Introduction
Definition of Cemented Carbide Rods
Cemented carbide rods are a type of cutting tool material that is widely used in various industries. These rods are made by combining tungsten carbide particles with a binder material, such as cobalt. The resulting material is extremely hard and durable, making it ideal for applications that require high wear resistance and cutting performance. Cemented carbide rods are commonly used in the manufacturing of drills, end mills, and other cutting tools. They are known for their excellent strength, toughness, and heat resistance, allowing them to withstand the demanding conditions of machining operations. Overall, cemented carbide rods play a crucial role in enhancing productivity and efficiency in the metalworking industry.
History of Cemented Carbide Rods
Cemented carbide rods have a rich history that dates back several decades. The development of cemented carbide as a material can be traced back to the early 20th century, with notable advancements made in the 1920s and 1930s. The use of cemented carbide rods became increasingly popular in various industries, including manufacturing, mining, and construction, due to their exceptional hardness, wear resistance, and high strength. Over the years, cemented carbide rods have undergone continuous improvements, leading to the development of various grades and compositions to suit specific applications. Today, cemented carbide rods are widely used in cutting tools, drilling equipment, and wear parts, playing a crucial role in enhancing productivity and efficiency in various industrial processes.
Applications of Cemented Carbide Rods
Cemented carbide rods find a wide range of applications in various industries. One of the key uses of these rods is in the manufacturing of cutting tools, such as drills, end mills, and inserts. The exceptional hardness and wear resistance of cemented carbide make it an ideal material for these applications, ensuring long tool life and high cutting speeds. Additionally, cemented carbide rods are also utilized in the production of wear parts for mining and construction equipment, where their durability and toughness are highly valued. Furthermore, these rods are used in the fabrication of precision components for the automotive and aerospace industries, where tight tolerances and excellent mechanical properties are crucial. Overall, the applications of cemented carbide rods are diverse and essential in enhancing productivity and performance across various sectors.
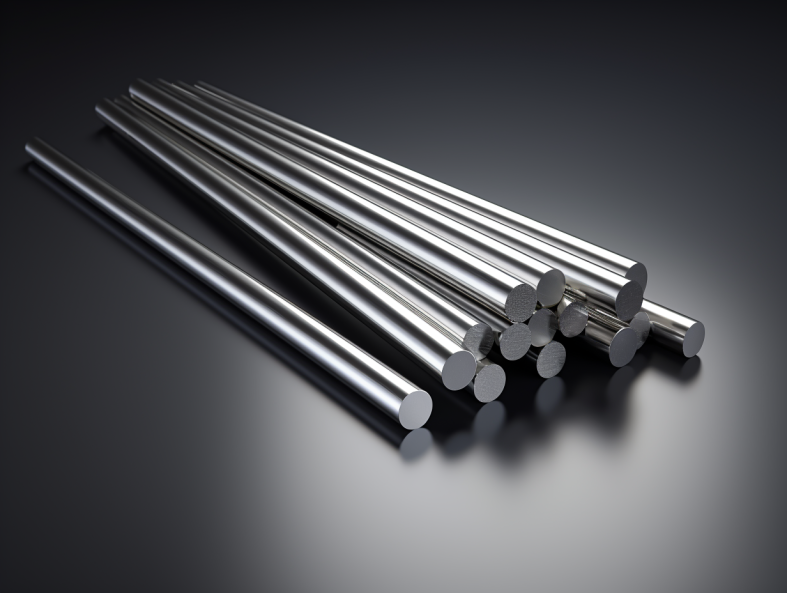
Composition
Tungsten Carbide
Tungsten Carbide is a type of cemented carbide that is widely used in various industries. It is known for its exceptional hardness, strength, and resistance to wear and corrosion. Tungsten Carbide is composed of tungsten and carbon atoms, which are combined through a process called sintering. This material is commonly used in the manufacturing of cutting tools, such as drills, milling cutters, and inserts for machining operations. Due to its high hardness, Tungsten Carbide can withstand high temperatures and is often used in applications where extreme conditions are present. Additionally, it is also used in the production of wear-resistant parts, such as nozzles, valves, and bearings. Overall, Tungsten Carbide is a versatile material that plays a crucial role in many industries, providing durability and efficiency in various applications.
Cobalt
Cobalt is an essential component in cemented carbide rods. It acts as a binder, holding the tungsten carbide particles together. This combination of cobalt and tungsten carbide results in a material that is extremely hard and wear-resistant. Cobalt also improves the toughness and strength of the cemented carbide rods, making them suitable for a wide range of applications, including cutting tools, mining tools, and wear parts. The amount of cobalt in the cemented carbide rods can vary depending on the desired properties and applications.
Other Additives
Cemented carbide rods are widely used in various industries for their exceptional hardness and strength. However, in addition to the main components of tungsten carbide and cobalt, there are also other additives that play a crucial role in enhancing the performance of these rods. These additives, such as titanium carbide and tantalum carbide, help improve the wear resistance and toughness of the cemented carbide rods, making them suitable for demanding applications in cutting tools, mining equipment, and wear parts. Furthermore, the addition of these additives also allows for the customization of the rods’ properties, enabling manufacturers to meet specific requirements of their customers. Overall, these other additives contribute to the overall quality and versatility of cemented carbide rods, making them a preferred choice in various industrial applications.
Manufacturing Process
Powder Preparation
Powder preparation is a crucial step in the production of cemented carbide rods. It involves the careful selection and blending of raw materials to achieve the desired composition and properties. The process begins with the milling of tungsten carbide powder, which is then mixed with a binder material such as cobalt. This mixture is then subjected to a series of heating and cooling cycles to ensure proper bonding and uniform distribution of the binder. The resulting powder is then ready to be pressed into the desired shape and size, forming the basis for the subsequent steps in the production of cemented carbide rods.
Mixing and Blending
Mixing and blending are crucial processes in the production of cemented carbide rods. During the mixing stage, various materials such as tungsten carbide powder, cobalt powder, and other additives are combined to create the desired composition. This composition will determine the properties and performance of the final product. The blending process ensures that the materials are thoroughly mixed and distributed evenly, resulting in a homogenous mixture. Proper mixing and blending techniques are essential to achieve consistent quality and enhance the overall performance of cemented carbide rods.
Compaction and Shaping
Compaction and shaping are crucial steps in the production of cemented carbide rods. During the compaction process, a mixture of tungsten carbide powder and a binder is compressed at high pressure to form a compact. This compact is then subjected to shaping, where it is either extruded or pressed into the desired shape. The compaction and shaping processes ensure that the cemented carbide rods have the necessary density and shape to exhibit their desired mechanical properties. These steps require precision and expertise to achieve the desired quality and performance of the final product.
Properties
Hardness
Cemented carbide rods are well-known for their exceptional hardness. This is due to the combination of tungsten carbide particles, which provide the material with high wear resistance, and a metallic binder, typically cobalt or nickel, which enhances the toughness of the rods. The hardness of cemented carbide rods makes them ideal for applications that require resistance to abrasion, such as cutting tools, machining components, and drilling equipment. Additionally, their hardness allows for higher cutting speeds and improved productivity in various industries, including automotive, aerospace, and manufacturing.
Wear Resistance
Cemented carbide rods exhibit exceptional wear resistance, making them ideal for various industrial applications. The combination of tungsten carbide particles embedded in a metallic binder gives these rods their remarkable hardness and durability. They can withstand high temperatures, heavy loads, and abrasive environments, ensuring long-lasting performance. Whether used in drilling, cutting, or machining operations, cemented carbide rods provide superior wear resistance, reducing the need for frequent tool replacements and increasing productivity. With their excellent wear resistance properties, these rods are a reliable choice for industries such as automotive, aerospace, and mining, where high-performance tools are essential.
Strength
Cemented carbide rods are known for their exceptional strength, making them a popular choice in various industries. These rods are made by combining tungsten carbide particles with a binder material, such as cobalt. The resulting material is incredibly hard and durable, allowing it to withstand high temperatures and heavy loads. This strength makes cemented carbide rods ideal for applications that require resistance to wear, impact, and corrosion. Whether used in machining, mining, or construction, these rods provide the necessary strength to tackle even the toughest tasks with ease.
Advantages
High Hardness
Cemented carbide rods are known for their exceptional hardness, making them a popular choice in various industries. In particular, the high hardness of these rods is a key characteristic that sets them apart from other materials. The high hardness of cemented carbide rods allows them to withstand extreme conditions and resist wear and tear, making them ideal for applications that require durability and longevity. Additionally, the high hardness of these rods ensures superior performance and precision, making them essential in industries such as metalworking, mining, and construction. Overall, the high hardness of cemented carbide rods makes them an indispensable material for demanding applications where strength and reliability are paramount.
Excellent Wear Resistance
Cemented carbide rods exhibit excellent wear resistance, making them a popular choice in various industries. The unique combination of tungsten carbide and a metallic binder creates a material that can withstand high temperatures, heavy loads, and abrasive environments. This exceptional wear resistance allows cemented carbide rods to maintain their shape and performance for extended periods, reducing the need for frequent replacements. Whether used in cutting tools, drilling equipment, or wear parts, cemented carbide rods provide reliable and long-lasting performance, ensuring efficient and cost-effective operations.
Good Thermal Conductivity
Cemented carbide rods exhibit excellent thermal conductivity, making them a preferred choice in various applications. The unique combination of tungsten carbide and a metallic binder allows for efficient heat transfer, ensuring that heat is quickly dissipated from the source. This property is particularly beneficial in high-temperature environments where maintaining optimal operating conditions is crucial. With their good thermal conductivity, cemented carbide rods enable enhanced performance, increased productivity, and extended tool life, making them an indispensable component in industries such as aerospace, automotive, and manufacturing.
Applications
Cutting Tools
Cemented carbide rods are widely used in the manufacturing of cutting tools. These rods, made from a combination of tungsten carbide and cobalt, exhibit exceptional hardness and wear resistance. They are known for their ability to withstand high temperatures and maintain their cutting performance even under extreme conditions. The unique properties of cemented carbide rods make them ideal for applications that require precision cutting, such as machining, drilling, and milling. With their superior durability and performance, cemented carbide rods have become an indispensable component in the tool industry.
Milling Inserts
Milling inserts are an essential component in the field of machining and cutting. These small, replaceable cutting tools are designed to fit into the slots or pockets of milling machines, enabling precise and efficient material removal. Made from cemented carbide rods, milling inserts offer exceptional hardness, wear resistance, and heat resistance, making them ideal for high-speed machining operations. With their various geometries and coatings, milling inserts can be customized to meet specific machining requirements, ensuring optimal performance and extended tool life. Whether used in aerospace, automotive, or general machining applications, milling inserts play a crucial role in achieving superior accuracy and productivity.
Drilling Tools
Cemented carbide rods are widely used in the manufacturing of drilling tools. These rods are known for their exceptional hardness and wear resistance, making them ideal for drilling through tough materials such as concrete, metal, and rock. The high strength and durability of cemented carbide rods allow for efficient and precise drilling operations, resulting in improved productivity and reduced downtime. Additionally, the excellent heat resistance of these rods ensures that they can withstand the high temperatures generated during drilling, further enhancing their performance and longevity. Overall, cemented carbide rods are essential components in the construction, mining, and oil and gas industries, enabling the development of reliable and efficient drilling tools.