Imagine a world where your equipment constantly battled wear and tear, succumbing to scratches, gouges, and relentless erosion. This harsh reality is the daily grind for countless industries, from mining and construction to manufacturing and waste management. Thankfully, there’s a hero in this fight: the carbide wear plate.
What is a Carbide Wear Plate?
A carbide wear plate is a metal plate clad with a thin layer of tungsten carbide, one of the hardest materials on Earth, second only to diamond. This potent combination creates a virtually impervious shield, safeguarding underlying components from the harshest abrasive environments.
Why Use Carbide Wear Plates?
The benefits of incorporating carbide wear plates are undeniable:
- Unmatched Abrasion Resistance: Carbide boasts exceptional resistance to wear and tear, significantly outperforming mild steel and even its tougher cousin, stainless steel. This translates to extended equipment lifespan, reduced maintenance costs, and minimized downtime.
- Impact Resilience: While not indestructible, carbide offers commendable impact resistance, making it suitable for applications involving moderate impact alongside abrasion.
- Versatility: Carbide wear plates come in various shapes, sizes, and thicknesses, allowing for customization to fit diverse applications. Additionally, they can be welded, drilled, and machined to integrate seamlessly into existing equipment.
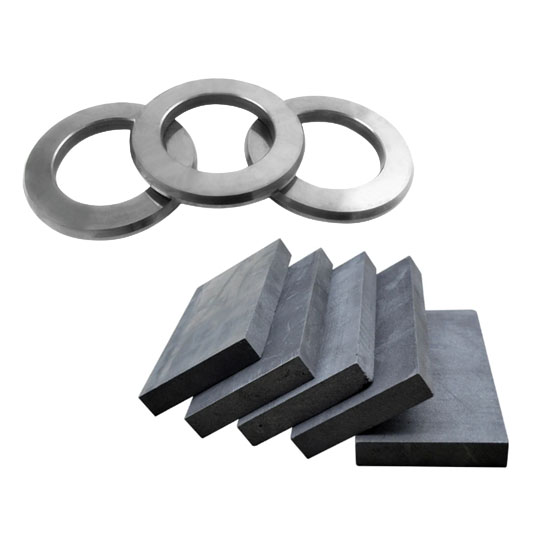
Applications of Carbide Wear Plates
Carbide wear plates are the workhorses of numerous industries, including:
- Mining and Construction: Protecting chutes, hoppers, conveyor systems, and dump truck beds from the relentless onslaught of rocks, gravel, and debris.
- Manufacturing: Shielding equipment like shredders, crushers, and pulverizers from the wear and tear of processing operations.
- Power Generation: Safeguarding coal chutes, ash handling systems, and boiler components from abrasive materials.
- Waste Management: Prolonging the life of landfill equipment like conveyors, trommel screens, and waste processing machinery.
Types of Carbide Wear Plates
Not all carbide wear plates are created equal. Here’s a breakdown of the two most common types:
- Chromium Carbide Overlay Plates: These plates feature a mild steel base clad with a layer of chromium carbide. They offer a cost-effective solution for moderate to high abrasion environments with moderate impact.
- Tungsten Carbide Overlay Plates: As the name suggests, these plates boast a higher tungsten carbide content, making them ideal for extreme abrasion and moderate impact applications. They are the toughest option but come at a premium price.
Factors to Consider When Choosing a Carbide Wear Plate
Selecting the right carbide wear plate requires careful consideration of several factors:
- Severity of Wear: Evaluate the level of abrasion and impact your equipment will encounter. Opt for tungsten carbide for extreme conditions and chromium carbide for moderate scenarios.
- Budget: Chromium carbide plates offer a more budget-friendly option, while tungsten carbide provides superior protection at a higher cost.
- Application: Consider the specific function of the plate. Some applications, like chutes, might require weldability for seamless integration.
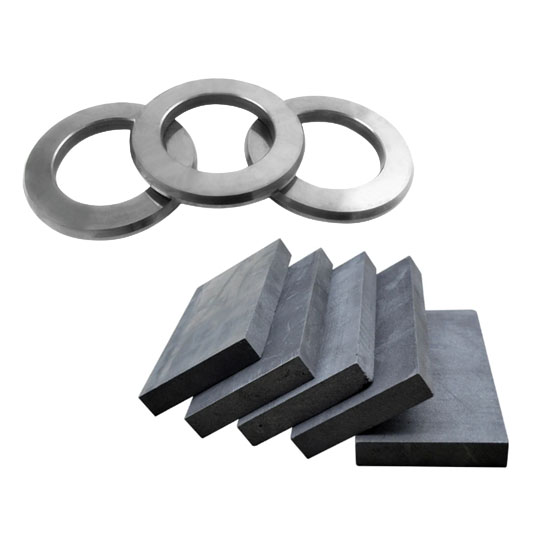
Advanced Considerations for Carbide Wear Plate Selection
While the core selection factors are crucial, there are additional considerations for seasoned users:
- Substrate Material: The base material beneath the carbide layer can influence the plate’s overall properties. AR500 steel is a popular choice for its durability and weldability.
- Carbide Overlay Thickness: The thickness of the carbide layer directly impacts its wear lifespan. Opt for thicker layers for areas experiencing extreme abrasion.
