Carbide saw tips are essential components in various industries, especially in woodworking and metal cutting. These small, yet powerful pieces of technology play a crucial role in ensuring precision, durability, and efficiency in cutting processes. Whether you’re a professional craftsman or someone just getting into the industry, understanding carbide saw tips is vital for maximizing your tools’ performance.
In this comprehensive guide, we’ll delve deep into everything related to carbide saw tips. We’ll explore their types, applications, material properties, compositions, and much more. By the end, you’ll have a thorough understanding of these critical tools, enabling you to make informed decisions on their selection and use.
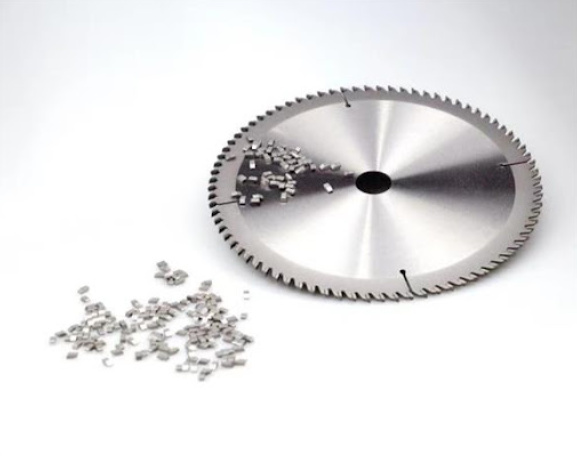
Overview of Carbide Saw Tips
Carbide saw tips are the cutting edges attached to the teeth of saw blades, typically used in circular saws, band saws, and other types of cutting tools. Made primarily from tungsten carbide, these tips are known for their extreme hardness, wear resistance, and ability to maintain a sharp cutting edge longer than steel tips.
Carbide is a compound composed of carbon and another metal, in this case, tungsten. The combination of these materials gives carbide its unique properties, making it highly effective in industrial applications where precision and durability are paramount.
Why Carbide?
Carbide saw tips offer several advantages over traditional steel or high-speed steel (HSS) tips. They are harder, more wear-resistant, and can cut through tougher materials without dulling quickly. This makes them ideal for applications involving hard metals, hardwoods, and composite materials.
Types of Carbide Saw Tips
The type of carbide used in saw tips can vary significantly, affecting the performance, durability, and cost of the tool. Below are some of the most common types of carbide saw tips available:
Type of Carbide Saw Tip | Description |
---|---|
C1 Carbide | Excellent for cutting softwood and non-ferrous metals, offering good wear resistance. |
C2 Carbide | Versatile, suitable for cutting hardwood, softwood, and some metals, offers balance between toughness and wear resistance. |
C3 Carbide | Ideal for cutting hardwood and MDF, providing a higher hardness level for longer wear resistance. |
C4 Carbide | Used for cutting very hard materials, including metals, with the highest wear resistance and hardness. |
Micrograin Carbide | Provides a sharp cutting edge for precise cuts, ideal for detailed work on wood and metal. |
Submicron Carbide | Offers the finest grain size, leading to superior sharpness and cutting performance. |
Nano-grain Carbide | Designed for the highest precision cuts, with extreme hardness and wear resistance. |
Polycrystalline Diamond (PCD) | A blend of carbide and diamond particles, perfect for ultra-hard materials and high-volume cutting. |
Titanium Carbide | A specialized carbide that offers high corrosion resistance and is used in cutting abrasive materials. |
Tantalum Carbide | Known for its exceptional toughness and resistance to thermal shock, ideal for cutting applications involving high temperatures. |
