Introduction
Definition of Cemented Carbide Rod
A cemented carbide rod is a type of tool material that is widely used in various industrial applications. It is made by mixing tungsten carbide particles with a binder material, such as cobalt, and then compressing and sintering the mixture at high temperatures. The resulting material is extremely hard and wear-resistant, making it ideal for cutting, drilling, and shaping hard materials like steel, cast iron, and stainless steel. Cemented carbide rods are commonly used in the manufacturing of cutting tools, such as drills, end mills, and reamers, as well as in the production of wear parts, such as dies and punches. They offer excellent performance and durability, making them a popular choice among manufacturers and machining professionals.
Importance of Cemented Carbide Rod
Cemented carbide rods play a crucial role in various industries due to their exceptional properties. These rods are widely used in the manufacturing of cutting tools, such as drills, end mills, and reamers, as they offer high hardness, wear resistance, and toughness. The importance of cemented carbide rods lies in their ability to provide superior cutting performance, increased productivity, and extended tool life. With their excellent thermal conductivity and resistance to deformation, these rods ensure efficient machining operations, making them a preferred choice for precision machining applications. Moreover, the exceptional strength and durability of cemented carbide rods make them suitable for challenging machining conditions, including high-speed cutting and heavy-duty operations. Overall, the use of cemented carbide rods significantly enhances the performance and reliability of cutting tools, contributing to the success of various industries.
History of Cemented Carbide Rod
The history of cemented carbide rod dates back to the early 20th century. It was first developed by researchers who were looking for a material that could withstand high temperatures and extreme conditions. The breakthrough came when they discovered that by combining tungsten carbide with a binder material, they could create a strong and durable rod. This innovation revolutionized various industries, including mining, construction, and manufacturing. Today, cemented carbide rod factories play a crucial role in producing high-quality rods that are used in a wide range of applications, from cutting tools to wear-resistant parts.
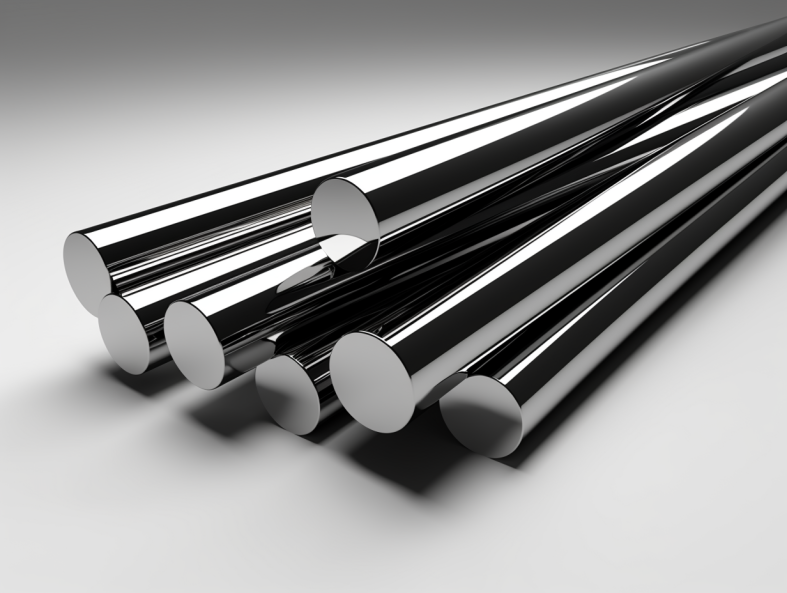
Manufacturing Process
Raw Materials
Raw materials play a crucial role in the production of cemented carbide rods. The main components used in the manufacturing process include tungsten carbide powder, cobalt powder, and other additives. Tungsten carbide powder is the primary raw material, known for its exceptional hardness and wear resistance. Cobalt powder is used as a binder to hold the tungsten carbide particles together. The quality and consistency of the raw materials directly impact the performance and durability of the final cemented carbide rods. Therefore, sourcing high-quality raw materials from reliable suppliers is essential for cemented carbide rod factories.
Mixing and Blending
Mixing and blending are crucial processes in cemented carbide rod factories. These processes involve combining different materials and ensuring a homogeneous mixture. The quality of the mixture directly impacts the final product’s performance and durability. Skilled technicians carefully measure and weigh the raw materials before introducing them into the mixing equipment. The mixing process is carefully controlled to achieve the desired composition and consistency. Specialized blending techniques, such as ball milling or attrition milling, may be employed to further enhance the uniformity of the mixture. The resulting mixture is then ready for the subsequent steps in the cemented carbide rod manufacturing process.
Compacting and Shaping
Compacting and shaping are crucial steps in the manufacturing process of cemented carbide rods. During the compacting stage, a mixture of tungsten carbide powder and a binder material is pressed into a specific shape using high pressure. This helps to ensure the uniform distribution of the tungsten carbide particles, resulting in a dense and strong rod. After compacting, the shaped rod is then sintered at high temperatures to bond the particles together and further enhance its strength and durability. The compacting and shaping processes are carefully controlled to achieve the desired dimensions and properties of the cemented carbide rods, making them suitable for various industrial applications.
Properties of Cemented Carbide Rod
Hardness
Hardness is a crucial characteristic of cemented carbide rods. It refers to the ability of the material to resist deformation and wear. The hardness of cemented carbide rods is typically measured using the Rockwell scale or the Vickers scale. These rods are known for their exceptional hardness, making them highly resistant to abrasion, impact, and heat. The high hardness of cemented carbide rods ensures their longevity and reliability in various industrial applications, such as metal cutting, mining, and machining. Additionally, the hardness of these rods allows for precise and efficient machining, resulting in high-quality finished products.
Wear Resistance
Wear resistance is a crucial characteristic when it comes to cemented carbide rods. These rods are specifically designed to withstand extreme wear and tear in various industrial applications. The unique composition of cemented carbide, which typically consists of tungsten carbide particles embedded in a metallic binder, provides exceptional hardness and resistance to abrasion. This enables the rods to maintain their performance and durability even under harsh operating conditions. Whether it is drilling, cutting, or shaping, cemented carbide rods with high wear resistance ensure longer tool life and improved productivity. Manufacturers of cemented carbide rods prioritize the development of materials and processes that enhance wear resistance, making them reliable components for industries such as mining, construction, and manufacturing.
Toughness
Toughness is a crucial characteristic of cemented carbide rods. It refers to the ability of the material to absorb energy and deform without fracturing. In the context of cemented carbide rods, toughness is especially important as these rods are often subjected to high impact and heavy load conditions. A high level of toughness ensures that the rods can withstand these demanding applications without breaking or chipping. This is achieved through the careful selection of carbide grain size, binder composition, and manufacturing processes. By enhancing the toughness of cemented carbide rods, manufacturers can provide customers with reliable and durable products that can effectively handle the challenges of various industrial applications.
Applications
Cutting Tools
Cutting tools play a crucial role in various industries, including manufacturing and construction. They are essential for shaping, drilling, and cutting different materials with precision and efficiency. One of the key components used in cutting tools is cemented carbide rods. These rods are known for their exceptional hardness and wear resistance, making them ideal for demanding cutting applications. Cemented carbide rod factories specialize in the production of these high-quality rods, ensuring consistent and reliable performance. With their expertise and advanced manufacturing processes, these factories contribute to the development of cutting-edge cutting tools that enhance productivity and deliver superior results.
Mining Tools
Mining tools are essential for the extraction of minerals and ores from the earth’s crust. One crucial component of these tools is cemented carbide rods. Cemented carbide rods are widely used in the mining industry due to their exceptional hardness and resistance to wear and corrosion. These rods are manufactured in specialized factories that employ advanced technologies and stringent quality control measures. The production process involves carefully selecting the right blend of tungsten carbide powders and binding agents, followed by pressing, sintering, and precision machining. The resulting cemented carbide rods are highly durable and capable of withstanding the harsh conditions encountered in mining operations. They play a vital role in drilling, cutting, and crushing rocks, making them indispensable tools for miners worldwide.
Wear Parts
Wear parts are essential components in various industries, including manufacturing, construction, and mining. These parts are designed to withstand high levels of wear and tear, ensuring the longevity and efficiency of machinery and equipment. Cemented carbide rods are widely used in the production of wear parts due to their exceptional hardness, strength, and resistance to abrasion. These rods are commonly used in the manufacturing of cutting tools, such as drills and end mills, as well as in the production of wear-resistant components for machinery and equipment. With their superior performance and durability, cemented carbide rods have become a popular choice for many factories specializing in the production of wear parts.
