Carbide turning inserts are the unsung heroes of machining. They help us shape, carve, and perfect metal into the precise forms we need for countless applications. If you’re involved in machining or manufacturing, understanding carbide turning inserts is crucial. This guide will dive deep into the world of carbide turning inserts, covering everything from types and applications to selecting the right one for your needs.
Overview of Carbide Turning Inserts
Carbide turning inserts are cutting tools used in lathes for turning operations. They are made from carbide, a compound of carbon and tungsten, known for its hardness and resistance to wear. These inserts are designed to handle the high-speed cutting of tough materials like steel, stainless steel, cast iron, and non-ferrous metals. They come in various shapes, sizes, and grades, each tailored to specific cutting conditions and materials.
Types of Carbide Turning Inserts
There are numerous types of carbide turning inserts, each suited for different machining tasks. Here’s a detailed table summarizing the main types of carbide turning inserts:
Insert Type | Shape | Typical Use | Advantages | Disadvantages |
---|---|---|---|---|
C-Type (CNMG, CNMM) | Rhombic | General turning | Versatile, strong edges | Limited chip control |
D-Type (DNMG, DNMM) | 55° Rhombic | Finishing operations | Good for light cuts | Fragile edges |
S-Type (SNMG, SNMM) | Square | Heavy-duty turning | Strong cutting edges | Less flexible in shapes |
T-Type (TNMG, TNMM) | Triangle | Roughing and finishing | Multi-corner usability | Lower strength edges |
V-Type (VNMG, VNMM) | 35° Rhombic | Fine finishing | Excellent for precise cuts | Fragile, less durable |
