Introduction
Carbide products are essential in industries ranging from machining to mining. They offer unparalleled strength, wear resistance, and versatility. But here’s the big question: Should you go for standard carbide products or invest in custom carbide solutions? It’s a bit like choosing between a ready-made suit and a tailored one. Let’s dive deep into this fascinating topic and explore every detail to help you make an informed choice.
What Are Carbide Products?
Carbide products, typically composed of tungsten carbide, are a combination of tungsten powder and a binder metal like cobalt. They’re celebrated for their toughness, heat resistance, and ability to maintain sharpness even under high-stress conditions. From cutting tools to wear parts, these materials are the backbone of many industrial applications.
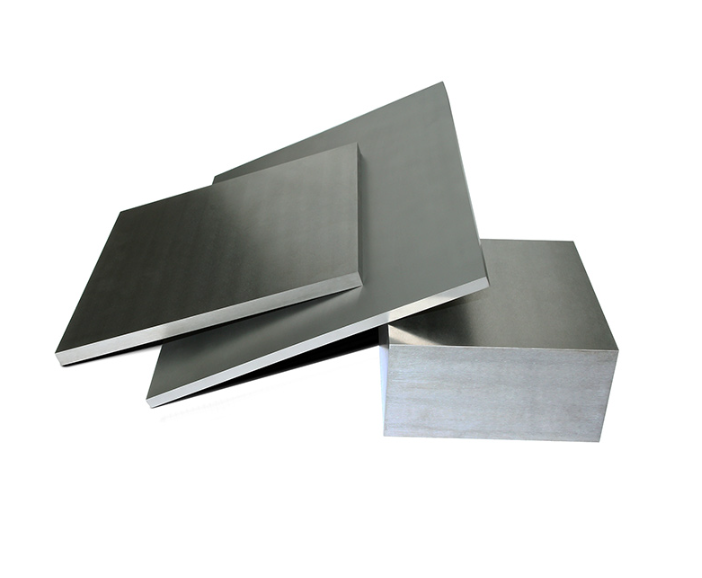
Key Differences Between Standard and Custom Carbide Products
Standard Carbide Products are pre-designed with fixed specifications, offering convenience and cost-effectiveness. They’re great for general applications where customization isn’t a priority.
Custom Carbide Products, on the other hand, are like bespoke tools. They’re designed to meet specific requirements, whether it’s a unique shape, size, or performance characteristic. While pricier, they’re perfect for specialized tasks.
Here’s a quick comparison:
Feature | Standard Carbide Products | Custom Carbide Products |
---|---|---|
Design | Predefined | Tailored to exact specifications |
Cost | Lower | Higher |
Lead Time | Shorter | Longer |
Flexibility | Limited | High |
Applications | General-purpose | Niche or specialized industries |
Types of Custom Carbide Products
Custom carbide products come in many forms, each catering to specific needs. Below is a table showcasing the variety available:
Type | Description | Applications |
---|---|---|
Cutting Tools | Tailored for specific machining tasks, offering precision and durability | Aerospace, automotive |
Mining Inserts | Designed for high wear resistance in mining applications | Mining, drilling |
Wear Parts | Custom parts made to resist extreme abrasion and impact | Heavy machinery |
Carbide Dies | Precision dies for forming and shaping metals | Manufacturing, extrusion |
Valve Components | Components offering excellent corrosion resistance in harsh environments | Oil and gas, petrochemicals |
Custom Blades | Specially designed for unique cutting requirements | Food processing, textiles |
Nozzles | Engineered for high-pressure and wear-resistant fluid dynamics | Water jet cutting, spraying |
Rollers | High-strength rollers for specific industrial applications | Paper mills, steel processing |
Specialty Powders | Custom compositions to meet unique manufacturing needs | Additive manufacturing |
Inserts for Electronics | Precision components for electronics requiring thermal and electrical conductivity | Electronics manufacturing |
Raw Materials and Composition of Custom Carbide Products
The quality of a carbide product begins with its raw materials. Custom carbide products typically use:
- Tungsten Carbide Powder: Provides hardness and wear resistance.
- Cobalt Binder: Adds toughness.
- Nickel or Titanium Additives: Enhance corrosion resistance for specific applications.
