Selecting the right carbide saw tips involves a blend of understanding your cutting needs and matching them with the characteristics of available tips. Here’s a detailed guide to help you make an informed choice:
Material to be Cut
The type of material you’ll be cutting—whether it’s wood, metal, plastic, or composites—affects the selection of carbide saw tips. Each material has different hardness and abrasiveness, which requires a specific type of carbide tip to achieve optimal cutting performance.
- Wood: For woodworking, micro-grain or tungsten carbide tips are preferred due to their fine edge and durability. They offer smooth cuts and longevity.
- Metal: When cutting metals, especially ferrous materials, tungsten carbide or cobalt-bonded tips are ideal for their hardness and resistance to wear.
- Composites and Plastics: Titanium carbide tips or PCD (Polycrystalline Diamond) tips are often used due to their ability to handle non-ferrous materials and maintain sharpness.
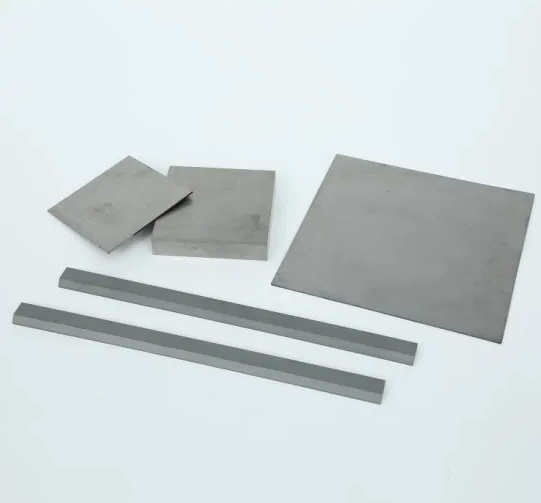
Cutting Conditions
The environment in which the saw tips will operate—such as temperature, humidity, and the presence of corrosive substances—can influence the choice.
- High Temperatures: For cutting at high temperatures, tips with excellent thermal resistance like silicon carbide or titanium carbide are beneficial.
- Corrosive Environments: In environments prone to corrosion, chrome carbide tips or those with special coatings can offer added protection.
Tip Hardness and Wear Resistance
Different carbide tips offer varying levels of hardness and wear resistance. Harder tips last longer but may be more brittle, while those with high wear resistance maintain their edge but can be less tough.
- Hardness: Choose tips with higher hardness for long-lasting sharpness and precision. Tungsten carbide tips generally offer high hardness.
- Wear Resistance: Tips with high wear resistance are suited for applications involving abrasive materials or prolonged use. PCD tips are known for their exceptional wear resistance.
Cost vs. Performance