Applications of Carbide Saw Tips
Carbide saw tips are used in a wide range of applications due to their versatility and durability. The following table highlights some of the primary industries and applications where carbide saw tips are essential:
Application | Description |
---|---|
Woodworking | Used for cutting hardwood, softwood, plywood, MDF, and other composite materials with precision and durability. |
Metalworking | Essential for cutting non-ferrous metals like aluminum, brass, and copper, as well as ferrous metals with advanced carbide grades. |
Plastics and Composites | Carbide tips are perfect for cutting plastics, laminates, and composites without melting or chipping the material. |
Masonry and Concrete Cutting | Specialized carbide tips are used to cut through concrete, bricks, and stones, offering long-lasting performance. |
Glass and Ceramics | Involved in precise cutting of glass and ceramics, especially when using diamond-enhanced carbide tips. |
Automotive Industry | Used in manufacturing processes for cutting engine components, exhaust systems, and other metallic parts. |
Aerospace Industry | Applied in cutting high-strength alloys and composites used in aircraft construction. |
Textile Industry | Involved in cutting thick fabrics, leathers, and textiles with precision and minimal fraying. |
Food Processing | Carbide saw tips are used in industrial food slicing machines for cutting frozen or dense food products. |
Recycling Industry | Utilized in shredders and other recycling equipment to cut through tough materials like metal scraps and plastics. |
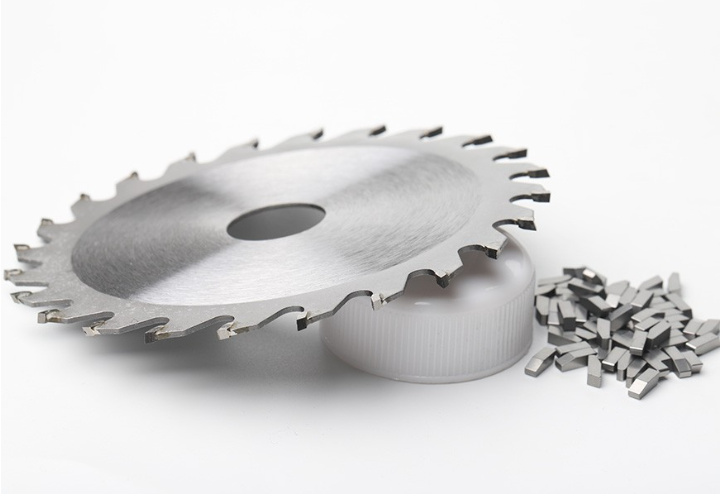
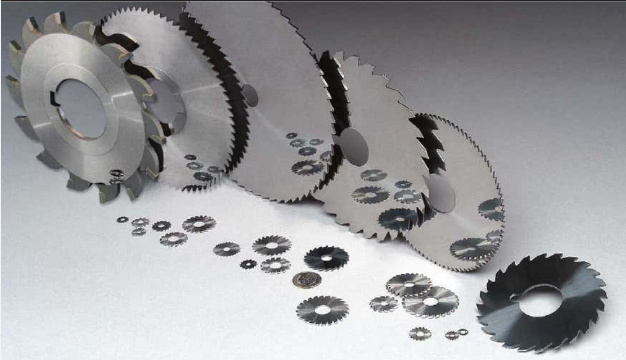
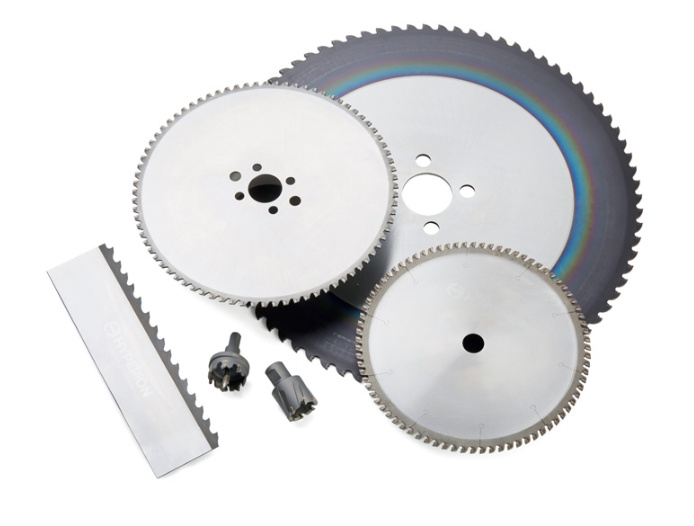
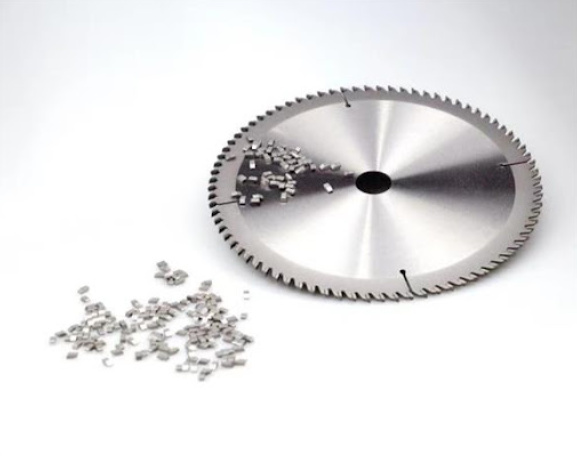
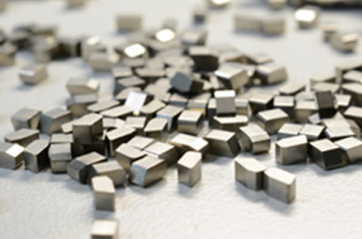
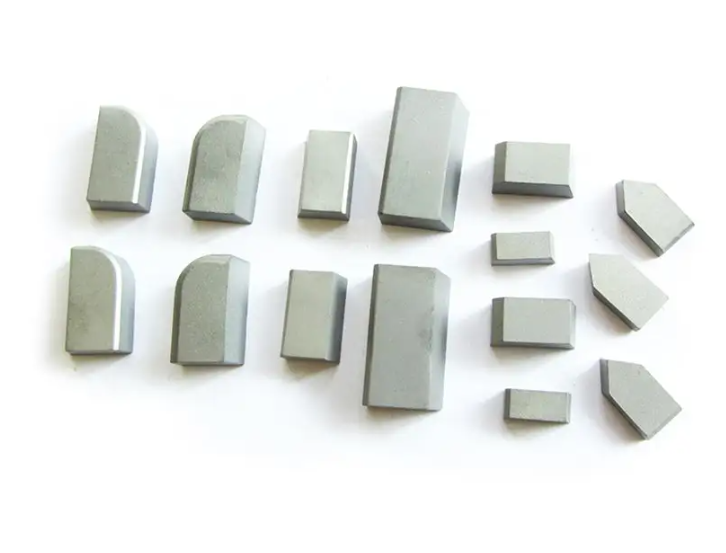
Material Properties of Carbide Saw Tips
The performance of carbide saw tips depends heavily on their material properties. These properties influence how the tips handle heat, stress, and wear during cutting operations. Here’s a closer look at some of the critical material properties of carbide saw tips:
Property | Description |
---|---|
Hardness | Carbide is extremely hard, often ranging between 1,700 and 2,200 Vickers Hardness (HV), making it suitable for cutting hard materials. |
Wear Resistance | High resistance to wear and abrasion, ensuring a longer tool life even in harsh conditions. |
Toughness | Balancing hardness with toughness is crucial; higher toughness allows carbide tips to absorb shocks without chipping. |
Thermal Conductivity | Carbide has good thermal conductivity, allowing it to dissipate heat efficiently and reducing the risk of overheating. |
Corrosion Resistance | Some carbides, like titanium carbide, offer excellent corrosion resistance, ideal for cutting in corrosive environments. |
Edge Retention | Carbide tips maintain a sharp edge for longer periods, reducing the frequency of sharpening or replacement. |
Density | Carbide is denser than steel, providing stability during cutting operations and reducing vibrations. |
Composition, Properties, and Characteristics
