Introduction
Definition of Carbide Rods
Carbide rods are a type of cutting tool material used in the manufacturing industry, specifically for end mills. These rods are made from a combination of tungsten carbide and cobalt, which gives them exceptional hardness and durability. The main purpose of carbide rods is to provide a strong and reliable cutting edge for end mills, allowing for efficient and precise machining of various materials. With their high resistance to wear and heat, carbide rods are able to withstand the demanding conditions of heavy-duty machining operations. Overall, carbide rods play a crucial role in enhancing productivity and performance in the field of milling and machining.
Importance of Carbide Rods in End Mills
Carbide rods play a crucial role in the performance and longevity of end mills. These rods are made from a combination of tungsten carbide and cobalt, which gives them exceptional hardness and durability. The use of carbide rods in end mills allows for higher cutting speeds and feeds, resulting in improved machining efficiency. Additionally, the hardness of carbide rods ensures that they can withstand the high temperatures and pressures generated during the milling process. This makes them ideal for applications that involve cutting hard materials like stainless steel, cast iron, and titanium. Overall, the use of carbide rods in end mills is of utmost importance as it directly impacts the quality and precision of the machining process.
Overview of the Article
Carbide rods for end mills play a crucial role in the machining industry. These rods are made from a high-strength and durable material known as carbide, which allows them to withstand the extreme conditions of cutting and milling processes. The article provides an in-depth overview of carbide rods for end mills, discussing their composition, manufacturing process, and various applications. It highlights the advantages of using carbide rods, such as their superior hardness, wear resistance, and heat resistance, which result in improved tool life and machining efficiency. Additionally, the article explores the different types and sizes of carbide rods available, along with their specific uses in different machining operations. Overall, this comprehensive overview serves as a valuable resource for professionals in the machining industry, providing them with essential information on carbide rods for end mills.
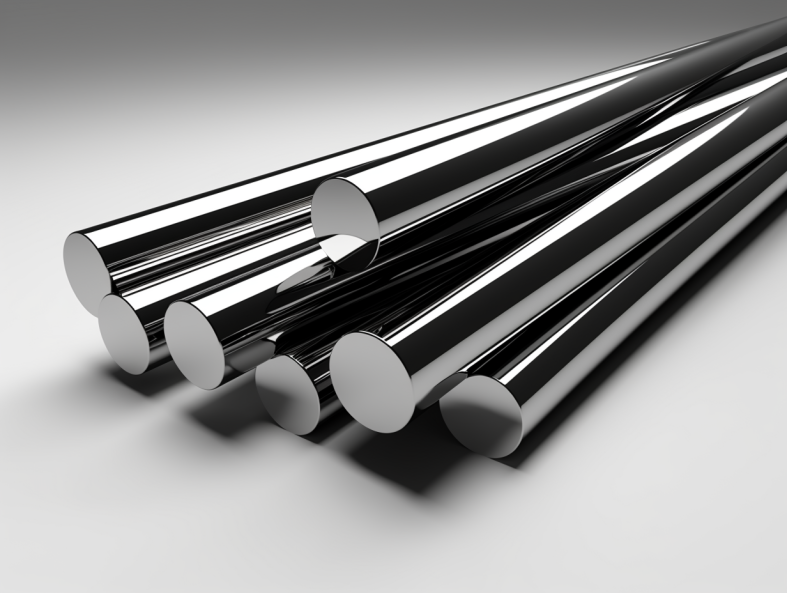
Properties of Carbide Rods
Composition of Carbide Rods
Carbide rods for end mills are an essential component in the manufacturing industry. They are widely used in the production of cutting tools due to their exceptional hardness and wear resistance. The composition of carbide rods typically consists of tungsten carbide particles embedded in a metallic binder, such as cobalt. This combination of materials provides the necessary strength and durability required for high-speed machining operations. Additionally, carbide rods can withstand extreme temperatures and maintain their performance even under challenging conditions. As a result, they enable efficient and precise cutting, contributing to enhanced productivity and quality in various machining applications.
Hardness and Wear Resistance
Carbide rods for end mills are known for their exceptional hardness and wear resistance. This makes them an ideal choice for cutting and milling applications that require high precision and durability. The hardness of carbide rods ensures that they can withstand the extreme forces and heat generated during the cutting process, resulting in longer tool life and reduced downtime. Additionally, their superior wear resistance allows for consistent performance even when working with tough materials such as stainless steel and hardened alloys. Overall, carbide rods for end mills are essential tools for achieving efficient and reliable machining operations.
Heat Resistance and Thermal Conductivity
Carbide rods for end mills are known for their exceptional heat resistance and thermal conductivity. These properties make them ideal for high-speed machining applications where the tool is subjected to intense heat and friction. The heat resistance of carbide rods allows them to maintain their hardness and strength even at elevated temperatures, ensuring long-lasting performance. Additionally, their high thermal conductivity helps to dissipate heat efficiently, preventing the tool from overheating and prolonging its lifespan. With their impressive heat resistance and thermal conductivity, carbide rods for end mills are a reliable choice for demanding machining operations.
Manufacturing Process
Raw Materials for Carbide Rods
Carbide rods for end mills are manufactured using various raw materials. The most common raw material used is tungsten carbide, which is known for its exceptional hardness and wear resistance. Other materials such as cobalt and titanium are also added to enhance the strength and toughness of the carbide rods. These raw materials are carefully selected and blended in precise proportions to achieve the desired properties. The quality of the raw materials plays a crucial role in determining the performance and durability of the carbide rods for end mills.
