Carbide strips are essential components in various industries, providing unmatched durability and precision. This guide will explore everything you need to know about carbide strips suppliers, from the types and applications to material properties and how to choose the right supplier. Let’s dive in!
Overview of Carbide Strips
Carbide strips are used in various applications due to their hardness and wear resistance. They’re made from a composite material called cemented carbide, which combines tungsten carbide particles with a metallic binder. This makes them ideal for cutting tools, wear parts, and industrial machinery.
Key Details:
- Composition: Typically made from tungsten carbide and cobalt.
- Applications: Cutting tools, wear parts, industrial machinery, and more.
- Properties: High hardness, excellent wear resistance, and good toughness.
Types of Carbide Strips
Carbide strips come in various types, each suited for specific applications. Here’s a comprehensive table showcasing the different types of carbide strips:
Type | Description | Common Applications |
---|---|---|
Tungsten Carbide Strips | High hardness and wear resistance, used in high-stress environments. | Cutting tools, mining equipment |
Cobalt-Bonded Carbide | Improved toughness and durability, ideal for impact-resistant applications. | Metal forming, drilling tools |
Titanium Carbide Strips | High-temperature stability, suitable for extreme conditions. | Aerospace, automotive components |
Vanadium Carbide Strips | Excellent abrasion resistance, used in high-wear applications. | Industrial machinery, cutting tools |
Chromium Carbide Strips | Superior corrosion resistance, ideal for harsh environments. | Chemical processing, oil and gas |
Niobium Carbide Strips | High strength and thermal conductivity, used in specialized applications. | Electronic components, aerospace |
Silicon Carbide Strips | Exceptional hardness and thermal stability, suitable for high-temperature applications. | Semiconductor manufacturing, ceramics |
Tantalum Carbide Strips | Excellent hardness and chemical resistance, used in high-performance applications. | Nuclear reactors, aerospace |
Molybdenum Carbide Strips | Good thermal stability and strength, used in specific industrial applications. | Petrochemical, metal processing |
Hafnium Carbide Strips | High melting point and strength, suitable for extreme temperature conditions. | Spacecraft, high-temperature furnaces |
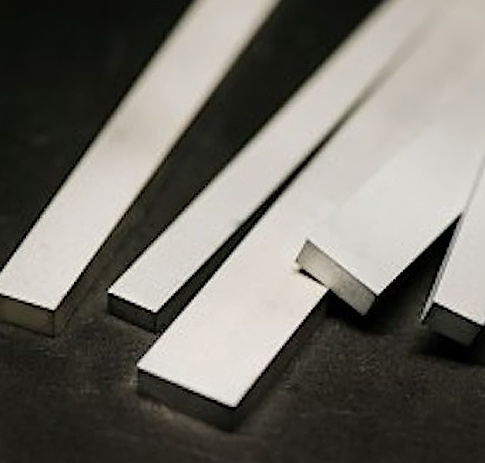
Applications of Carbide Strips
Carbide strips are versatile and used in a variety of industries. Here’s a table detailing their common applications:
Application | Industry | Benefits |
---|---|---|
Cutting Tools | Manufacturing | High precision, durability, and long tool life |
