Carbide square blanks are an important tool for metalworking and manufacturing. This article provides a comprehensive overview of carbide square blanks, their applications, specifications, installation, and tips for choosing suppliers.
Overview of Carbide Square Blanks
Carbide square blanks are pieces of carbide that have been cut into square shapes to be further machined and finished into end-use parts. Carbide is an extremely hard metal alloy composed of tungsten and carbon atoms.
Some key features of carbide square blanks:
- High hardness and wear resistance – Carbide has a very high hardness rating on the Rockwell scale, making it excellent for cutting tools and wear parts. It maintains sharp cutting edges and resists abrasion.
- Strength at high temperatures – Carbide retains strength and hardness even at high machining temperatures. This allows faster material removal rates.
- Chemical inertness – It resists corrosion and oxidation. Parts made from carbide have long service life even in extreme environments.
- Dimensional stability – Carbide has low thermal expansion, so parts hold form and precise dimensions under temperature changes.
- Manufacturability – Carbide blanks can be machined using grinding and EDM to make intricate geometries. Coatings improve machining.
Carbide square blanks provide an economical starting base material for making cutting tools like end mills, burrs, router bits, engravers, and other wear parts like pelletizer knives, draw dies, and tooling components.
The square shape allows centering the part easily for machining operations on lathes, mills, and other tools. The blanks are made slightly oversized to allow finishing to tight tolerances.
Types of Carbide Square Blanks
There are two main classifications of carbide: tungsten carbide and titanium carbide. They have slightly different properties and applications.
Tungsten Carbide Blanks
- Most commonly used type of carbide. Accounts for >90% of carbide cutting tools.
- Contains 88-97% tungsten carbide along with cobalt binder that holds the carbide particles together.
- Grades vary based on grain size of tungsten carbide and percentage of cobalt. Together they determine hardness, fracture toughness, and strength.
- Common tungsten carbide grades: C1 to C6, K grades
- Used for tooling for machining steels, cast iron, aluminum, wood, plastics etc.
Titanium Carbide Blanks
- Made of titanium carbide instead of tungsten carbide.
- Exhibits higher hardness but lower fracture toughness than tungsten carbide.
- Used where very high wear resistance is needed. Common in wire drawing dies, pelletizer tooling.
- More expensive than tungsten carbide.
Table 1 compares the properties between tungsten carbide and titanium carbide square blanks:
Property | Tungsten Carbide | Titanium Carbide |
---|---|---|
Hardness | 88-93 HRA | 91-95 HRA |
Transverse Rupture Strength | 350-600 ksi | 300-500 ksi |
Fracture Toughness | 6-12 MPa-m^1/2 | 3-6 MPa-m^1/2 |
Maximum Use Temperature | 1000°C | 800°C |
Density | 14.95 g/cc | 4.9 g/cc |
Cost | Low | High |
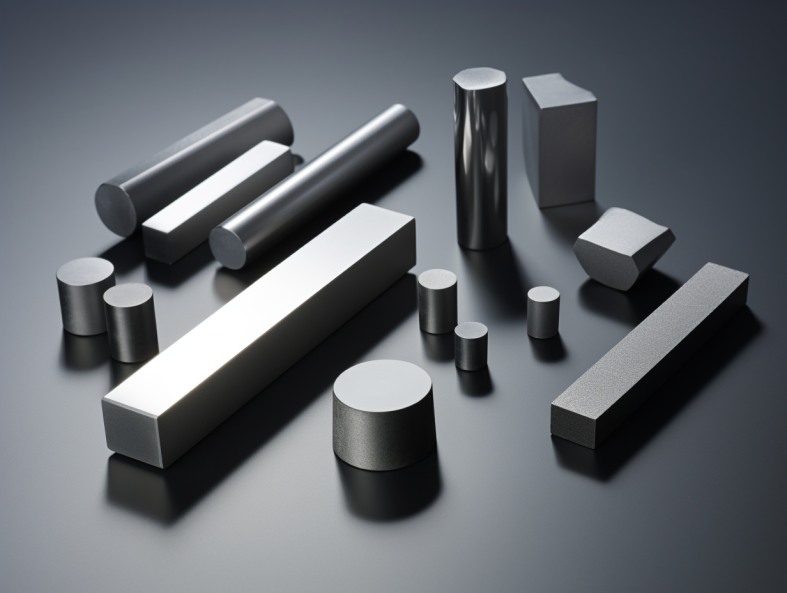
Applications of Carbide Square Blanks
Carbide square blanks are used to manufacture a wide variety of cutting tools, wear parts, and components across metalworking industries.