Powder Metallurgy
Powder metallurgy is a widely used manufacturing process in the production of carbide rods for end mills. This method involves the blending and compaction of fine metal powders, such as tungsten carbide, along with other additives. The powdered mixture is then subjected to high temperatures and pressure, resulting in a solid and dense material. The use of powder metallurgy allows for precise control over the composition and properties of the carbide rods, ensuring high performance and durability. Additionally, this manufacturing technique enables the production of complex shapes and sizes, making it suitable for a wide range of end mill applications.
Sintering and Finishing
Sintering and finishing are crucial processes in the production of carbide rods for end mills. Sintering involves heating the raw materials, typically tungsten carbide powder and a binder, at high temperatures to form a solid mass. This process helps to enhance the strength and hardness of the carbide rods, making them suitable for cutting applications. Finishing, on the other hand, involves grinding, polishing, and coating the carbide rods to achieve the desired surface finish and dimensional accuracy. By carefully controlling these processes, manufacturers can ensure that the carbide rods meet the strict quality standards required for end mills, resulting in high-performance cutting tools that excel in durability and precision.
Types of Carbide Rods
Solid Carbide Rods
Solid carbide rods are essential components in the manufacturing of end mills. These rods are made from high-quality carbide material, which provides exceptional hardness and wear resistance. The use of solid carbide rods ensures the production of end mills that are durable and capable of withstanding high-speed machining operations. Additionally, the carbide material allows for superior cutting performance, resulting in precise and efficient machining processes. Overall, solid carbide rods play a crucial role in the production of high-quality end mills, making them a preferred choice in the metalworking industry.
Tungsten Carbide Rods
Tungsten carbide rods are essential components in the manufacturing of end mills. These rods are made from a combination of tungsten and carbon, resulting in a material that is incredibly strong and durable. The high hardness and wear resistance of tungsten carbide rods make them ideal for cutting and milling applications. They are capable of withstanding high temperatures and can maintain their sharpness for extended periods of time. Tungsten carbide rods provide excellent performance and precision, making them a popular choice in the machining industry.
Cobalt Carbide Rods
Cobalt carbide rods are essential components in the manufacturing of end mills. These rods are made from a combination of cobalt and carbide, resulting in a material that offers superior hardness and durability. The use of cobalt carbide rods in end mills allows for high-speed cutting, increased precision, and extended tool life. With their excellent heat resistance and wear resistance properties, cobalt carbide rods are highly sought after in the machining industry. Whether it’s for milling, drilling, or other cutting applications, cobalt carbide rods are the go-to choice for professionals seeking top-notch performance and reliability.
Applications of Carbide Rods in End Mills
Milling Operations
Milling operations are an essential part of the manufacturing process, especially when it comes to shaping and cutting materials. Carbide rods for end mills play a crucial role in these operations, providing high durability and performance. These rods are made from a combination of tungsten carbide and cobalt, which makes them extremely tough and resistant to wear. With their sharp cutting edges, carbide rods for end mills can efficiently remove material and create precise shapes and contours. Whether it’s milling metal, wood, or plastic, these rods are the go-to choice for achieving excellent results in various milling applications.
Drilling Operations
Drilling operations are an essential part of machining processes, and carbide rods for end mills play a crucial role in achieving precise and efficient drilling. These rods are made from high-quality carbide material, known for its exceptional hardness and durability. With their sharp cutting edges and excellent heat resistance, carbide rods can withstand the high-speed and heavy-duty drilling operations. They provide superior performance, ensuring clean and accurate holes in various materials, including metals, plastics, and composites. Whether it’s drilling holes for industrial applications or creating precision holes in woodworking projects, carbide rods for end mills are the go-to choice for professionals seeking reliable and consistent drilling results.
Reaming Operations
Reaming operations are an essential part of the machining process when it comes to creating precise and accurate holes. Carbide rods for end mills play a crucial role in these operations. These rods are known for their exceptional hardness and durability, making them ideal for reaming tasks. With their superior cutting performance, carbide rods ensure smooth and efficient hole enlargement, resulting in precise dimensions and surface finishes. Whether it’s in the automotive, aerospace, or manufacturing industry, using carbide rods for end mills in reaming operations guarantees high-quality and reliable results.
Advantages and Limitations
Advantages of Carbide Rods
Carbide rods for end mills offer several advantages over other types of materials. Firstly, carbide rods have exceptional hardness and wear resistance, making them ideal for cutting and milling applications. They can withstand high temperatures and maintain their cutting edge for longer periods, resulting in improved productivity and reduced downtime. Additionally, carbide rods provide excellent dimensional stability, ensuring consistent and precise machining results. Moreover, they have a higher strength-to-weight ratio compared to steel, allowing for faster cutting speeds and higher feed rates. Overall, the use of carbide rods in end mills enhances performance, durability, and efficiency in various machining operations.
Limitations of Carbide Rods
Carbide rods are widely used in the manufacturing of end mills due to their exceptional hardness and wear resistance. However, like any material, carbide rods have certain limitations that need to be considered. One limitation is their brittleness, which makes them prone to chipping or breaking under excessive force or impact. Another limitation is their high cost compared to other materials, which can make them less economical for certain applications. Additionally, carbide rods require special handling and machining techniques due to their hardness, which may increase production time and costs. Despite these limitations, carbide rods remain a popular choice for end mills due to their superior performance and durability in cutting and milling operations.
Comparison with Other Materials
Carbide rods for end mills offer several advantages when compared to other materials. Firstly, carbide rods have a higher hardness and wear resistance, allowing them to withstand the high-speed and high-temperature conditions during milling operations. This results in longer tool life and improved machining accuracy. Additionally, carbide rods have excellent heat resistance, reducing the risk of tool deformation and ensuring consistent performance. Moreover, carbide rods have a higher strength-to-weight ratio, making them ideal for applications that require precision and efficiency. Overall, the use of carbide rods for end mills provides a significant advantage in terms of performance, durability, and cost-effectiveness.