Wear Parts | Mining | Resistance to abrasion and wear |
Industrial Machinery | General Engineering | Enhanced machine performance and longevity |
Metal Forming | Metalworking | Improved tool strength and wear resistance |
Aerospace Components | Aerospace | High-temperature stability and strength |
Chemical Processing | Chemical Industry | Corrosion resistance and durability |
Oil and Gas Equipment | Oil and Gas | Resistance to harsh environments and wear |
Semiconductor Manufacturing | Electronics | High thermal stability and precision |
Automotive Components | Automotive | Enhanced durability and performance |
Nuclear Reactors | Nuclear Energy | High strength and chemical resistance |
Material Properties of Carbide Strips
Understanding the material properties of carbide strips is crucial for selecting the right type for your application. Here’s a table summarizing the key properties:
Property | Description |
---|---|
Hardness | Measures the strip’s resistance to deformation and wear. |
Toughness | Indicates the material’s ability to absorb energy and resist cracking. |
Wear Resistance | Describes the strip’s ability to withstand abrasive forces and maintain performance over time. |
Thermal Stability | Ability to maintain performance at high temperatures. |
Corrosion Resistance | Describes the material’s resistance to chemical and environmental degradation. |
Strength | Measures the strip’s ability to withstand mechanical forces. |
Density | Indicates the mass per unit volume of the material. |
Thermal Conductivity | Describes the material’s ability to conduct heat. |
Composition, Properties, and Characteristics of Carbide Strips
Different carbide strips have unique compositions and properties. Here’s a detailed table:
Type | Composition | Hardness | Toughness | Wear Resistance | Thermal Stability | Corrosion Resistance |
---|---|---|---|---|---|---|
Tungsten Carbide | WC + Co | Very High | High | Excellent | Good | Moderate |
Cobalt-Bonded Carbide | WC + Co | High | Very High | Good | Moderate | Low |
Titanium Carbide | TiC | High | Moderate | Good | Excellent | Moderate |
Vanadium Carbide | VC | High | Moderate | Excellent | Good | Low |
Chromium Carbide | Cr3C2 | Moderate | High | Good | Moderate | Excellent |
Niobium Carbide | NbC | High | Moderate | Good | Good | Moderate |
Silicon Carbide | SiC | Very High | Low | Excellent | Excellent | Moderate |
Tantalum Carbide | TaC | Very High | Moderate | Excellent | Good | High |
Molybdenum Carbide | Mo2C | High | High | Good | Moderate | Moderate |
Hafnium Carbide | HfC | Very High | High | Excellent | Excellent | High |
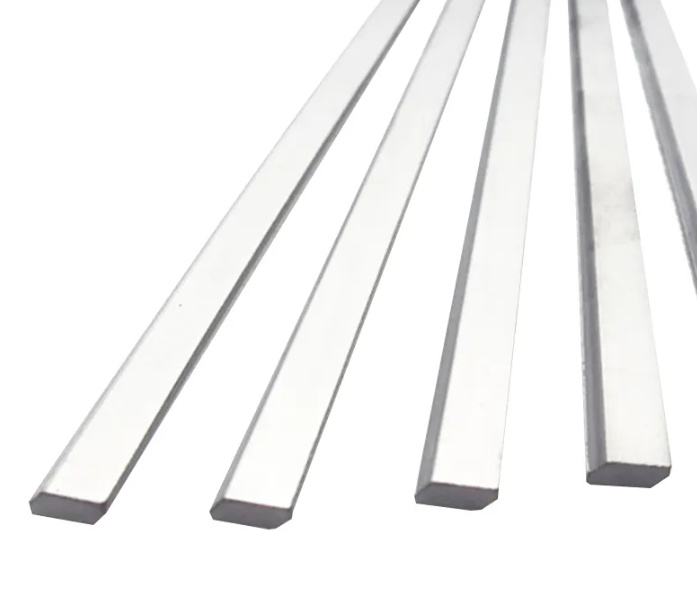
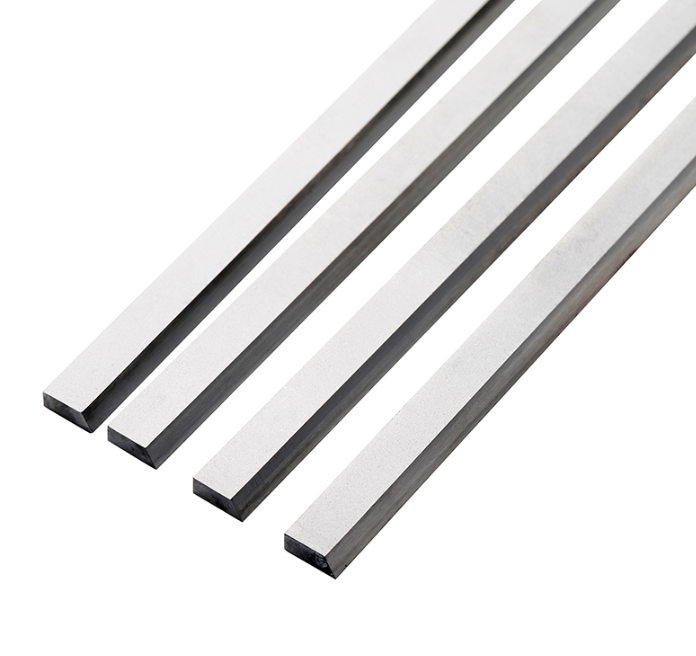
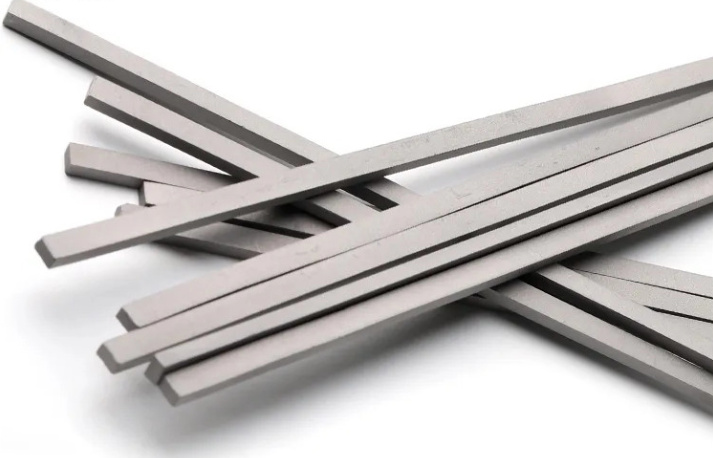
