Carbide strips are integral to modern manufacturing and engineering, thanks to their exceptional hardness, durability, and resistance to wear. Whether you’re an engineer, a machinist, or simply someone curious about advanced materials, this comprehensive guide will help you understand everything you need to know about carbide strips.
We’ll explore what carbide strips are, how they’re made, their applications, and the different types available. By the end of this article, you’ll have a thorough understanding of carbide strips, along with detailed insights into how to choose the right one for your needs. So, let’s dive in!
Overview of Carbide Strips
Carbide strips, also known as tungsten carbide strips, are hard, wear-resistant materials made by combining tungsten carbide powder with a binder metal, usually cobalt. These strips are widely used in various industries, including manufacturing, mining, and woodworking, due to their incredible strength, toughness, and resistance to wear and tear.
Why Carbide Strips?
Carbide strips stand out in industrial applications because of their unique combination of hardness and toughness. Unlike traditional steel, which may wear down or break under extreme conditions, carbide strips offer superior performance, even in the most challenging environments. This makes them ideal for cutting tools, wear parts, and various precision components.
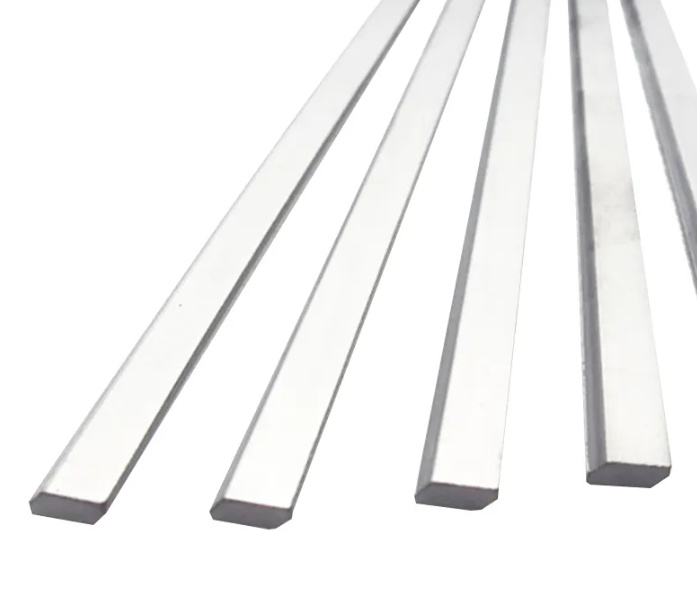
Types of Carbide Strips
Carbide strips come in various grades and sizes, each tailored for specific applications. The composition of tungsten carbide and the binder percentage define the properties of these strips.