Advantages and Disadvantages
Advantages of Cemented Carbide Rod
Cemented carbide rods are widely used in various industries due to their numerous advantages. One of the key advantages of cemented carbide rods is their exceptional hardness and wear resistance. This makes them ideal for applications that require cutting, drilling, or milling in tough materials such as steel, cast iron, and stainless steel. Additionally, cemented carbide rods have excellent thermal stability, which allows them to withstand high temperatures without losing their hardness or shape. Another advantage is their exceptional strength-to-weight ratio, making them lightweight yet incredibly strong. This makes cemented carbide rods highly versatile and suitable for a wide range of applications, including tooling, machining, and wear parts. Overall, the advantages of cemented carbide rods make them a preferred choice for many industries seeking durable and high-performance materials.
Disadvantages of Cemented Carbide Rod
Cemented carbide rods, while widely used in various industries, do have some disadvantages. One of the main drawbacks is their brittleness. Due to their high hardness, these rods are prone to cracking or breaking under excessive stress or impact. Additionally, cemented carbide rods have limited resistance to thermal shock, which means they can crack when exposed to rapid temperature changes. Another disadvantage is their high cost compared to other types of rod materials. Despite these drawbacks, cemented carbide rods remain popular due to their exceptional wear resistance and durability.
Comparison with Other Materials
Cemented carbide rods have gained significant popularity in various industries due to their exceptional properties and performance. When compared to other materials, such as steel and ceramic, cemented carbide rods exhibit superior hardness, wear resistance, and thermal stability. The high hardness of cemented carbide rods allows them to withstand heavy loads and resist deformation, making them ideal for applications that require high cutting speeds and precision. Additionally, the excellent wear resistance of cemented carbide rods ensures a longer tool life, reducing the need for frequent replacements and increasing productivity. Moreover, the exceptional thermal stability of cemented carbide rods allows them to operate at elevated temperatures without compromising their performance. This makes them suitable for demanding applications that involve high-speed machining and heavy-duty cutting. Overall, cemented carbide rods offer unmatched performance and durability, making them a preferred choice in various industrial applications.
Future Trends
Advancements in Manufacturing
In recent years, there have been significant advancements in manufacturing, particularly in the field of cemented carbide rod factories. These factories have embraced cutting-edge technologies and innovative processes to enhance the production of cemented carbide rods. One notable advancement is the use of computer numerical control (CNC) machines, which have revolutionized the manufacturing process by providing precise and efficient machining. Additionally, the integration of automation and robotics has greatly improved productivity and reduced human error. With these advancements, cemented carbide rod factories are able to produce high-quality rods that meet the stringent requirements of various industries, including automotive, aerospace, and machining. The continuous advancements in manufacturing techniques and technologies in cemented carbide rod factories have undoubtedly contributed to the overall growth and success of the industry.
New Applications
Cemented carbide rods have been widely used in various industries due to their exceptional hardness and wear resistance. In recent years, there has been a surge in the development of new applications for these rods. From cutting tools to wear parts, cemented carbide rods are now being utilized in innovative ways to enhance productivity and efficiency. With advancements in technology, manufacturers are constantly exploring new possibilities, pushing the boundaries of what cemented carbide rods can achieve. As a result, industries such as automotive, aerospace, and machining are benefiting from the superior performance and durability offered by cemented carbide rods in their applications. The versatility and reliability of these rods make them an indispensable component in the manufacturing processes of many factories worldwide.
Research and Development
Research and development is an essential component of any industry, and the cemented carbide rod factories are no exception. These factories prioritize continuous innovation and improvement in their products and processes. Through extensive research, they aim to develop cutting-edge technologies and materials that meet the ever-evolving demands of the market. The dedicated R&D teams in these factories work tirelessly to explore new possibilities, test different formulations, and optimize the performance of cemented carbide rods. Their efforts not only ensure the production of high-quality and durable products but also contribute to the advancement of the industry as a whole. Research and development is the driving force behind the success of cemented carbide rod factories, enabling them to stay at the forefront of technological advancements and maintain their competitive edge.