Example Metal Powder Models
Here’s a selection of specific models and their properties:
Model | Composition | Properties | Applications |
---|---|---|---|
WC-Co 90/10 | 90% Tungsten, 10% Cobalt | High wear resistance | Cutting tools, mining inserts |
WC-Co 94/6 | 94% Tungsten, 6% Cobalt | Enhanced toughness | Drilling, heavy machinery |
WC-Ni 95/5 | 95% Tungsten, 5% Nickel | Corrosion resistance | Oil and gas, chemical processing |
WC-Ti 92/8 | 92% Tungsten, 8% Titanium | Heat resistance | Aerospace |
WC-Co-Cr 88/12 | 88% Tungsten, 12% Cobalt-Chromium | Wear and corrosion resistance | Valve components, nozzles |
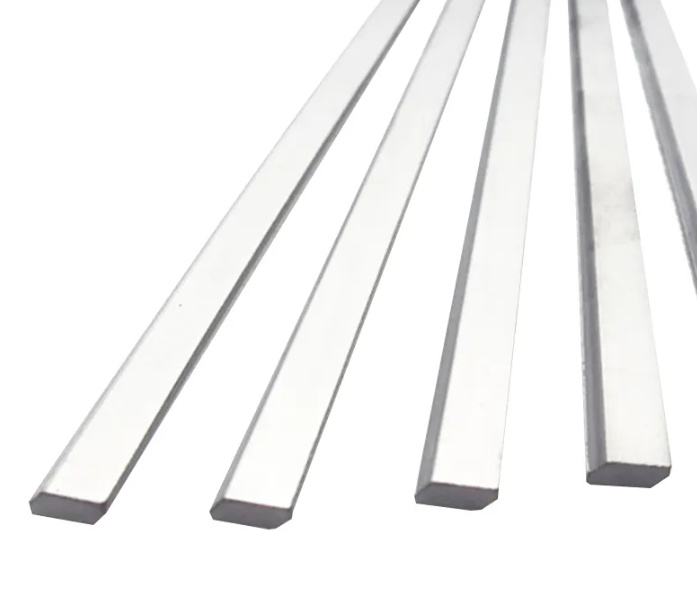
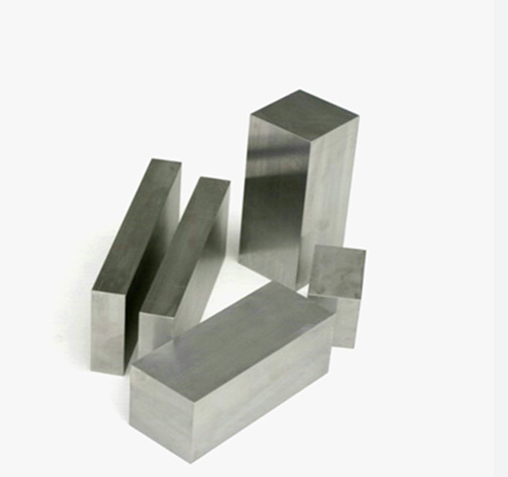

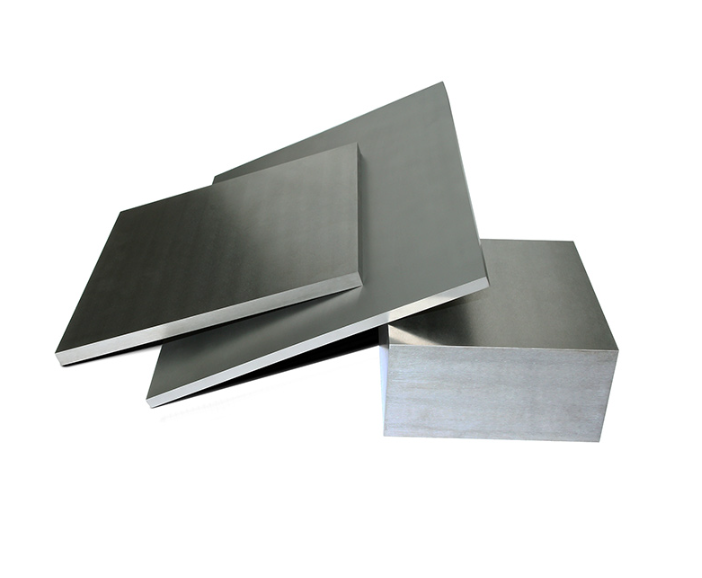
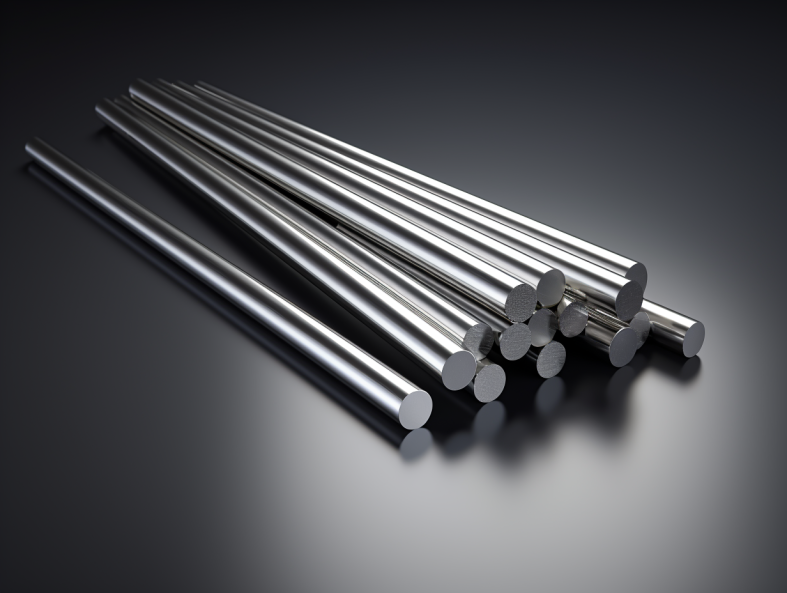
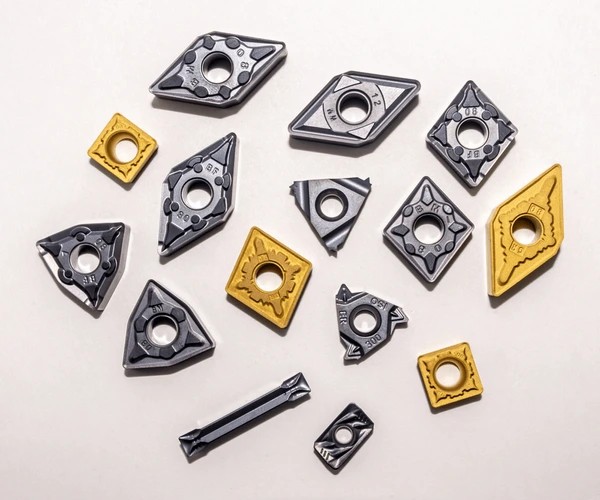
Applications of Custom Carbide Products
Custom carbide products find their way into numerous industries. Here’s how they’re used:
Application | Industries | Examples |
---|---|---|
Precision Cutting Tools | Aerospace, automotive | Custom end mills, drill bits |
Mining and Drilling | Mining, oil & gas | Wear-resistant inserts, cutters |
Wear Parts | Construction | Excavator bucket teeth, crusher parts |
Specialty Nozzles | Fluid dynamics | Water jet cutting, high-pressure spraying |
Production Process Flow of Custom Carbide Products
The production of custom carbide products involves several meticulous steps:
- Powder Preparation: Raw materials like tungsten carbide and cobalt are blended into precise ratios.
- Shaping: The mixture is pressed into desired shapes using molds or additive manufacturing techniques.
- Sintering: The shaped product is heated at high temperatures to achieve hardness and density.
- Finishing: Grinding and polishing ensure precise dimensions and smooth surfaces.
- Quality Control: Rigorous testing guarantees the product meets specifications.