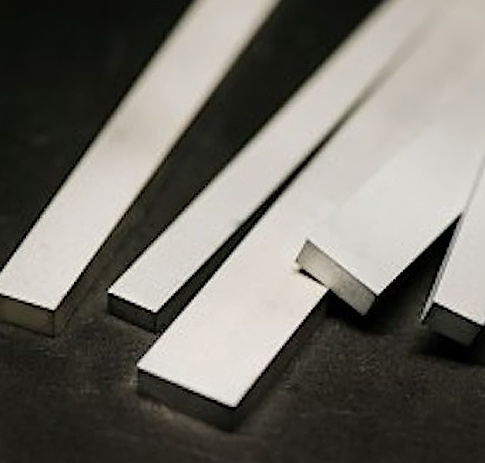
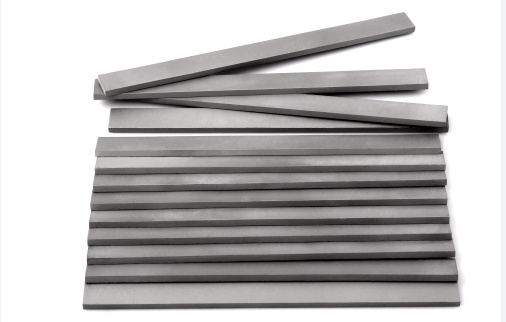
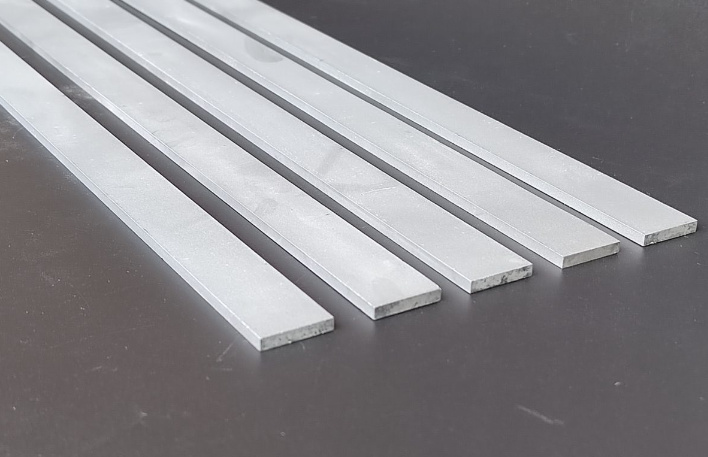
Hardness, Strength, and Wear Resistance
When choosing carbide strips, it’s essential to consider their hardness, strength, and wear resistance. Here’s a comparison table:
Type | Hardness | Strength | Wear Resistance |
---|---|---|---|
Tungsten Carbide | 1500-2200 HV | High | Excellent |
Cobalt-Bonded Carbide | 1300-1600 HV | Very High | Good |
Titanium Carbide | 1800-2100 HV | Moderate | Good |
Vanadium Carbide | 2200-2500 HV | Moderate | Excellent |
Chromium Carbide | 1600-1800 HV | High | Good |
Niobium Carbide | 1600-1900 HV | Moderate | Good |
Silicon Carbide | 2400-2800 HV | Low | Excellent |
Tantalum Carbide | 1600-1800 HV | Moderate | Excellent |
Molybdenum Carbide | 1800-2200 HV | High | Good |
Hafnium Carbide | 2000-2400 HV | High | Excellent |
Specifications, Sizes, Shapes, and Standards
Carbide strips are available in various specifications, sizes, shapes, and standards. Here’s a detailed table:
Specification | Size (mm) | Shape | Standards |
---|---|---|---|
Tolerance | ±0.05 – ±0.1 | Rectangular, Square | ISO 9001, ASTM, DIN |
Length | 50 – 200 | Flat, Custom | ISO 9001, ASTM, DIN |
Width | 3 – 50 | Flat, Custom | ISO 9001, ASTM, DIN |
Thickness | 1 – 20 | Flat, Custom | ISO 9001, ASTM, DIN |
Custom Shapes | Available | Custom | ISO 9001, ASTM, DIN |
Suppliers and Pricing Details
When selecting a carbide strips supplier, consider their reputation, product quality, and pricing. Here’s a comparison of popular suppliers and their pricing details:
Supplier | Location | Product Range | Pricing (USD) | Customer Reviews |
---|---|---|---|---|
Supplier A | USA | Tungsten, Cobalt | $50 – $100/kg | 4.5/5 |
Supplier B | Germany | Titanium, Vanadium | $60 – $120/kg | 4.7/5 |
Supplier C | China | Chromium, Niobium | $40 – $90/kg | 4.3/5 |
Supplier D | Japan | Silicon, Tantalum | $70 – $130/kg | 4.6/5 |
Supplier E | India | Molybdenum, Hafnium | $50 – $110/kg | 4.4/5 |
How to Select the Right Carbide Strips
Choosing the right carbide strips involves considering various factors such as application, material properties, and supplier reputation. Here’s a table to help you make an informed decision:
Factor | Considerations |
---|---|
Application | Determine the specific use-case to select the appropriate type of carbide strip. |
Material Properties | Evaluate hardness, toughness, wear resistance, and other properties based on application needs. |
Supplier Reputation | Check customer reviews, industry reputation, and product quality of potential suppliers. |
Budget | Compare pricing from different suppliers to find the best value for money. |