Some common applications include:
- Cutting tools
- End mills
- Burrs
- Router bits
- Engraving tools
- Form tools
- Counterbores/saws
- Wear parts
- Pelletizer knives
- Wire drawing dies
- Nozzles
- Pump parts
- Components
- Food processing equipment
- High temperature tooling
- Sheet metal forming/stamping
- Bearings and bushings
- Fluid handling parts
Carbide allows longer tool life, faster machining, and precision cutting compared to high speed steel tools. It resists abrasive and corrosive wear in demanding environments.
Table 2 shows some example applications suited for tungsten carbide vs titanium carbide based on their properties:
Application | Tungsten Carbide Grades | Titanium Carbide |
---|---|---|
Cutting tools for steels | C2,C4 | |
Aluminum machining | C6 | |
Mining and construction tools | K10, K20 | K30 |
Pelletizer knives | Grade 5 | |
Circuit board drills | C1 |
Specifications of Carbide Square Blanks
Carbide square blanks are available in a range of standard sizes and dimensions. Typical specifications are given below:
- Sizes: 1/8” to 1” square cross-section
- Lengths: 1” to 4” long
- Tolerances: ±0.002” to ±0.005”
- Corner radii: 0.010” or customized
- Surface finish: 20-25 μin, customized grinding available
- Grades: Standard tungsten carbide C1 to C6 and titanium carbide. Custom alloys available.
- Coatings: TiAlN, TiCN, etc. to improve machining.
Carbide blanks can be made to order with non-standard dimensions, tighter tolerances, edge preps, hole drilling, flats added, and other customized features.
Table 3 shows common sizes and grades of ready stock carbide square blanks from leading manufacturers:
Size (inches) | Standard Grades Stocked |
---|---|
0.125 (1/8) | C1, C2, C4 |
0.250 (1/4) | C2, C4 |
0.375 (3/8) | C2, C4 |
0.500 (1/2) | C2, C4 |
0.625 | C2, C3, C4 |
0.750 | C2, C3, C4 |
1.000 | C2, C3, C4 |
Carbide Blank Installation Tips
Carbide square blanks need proper handling and workholding during machining to prevent damage. Here are some best practices:
- Use carbide-tipped vise jaws or aluminum soft jaws to grip parts
- Clamp only on the edges, not on the delicate corners
- Allow for expansion – do not clamp too tightly
- Use through bolts to secure parts if needed
- Minimize overhang when holding in chucks
- Use parallels or shims to spread clamping force
- Lubricate contacting surfaces
- Keep coolant directed to contact areas
Take light finishing cuts and avoid rapid changes in force or temperature. Allow time for heat dissipation. Use coated carbide inserts designed for hard metals machining.
Tips for Choosing a Carbide Blank Supplier
Consider the following when selecting a supplier for your carbide square blanks:
- Range of sizes and grades in ready stock
- Availability of customized blank dimensions
- Consistent quality and adherence to specifications
- Tight dimensional tolerances held (±0.0005″ or better)
- Corner edge quality (small radius, no chips)
- Squareness of the blanks (0.0005″ or better)
- Surface finish quality (20 μin or lower)
- Optional value-added services like edge preps or coatings
- Inventory availability and fast turnaround on orders
- Competitive pricing with quantity discounts
- Responsive customer service and technical expertise
Leading global suppliers of carbide blanks include Kennametal, Mitsubishi Materials, Midwest Tungsten Service, Carbide USA, Command Tooling Systems, and Advent Tool & Manufacturing.
