Introduction
In the realm of cutting tools, the material of the saw tip is a critical determinant of performance, durability, and efficiency. Carbide saw tips, made from tungsten carbide, have emerged as a leading choice for saw blades and cutting tools across various industries. This blog explores the myriad advantages of using carbide saw tips over other materials, emphasizing their unique properties and the benefits they bring to cutting applications.
What Are Carbide Saw Tips?
Carbide saw tips are small, hard components attached to the teeth of saw blades. They are typically made from tungsten carbide, a material renowned for its exceptional hardness and wear resistance. These tips are engineered to withstand the rigors of cutting through various materials, from wood and plastics to metals and composites.
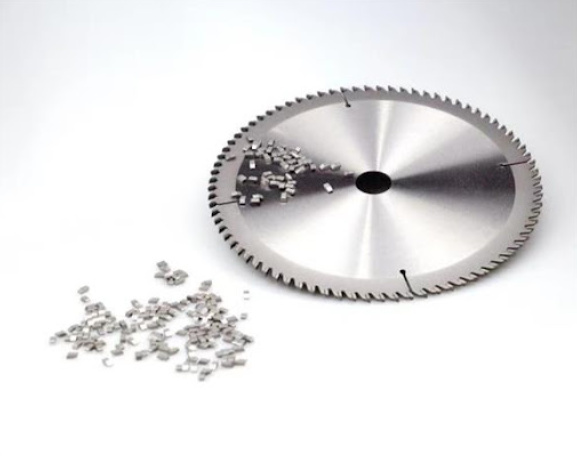
Advantages of Carbide Saw Tips
1. Exceptional Hardness and Durability
Carbide saw tips are known for their remarkable hardness, which significantly contributes to their durability. Tungsten carbide is one of the hardest materials available, second only to diamond. This exceptional hardness allows carbide saw tips to maintain their sharpness and cutting edge far longer than tips made from other materials like high-speed steel (HSS) or tool steel.
2. Superior Wear Resistance
One of the standout features of carbide saw tips is their superior wear resistance. This property ensures that the tips can endure extended periods of cutting without significant wear. The wear resistance of carbide tips translates into longer tool life, reducing the frequency of replacements and maintenance.
3. High Cutting Efficiency
Carbide saw tips offer high cutting efficiency, making them ideal for high-speed cutting applications. The sharpness and hardness of carbide allow for smoother and faster cuts, reducing the effort and energy required. This efficiency is particularly beneficial in industrial settings where productivity and precision are paramount.
4. Versatility Across Materials
Carbide saw tips are incredibly versatile, capable of cutting through a wide range of materials with ease. Whether it’s wood, plastic, non-ferrous metals, or even hard metals, carbide tips deliver consistent performance. This versatility makes them a preferred choice for various industries, from woodworking and metalworking to construction and manufacturing.
5. Heat Resistance
During cutting operations, saw tips are subjected to high temperatures due to friction. Carbide saw tips excel in heat resistance, maintaining their hardness and cutting efficiency even at elevated temperatures. This characteristic prevents tip deformation and ensures consistent cutting performance under demanding conditions.
6. Precision and Finish Quality
The sharpness and stability of carbide saw tips contribute to superior precision and finish quality. Carbide tips produce cleaner cuts with minimal burring or rough edges, enhancing the overall quality of the finished product. This precision is crucial in applications where accuracy and fine finishes are essential.
7. Cost-Effectiveness Over Time
While carbide saw tips may have a higher initial cost compared to other materials, their longevity and performance make them cost-effective in the long run. The extended tool life and reduced maintenance requirements lead to lower overall costs, offering excellent value for money.
8. Improved Tool Stability
The rigidity and strength of carbide saw tips provide improved tool stability during cutting operations. This stability minimizes vibrations and deflections, resulting in more accurate and consistent cuts. The enhanced stability also contributes to operator safety by reducing the likelihood of tool breakage or malfunction.
Comparing Carbide Saw Tips with Other Materials
To better understand the advantages of carbide saw tips, let’s compare them with other commonly used materials in cutting tools:
Table: Comparison of Saw Tip Materials
Property | Carbide Saw Tips | High-Speed Steel (HSS) | Tool Steel |
---|---|---|---|
Hardness | Extremely high | Moderate | Moderate |
Wear Resistance | Superior | Good | Fair |
Heat Resistance | Excellent | Good | Moderate |
Cutting Efficiency | High | Moderate | Moderate |
Durability | Superior | Good | Moderate |
Cost | Higher initial cost, cost-effective long-term | Lower initial cost, higher replacement frequency | Moderate initial cost, moderate replacement frequency |
Versatility | Highly versatile | Versatile | Less versatile |
Finish Quality | Superior | Good | Fair |
Description: This table highlights the key properties of carbide saw tips in comparison to high-speed steel (HSS) and tool steel. Carbide saw tips outperform other materials in hardness, wear resistance, heat resistance, and overall cutting efficiency, making them the preferred choice for demanding cutting applications.
