Cemented carbide inserts, also known as tungsten carbide inserts, are a critical component in the world of metalworking and machining. They are indispensable for their durability, efficiency, and versatility. If you’re diving into the world of machining or simply looking to upgrade your tooling arsenal, this guide will walk you through everything you need to know about cemented carbide inserts. From their types and applications to material properties and selecting the right one, let’s get started.
Overview of Cemented Carbide Inserts
Cemented carbide inserts are cutting tools used extensively in manufacturing and metalworking. They consist of a composite material made up of carbide particles bonded together by a metallic binder. This unique composition gives them superior hardness, wear resistance, and the ability to withstand high temperatures, making them ideal for cutting, drilling, and shaping metal materials.
Why Cemented Carbide?
- Durability: Cemented carbide inserts are incredibly durable and can withstand heavy usage.
- Efficiency: They maintain sharpness and cutting efficiency over long periods.
- Versatility: Suitable for a wide range of materials and machining operations.
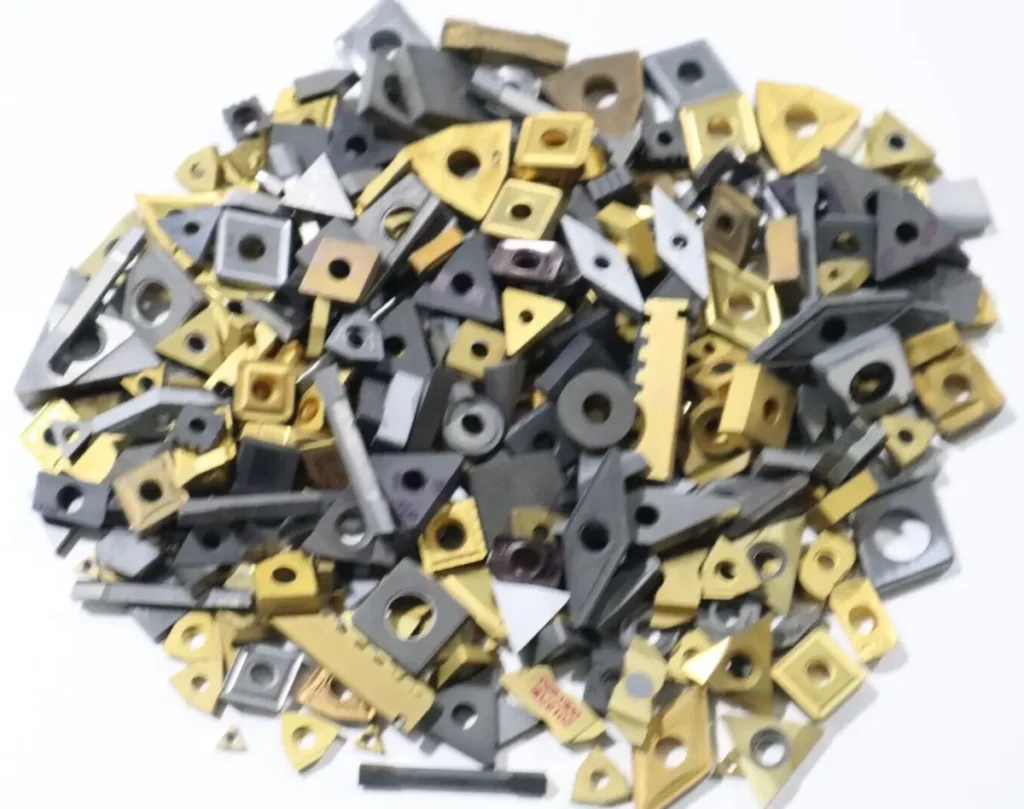
Types of Cemented Carbide Inserts
There are various types of cemented carbide inserts designed for specific applications. Here’s a breakdown of some common types:
Insert Type | Description |
---|---|
CNMG | General-purpose insert with 80° cutting edge, suitable for roughing and finishing. |
DNMG | 55° cutting edge insert, ideal for finishing operations. |
TNMG | Triangular insert, versatile for both roughing and finishing. |
WNMG | Trigon shape with 80° cutting edge, used for roughing and interrupted cuts. |
SNMG | Square insert, very strong, used for heavy-duty operations. |
CCMT | Single-sided insert with 80° cutting edge, used for turning applications. |
VBMT | Diamond-shaped insert, used for fine finishing. |
RCMT | Round insert, ideal for profiling and contouring. |
APKT | Rectangular insert, used for milling applications. |
RPGN | Round insert, great for profiling soft materials. |
Applications of Cemented Carbide Inserts
Cemented carbide inserts are used in a variety of machining operations. Here’s a look at their applications:
Application | Insert Types | Details |
---|---|---|
Turning | CNMG, DNMG, CCMT, VBMT | Turning operations involve rotating the workpiece while a stationary cutting tool removes material. |
Milling | APKT, RPGN | Milling uses a rotating cutting tool to remove material from a workpiece in various directions. |
Drilling | WNMG, SNMG | Drilling operations create round holes in a workpiece using a rotating drill bit. |
Boring | CNMG, VBMT | Boring enlarges existing holes to achieve greater accuracy. |
Profiling | RCMT, RPGN | Profiling operations create complex contours and shapes on a workpiece. |
Threading | TNMG, VBMT | Threading inserts are used to cut screw threads into a workpiece. |
Grooving | SNMG, CCMT | Grooving involves cutting narrow channels into a workpiece. |
Parting | SNMG, WNMG | Parting operations cut off a section of a workpiece. |
Face Milling | APKT, CCMT | Face milling uses a cutter to remove material from the surface of a workpiece to create a flat surface. |
Interrupted Cutting | WNMG, SNMG | Inserts designed for interrupted cutting can withstand shocks and impacts from irregular cuts. |
Material Properties of Cemented Carbide Inserts
Understanding the material properties of cemented carbide inserts is crucial for selecting the right one for your application.
Property | Description |
---|---|
Hardness | Cemented carbide inserts are extremely hard, typically measuring 8.5-9 on the Mohs scale. |
Wear Resistance | High resistance to wear, making them ideal for cutting and abrasive applications. |
Toughness | Despite their hardness, they have sufficient toughness to withstand impact and shocks. |
Heat Resistance | Able to maintain hardness and performance at high temperatures, often exceeding 1000°C. |
Corrosion Resistance | Resistant to corrosion, extending their lifespan in various environments. |
Thermal Conductivity | Good thermal conductivity helps in heat dissipation during cutting operations. |
Density | High density, typically between 14.5-15.0 g/cm³. |
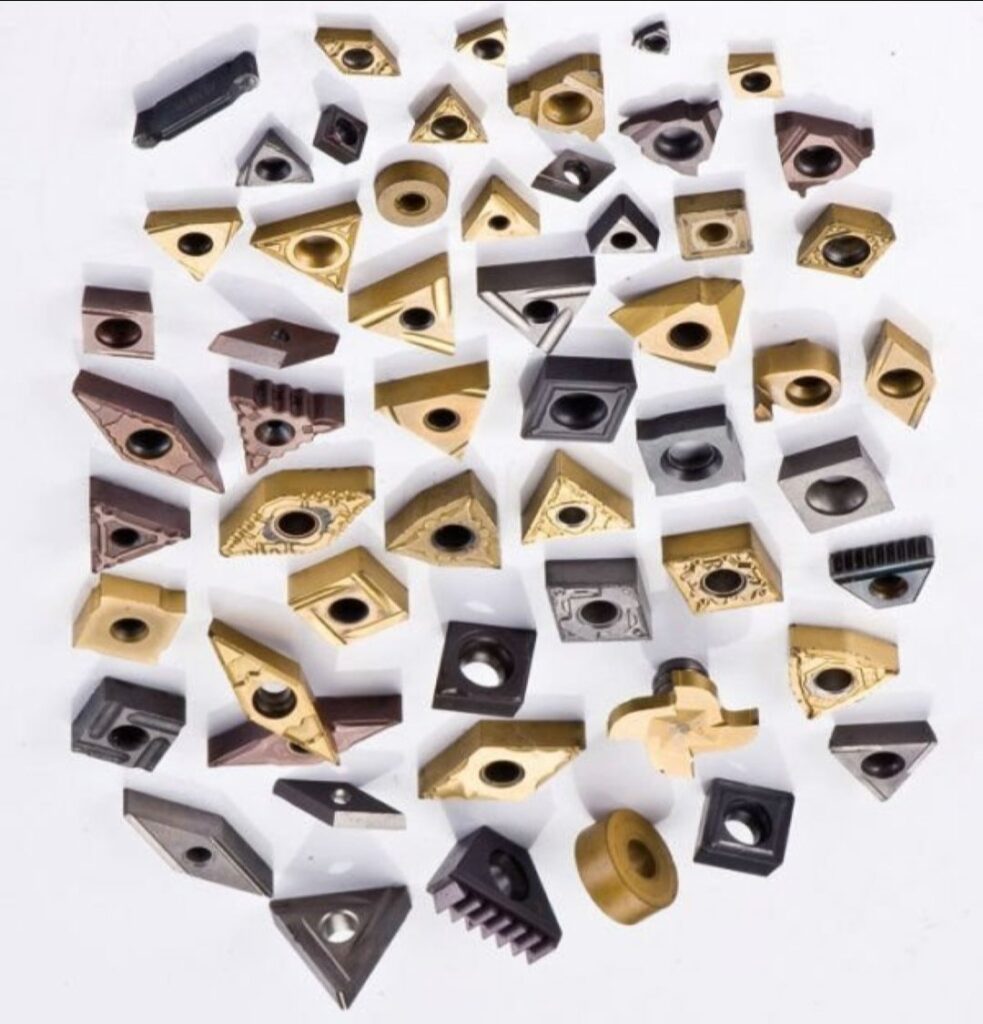
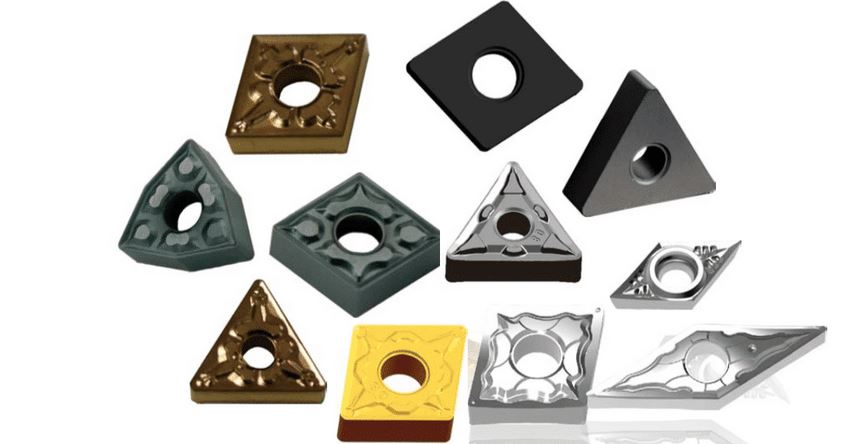
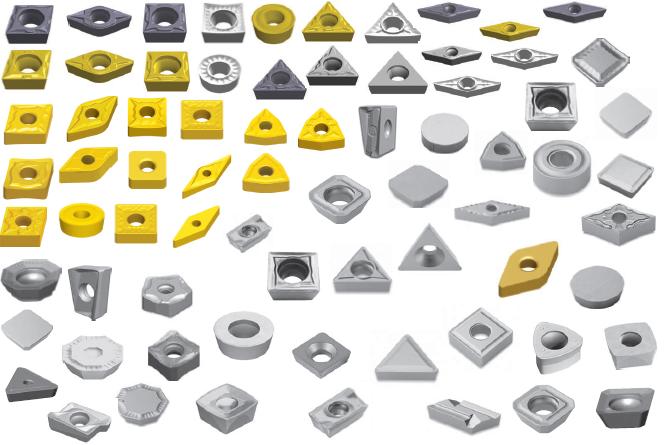
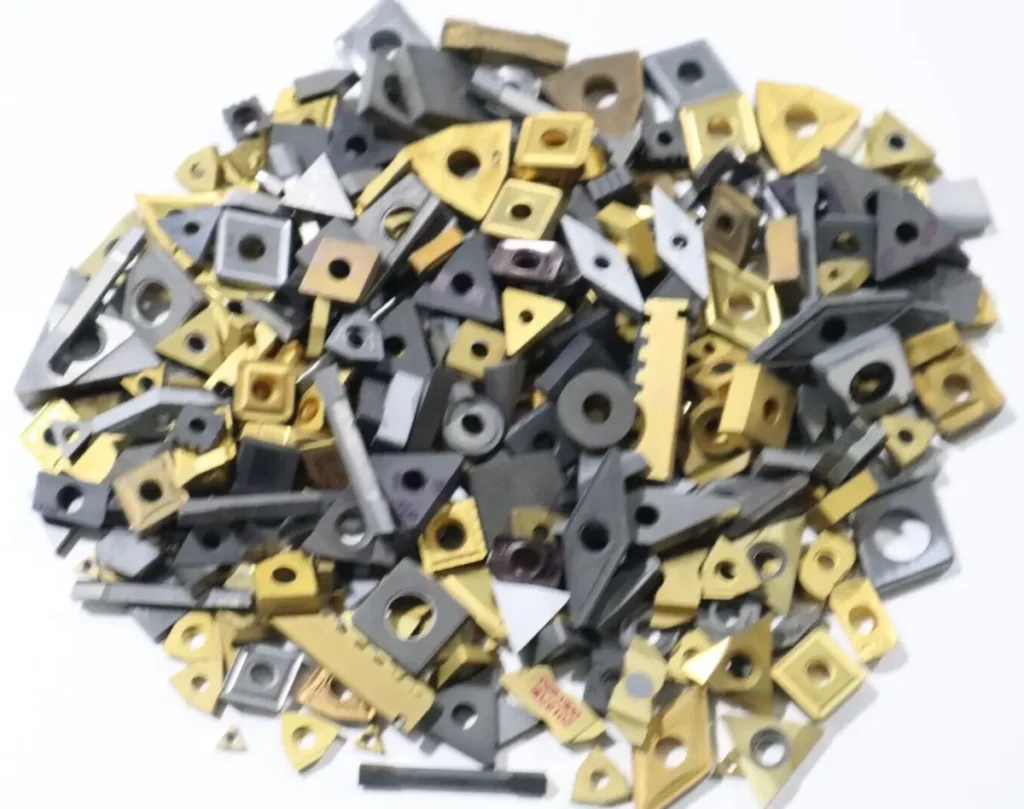
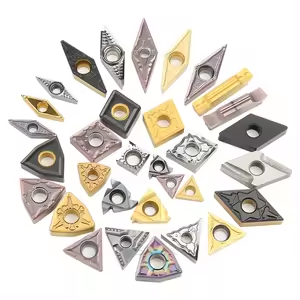
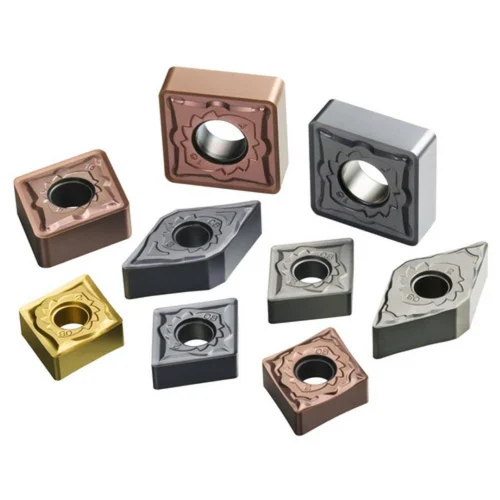
Composition and Characteristics
The composition of cemented carbide inserts affects their properties and performance.
Component | Description |
---|---|
Tungsten Carbide | Main component, provides hardness and wear resistance. |
Cobalt | Acts as a binder, providing toughness and impact resistance. |
Titanium Carbide | Enhances hardness and thermal resistance, especially in high-speed cutting applications. |
Tantalum Carbide | Increases resistance to wear and deformation, especially at high temperatures. |
Niobium Carbide | Improves the grain structure, enhancing toughness and resistance to thermal shock. |
Hardness, Strength, and Wear Resistance
These three properties are crucial in determining the suitability of a cemented carbide insert for a specific application.
Property | Description |
---|---|
Hardness | Measured using the Rockwell or Vickers scales, indicating the material’s resistance to deformation. |
Strength | Indicates the material’s ability to withstand mechanical stress without breaking or deforming. |
Wear Resistance | Refers to the material’s ability to resist wear and abrasion during cutting operations. |
Specifications, Sizes, Shapes, and Standards
Cemented carbide inserts come in various sizes, shapes, and standards to meet different machining needs.
Specification | Details |
---|---|
ISO Standards | ISO 1832: Specifies dimensions and tolerances for carbide inserts. |
Shapes | Triangle, square, diamond, round, rectangular, trigon, etc. |
Sizes | Available in various sizes to fit different tool holders and applications. |
Grades | Different grades offer varying levels of hardness, toughness, and wear resistance. |
Suppliers and Pricing Details
Finding reliable suppliers and understanding pricing is crucial for making an informed purchase.
Supplier | Region | Product Range | Pricing (Approx.) |
---|---|---|---|
Kennametal | Global | Wide range of carbide inserts | $5 – $50 per insert |
Sandvik Coromant | Global | High-performance inserts | $10 – $60 per insert |
Mitsubishi Materials | Global | Various types and grades | $7 – $45 per insert |
Sumitomo Electric | Global | Advanced cutting tools | $8 – $55 per insert |
ISCAR | Global | Innovative carbide inserts | $9 – $65 per insert |
Walter Tools | Global | Comprehensive range | $6 – $40 per insert |
Seco Tools | Global | High-precision inserts | $7 – $50 per insert |
YG-1 | Global | Affordable, quality inserts | $5 – $35 per insert |
Tungaloy | Global | Advanced material inserts | $10 – $55 per insert |
Kyocera | Global | High-durability inserts | $8 – $50 per insert |
Selecting the Right Cemented Carbide Inserts
Choosing the right cemented carbide insert involves considering several factors.
Consideration | Details |
---|---|
Material to be Machined | Different materials require different insert properties. |
Type of Machining | The type of operation (turning, milling, drilling) dictates the insert shape and properties needed. |
Cutting Conditions | Speed, feed rate, and depth of cut are crucial factors. |
Tool Holder Compatibility | Ensure the insert fits the tool holder being used. |
Cost | Balance between cost and performance to meet budgetary constraints. |
Advantages and Limitations
Comparing the advantages and limitations of cemented carbide inserts helps in making an informed decision.