Understanding the composition and properties of carbide saw tips can help in selecting the right type for your specific needs. Below is a breakdown of various compositions and their characteristics:
Carbide Composition | Properties | Characteristics |
---|---|---|
Tungsten Carbide (WC) | High hardness, excellent wear resistance, moderate toughness. | The most common carbide used in saw tips, offering a good balance between wear resistance and toughness. |
Cobalt Binder (Co) | Enhances toughness, helps bind carbide particles, improves shock absorption. | Cobalt increases the overall toughness, making the carbide less brittle and more durable under stress. |
Nickel Binder (Ni) | Offers better corrosion resistance than cobalt, with moderate toughness. | Ideal for applications involving moisture or corrosive environments. |
Titanium Carbide (TiC) | Excellent wear resistance, high hardness, and good thermal stability. | Used in applications requiring cutting of abrasive materials or high-temperature operations. |
Tantalum Carbide (TaC) | High toughness, excellent resistance to thermal shock, and good wear resistance. | Suitable for high-temperature cutting operations and where thermal cycling is frequent. |
Chromium Carbide (CrC) | Superior corrosion resistance, moderate hardness, and good toughness. | Often used in corrosive environments or for cutting materials that produce corrosive by-products. |
Vanadium Carbide (VC) | Extremely high hardness and wear resistance, used as an additive to improve performance. | Enhances wear resistance and cutting performance, especially in abrasive applications. |
Polycrystalline Diamond (PCD) | Exceptional hardness, ultra-high wear resistance, ideal for cutting ultra-hard materials. | Combines diamond particles with carbide to achieve the highest levels of wear resistance and cutting precision. |
Hardness, Strength, and Wear Resistance
Carbide saw tips must balance hardness, strength, and wear resistance to perform optimally in different applications. The following table outlines these properties for various carbide compositions:
Carbide Composition | Hardness (HV) | Compressive Strength (MPa) | Wear Resistance |
---|---|---|---|
Tungsten Carbide (WC) | 1,700 – 2,200 | 4,000 – 7,000 | High |
Cobalt Binder (Co) | 1,200 – 1,800 | 3,500 – 6,000 | Moderate |
Nickel Binder (Ni) | 1,300 – 1,900 | 3,800 – 6,200 | Moderate |
Titanium Carbide (TiC) | 2,400 – 3,000 | 4,500 – 7,500 | Very High |
Tantalum Carbide (TaC) | 1,800 – 2,500 | 4,000 – 7,000 | High |
Chromium Carbide (CrC) | 1,500 – 2,100 | 3,800 – 6,500 | Moderate to High |
Vanadium Carbide (VC) | 2,600 – 3,200 | 4,800 – 8,000 | Very High |
Polycrystalline Diamond (PCD) | 6,000 – 10,000 | 8,000 – 10,000 | Ultra-High |
Specifications, Sizes, Shape, and Standards
Carbide saw tips come in various sizes, shapes, and standards depending on the application and the type of material being cut. Understanding these specifications is crucial for selecting the right saw tips for your needs:
Specification | Description |
---|---|
Size | Carbide saw tips range in size, typically from 0.5mm to 5mm in thickness, and up to 20mm in width. |
Shape | Common shapes include trapezoidal, rectangular, triangular, and custom profiles for specific tools. |
