Requirements of High-Speed Cutting Tools
Have you ever wondered what makes a cutting tool capable of slicing through metal at lightning speeds without wearing out too quickly? It turns out, it takes more than just a sharp edge. High-speed cutting tools must meet some pretty demanding criteria.
First and foremost, these tools need exceptional hardness to withstand the forces involved in high-speed machining. When metal meets metal at high velocity, there’s heat, there’s friction, and there’s wear. If your tool can’t handle that, it’s game over.
Next, they need thermal stability. That means the material needs to maintain its hardness even at temperatures soaring past 800°C. Imagine trying to cut steel while your tool is literally glowing red-hot!
Add in toughness to resist chipping or cracking, resistance to chemical wear (from lubricants and workpiece materials), and precision machinability to make sure the tools can be manufactured to tight tolerances. You now see the high bar that cutting tool materials need to clear.
So where does carbide fit into this demanding lineup? Let’s find out.
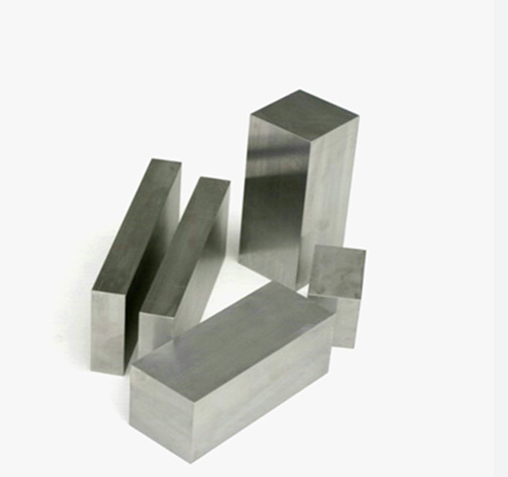
Why Carbide Rods Are Ideal for High-Speed Cutting Tools
Let’s talk about the real MVP here: carbide rods. If high-speed cutting were an Olympic sport, carbide rods would be the gold medalist, every time. But why exactly are they such top performers?
At their core (literally), carbide rods are made from tungsten carbide (WC) powder combined with a metallic binder like cobalt. This combo gives them a killer mix of hardness and toughness. Think of it like Wolverine’s claws – almost unbreakable, incredibly sharp, and ready for a fight.
Carbide rods offer:
- Superb hardness and wear resistance: Perfect for cutting hard metals like stainless steel, titanium, and high-nickel alloys.
- Thermal stability: They don’t lose their edge even when temperatures hit 1000°C.
- Dimensional accuracy: Thanks to precise sintering and grinding processes, you get consistency in every tool made.
- Shock resistance: Not as brittle as ceramics, but still hard enough to last way longer than HSS (High-Speed Steel).
And here’s the kicker: Carbide tools made from high-grade rods often last 3-10 times longer than tools made from traditional materials.
Comparison with Other Materials: Carbide vs HSS, Ceramics, and Cermets
Now let’s put carbide rods up against the competition. You know, for science.
Material | Hardness (HV) | Thermal Resistance | Toughness | Tool Life | Cost | Common Use |
---|---|---|---|---|---|---|
Carbide Rods | 1600-2000 | Up to 1000°C | Medium | High | $$$ | Milling, turning, drilling |
HSS | 600-900 | Up to 600°C | High | Medium | $ | General machining, hobby use |
Ceramics | 2000+ | Up to 1200°C | Low | Very High | $$$$ | High-speed finishing of cast iron |
Cermets | 1400-1600 | Up to 800°C | Medium | Medium-High | $$ | Finishing operations |
So yeah, carbide hits that sweet spot: hard enough to cut, tough enough to last, and stable enough under heat. It’s no wonder it’s become the industry standard.