Type of Carbide Strip | Tungsten Carbide Grade | Cobalt Binder Content (%) | Grain Size (µm) | Application |
---|---|---|---|---|
YG6 | 94% WC | 6% | 1.6 – 2.2 | Mining Tools |
YG8 | 92% WC | 8% | 1.6 – 2.2 | General Purpose |
YG10 | 90% WC | 10% | 1.6 – 2.2 | Cutting Tools |
YG15 | 85% WC | 15% | 1.6 – 2.2 | Heavy-duty Tools |
YG20 | 80% WC | 20% | 1.6 – 2.2 | Impact Tools |
YT5 | 92% WC, 8% TiC | 8% | 1.6 – 2.2 | Heat-resistant Tools |
YT15 | 85% WC, 15% TiC | 8% | 1.6 – 2.2 | Precision Cutting |
K10 | 94% WC | 6% | 1.2 – 1.8 | Finishing Cuts |
K20 | 90% WC | 10% | 1.2 – 1.8 | General Machining |
P20 | 85% WC, 15% Co | 8% | 1.2 – 1.8 | Steel Cutting |
Applications of Carbide Strips
Carbide strips are used in various industries for their hardness and resistance to abrasion. Let’s take a closer look at some of the most common applications:
Application | Industry | Description |
---|---|---|
Cutting Tools | Metalworking | Carbide strips are used in lathe tools, milling cutters, and drill bits due to their hardness. |
Woodworking Tools | Woodworking | Ideal for saw blades and routers, providing long-lasting sharpness and precision. |
Wear Parts | Mining | Used in crusher machines, conveyor belt systems, and mining tools to withstand harsh conditions. |
Precision Components | Aerospace | Used in high-stress, high-temperature environments, such as turbine blades and rocket nozzles. |
Moulds and Dies | Manufacturing | Carbide strips are essential for producing molds and dies that require exceptional durability. |
Heat-resistant Tools | Foundries | Excellent for tools exposed to extreme heat, such as those used in foundries and forging. |