Balancing cost and performance is crucial. Higher-end tips like PCD are expensive but offer unmatched performance and longevity. For budget-conscious applications, standard tungsten carbide or cobalt-bonded tips might be more cost-effective.
- Budget-Friendly: Tungsten carbide tips are a good balance between cost and performance.
- Premium Performance: For critical applications where performance is paramount, investing in PCD or ultra-fine grain carbide tips is advisable.
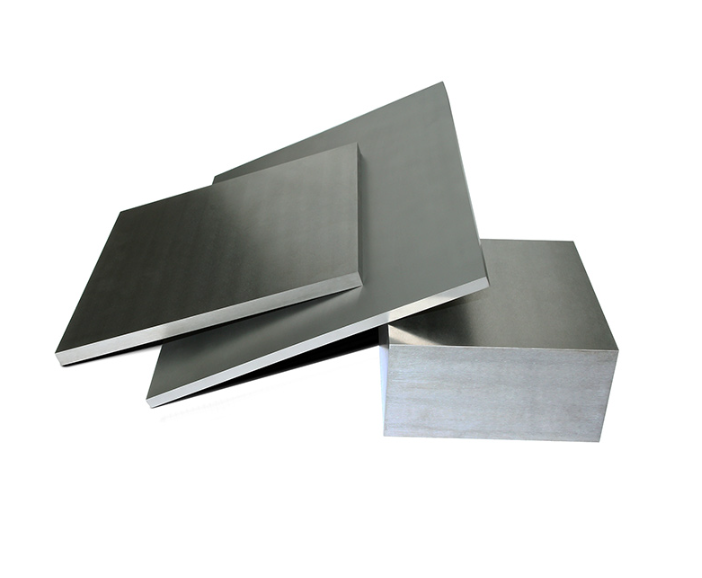
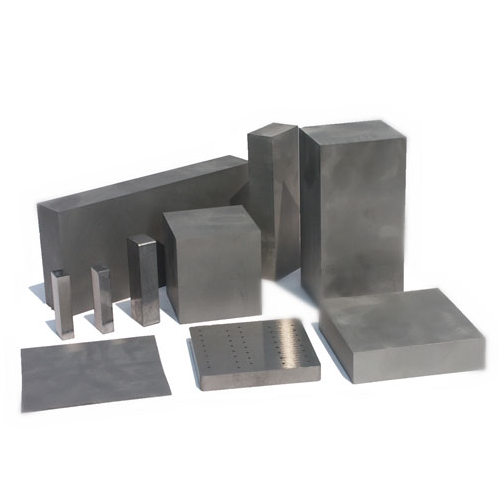
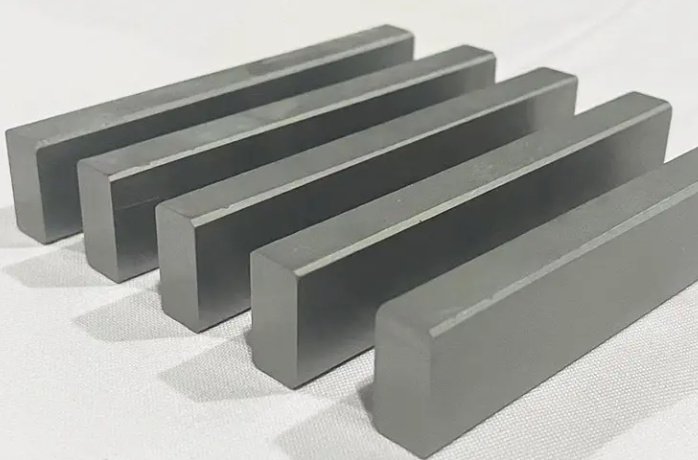
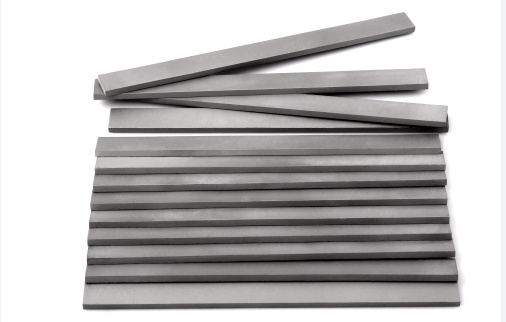
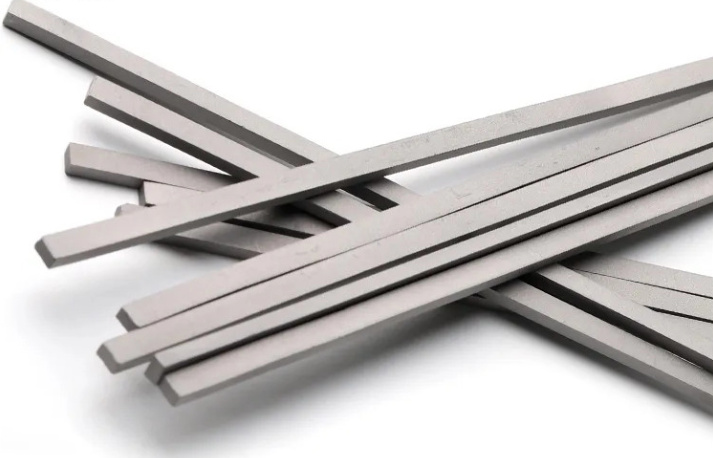
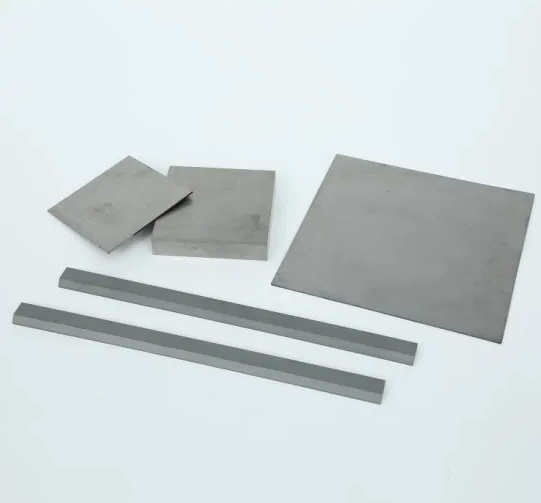
Advantages and Limitations of Carbide Saw Tips
To make a well-informed decision, it’s helpful to understand the advantages and limitations of different carbide saw tips. Here’s a comparison to guide your choice:
Tungsten Carbide Tips vs. Cobalt-Bonded Carbide Tips
Feature | Tungsten Carbide Tips | Cobalt-Bonded Carbide Tips |
---|---|---|
Hardness | High, maintains sharp edge for extended periods. | Slightly less hard but more impact resistant. |
Wear Resistance | Excellent, ideal for abrasive materials. | Good, suitable for less abrasive applications. |
Toughness | Hard but can be brittle under high impact. | More impact resistant, less brittle. |
Cost | Generally higher due to material cost. | Usually less expensive than tungsten carbide tips. |
Polycrystalline Diamond (PCD) Tips vs. Silicon Carbide Tips
Feature | PCD Tips | Silicon Carbide Tips |
---|---|---|
Hardness | Extremely hard, suitable for the hardest materials. | Hard but less than PCD. |
Wear Resistance | Superior, excellent for high-abrasion applications. | Good, suited for cutting ceramics and glass. |
Toughness | Brittle, not ideal for high-impact applications. | More tough and impact resistant. |
Cost | Expensive, reflecting its high performance. | More affordable compared to PCD tips. |
Micro-grain Carbide Tips vs. Ultra-fine Grain Carbide Tips
Feature | Micro-grain Carbide Tips | Ultra-fine Grain Carbide Tips |
---|---|---|
Hardness | Very hard, good for fine cuts. | Extremely hard, best for high-precision work. |