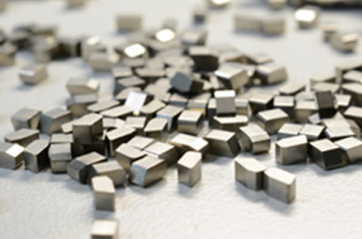
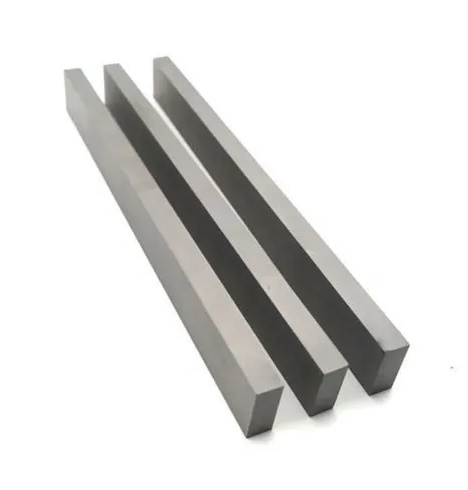
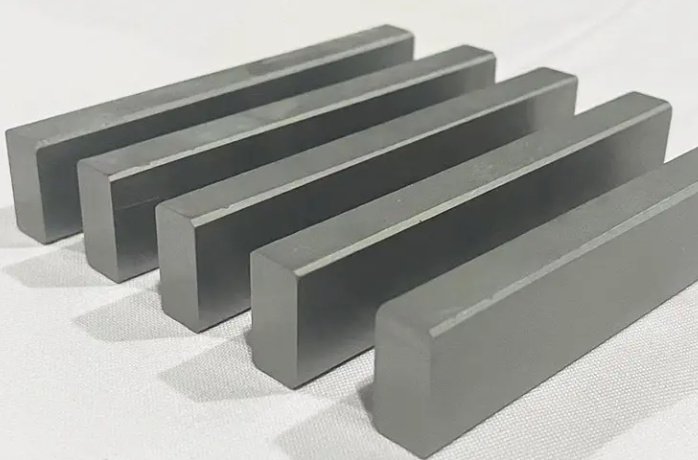
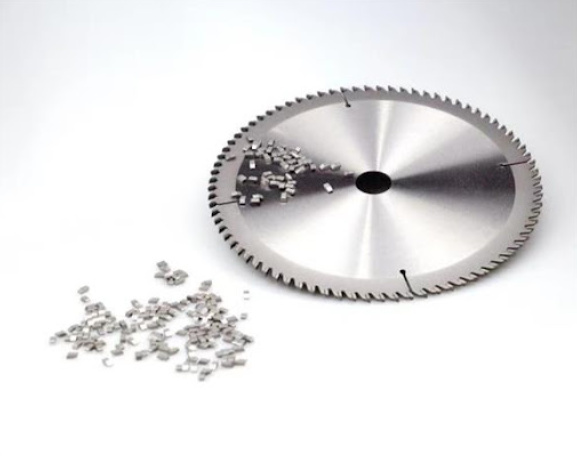
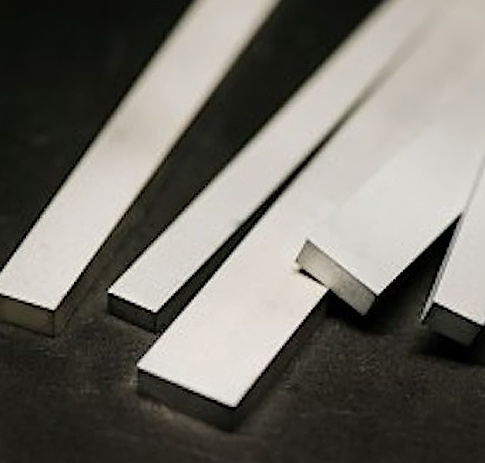

Common Applications of Carbide Rods in Industrial Tooling
The beauty of carbide rods is how versatile they are. Here’s a quick breakdown of where they shine:
Application | Examples of Tools Made | Advantages in Use |
---|---|---|
CNC Machining | End mills, drills, reamers | Long life, high accuracy |
Aerospace Manufacturing | Milling cutters, boring bars | Withstands heat and cuts tough alloys |
Automotive Industry | Forming tools, punches | High-speed steel cutting, repeatability |
Mold and Die Making | Micro tools, engraving bits | Precision detail, surface finish |
Woodworking & Composites | Router bits, saw blades | Edge retention, smoother finishes |
Carbide rods are like the Swiss Army knife of the cutting tool world – they’ve got a tool for every job.