Surgical Instruments | Medical | High wear resistance makes carbide strips perfect for precise, durable surgical tools. |
Impact Tools | Construction | Carbide strips are used in jackhammer bits and drilling tools due to their impact resistance. |
Material Properties of Carbide Strips
Carbide strips are renowned for their outstanding material properties, which include extreme hardness, high compressive strength, and excellent wear resistance. These properties make them suitable for demanding applications where traditional materials would fail.
Material Property | Description |
---|---|
Hardness | Tungsten carbide is incredibly hard, typically between 8.5 and 9 on the Mohs scale. |
Compressive Strength | Carbide strips have a compressive strength of up to 4000 MPa, making them resistant to deformation. |
Wear Resistance | The combination of hardness and toughness results in excellent wear resistance, even in abrasive conditions. |
Thermal Stability | Tungsten carbide retains its properties at high temperatures, making it ideal for cutting and wear applications. |
Toughness | Despite their hardness, carbide strips offer good toughness, resisting chipping and breaking. |
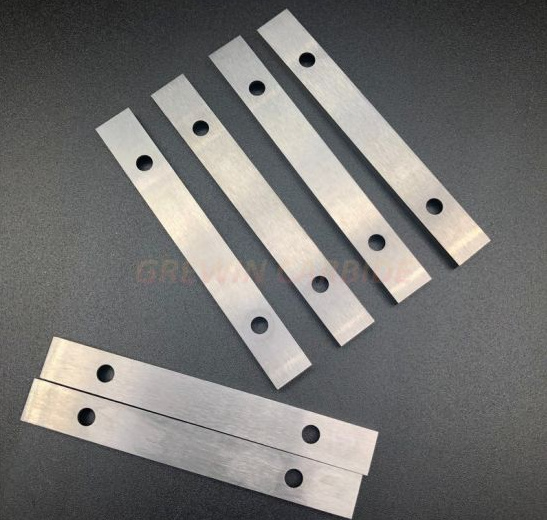
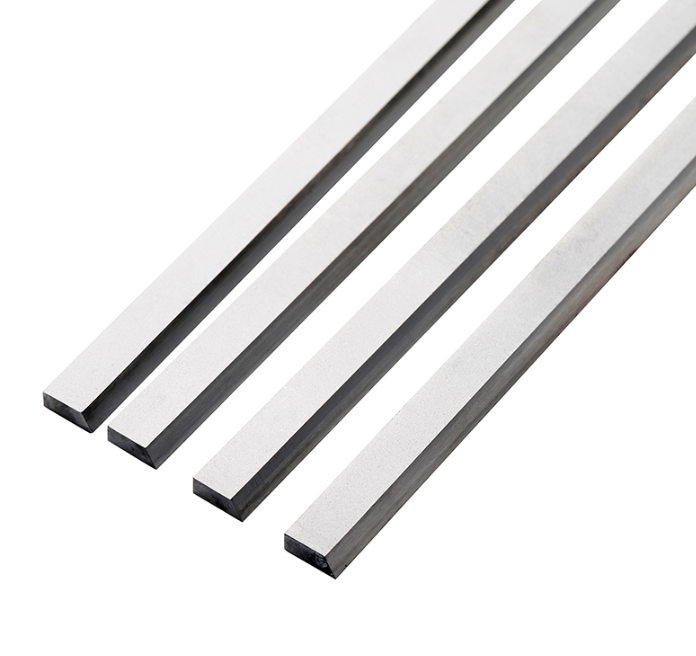
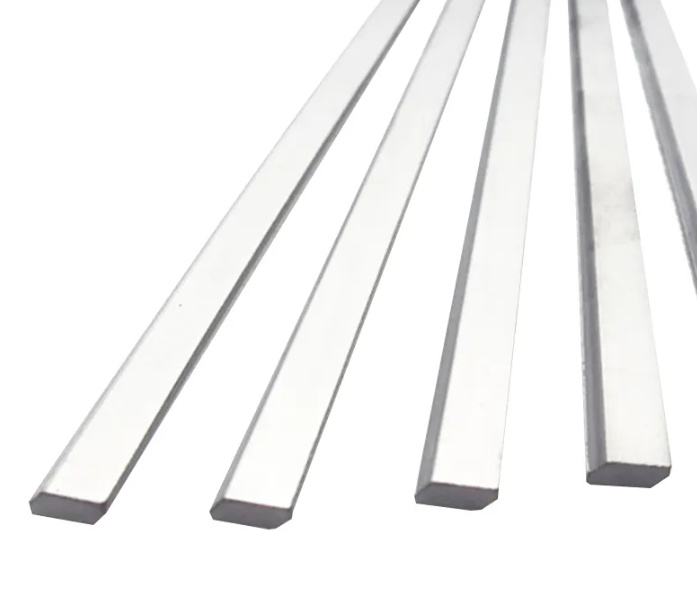
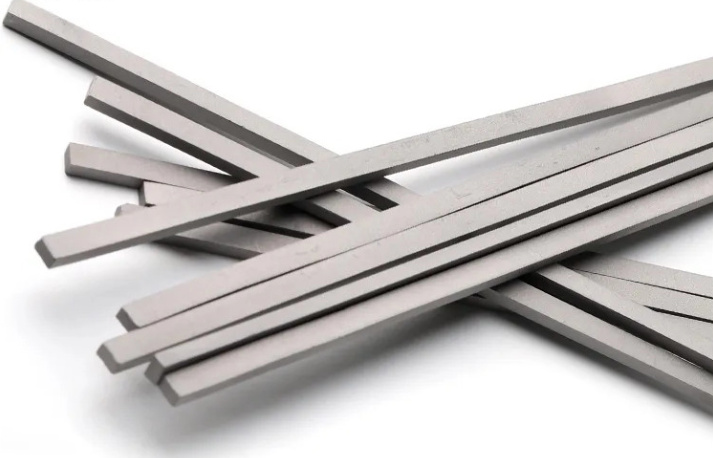
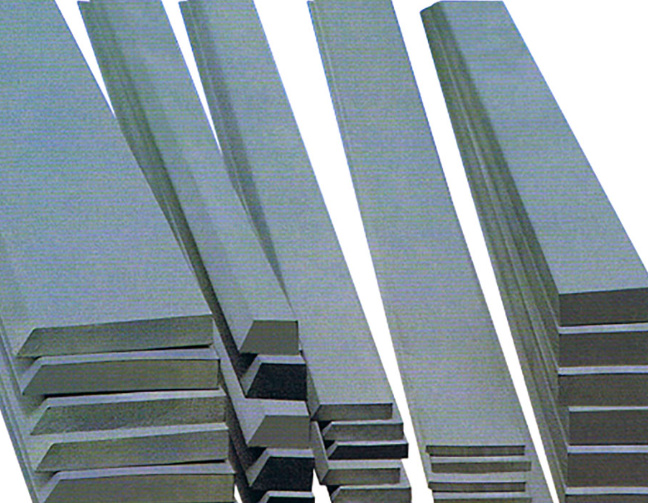
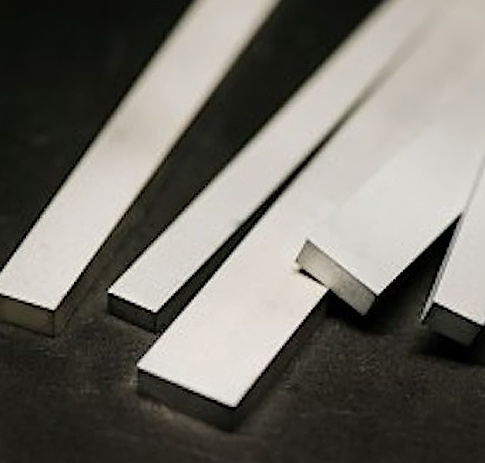
Composition, Properties, and Characteristics
Carbide strips are typically composed of tungsten carbide and a metal binder, usually cobalt. The ratio of tungsten carbide to the binder affects the properties of the strip.