Standards | Carbide saw tips often adhere to international standards such as ISO, ANSI, and DIN for consistency in quality. |
Edge Geometry | Tips may have different edge geometries, such as flat, beveled, or rounded edges, depending on the cutting application. |
Grade | Grades vary based on the composition and intended use, with common grades including K10, K20, and K30. |
Coating | Some carbide tips may be coated with additional materials like titanium nitride (TiN) for enhanced performance. |
Tolerance | Precision is key, with tolerances typically ranging from ±0.001mm to ±0.01mm depending on the application. |
Suppliers and Pricing Details
Finding the right supplier for carbide saw tips is crucial, as it directly impacts the quality and cost of your tools. Here’s a table with some suppliers and general pricing information:
Supplier | Country | Product Range | Average Price (per tip) |
---|---|---|---|
Kennametal | USA | Wide range of carbide saw tips for various applications. | $2.50 – $15.00 |
Sandvik Coromant | Sweden | High-performance carbide tips with advanced coatings. | $3.00 – $20.00 |
Sumitomo Electric | Japan | Innovative carbide solutions with a focus on durability. | $2.00 – $18.00 |
Guhring | Germany | Precision-engineered carbide tips for industrial use. | $2.50 – $17.00 |
Seco Tools | Sweden | Specialized in carbide tips for metalworking applications. | $3.50 – $19.00 |
Kyocera | Japan | Comprehensive range of carbide tips for cutting applications. | $2.00 – $16.00 |
Carbide Depot | USA | Distributor of various carbide tip brands and custom solutions. | $2.00 – $15.00 |
Iscar | Israel | High-quality carbide tips with a focus on innovation. | $3.00 – $18.00 |
TaeguTec | South Korea | Offers a wide selection of carbide tips for diverse industries. | $2.50 – $17.00 |
Mitsubishi Materials | Japan | Premium carbide tips designed for high-performance applications. | $3.00 – $20.00 |
Selecting the Right Carbide Saw Tips
Choosing the right carbide saw tips involves considering several factors, including the material to be cut, the desired finish, the cutting speed, and the tool’s longevity. Here’s a guide to help you select the most suitable carbide saw tips for your needs:
Consideration | Description |
---|---|
Material Being Cut | Harder materials require carbide tips with higher wear resistance (e.g., C4 or PCD tips for metal cutting). |
Cutting Speed | Higher cutting speeds may demand tougher carbide grades to prevent chipping (e.g., micrograin carbide). |
Desired Finish | Finer finishes often require sharper tips with precise edge geometries (e.g., submicron or nano-grain carbide). |
Tool Longevity | For long-lasting performance, select carbide tips with superior hardness and wear resistance (e.g., WC with TiC). |
Budget | Higher-grade carbide tips cost more but offer better performance and longevity, balancing upfront cost against long-term savings. |
Application Specificity | Specialized applications, like cutting composites or abrasive materials, may require tailored carbide compositions (e.g., CrC or TaC). |
Advantages and Limitations of Carbide Saw Tips
