Container carbide blanks refer to containers or canisters filled with carbide material to be used for making cutting tools and wear-resistant parts. This article provides a detailed overview of container carbide blanks, their key properties, manufacturing process, applications, suppliers, costs and other aspects to consider when selecting and using them.
Overview of Container Carbide Blanks
Container carbide blanks provide an efficient way to transport and utilize carbide for tool making applications. Here are the key details about these blanks:
- Container carbide blanks consist of a metal canister or container filled with compacted carbide powder material.
- The carbide material is most commonly tungsten carbide or titanium carbide powders.
- The container is usually made of mild steel, stainless steel or nickel.
- Blanks come in different standard sizes based on container diameter and length.
- Typical sizes range from 3mm to 150mm diameter and 10mm to 300mm length.
- Blanks are supplied based on the carbide grade, grain size, binder percentage, and container dimensions.
- They are used as molded perform blanks to make cutting tools, wear parts and components using machining and pressing operations.
- Blanks provide even distribution of consistent quality carbideIdeal for complex tool geometries.
- Main advantages are ease of transportation, storage and handling.
Types of Container Carbide Blanks
There are two main types of container carbide blanks:
Blank Type | Description |
---|---|
Straight Blanks | Cylindrical blanks with constant diameter and carbide fill |
Tapered Blanks | Blanks tapered on one or both ends to fit holder cone |
Key Properties of Carbide Blanks
The key properties of container carbide blanks that determine applications and performance:
Property | Description |
---|---|
Carbide grade | Chemical composition of tungsten or titanium carbide |
Carbide grain size | Measured in microns based on microscopic structure |
Binder percentage | Amount of metallic binder like cobalt in the carbide |
Hardness | Resistance to deforming, cutting or wearing |
Transverse Rupture Strength (TRS) | Ability to withstand breakage forces |
Toughness | Resistance to chipping during machining |
Wear resistance | Resistance to abrasion and adhesive wear |
Chemical resistance | Resistance to acids, alkalis and other chemicals |
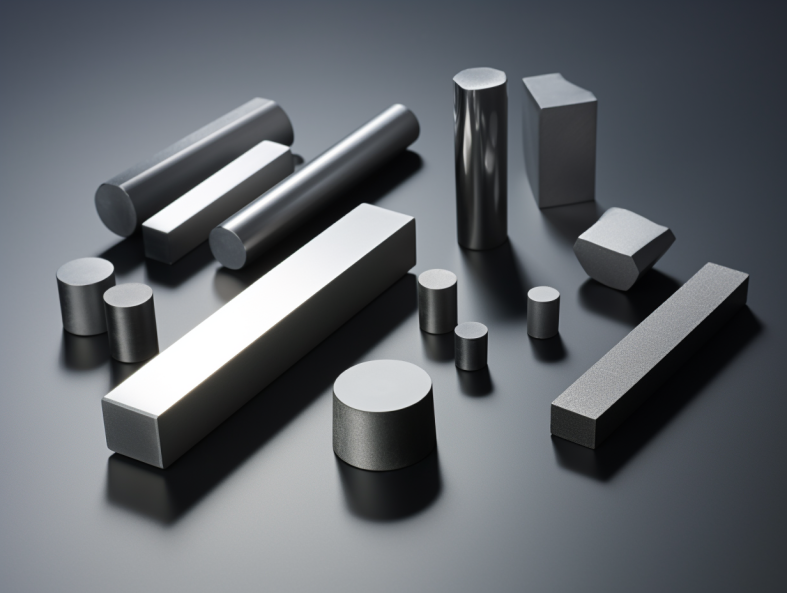
Manufacturing Process for Carbide Blanks
Carbide blanks are made using the following key manufacturing steps:
- Milling and blending – The tungsten or titanium powders and binder alloy powders are measured, milled and blended to achieve the desired composition.
- Compaction – The powder mixture is compacted into a cohesive preform using cold or hot isostatic pressing.
- Sintering – The pressed compact is sintered at 1300-1700°C in a controlled atmosphere to form dense carbide.
- Crushing and milling – The sintered mass is crushed and milled into fine powder of specific particle sizes.
- Loading – The carbide powder is loaded and compacted into steel containers under vibration.
- Sealing – The loaded containers are sealed using covers which are welded to enclose the carbide.
- Quality checks – The blanks undergo finishing operations and stringent quality checks before shipment.
Applications and Uses of Container Carbide Blanks
Here are the main applications and uses of container carbide blanks:
Cutting Tools
- Turning inserts
- Milling cutters
- Drills and reamers
- Threading tools
- Form tools
- Burrs and routers
Wear Parts
- Extrusion dies
- Drawing dies
- Pelletizing tools
- Wear plates
- Seals and bearings
Components
- Extruder screws
- Valve parts
- Nozzles
- Pump shafts
- Rollers
Carbide blanks enable machining of complex tool and component geometries needed for critical applications.
