties.