Introduction
Definition of cemented carbide rod
A cemented carbide rod is a type of cutting tool used in milling applications. It is made from a combination of tungsten carbide particles and a binder material, typically cobalt. The tungsten carbide particles provide the rod with exceptional hardness and wear resistance, while the binder material ensures its strength and durability. Cemented carbide rods are widely used in the manufacturing industry for milling operations, as they can effectively cut through various materials, including steel, cast iron, and aluminum. These rods are known for their high cutting speeds, excellent precision, and long tool life, making them a preferred choice for end mill applications.
Applications of cemented carbide rod
Cemented carbide rods are widely used in various applications due to their exceptional hardness and wear resistance. One of the main applications of cemented carbide rods is in the manufacturing of end mills. End mills are cutting tools used in milling operations to remove material from a workpiece. The high hardness of cemented carbide rods allows end mills to effectively cut through different materials, including metals, plastics, and composites. Additionally, the excellent wear resistance of cemented carbide rods ensures that the end mills maintain their sharpness and cutting performance over an extended period of use. This makes cemented carbide rods an ideal choice for end mill applications, providing precision and durability in machining processes.
Importance of cemented carbide rod in end mill manufacturing
Cemented carbide rods play a crucial role in the manufacturing of end mills. These rods are made from a combination of tungsten carbide and cobalt, resulting in a material that is extremely hard and wear-resistant. The importance of cemented carbide rods lies in their ability to withstand the high temperatures and pressures involved in cutting and milling operations. They provide the necessary strength and durability to ensure the longevity of end mills, allowing for efficient and precise machining. Additionally, cemented carbide rods offer excellent performance in terms of tool life, cutting speed, and surface finish. Their exceptional hardness and resistance to wear make them an ideal choice for end mill manufacturing, contributing to improved productivity and cost-effectiveness in various industries.
Composition and Properties
Materials used in cemented carbide rod
Cemented carbide rods for end mills are made from a combination of tungsten carbide and a binder material, typically cobalt. Tungsten carbide, known for its exceptional hardness, provides the rod with the necessary strength and wear resistance. The binder material, on the other hand, acts as a binding agent, holding the tungsten carbide particles together and providing toughness to the rod. The use of these materials in the manufacturing of cemented carbide rods ensures that the end mills have high cutting performance, excellent durability, and can withstand the demanding conditions of machining operations.
Physical and mechanical properties of cemented carbide rod
Cemented carbide rod is a highly durable material used in the manufacturing of end mills. It exhibits excellent physical and mechanical properties, making it an ideal choice for various cutting applications. The rod is known for its high hardness, which allows it to withstand extreme temperatures and resist wear and abrasion. Additionally, it has a high compressive strength, ensuring its ability to withstand heavy loads and maintain its shape under pressure. The cemented carbide rod also offers good thermal conductivity, enabling efficient heat dissipation during cutting operations. Overall, the physical and mechanical properties of cemented carbide rod make it a reliable and long-lasting option for end mill production.
Effect of composition on the properties of cemented carbide rod
The composition of cemented carbide rod plays a crucial role in determining its properties. The selection of different elements and their proportions can greatly impact the hardness, toughness, and wear resistance of the rod. For instance, adding cobalt to the tungsten carbide matrix enhances the strength and fracture resistance, while increasing the carbon content improves the hardness and wear resistance. Moreover, the presence of other elements like titanium, tantalum, and niobium can further enhance the performance of the rod by providing additional grain refinement and resistance to deformation. Therefore, understanding the effect of composition on the properties of cemented carbide rod is essential for optimizing its performance in end mill applications.