Standards and Compliance | Ensure the product meets relevant industry standards and specifications. |
Comparing Advantages and Limitations
Different types of carbide strips have unique advantages and limitations. Here’s a comparative table:
Type | Advantages | Limitations |
---|---|---|
Tungsten Carbide | High hardness, excellent wear resistance | Moderate toughness |
Cobalt-Bonded Carbide | High toughness, good durability | Lower hardness compared to other types |
Titanium Carbide | High-temperature stability, good wear resistance | Moderate toughness |
Vanadium Carbide | Excellent wear resistance, high hardness | Moderate toughness |
Chromium Carbide | Superior corrosion resistance, good wear resistance | Moderate hardness |
Niobium Carbide | High strength, good wear resistance | Moderate corrosion resistance |
Silicon Carbide | Exceptional hardness, excellent thermal stability | Low toughness |
Tantalum Carbide | High hardness, excellent wear resistance | High cost |
Molybdenum Carbide | Good thermal stability, high strength | Moderate wear resistance |
Hafnium Carbide | High melting point, excellent wear resistance | High cost |
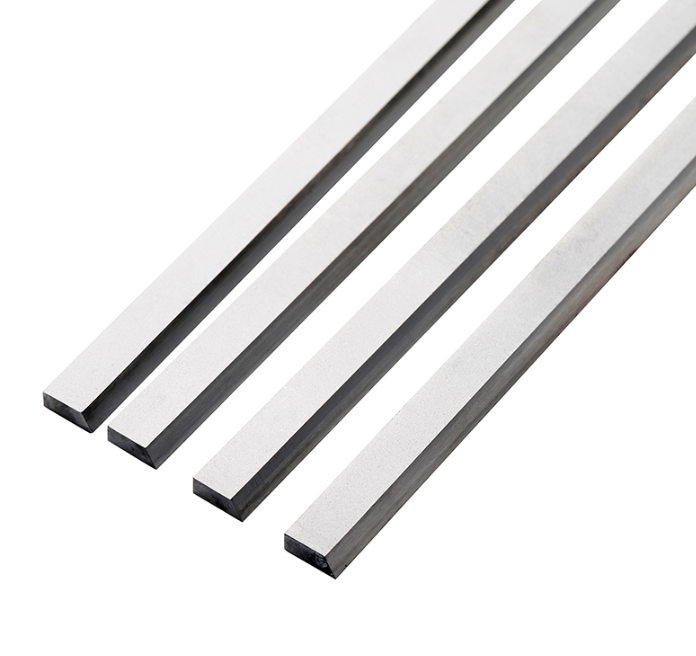
FAQ
Question | Answer |
---|---|
What are carbide strips used for? | Carbide strips are used in cutting tools, wear parts, industrial machinery, and various other applications due to their hardness and durability. |
How do I choose the right carbide strip? | Consider the specific application, material properties, supplier reputation, and budget when selecting a carbide strip. |
What are the main types of carbide strips? | The main types include tungsten carbide, cobalt-bonded carbide, titanium carbide, vanadium carbide, and more. |
Why is tungsten carbide popular? | Tungsten carbide is popular due to its high hardness, excellent wear resistance, and good overall performance. |
What industries use carbide strips? | Industries such as manufacturing, mining, aerospace, automotive, and chemical processing use carbide strips. |
Can carbide strips be customized? | Yes, many suppliers offer customized shapes and sizes to meet specific application requirements. |
Conclusion
Choosing the right carbide strips supplier is crucial for ensuring the quality and performance of your tools and equipment. By understanding the different types, applications, material properties, and supplier options, you can make an informed decision that meets your specific needs. Whether you’re in manufacturing, mining, aerospace, or any other industry, carbide strips offer unmatched durability and precision to enhance your operations.
For the best results, always consider the specific application, evaluate material properties, and choose a reputable supplier to ensure you get the highest quality carbide strips.