The Use of Carbide Rods
Carbide rods are the backbone of precision machining and manufacturing. Used in everything from cutting tools to industrial machinery, these high-performance materials offer unmatched hardness, wear resistance, and heat endurance. But why does quality matter? Think of it like this: if carbide rods were the tires of a race car, using substandard ones would be like trying to win a Formula 1 race on cheap, worn-out tires. Not a great idea, right? That’s why ensuring carbide rods meet top-notch quality standards is crucial.
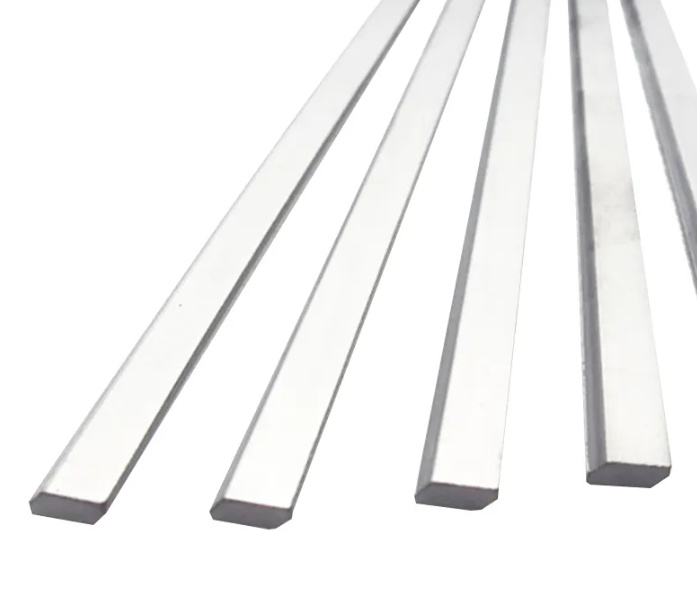
What Are Carbide Rods?
Carbide rods are solid cylindrical bars made from tungsten carbide powder, typically bound with cobalt or other metals. These rods are sintered at extremely high temperatures to form a dense, super-hard material used in metal cutting tools, drills, end mills, and wear-resistant applications. Their durability makes them ideal for demanding industries such as aerospace, automotive, and medical equipment manufacturing.
Key Benefits of Carbide Rods:
- Extreme Hardness – Much harder than steel, making them last longer in cutting applications.
- High Wear Resistance – Ideal for machining tough materials.
- Heat Resistance – Can endure extreme temperatures without losing performance.
- Precision Manufacturing – Ensures accuracy in cutting and drilling applications.
Key Quality Standards for Carbide Rods
When choosing carbide rods, it’s essential to ensure they meet international quality standards. These standards define the mechanical properties, composition, and performance expectations, guaranteeing consistency and reliability.
Major Quality Standards:
- ISO 513 & ISO 9001 – International standards for cutting materials and general quality management.
- ASTM B777 – Specifies the density and hardness requirements for tungsten-based materials.
- GB/T 18376.1-2001 – Chinese standard for evaluating carbide materials.
- DIN ISO 513 – German standard covering various carbide compositions.
- JIS B4053 – Japanese standard for carbide tool materials.