Like any material, carbide saw tips have their pros and cons. Understanding these can help you make better decisions when selecting the right tips for your projects.
Advantages | Limitations |
---|---|
Exceptional Hardness | Can be more brittle compared to other materials. |
Longer Tool Life | Higher initial cost compared to steel or HSS. |
Maintains Sharp Edge Longer | Requires specialized equipment for sharpening. |
Versatile Across Materials | Not suitable for all materials, especially ultra-soft ones. |
High Heat Resistance | May require coatings for specific high-temperature applications. |
Precision Cutting | Overkill for simple or soft material cutting tasks. |
How to Choose the Right Carbide Saw Tips
Selecting the right carbide saw tips can feel overwhelming, especially with so many factors to consider. But don’t worry, it’s not as complicated as it seems. Think of it like picking out a pair of shoes. You wouldn’t wear the same shoes for a marathon that you’d wear to a formal event, right? The same principle applies here. Let’s break down how to choose the right carbide saw tips for your needs.
1. Understand Your Material
The first step is understanding the material you’ll be cutting. Are you slicing through hardwood, softwood, metal, or perhaps something more exotic like composites or ceramics? Each material demands different properties from your carbide saw tips.
- For Softwoods and Non-Ferrous Metals: Consider C1 or C2 carbide tips. They offer a good balance of wear resistance and toughness.
- For Hardwoods and MDF: C3 or C4 carbide tips are better suited as they provide higher hardness, which is essential for these tougher materials.
- For Metals and Abrasive Materials: Go for higher-grade carbides like C4 or specialized compositions like Titanium Carbide or PCD.
2. Consider the Cutting Speed
Faster isn’t always better, especially when it comes to cutting speed. If your saw operates at high speeds, you’ll need tips that can withstand the heat and friction without dulling quickly.
- High-Speed Cutting: Opt for carbide tips with superior wear resistance, such as micrograin or submicron carbides. They maintain sharpness even at high RPMs.
- Lower-Speed Cutting: If you’re not in a rush, you can use standard C2 or C3 carbide tips, which balance durability and cost-effectiveness.
3. Factor in the Desired Finish
Not all cuts are created equal. Sometimes, you need a rough cut, and other times, you want a finish so smooth it feels like glass. Your carbide saw tips play a big role in this.
- For Fine Finishes: Choose tips with precise edge geometries, like submicron or nano-grain carbide tips. These are designed for high-precision cuts.
- For Rough Cuts: Standard carbide tips with a robust edge will do the job, especially if speed is more important than finish quality.
4. Think About Tool Longevity
Nobody likes replacing tools frequently. If you want your carbide saw tips to last longer, pay attention to their composition.
- For Long-Lasting Performance: Invest in tips made from Tungsten Carbide with additional elements like Titanium Carbide (TiC) or Tantalum Carbide (TaC). These enhance durability and wear resistance.