Guide to Selecting Container Carbide Blanks
Proper selection of the carbide blank is key to getting optimal performance. Use this guide when choosing blanks:
Parameter | Details to Consider |
---|---|
Carbide grade | Hardness, wear resistance and toughness needs |
Grain size | Finer for sharp edges, coarser for toughness |
Binder percentage | Higher for toughness, lower for hardness and wear resistance |
Blank dimensions | Diameter, length, straight or tapered based on final part dimensions |
Tolerance | Tighter tolerances for precision parts, looser for roughing |
Surface finish | Smoother finish required for fine finishing operations |
Certifications | ISO certified for consistent quality |
Consult manufacturer to select optimal blank specifications for your specific application.
Suppliers and Costs of Carbide Blanks
There are many global suppliers that manufacture and sell carbide blanks. Here are typical price ranges:
Carbide Type | Carbide Grade | Cost per kg |
---|---|---|
Tungsten Carbide | Simple grades | $18-$35 |
Complex grades | $50-$150 | |
Titanium Carbide | Common grades | $25-$60 |
Specialty grades | $70-$250 |
Larger size blanks, finer grain size, higher purity and complex grades are more expensive. Customized blank dimensions and properties are also costlier.
Top global suppliers include:
- Sandvik
- Kennametal
- Mitsubishi Materials
- GTSM Sintermetall
- Hyperion Materials & Technologies
- Zhuzhou Jade New Materials
Installation, Storage and Handling of Blanks
Follow these guidelines for using carbide blanks:
- Handle carefully to avoid shocks which can cause cracks.
- Use cushioned containers and secure packaging for transportation.
- Store in a cool, dry place and avoid temperature extremes.
- Use proper fixtures and clamping when machining to prevent damage.
- Follow recommended machining parameters like speeds, feeds and tooling.
- Use appropriate safety precautions when handling fine carbide powder.
How to Select a Reliable Carbide Blanks Supplier
Follow these tips for choosing a good carbide blanks supplier:
- Look for ISO 9001 certified manufacturers with strict quality control.
- Prefer suppliers with a wide range of carbide grades, grain sizes and binders.
- Check capabilities for custom blank dimensions and tolerances.
- Ensure they have expertise in recommending the optimal blanks.
- Ask for technical data sheets and test certificates for their products.
- Evaluate their post-sales service and technical support.
- Compare pricing but give higher priority to quality and consistency.
- Check lead times and availability of ready stock for faster delivery.
- Ensure capabilities to meet large volume or bulk orders if needed.
- Give preference to manufacturers over resellers for quality assurance.
Pros and Cons of Container Carbide Blanks
Advantages | Limitations |
---|---|
Consistent quality carbide | Higher upfront costs than loose powder |
No blending needed | Limited to standard blank sizes |
Uniform hardness and properties | Requires decompaction and crushing after use |
Reduced carbide waste during processing | Reusing crushed powder can cause contamination |
Better control over composition | Limitation on maximum blank size |
Easier handling than loose powder | Restricted to simpler blank geometries |
Avoid inhalation of fine powder | Surface defects possible due to container |
Low porosity | May still require blending with other powders |
Reduced pressing cycle times | Container separation can be challenging |
FAQs
Q: What are the differences between iron-rich carbide grades versus nickel-rich grades?
A: Iron-rich carbide grades like C1-C6 have higher hardness and wear resistance but lower toughness. Nickel-rich grades like C9-C11 have improved toughness but slightly lower hot hardness and chemical resistance.
Q: How are custom blank dimensions possible?
A: Suppliers can provide custom blank diameters and lengths within certain size limits based on their container inventories. Special tapered, hollow or layered blanks can also be engineered.
Q: What are recommended machining parameters for carbide blanks?
A: Lower surface speeds of 100-250 m/min, higher feed rates of 0.2-0.4 mm/rev and rigid clamping are recommended. Use coated carbide tools with appropriate edge preparations.
Q: How to decide between pressed blanks versus sintered blanks?
A: Pressed blanks are less expensive but have lower density and strength. Sintered blanks offer the highest quality but are costlier. Medium density hot pressed blanks provide a good compromise.
Q: Why are higher purity grades and fine grain sizes more expensive?
A: Achieving higher carbide purity and finer grain size requires additional processing steps and advanced techniques, hence the higher cost.
Q: What are typical applications of cobalt versus nickel binding agents?
A: Cobalt binders provide excellent wear resistance suited for cutting tools and dies. Nickel binders provide improved corrosion resistance preferred for extruder parts, valves and pump components.