Factors That Determine Carbide Rod Quality
Factor | Description |
---|---|
Tungsten Purity | Higher purity ensures better hardness and strength. |
Grain Size | Finer grains improve toughness and wear resistance. |
Cobalt Binder | Affects the toughness and hardness balance. |
Sintering Process | Advanced sintering leads to a more uniform structure. |
Surface Finish | Affects performance in machining applications. |
Tolerance Standards | Precision in diameter and straightness for better accuracy. |
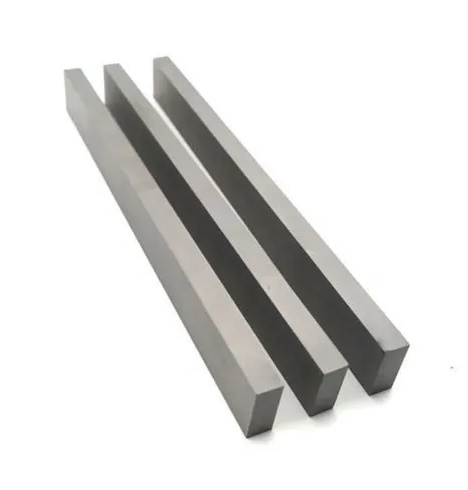
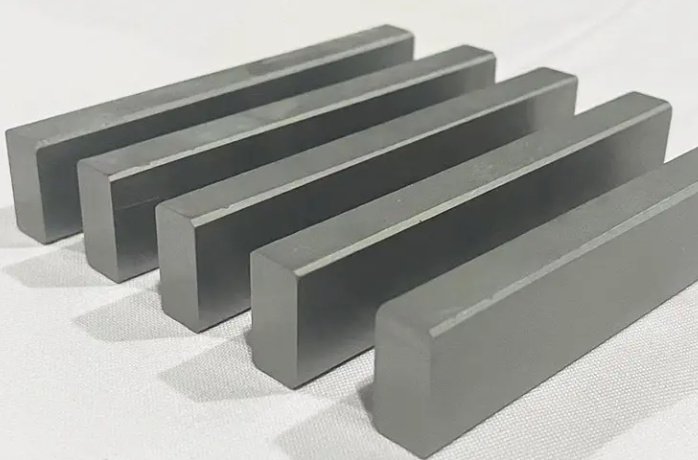
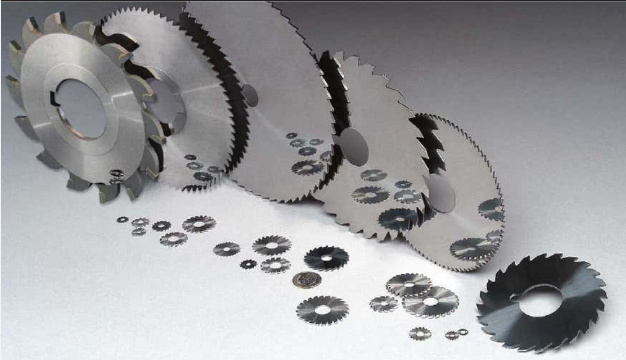
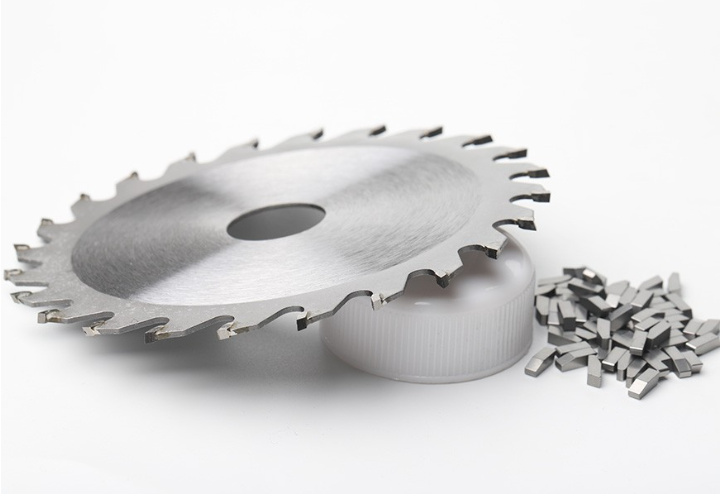
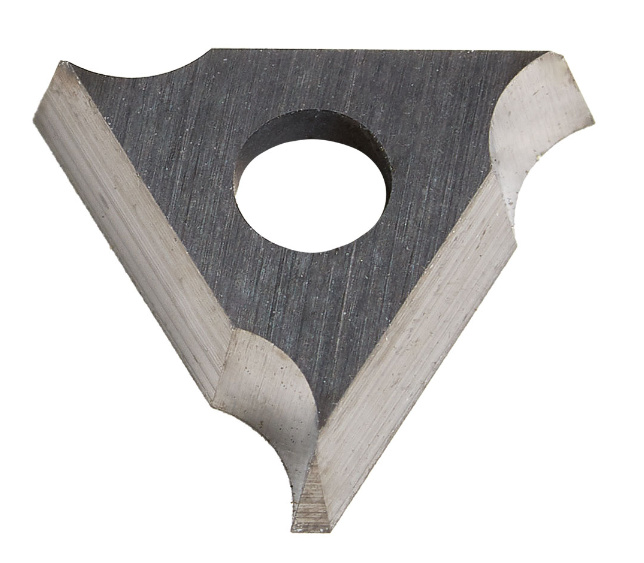
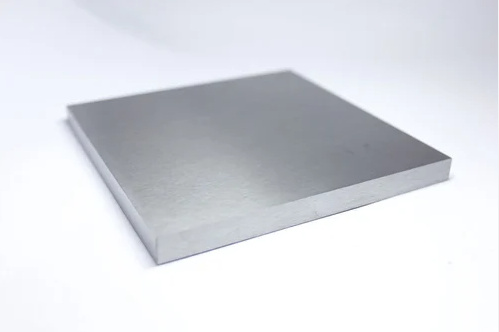
How to Choose High-Quality Carbide Rods?