Aspect | Advantages | Limitations |
---|---|---|
Hardness | Extremely hard, maintaining sharpness over long periods. | Can be brittle and prone to chipping under improper use. |
Wear Resistance | High wear resistance, reducing the need for frequent replacements. | May be more expensive compared to other materials. |
Heat Resistance | Retains properties at high temperatures, suitable for high-speed operations. | Requires precise cooling and lubrication to avoid thermal damage. |
Versatility | Suitable for a wide range of materials and applications. | Specific inserts needed for different applications, adding to inventory complexity. |
Durability | Long lifespan, reducing downtime and increasing productivity. | High initial cost may be a consideration for some users. |
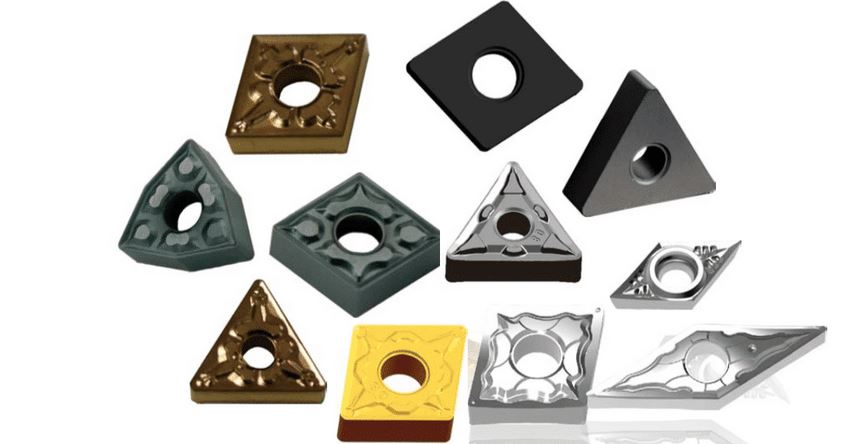
FAQs
What are cemented carbide inserts used for?
Cemented carbide inserts are used in various machining operations such as turning, milling, drilling, and boring. They are preferred for their hardness, wear resistance, and ability to maintain performance at high temperatures.
How do I choose the right carbide insert for my application?
Selecting the right carbide insert involves considering the material to be machined, the type of machining operation, cutting conditions, tool holder compatibility, and cost.
What are the benefits of using cemented carbide inserts?
The main benefits include high hardness, excellent wear resistance, heat resistance, versatility, and durability. These properties result in increased productivity and longer tool life.
Can carbide inserts be reused?
Yes, carbide inserts can often be reused after re-sharpening. However, the extent of reuse depends on the insert’s condition and the specific machining requirements.
What are the common grades of cemented carbide inserts?
Common grades include C2, C3, C5, and C7, each offering different levels of hardness, toughness, and wear resistance suitable for specific applications.
How should I store cemented carbide inserts?
Store them in a cool, dry place away from direct sunlight and moisture. Using appropriate storage containers can help prevent damage and maintain their quality.
Are there any environmental considerations with carbide inserts?
Cemented carbide inserts are made from materials that can be recycled. It’s important to follow proper recycling practices to minimize environmental impact.
What are some common brands of cemented carbide inserts?
Some popular brands include Kennametal, Sandvik Coromant, Mitsubishi Materials, Sumitomo Electric, ISCAR, Walter Tools, Seco Tools, YG-1, Tungaloy, and Kyocera.
How do carbide inserts compare to other cutting tools?
Compared to other cutting tools, carbide inserts offer superior hardness, wear resistance, and heat resistance. They are more durable and efficient but may come at a higher initial cost.
What is the average lifespan of a carbide insert?
The lifespan varies depending on the application, material being machined, and cutting conditions. However, carbide inserts generally last longer than other cutting tools due to their durable properties.
Conclusion
Cemented carbide inserts are a cornerstone of modern machining, offering unmatched durability, efficiency, and versatility. Whether you’re a seasoned professional or just starting in the world of machining, understanding the types, applications, material properties, and selection criteria for carbide inserts can significantly impact your productivity and machining success.
By choosing the right carbide insert, you can enhance your machining operations, reduce downtime, and achieve superior results. Explore the various options, understand your specific needs, and make informed decisions to leverage the full potential of cemented carbide inserts in your projects.