- For Short-Term or Low-Volume Use: You might opt for less expensive tips, such as standard C2 or C3 grades.
5. Budget Matters
Let’s be real—cost is always a factor. While carbide saw tips are an investment, it’s important to balance cost with performance.
- Higher Budget: If you have the budget, go for higher-grade carbide tips, as they offer better performance and longer tool life.
- Tighter Budget: If cost is a concern, choose mid-range options like C2 or C3 carbide tips, which provide good performance without breaking the bank.
Comparing Advantages and Limitations
When comparing different carbide saw tips, it’s important to weigh the pros and cons to see what fits best with your specific needs.
Advantage | Limitation |
---|---|
Long-lasting Sharpness | Brittle Nature: Prone to chipping if used improperly. |
Versatility Across Various Materials | Higher Initial Cost: More expensive than steel. |
High Heat Resistance | Requires Specialized Sharpening Equipment: Not easily sharpened by standard tools. |
Durable and Hard-wearing | Not Ideal for All Applications: Over-engineered for softer materials. |
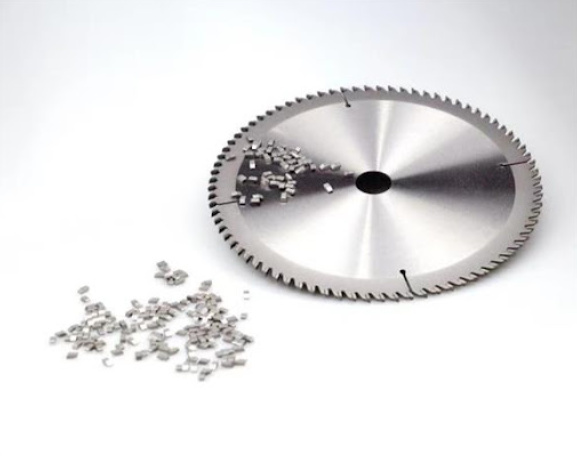
FAQs
Here are some frequently asked questions that might help clarify any lingering doubts:
Question | Answer |
---|---|
What are carbide saw tips made of? | Carbide saw tips are primarily made of tungsten carbide, often combined with other elements like cobalt, nickel, or titanium to enhance performance. |
How do I know when to replace my carbide saw tips? | Replace your tips when they start to show signs of dullness, chipping, or if the quality of the cut begins to deteriorate. |
Can carbide saw tips be sharpened? | Yes, but they require specialized equipment to sharpen due to their hardness. It’s often more cost-effective to replace them. |
Are carbide saw tips worth the investment? | Absolutely! While they are more expensive upfront, their longevity, durability, and performance make them a cost-effective choice in the long run. |
Can I use carbide saw tips on any material? | Carbide saw tips are versatile, but it’s essential to choose the right type for the specific material you’re cutting to avoid damage or poor performance. |
How do I choose the right carbide saw tip for my project? | Consider the material you’re cutting, the desired finish, cutting speed, and your budget when selecting a carbide saw tip. |
Why are carbide saw tips so expensive? | The cost is due to the advanced materials and manufacturing processes involved in making carbide tips, which provide superior performance and longevity. |
How do carbide saw tips compare to steel tips? | Carbide tips are harder, last longer, and perform better on tougher materials compared to steel tips, though they are also more expensive. |
What is the difference between micrograin and submicron carbide? | Micrograin carbide has larger grains and is used for general-purpose cutting, while submicron carbide has finer grains for precision cutting and sharper edges. |
Do carbide saw tips require any special care? | Keep them clean, avoid cutting materials they aren’t designed for, and store them properly to prevent damage or chipping. |
Conclusion
Carbide saw tips are a critical component in achieving precise, efficient, and durable cutting performance across various industries. Whether you’re working with wood, metal, or composites, choosing the right carbide saw tips can significantly impact your productivity and the quality of your work.
By understanding the types of carbide saw tips available, their applications, material properties, and how to select the right ones, you can make informed decisions that will enhance your cutting operations and save you time and money in the long run.
Remember, the right carbide saw tip is not just about the material it cuts but how it performs under your specific conditions. So, invest wisely, and you’ll see the benefits in your work quality and tool longevity.