So, how do you pick the best carbide rods? It’s like choosing a top-tier chef’s knife—material quality, craftsmanship, and durability matter. Here’s what to look for:
- Check the Grain Structure: Finer grains mean stronger rods. Opt for ultrafine or submicron grain carbide rods for precision cutting.
- Look at the Cobalt Content: More cobalt increases toughness, but too much can reduce wear resistance.
- Verify the Sintering Process: High-quality sintering ensures even hardness and fewer defects.
- Surface Inspection: Choose rods with a polished or ground finish for enhanced performance.
- Manufacturer Reputation: Stick with trusted brands that meet international standards.
Common Defects and How to Avoid Them
Even the best materials can have flaws. Here are some common defects and how to avoid them:
Defect | Cause | Prevention |
---|---|---|
Porosity | Poor sintering process | Choose high-quality sintered rods |
Cracks | High internal stress or cooling issues | Ensure uniform heat treatment |
Uneven Hardness | Inconsistent material composition | Verify with quality certifications |
Chipping | Improper handling or weak grain structure | Opt for fine-grain carbide rods |
Top Carbide Rod Manufacturers and Certifications
Manufacturer | Certifications |
---|---|
Sandvik | ISO 9001, ISO 14001 |
Kennametal | ASTM B777, ISO 9001 |
Zhuzhou Cemented Carbide | GB/T 18376.1-2001, ISO 9001 |
Ceratizit | DIN ISO 513, ISO 9001 |
Sumitomo Electric | JIS B4053, ISO 9001 |
Guhring | ISO 513, DIN ISO 9001 |
ISCAR | ISO 9001, ISO 14001 |
Hyperion Materials | ASTM B777, ISO 9001 |
Mitsubishi Materials | JIS B4053, ISO 9001 |
Seco Tools | ISO 513, ISO 9001 |
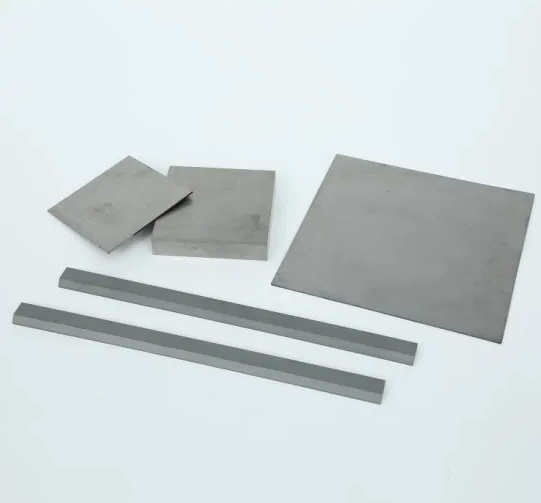
FAQ
Question | Answer |
---|---|
What is the best carbide rod for machining? | Submicron grain carbide rods offer the best precision and wear resistance. |
How do I test carbide rod quality? | Check hardness, grain size, and surface finish. Look for industry certifications. |
Why do carbide rods break? | Poor sintering, excessive internal stress, or improper use can lead to breakage. |
What is the difference between tungsten carbide and solid carbide? | Solid carbide is 100% carbide, while tungsten carbide is usually mixed with a binder like cobalt. |
How long do carbide rods last? | Longevity depends on usage, but high-quality rods can last significantly longer than lower-grade alternatives. |