Component | Percentage | Characteristics |
---|---|---|
Tungsten Carbide (WC) | 80% – 95% | Provides hardness and wear resistance. |
Cobalt (Co) | 5% – 20% | Acts as a binder, offering toughness and resistance to cracking. |
Titanium Carbide (TiC) | 0% – 15% | Enhances heat resistance and wear properties in specialized applications. |
Hardness, Strength, and Wear Resistance
Carbide strips are prized for their hardness, strength, and wear resistance, which make them superior to other materials in demanding applications.
Property | Value | Explanation |
---|---|---|
Hardness (Vickers) | 1300 – 1800 HV | High hardness ensures excellent wear resistance and cutting performance. |
Compressive Strength | 3000 – 4000 MPa | High compressive strength makes carbide strips resistant to deformation under heavy loads. |
Fracture Toughness (K_IC) | 10 – 15 MPa·m^0.5^ | Balanced fracture toughness helps prevent chipping and cracking during use. |
Wear Resistance | Very High | Exceptional wear resistance ensures long service life, even in abrasive environments. |
Specifications, Sizes, Shapes, and Standards
Carbide strips are available in various sizes, shapes, and specifications to suit different industrial needs. The specifications often adhere to international standards to ensure consistency and quality.
Specification | Size (mm) | Shape | Standard |
---|---|---|---|
Length | 100 – 500 | Rectangular, Square | ISO 9001 |
Width | 10 – 100 | Round, Flat | ASTM B777 |
Thickness | 2 – 30 | Custom shapes | DIN ISO 2768 |
Tolerance | ±0.01 | Straight, Curved | ANSI B212.15 |
Suppliers and Pricing Details
The cost of carbide strips can vary depending on the grade, size, and supplier. It’s essential to compare prices and suppliers to get the best value.
Supplier | Location | Grade Available | Price Range (USD) | MOQ (Minimum Order Quantity) |
---|---|---|---|---|
XYZ Carbide Ltd. | USA | YG6, YG8, YG10 | $50 – $150 per kg | 10 kg |
ABC Materials Co. | Germany | K10, K20, YT15 | $60 – $170 per kg | 20 kg |
Precision Metals Inc. | China | YG15, YG20, P20 | $40 – $140 per kg | 5 kg |
Carbide Pro Tools | Japan | YT5, YT15, K10 | $70 – $180 per kg | 15 kg |
How to Select the Right Carbide Strip
Choosing the right carbide strip depends on the specific application and the properties you need. Here’s a guide to help you make the best decision.