- Attachment Method: Depending on the application, welding, bolting, or mechanical fastening might be the preferred method for attaching the plate.
The Nuances of Carbide Wear Plate Performance
While carbide’s exceptional hardness translates to superior wear resistance, it’s crucial to understand that performance can vary depending on several factors:
Carbide Grade: Different carbide grades boast varying hardness, toughness, and fracture resistance. Selecting the optimal grade for your application is essential. For instance, applications prioritizing maximum wear resistance might benefit from a higher carbide content, even if it sacrifices some toughness. Conversely, situations with moderate abrasion and potential impact might favor a carbide grade that balances hardness with toughness.
Matrix Material: The material binding the carbide particles significantly influences the plate’s overall performance. Chromium is a common matrix material, offering a cost-effective option with good wear resistance. However, nickel-based matrices provide superior toughness and impact resistance, making them suitable for demanding applications.
Overlay Thickness: As mentioned earlier, the thickness of the carbide layer directly impacts its wear lifespan. A thicker layer offers extended protection but comes at the cost of increased weight and cost. Finding the optimal balance between wear protection and practical considerations is crucial.
Installation and Maintenance for Optimal Performance
While carbide wear plates themselves are exceptionally durable, their effectiveness hinges on proper installation and maintenance:
- Installation:
- Surface preparation: Ensure the installation surface is clean, dry, and free of contaminants for optimal adhesion.
- Welding: If welding is the chosen attachment method, employ qualified welders who understand the specific requirements of carbide wear plates. Using proper welding techniques and filler materials is crucial to preserve the plate’s integrity and performance.
- Bolting or mechanical fastening: When bolting or using mechanical fasteners, ensure proper torque specifications are followed to prevent the plate from becoming loose or detaching under stress.
- Maintenance:
- Regular inspections: Conduct routine inspections to identify any signs of wear, such as chipping, cracking, or excessive material loss.
- Preventative maintenance: Address minor wear and tear promptly to prevent further damage and extend the plate’s lifespan. In some cases, welding repairs might be possible to restore functionality.
- Replacement: When wear surpasses a certain point, or the plate sustains significant damage, replacement becomes necessary to maintain optimal protection.
The Future of Carbide Wear Plates
The realm of carbide wear plates is constantly evolving, with ongoing research and development efforts exploring ways to enhance performance and functionality:
- Alternative Carbide Materials: Researchers are exploring alternative carbide materials, like tantalum carbide and boron carbide, which offer unique properties that might prove advantageous in specific applications.
- Composite Wear Plates: Combining carbide with other wear-resistant materials, like ceramics or polymers, is another area of exploration. Such composite plates might offer tailored properties for specific wear mechanisms.
- Advanced Manufacturing Techniques: Utilizing techniques like additive manufacturing (3D printing) to create complex shapes and customized wear plates holds immense potential for the future.
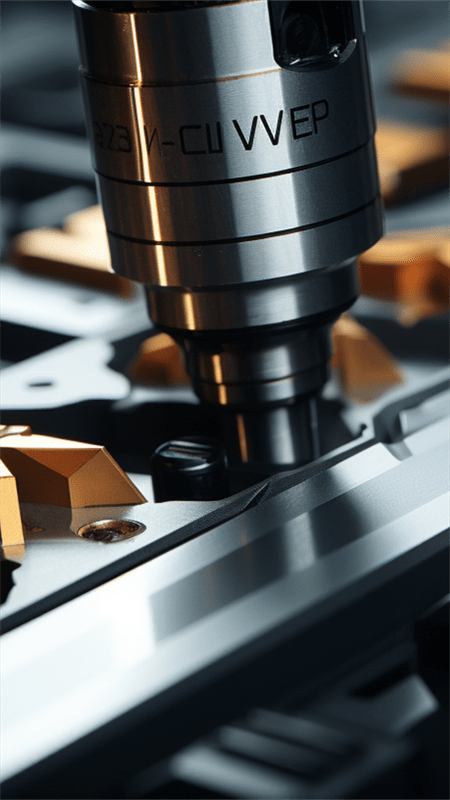
FAQs
Question | Answer |
---|---|
How long do carbide wear plates last? | The lifespan of a carbide wear plate depends on various factors, including the severity of wear, application, and thickness. In moderate environments, they can last for years, while extreme conditions might necessitate replacement sooner. |
Can carbide wear plates be repaired? | Yes, depending on the extent of the damage. Minor chipping or gouging might be repairable through welding or filling with a carbide compound. However, extensive wear often necessitates replacement. |
Are carbide wear plates safe to use? | Carbide itself is considered safe. However, the installation process, particularly welding, might pose safety hazards. Always follow proper safety protocols when handling and installing carbide wear plates. |
Conclusion
Carbide wear plates are undoubtedly the go-to solution for various wear-intensive applications. By understanding their properties, selection factors, and proper installation and maintenance practices, you can leverage their exceptional durability and cost-effectiveness to safeguard your equipment and ensure smooth operation across numerous industries. As the technology continues to evolve, the future of carbide wear plates promises even greater performance and versatility, catering to the ever-growing demands of diverse industrial applications.