W-Type (WNMG, WNMM) | Trigon | Heavy-duty roughing | High strength, versatile | Complex chip formation |
R-Type (RNMG, RNMM) | Round | Profiling, grooving | Strongest insert | Limited corner usability |
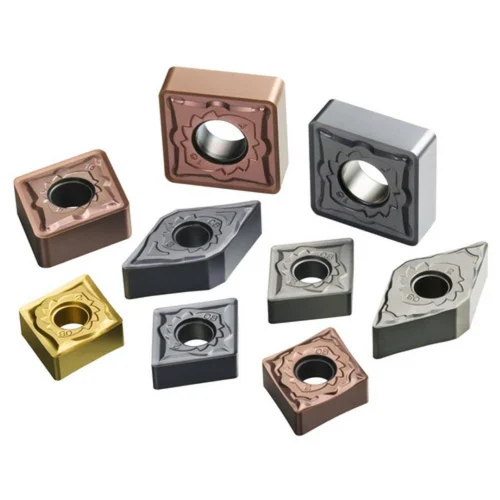
Applications of Carbide Turning Inserts
Carbide turning inserts are used across various industries due to their versatility and durability. Here’s a table detailing their applications:
Industry | Application | Insert Type Recommended |
---|---|---|
Automotive | Engine components, shafts | C-Type, S-Type |
Aerospace | Structural parts, turbine blades | V-Type, W-Type |
Medical Devices | Surgical instruments, implants | D-Type, V-Type |
Oil and Gas | Pipe fittings, valves | T-Type, S-Type |
General Engineering | Machinery parts, tools | C-Type, T-Type |
Electronics | Enclosures, connectors | D-Type, R-Type |
Construction Equipment | Hydraulic components, frames | S-Type, W-Type |
Material Properties of Carbide Turning Inserts
Understanding the material properties of carbide turning inserts is crucial for selecting the right one for your specific needs. Here’s a detailed table of these properties:
Property | Description |
---|---|
Hardness | High hardness, typically 80-90 HRA |
Toughness | Resistance to breaking and chipping |
Wear Resistance | Ability to withstand wear from abrasive materials |
Thermal Conductivity | High, dissipates heat effectively |
Chemical Stability | Resistant to oxidation and chemical reactions |
Composition and Characteristics of Carbide Turning Inserts
Carbide turning inserts are composed of several elements, each contributing to their unique characteristics:
Element | Percentage (%) | Characteristic |
---|---|---|
Tungsten (W) | 70-80 | Provides hardness and strength |