Consideration | Explanation | Recommended Grade |
---|---|---|
Application | Identify whether the strip will be used for cutting, wear parts, or precision components. | YG6, YG10 for cutting; YG15 for wear parts. |
Hardness Requirement | Higher hardness is ideal for wear resistance but may reduce toughness. | YG8, K10 for high hardness. |
Toughness | Necessary for applications where impact resistance is critical. | YG15, YG20 for high toughness. |
Thermal Stability | Required for high-temperature applications, such as metal cutting and forging. | YT5, YT15 for thermal stability. |
Cost | Balancing cost with performance is crucial, especially in large-scale operations. | YG6, YG8 for cost-effective solutions. |
Supplier Reputation | Ensure the supplier meets quality standards and offers reliable customer support. | Depends on region and availability. |
Comparing Advantages and Limitations of Carbide Strips
Carbide strips offer numerous benefits, but they also have some limitations. Understanding these can help you make a more informed decision.
Parameter | Advantages | Limitations |
---|---|---|
Hardness | Provides excellent wear resistance and cutting performance. | May cause brittleness in some applications. |
Toughness | Offers resistance to chipping and breaking under impact. | Slightly lower than other materials like steel. |
Thermal Stability | Maintains properties at high temperatures, ideal for hot environments. | Can be expensive compared to other materials. |
Cost | Long-lasting, reducing replacement frequency and overall cost. | Higher upfront cost compared to steel and other alloys. |
Versatility | Suitable for a wide range of applications across different industries. | Requires specialized machinery for cutting and shaping. |
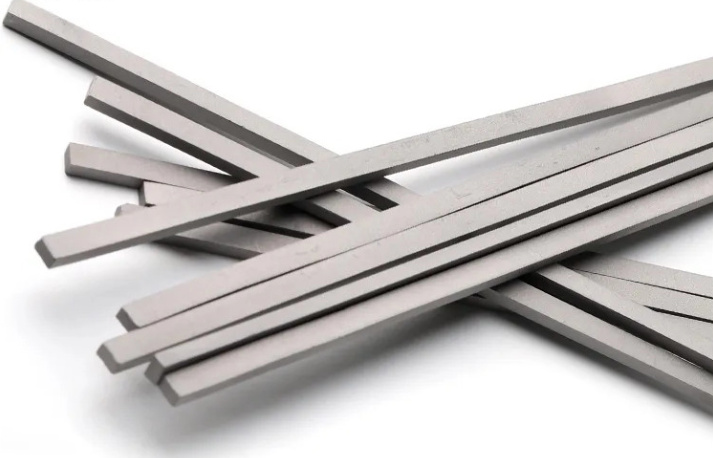
FAQ
What is a carbide strip used for?
Carbide strips are used in various industries for cutting tools, wear parts, and precision components due to their hardness and wear resistance.
How do I choose the right carbide strip?
Consider the specific application, required hardness, toughness, thermal stability, and cost. Refer to the “How to Select the Right Carbide Strip” section for detailed guidance.
Can carbide strips withstand high temperatures?
Yes, carbide strips, especially those with added titanium carbide, can withstand high temperatures and are ideal for cutting and heat-resistant applications.
Are carbide strips expensive?
Carbide strips can be more expensive than traditional materials like steel, but their durability and performance often justify the higher upfront cost.
Where can I buy carbide strips?
You can purchase carbide strips from specialized suppliers such as XYZ Carbide Ltd., ABC Materials Co., and Precision Metals Inc. Pricing and minimum order quantities vary by supplier.
How are carbide strips manufactured?
Carbide strips are made by mixing tungsten carbide powder with a binder, usually cobalt, pressing it into shape, and then sintering it at high temperatures to create a solid, durable material.
Conclusion
Carbide strips are indispensable in various industrial applications, offering unmatched hardness, wear resistance, and thermal stability. By understanding the types, applications, and material properties of carbide strips, you can make informed decisions when selecting the right product for your needs.
Whether you’re cutting, shaping, or forming materials, carbide strips provide a reliable solution that outperforms traditional steel and other materials. Remember to consider the specific requirements of your application and consult with suppliers to ensure you choose the best carbide strip for the job.