Wear Resistance | High, suitable for precise applications. | Very high, ideal for demanding cutting tasks. |
Toughness | Less tough, more suitable for non-impact applications. | Very hard and less tough, best for precision. |
Cost | Generally less expensive than ultra-fine tips. | Higher cost due to advanced manufacturing. |
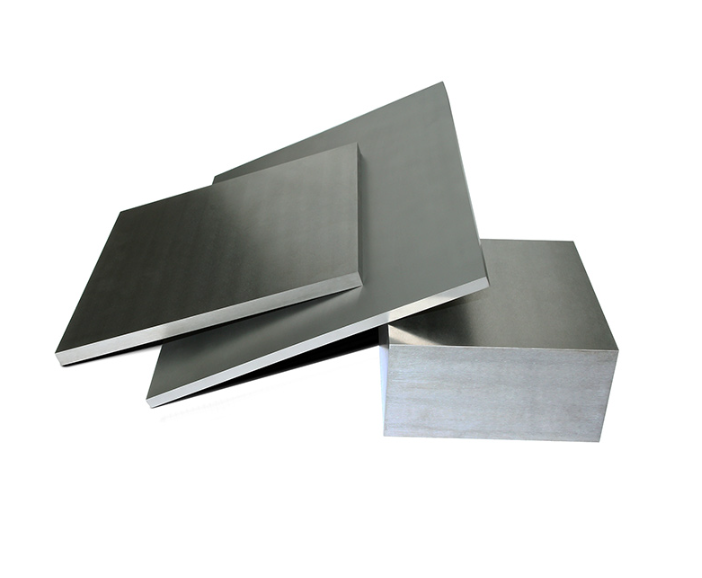
FAQ
Question | Answer |
---|---|
What are carbide saw tips made of? | Carbide saw tips are primarily made of tungsten carbide, though other materials like cobalt-bonded carbide, titanium carbide, and polycrystalline diamond (PCD) are also used. |
How do I choose the right carbide saw tips? | Consider the material you’re cutting, the cutting conditions, the hardness and wear resistance of the tips, and your budget. Matching these factors with the properties of the carbide tips will help you select the best option. |
What are the benefits of tungsten carbide tips? | Tungsten carbide tips are highly durable, offer excellent hardness and wear resistance, and are ideal for cutting hard materials. |
Are PCD tips worth the investment? | PCD tips are highly durable and offer superior performance for cutting hard and abrasive materials. They are expensive, so they are best suited for applications where their performance justifies the cost. |
How long do carbide saw tips typically last? | The lifespan of carbide saw tips varies based on usage, material being cut, and maintenance. Generally, tips with higher hardness and wear resistance last longer. |
Can carbide saw tips be customized? | Yes, many suppliers offer customization options for carbide saw tips to meet specific application needs. |
What are the typical applications for silicon carbide tips? | Silicon carbide tips are used for cutting ceramics, glass, and other abrasive materials. They are chosen for their ability to withstand high temperatures and corrosive environments. |
This guide should provide a solid foundation for understanding carbide saw tips and choosing the right supplier. For further details, especially regarding specific suppliers and pricing, it’s best to consult with industry experts or directly with suppliers.