Carbon (C) | 6-10 | Forms the carbide compound, enhancing hardness |
Cobalt (Co) | 5-10 | Binds the tungsten carbide particles together |
Titanium (Ti) | 1-5 | Increases toughness and wear resistance |
Tantalum (Ta) | 1-3 | Enhances high-temperature strength |
Niobium (Nb) | 0.5-2 | Improves resistance to thermal shock |
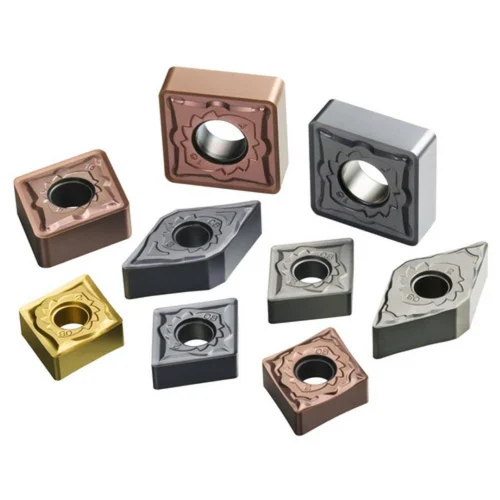
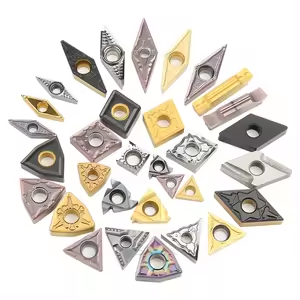
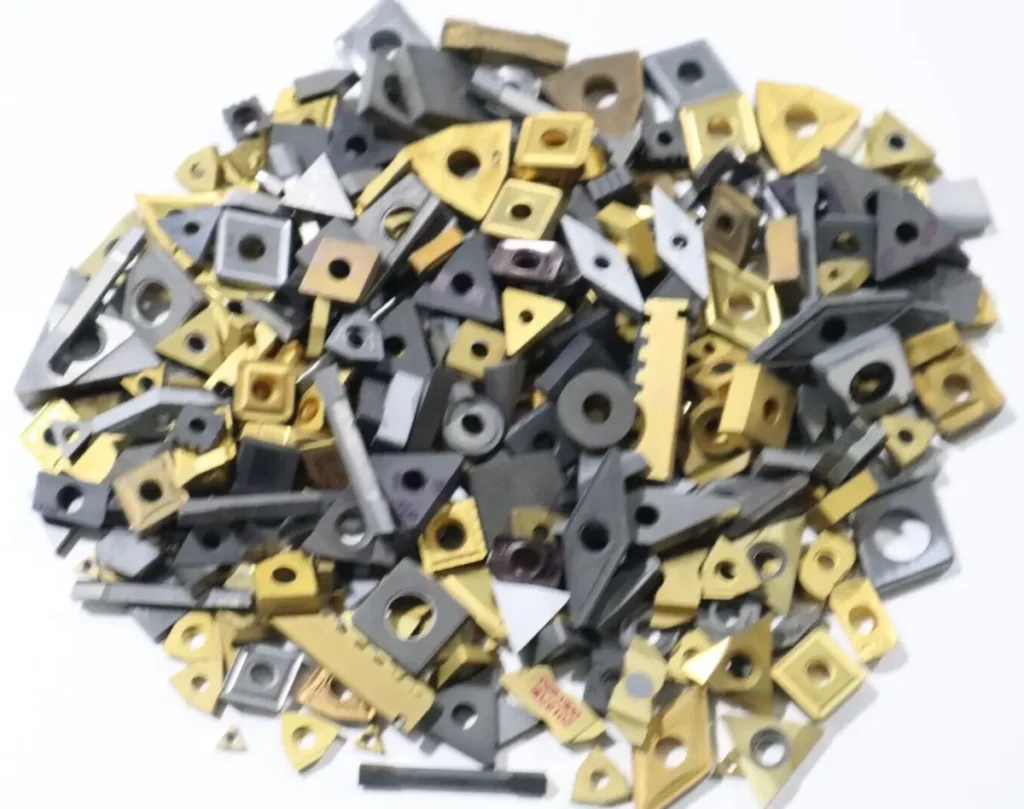
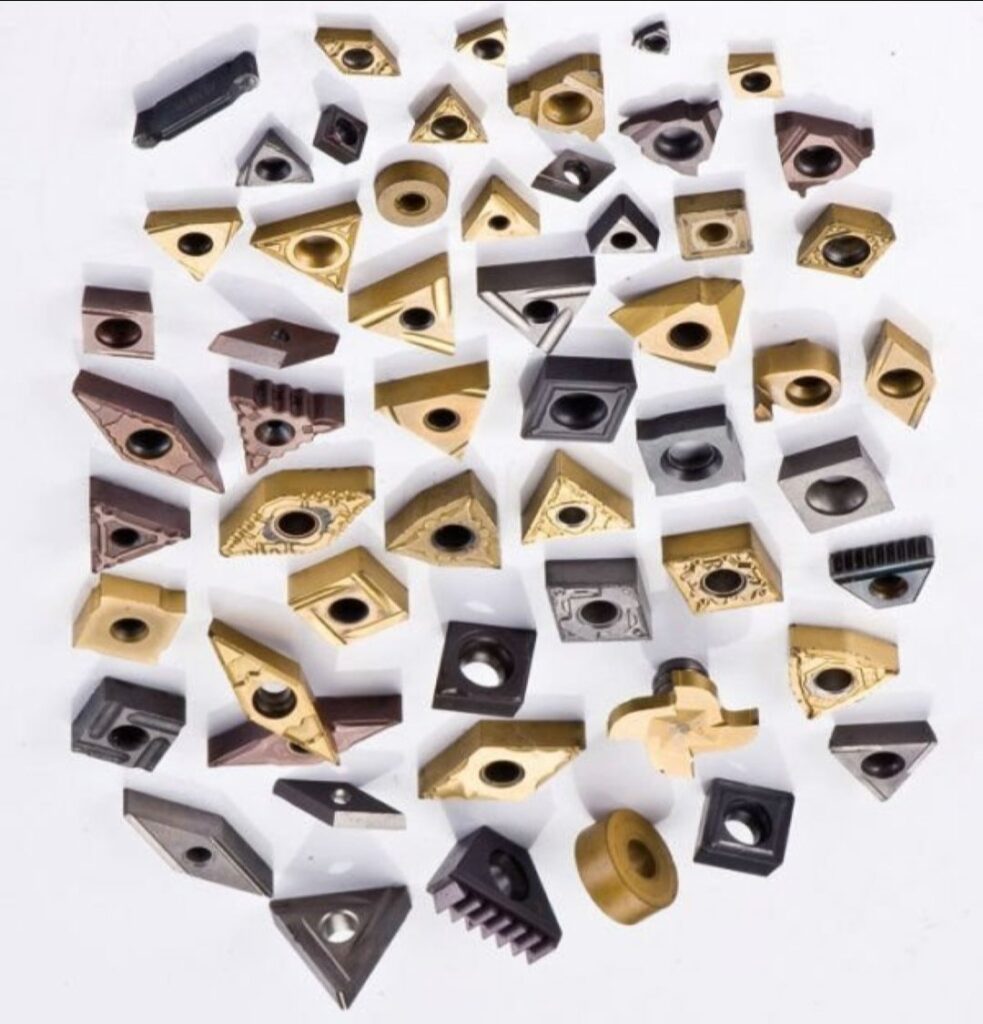
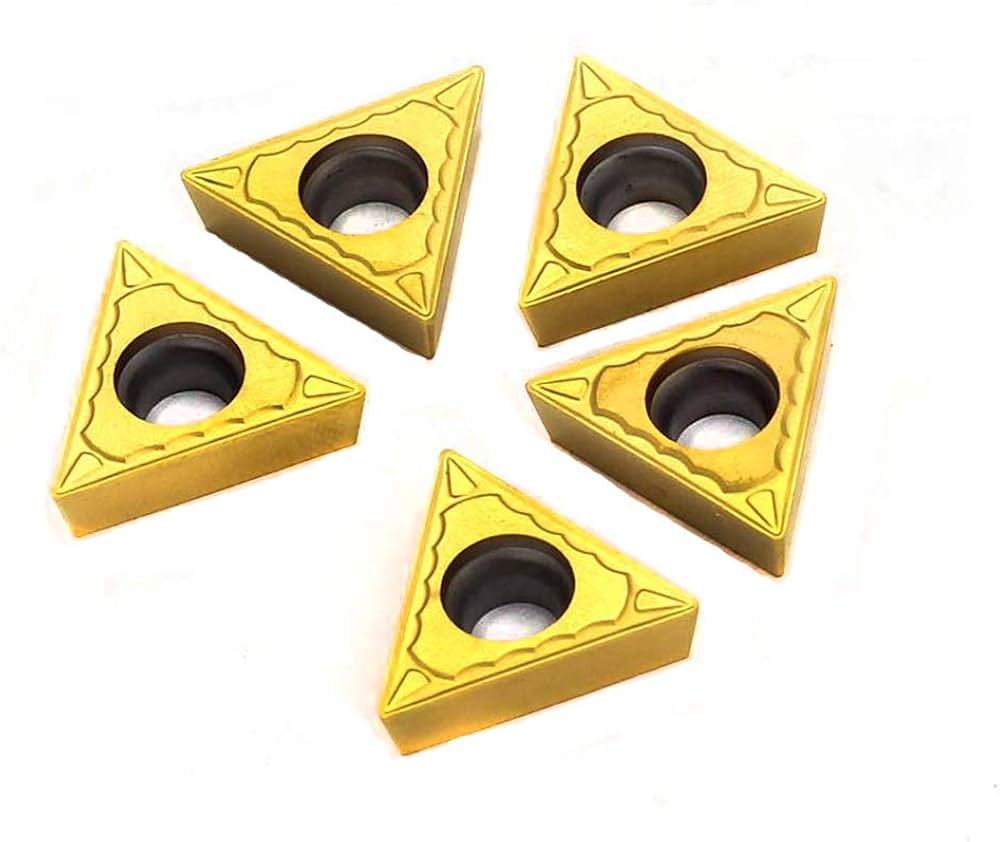
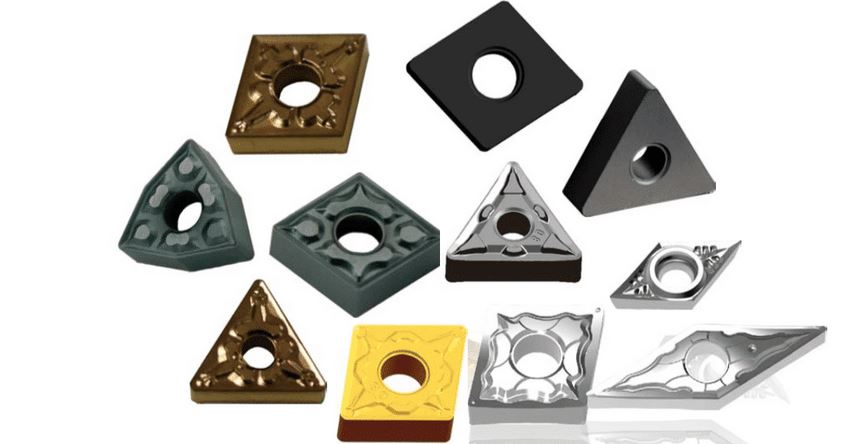
Hardness, Strength, and Wear Resistance
Carbide turning inserts must balance hardness, strength, and wear resistance to perform effectively. Here’s a comparative table:
Property | Description |
---|---|
Hardness | Ensures the insert can cut through tough materials. |
Strength | Prevents the insert from breaking under high pressure. |
Wear Resistance | Extends the insert’s life by resisting wear and tear. |
Specifications, Sizes, Shapes, and Standards
Carbide turning inserts come in various specifications to suit different machining tasks. Here’s a table detailing these specifications:
Specification | Details |
---|---|
Size | Ranges from 1/8″ to 1″ in cutting edge size |
Shape | Rhombic, square, triangle, round, trigon |
Standards | ISO, ANSI, DIN, JIS |
Suppliers and Pricing Details
Here’s a list of notable suppliers and their pricing details for carbide turning inserts:
Supplier | Country | Price Range (per insert) |
---|---|---|
Kennametal | USA | $5 – $30 |
Sandvik Coromant | Sweden | $8 – $40 |
Mitsubishi Materials | Japan | $7 – $35 |
Seco Tools | Sweden | $6 – $33 |
Walter Tools | Germany | $9 – $37 |
Iscar | Israel | $10 – $45 |
Sumitomo Electric | Japan | $8 – $38 |