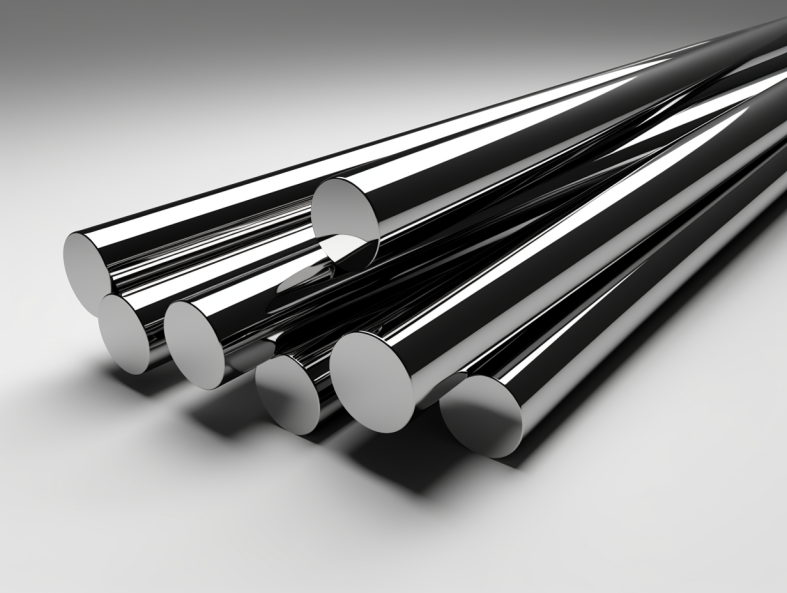
Manufacturing Process
Powder preparation
In the process of manufacturing cemented carbide rods for end mills, powder preparation is a crucial step. The quality of the powder used directly affects the performance and durability of the end mill. The powder is typically made by blending tungsten carbide with a binder material, such as cobalt, in precise proportions. This mixture is then milled to achieve a fine and homogeneous powder. The powder preparation process requires strict control over the particle size, distribution, and chemical composition to ensure the desired properties of the end mill. Additionally, the powder must undergo thorough testing and analysis to meet the specifications and standards set by the industry. Overall, the powder preparation stage plays a fundamental role in the production of high-quality cemented carbide rods for end mills.
Mixing and blending
Mixing and blending are crucial steps in the production of cemented carbide rods for end mills. These processes involve combining various raw materials, such as tungsten carbide powder and cobalt powder, in precise proportions to achieve the desired properties and performance of the end product. The mixture is then thoroughly blended to ensure uniform distribution of the components. This step is essential for achieving consistent quality and strength in the final cemented carbide rods. The mixing and blending process requires specialized equipment and expertise to ensure accurate and efficient production. Overall, the success of the cemented carbide rod manufacturing process heavily relies on the effectiveness of the mixing and blending phase.
Compaction and shaping
Compaction and shaping are crucial steps in the manufacturing process of cemented carbide rods for end mills. During compaction, a mixture of tungsten carbide powder and a binder is pressed into a desired shape under high pressure. This process ensures that the carbide particles are densely packed, providing the rod with excellent hardness and wear resistance. After compaction, the shaped rod is sintered in a furnace at high temperatures, which allows the binder to be removed and the tungsten carbide particles to bond together. The sintering process further enhances the strength and durability of the cemented carbide rod, making it suitable for the demanding applications of end mills. Overall, compaction and shaping are critical stages in the production of cemented carbide rods, ensuring the final product’s quality and performance.
Heat Treatment
Sintering
Sintering is a crucial process in the production of cemented carbide rods for end mills. It involves the heating of the raw materials, typically tungsten carbide and cobalt, to a high temperature in a controlled atmosphere. During sintering, the particles of tungsten carbide are bonded together, forming a dense and hard structure. This process not only enhances the strength and toughness of the carbide rod but also improves its wear resistance and cutting performance. Sintering is a highly specialized and precise technique that plays a vital role in ensuring the quality and durability of cemented carbide rods for end mills.
Cooling and annealing
Cooling and annealing are crucial steps in the production process of cemented carbide rods for end mills. After the rods are shaped and formed, they go through a cooling process to ensure their structural integrity. This cooling process helps to reduce any residual stresses and improve the overall hardness and toughness of the rods. Once the cooling process is complete, the rods undergo annealing, which involves heating them to a specific temperature and then slowly cooling them. Annealing helps to further enhance the strength and durability of the rods, making them suitable for high-speed machining applications. By carefully controlling the cooling and annealing processes, manufacturers can produce cemented carbide rods that exhibit excellent performance and longevity in end mill applications.