Purchasing through a distributor allows customizing blanks and combining various grades and sizes in one order.
Comparing Carbide Grades for Cutting Tools
Carbide tooling grade selection impacts performance in different material cutting applications. Comparing grades helps choose the optimal grade.
Coarse vs. Fine Grain Size
- Coarse grain carbide has higher fracture resistance
- Fine grain allows sharper cutting edges
Higher Cobalt Content
- Increases strength and heat resistance
- Less resistance to abrasive wear
Common Grades Compared
- C1/K10 – Universal use carbide, low cost
- C2/K20 – Good all-around tools and wear parts
- C4 – High cobalt alloy resists abrasive wear
- C6 – Finer grain for finishing cuts
- C5/K30 – Superior wear resistance but more brittle
Best Grades for Materials
- Steels – C2, C6
- Cast iron – C7, K40
- Aluminum – C2, C4
- Wood – C3, C4
- Hardened metals – C5, K30
Proper carbide selection maximizes tooling performance in specific material cutting applications. Consult suppliers to match the carbide grade with your workpiece materials based on the properties required.
Advantages and Limitations of Carbide Blanks
Carbide blanks offer notable benefits but also have some limitations to consider:
Advantages
- Extreme hardness and wear resistance
- Maintains sharp cutting edge
- Withstands high temperatures
- Dimensional stability in operation
- Corrosion and chemical resistance
- Consistent quality from sintering process
Limitations
- Brittle material – prone to chipping
- Difficult to machine without diamond grinding
- Heavier than steel tools of same size
- Higher cost than steel tooling
- Care required in handling and storage
- Coatings may delaminate under extreme use
Understanding both the strengths and limitations helps select the best applications for carbide and determine any special handling needed. Proper use of carbide blanks enhances machining performance.
Frequently Asked Questions About Carbide Blanks
Below are answers to some common questions about carbide square blanks:
Q: What precision can be achieved when machining carbide blanks?
A: Carbide blanks can be machined to tolerances of ±0.001” or ±0.0005” when using precision diamond grinding. Even tighter tolerances are possible for semi-finish blanks.
Q: Should carbide blanks be stored in a particular way?
A: Carbide blanks should be kept dry and clean. Avoid temperature extremes. Store in consistent shop conditions away from chemicals. Protect delicate edges/corners from contact damage.
Q: How long do carbide tooling and wear parts typically last?
A: Carbide parts see 5-10X longer life vs. steel parts. Tool life depends on factors like feed rate, work material, use of coolant. On average end mills last 30-60 mins, pelletizer knives 100-300 hours before needing replacement.
Q: Can any specialty coatings be applied to carbide blanks?
A: Yes, carbide blanks are commonly coated with TiAlN, TiCN, diamond, CVD diamond, titanium aluminium carbonitride, etc. to enhance tool performance.
Q: How are micro-cracks or large chips in a carbide blank repaired?
A: Damaged carbide blanks should not be machined further. Refurbishment options include edge honing, grinding away defects, welding on additional carbide, or using as a smaller square blank.
Q: What are the best ways to cut costs when buying carbide blanks?
A: Optimize blank dimensions to require less grinding. Buy in bulk for quantity discounts. Consider ready-to-use blanks with minimal machining needed. Use standard grades and sizes in stock rather than custom ordering.
Conclusion
Carbide square blanks provide an economical starting point for manufacturing precision cutting tools, wear parts, and components needing hardness, strength, and dimensional stability. Grades and specifications can be selected to suit the end application. With proper handling and machining technique, carbide blanks can be fabricated into high-performance parts with tight tolerances. This guide covers key considerations in selecting and working with carbide blanks to maximize their advantages.