Tungaloy | Japan | $7 – $34 |
Kyocera | Japan | $6 – $32 |
Taegutec | South Korea | $5 – $30 |
How to Select the Right Carbide Turning Inserts
Choosing the right carbide turning insert can significantly impact your machining efficiency and product quality. Here’s a table to guide you through the selection process:
Criteria | Considerations |
---|---|
Material Type | Choose inserts suited for the material you are machining. |
Cutting Speed | Higher speeds require tougher, more wear-resistant inserts. |
Feed Rate | Match the insert to your feed rate for optimal performance. |
Depth of Cut | Ensure the insert can handle your required depth of cut. |
Machine Power | Select inserts compatible with your machine’s power capacity. |
Finish Requirements | Choose inserts that can achieve your desired surface finish. |
Comparing Advantages and Limitations
Every type of carbide turning insert has its own set of advantages and limitations. Here’s a comparative table to help you understand them better:
Insert Type | Advantages | Limitations |
---|---|---|
C-Type | Versatile, strong edges | Limited chip control |
D-Type | Good for light cuts | Fragile edges |
S-Type | Strong cutting edges | Less flexible in shapes |
T-Type | Multi-corner usability | Lower strength edges |
V-Type | Excellent for precise cuts | Fragile, less durable |
W-Type | High strength, versatile | Complex chip formation |
R-Type | Strongest insert | Limited corner usability |
Metal Powder Models for Carbide Turning Inserts
Here are some specific metal powder models used in the production of carbide turning inserts, along with their descriptions:
- WC-Co (Tungsten Carbide-Cobalt):
- Description: A composite material made of tungsten carbide particles bonded with cobalt.