Applications of Carbide Saw Tips
Carbide saw tips are used across a wide range of industries and applications, offering unparalleled performance and reliability. Here are some key areas where carbide saw tips excel:
1. Woodworking
- Cutting Hardwood and Softwood: Carbide tips provide clean and precise cuts in both hardwood and softwood, making them ideal for fine woodworking and cabinetry.
- Creating Fine Finishes: The sharpness and stability of carbide tips ensure smooth finishes on wood surfaces, enhancing the aesthetic quality of the final product.
2. Metalworking
- Cutting Non-Ferrous Metals: Carbide tips are highly effective in cutting non-ferrous metals like aluminum and copper, providing clean and efficient cuts.
- Machining Hard Metals: The hardness and durability of carbide tips make them suitable for cutting hard metals such as stainless steel, ensuring long tool life and consistent performance.
3. Plastic Cutting
- Shaping Plastic Components: Carbide tips excel in cutting and shaping plastic sheets and components, delivering precise cuts with minimal burring.
- Manufacturing Plastic Products: The versatility of carbide tips allows for efficient cutting of various plastics, enhancing productivity in plastic manufacturing.
4. Construction
- Cutting Concrete and Masonry: The strength and durability of carbide tips make them ideal for cutting through tough construction materials like concrete and masonry.
- Fabrication of Building Components: Carbide tips provide reliable performance in the fabrication of building components, ensuring accuracy and efficiency.
5. Automotive Industry
- Manufacturing Automotive Parts: Carbide tips are used in the production of automotive parts, delivering precise cuts and ensuring high-quality components.
- Cutting Metal and Plastic Parts: The versatility of carbide tips allows for efficient cutting of both metal and plastic parts, meeting the diverse needs of the automotive industry.
6. Aerospace
- Precision Cutting of Aerospace Materials: Carbide tips provide the precision required for cutting aerospace materials, ensuring the quality and reliability of aircraft components.
- Fabrication of Aircraft Components: The durability and wear resistance of carbide tips make them suitable for the demanding conditions of aerospace manufacturing.
Innovations in Carbide Saw Tips
Recent advancements in carbide saw tip technology have further enhanced their performance and versatility. Innovations include:
1. Advanced Coatings
Applying advanced coatings such as titanium nitride (TiN) or diamond-like carbon (DLC) to carbide tips enhances their wear resistance and cutting efficiency. These coatings reduce friction, prevent material adhesion, and provide a protective layer that extends the tool’s lifespan.
2. Customized Geometries
Manufacturers are now able to produce carbide tips with customized geometries tailored to specific cutting conditions and materials. This customization ensures optimized performance and efficiency, meeting the unique needs of various industries.
3. Smart Technologies
The integration of smart technologies, such as IoT-enabled tools, allows real-time monitoring and predictive maintenance of carbide saw tips. These technologies enhance overall tool performance, reduce downtime, and improve productivity.
FAQ
Q1: What makes carbide saw tips more durable than other materials?
A1: Carbide saw tips are made from tungsten carbide, which is exceptionally hard and wear-resistant. This material maintains its sharpness and cutting edge far longer than other materials like high-speed steel or tool steel, resulting in greater durability and extended tool life.
Q2: How do carbide saw tips improve cutting efficiency?
A2: The sharpness and hardness of carbide saw tips allow for smoother and faster cuts, reducing the effort and energy required. This high cutting efficiency is especially beneficial in industrial settings where productivity and precision are crucial.
Q3: Can carbide saw tips be used for cutting hard metals?
A3: Yes, carbide saw tips are highly effective in cutting hard metals such as stainless steel. Their exceptional hardness and wear resistance make them suitable for demanding cutting applications, ensuring consistent performance and longevity.
Q4: Are carbide saw tips more cost-effective in the long run?
A4: Although carbide saw tips have a higher initial cost compared to other materials, their extended tool life and reduced maintenance requirements make them cost-effective over time. The longer lifespan and consistent performance lead to lower overall costs, offering excellent value for money.
Q5: What are the latest innovations in carbide saw tip technology?
A5: Recent innovations in carbide saw tip technology include advanced coatings like titanium nitride (TiN) and diamond-like carbon (DLC) that enhance wear resistance and cutting efficiency. Customized geometries tailored to specific cutting conditions and the integration of smart technologies for real-time monitoring and predictive maintenance are also notable advancements.
Want to buy Carbide Tipped Saw Tips at a good price? Please click here.