Hardening and tempering
Hardening and tempering are crucial processes in the production of cemented carbide rods for end mills. Hardening involves heating the rods to a high temperature and then rapidly cooling them to increase their hardness and strength. This process helps to enhance the wear resistance and durability of the rods, allowing them to withstand the demanding conditions of end milling operations. Tempering, on the other hand, involves reheating the hardened rods to a specific temperature and then cooling them slowly. This step helps to reduce the brittleness of the rods and improve their toughness and flexibility. By carefully controlling the hardening and tempering processes, manufacturers can ensure that the cemented carbide rods for end mills have the optimal combination of hardness, strength, and toughness, making them highly effective tools for machining applications.
Quality Control
Inspection of raw materials
The inspection of raw materials is a crucial step in the production of cemented carbide rods for end mills. It ensures that only high-quality materials are used, resulting in the production of durable and reliable end mills. During the inspection process, various parameters such as chemical composition, grain size, and hardness are carefully analyzed to meet the required specifications. Any deviation from the desired standards is immediately addressed to maintain the quality of the end product. By conducting thorough inspections of raw materials, manufacturers can guarantee the performance and longevity of cemented carbide rods for end mills.
Testing of physical and mechanical properties
In order to ensure the quality and performance of cemented carbide rods for end mills, extensive testing of their physical and mechanical properties is conducted. These tests evaluate various characteristics such as hardness, toughness, wear resistance, and dimensional stability. Hardness testing is performed to determine the material’s ability to resist indentation and deformation, while toughness testing assesses its ability to withstand impacts and shocks without fracturing. Wear resistance testing measures the rod’s ability to withstand abrasive forces and maintain its cutting edge over prolonged use. Dimensional stability testing ensures that the rod maintains its shape and size under different temperature and pressure conditions. By subjecting cemented carbide rods to rigorous testing, manufacturers can guarantee their reliability and performance in demanding milling applications.
Dimensional inspection
Dimensional inspection is a crucial step in ensuring the quality and performance of cemented carbide rods for end mills. During this process, various measurements are taken to verify the dimensions and tolerances of the rods. This includes checking the diameter, length, and straightness of the rods, as well as examining the surface finish and any potential defects. By conducting a thorough dimensional inspection, manufacturers can ensure that the cemented carbide rods meet the required specifications, resulting in high-quality end mills that deliver precise and efficient cutting performance.
Applications
End mills for milling
End mills for milling are essential tools in machining applications. They are used to remove material from a workpiece, creating various shapes and profiles. One type of end mill that is commonly used is the cemented carbide rod for end mill. This type of end mill is known for its durability and high cutting performance. It is made from a combination of tungsten carbide and cobalt, which gives it excellent hardness and wear resistance. The cemented carbide rod for end mill is suitable for milling a wide range of materials, including steel, stainless steel, cast iron, and aluminum. With its sharp cutting edges and efficient chip evacuation, this type of end mill ensures smooth and precise milling operations. Whether it’s for roughing, finishing, or profiling, the cemented carbide rod for end mill is a reliable tool that delivers consistent results.
Drills for drilling
Cemented carbide rods are widely used in the manufacturing of end mills, especially for drilling applications. These rods are known for their exceptional hardness and wear resistance, making them ideal for drilling through various materials such as metal, wood, and plastics. The unique composition of cemented carbide allows the end mill to withstand high temperatures and maintain its cutting edge, resulting in efficient and precise drilling operations. With their durability and reliability, cemented carbide rods have become a preferred choice for professionals and hobbyists alike when it comes to drilling tasks.
Reamers for precision hole making
Reamers for precision hole making are essential tools in various industries, including manufacturing and engineering. These specialized cutting tools are designed to enlarge and refine existing holes with utmost accuracy and precision. One such type of reamer is the cemented carbide rod for end mill. This innovative tool is made from a combination of tungsten carbide and cobalt, resulting in a strong and durable material that can withstand high temperatures and extreme conditions. The cemented carbide rod for end mill is specifically designed to create smooth and precise holes in a wide range of materials, including steel, aluminum, and composite materials. With its exceptional cutting performance and long tool life, this reamer is widely used in applications that require the highest level of precision and quality. Whether it’s for aerospace, automotive, or general machining purposes, the cemented carbide rod for end mill is the go-to tool for achieving accurate and reliable hole making.