- Characteristics: High hardness, toughness, and wear resistance.
- TiC (Titanium Carbide):
- Description: A carbide compound of titanium and carbon.
- Characteristics: Excellent wear resistance and chemical stability.
- TaC (Tantalum Carbide):
- Description: A refractory carbide of tantalum and carbon.
- Characteristics: High melting point, strength, and hardness.
- NbC (Niobium Carbide):
- Description: A hard refractory metal carbide.
- Characteristics: High hardness, thermal conductivity, and chemical resistance.
- VC (Vanadium Carbide):
- Description: A carbide of vanadium and carbon.
- Characteristics: Enhances toughness and wear resistance.
- CrC (Chromium Carbide):
- Description: A compound of chromium and carbon.
- Characteristics: High hardness and corrosion resistance.
- Mo2C (Molybdenum Carbide):
- Description: A carbide compound of molybdenum.
- Characteristics: Good hardness and thermal stability.
- WC-TiC-TaC (Composite Carbide):
- Description: A combination of tungsten carbide, titanium carbide, and tantalum carbide.
- Characteristics: Superior wear resistance and toughness.
- ZrC (Zirconium Carbide):
- Description: A carbide of zirconium.
- Characteristics: High hardness and thermal conductivity.
- HfC (Hafnium Carbide):
- Description: A refractory carbide of hafnium.
- Characteristics: Exceptional hardness and high melting point.
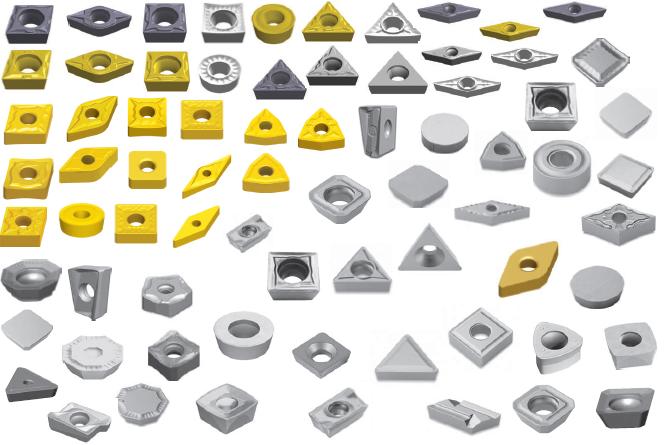
FAQs
What are carbide turning inserts made of?
Carbide turning inserts are primarily made from tungsten carbide, cobalt, and other elements like titanium, tantalum, and niobium.
Why are carbide inserts preferred in machining?
They are preferred for their hardness, wear resistance, and ability to handle high-speed cutting.
How do I choose the right carbide turning insert?
Consider the material type, cutting speed, feed rate, depth of cut, machine power, and finish requirements.
What are the main types of carbide turning inserts?
The main types include C-Type, D-Type, S-Type, T-Type, V-Type, W-Type, and R-Type.
Can carbide turning inserts be reused?
Yes, they can be indexed or rotated to use multiple cutting edges.
What is the lifespan of a carbide turning insert?
It depends on the material being machined and the cutting conditions but typically ranges from several hours to days of continuous use.
Are carbide turning inserts standardized?
Yes, they adhere to international standards such as ISO, ANSI, DIN, and JIS.
What industries use carbide turning inserts?
They are used in automotive, aerospace, medical devices, oil and gas, general engineering, electronics, and construction equipment industries.
How do carbide turning inserts affect machining performance?
They enhance machining performance by providing precise cuts, reducing downtime, and improving surface finishes.
What are some top brands for carbide turning inserts?
Top brands include Kennametal, Sandvik Coromant, Mitsubishi Materials, Seco Tools, Walter Tools, and Iscar.
Conclusion
Carbide turning inserts are indispensable tools in modern machining, offering unparalleled performance in terms of hardness, toughness, and wear resistance. Understanding the various types, applications, and selection criteria can help you choose the right insert for your specific needs, enhancing productivity and ensuring high-quality results in your machining operations.