Specific Metal Powder Models Used in Carbide Rods
When we talk carbide, we’re really talking about powders – tiny grains that get pressed and sintered into the rods. And not all powders are created equal. Here are 10+ specific models used in industry:
Powder Model | Composition & Characteristics |
---|---|
WC-Co (K20) | Fine-grain tungsten carbide with 10% cobalt; general-purpose with high hardness |
WC-Co (K30) | Medium grain with 12% cobalt; increased toughness for interrupted cutting |
WC-Co (K10) | Ultra-fine grain, 6% cobalt; extremely hard, ideal for finishing |
WC-Ni | Nickel-bonded carbide; used in corrosion-resistant applications |
WC-TiC-Co | Titanium carbide addition for higher heat resistance and wear protection |
WC-TaC-Co | Tantalum carbide added for better red hardness |
WC-Co-Cr | Chromium-modified for high oxidation resistance |
Submicron WC-Co | Extremely fine particles (<0.5 µm); ideal for micro-tools and precision applications |
Ultrafine WC-Co | 0.2 µm grains; allows super sharp edges and high surface finishes |
WC-Co-Vc | Vanadium-carbide doped; enhances wear resistance at high speeds |
WC-Co-ZrC | Zirconium-carbide doped; increased corrosion resistance and thermal shock resistance |
Each of these powder types tailors the carbide rod to a specific task. You wouldn’t wear hiking boots to run a marathon, right? Same logic here.
Tips for Choosing Quality Carbide Rods
Alright, so you know carbide rods are the real deal. But how do you pick the good ones from the junk? Here are a few insider tips:
- Check grain size: Finer grain = sharper tool and better wear resistance. Submicron and ultrafine powders rock for this.
- Binder content matters: More cobalt = more toughness, but less hardness. Match this to your application.
- Look for reputable brands: Names like Sandvik, Kennametal, and Sumitomo have tight QC processes.
- Ask for sintering data: Density and porosity metrics can tell you a lot about rod quality.
- Test samples when possible: Field testing beats spec sheets every time.
- Check for ISO grades: Grades like ISO K, M, P give you a quick idea if a rod suits steel, stainless, or cast iron.
Investing in high-quality rods might cost more upfront, but trust me – it pays off in fewer tool changes, less downtime, and better parts.
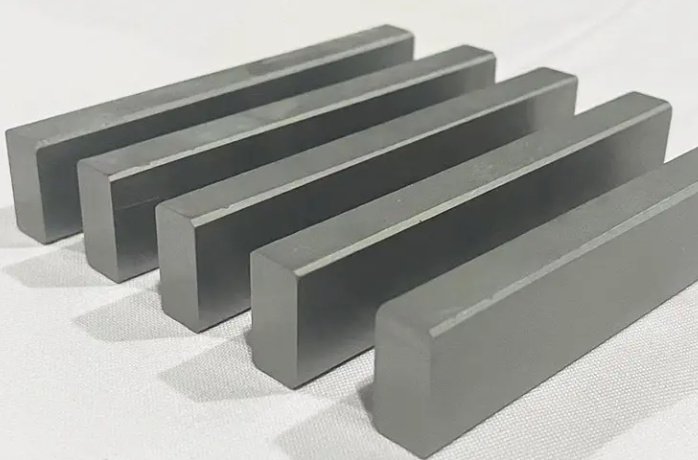
FAQs
Question | Answer |
---|---|
Why are carbide rods better than HSS for high-speed machining? | Carbide stays harder at high temps, cuts faster, and lasts longer – even if it costs more initially. |
Can carbide rods be resharpened? | Yes, with diamond grinding. But it’s tricky and requires precision equipment. |
Are all carbide rods the same? | Nope. Grain size, binder content, and additives vary widely. Choose based on your job needs. |
How do I know which ISO grade to use? | ISO P = steel, M = stainless, K = cast iron. Match the material to the grade for best performance. |
What’s the difference between ultrafine and submicron carbide? | Ultrafine is even smaller grain size than submicron, allowing sharper edges and better surface finish. |
Do carbide rods work well in CNC applications? | Absolutely. They offer precision, rigidity, and tool longevity – perfect for CNC environments. |
Are there environmental concerns with carbide tools? | Used tools can be recycled, and many manufacturers reclaim the cobalt and tungsten for reuse. |
Can I use carbide rods in DIY or hobby projects? | You can, but they require proper handling and sharpening equipment. Better suited for pro shops. |
How are carbide rods made? | Through powder metallurgy: mix powders, press into shape, then sinter at high temps. |
Which brands make the best carbide rods? | Sandvik, Ceratizit, Kennametal, Mitsubishi Materials, and Sumitomo lead the pack. |