Material Properties of Custom Carbide Products
Property | Description |
---|---|
Hardness | Exceptional wear resistance |
Strength | High compressive strength |
Toughness | Resists cracking under heavy loads |
Thermal Conductivity | Efficient heat dissipation |
Corrosion Resistance | Durable in harsh environments |
Comparison of Hardness, Strength, and Wear Resistance
Model | Hardness (HRA) | Strength (MPa) | Wear Resistance |
---|---|---|---|
WC-Co 90/10 | 91.5 | 2800 | Excellent |
WC-Co-Cr 88/12 | 89.5 | 2600 | Superior corrosion resistance |
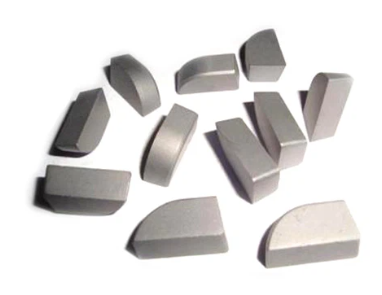
Choosing Custom Carbide Products Supplier
Factor | Consideration |
---|---|
Reputation | Look for established suppliers |
Customization Capability | Ensure they can meet specific needs |
Quality Standards | Check certifications like ISO 9001 |
Lead Time | Evaluate delivery timelines |
Pricing | Competitive yet reflective of quality |
FAQ
Question | Answer |
---|---|
What are custom carbide products? | Tailored carbide tools or components designed for specific applications. |
How are they different from standard products? | Custom products are made to order, offering specific sizes, shapes, and properties. |
Are custom carbide products worth the cost? | Yes, for specialized tasks requiring precision, durability, or unique features. |
What is the main difference between standard and custom carbide products? | Standard products have predefined specifications, while custom products are tailored to meet specific requirements. |
Which is better: standard or custom carbide products? | It depends on your needs. Standard products are cost-effective and quick to source, but custom products offer precision for specialized tasks. |
What industries benefit most from custom carbide products? | Industries like aerospace, automotive, mining, oil & gas, and precision manufacturing rely heavily on custom carbide solutions. |