What is Abrasion Resistance in Carbide Rods?
Carbide rods, primarily composed of tungsten carbide (WC) and a metallic binder like cobalt (Co), are widely used in cutting tools, drills, and wear-resistant components. The higher the abrasion resistance, the longer the tool lasts, reducing downtime and replacement costs.

Factors Affecting the Abrasion Resistance of Carbide Rods
Several factors influence how well a carbide rod resists abrasion. Let’s break them down:
1. Composition of the Carbide Rod
- The ratio of tungsten carbide (WC) to cobalt (Co) affects hardness and wear resistance.
- Higher WC content increases hardness, making it more resistant to abrasion but potentially more brittle.
- More cobalt enhances toughness but slightly reduces abrasion resistance.
2. Grain Size of Tungsten Carbide
- Fine-grain carbide offers superior wear resistance compared to coarse-grain variants.
- Ultrafine and nano-grain carbides provide maximum hardness for high-precision applications.
3. Metal Powder Models Used
- Various metal powders contribute to the final product’s properties. Here are some specific models:
- H10F – High hardness, ideal for dry cutting tools.
- H20F – Balanced hardness and toughness for multi-purpose cutting.
- K44 – Extremely wear-resistant, perfect for high-speed machining.
- MG18 – High cobalt content for shock-resistant tools.
- YF06 – Nano-grain structure for ultra-hard coatings.
- WC-12Co – High thermal stability, used in aerospace applications.
- F15 – Used in high-pressure, high-speed cutting.
- M42 – Known for outstanding heat resistance.
- G25 – Exceptional for carbide-tipped saw blades.
- ZC45 – Ideal for extreme wear environments.
4. Manufacturing Process & Sintering Conditions
- High-pressure sintering improves density and reduces porosity, enhancing abrasion resistance.
- Uniform carbide distribution prevents weak points in the material.
5. Coatings & Surface Treatments
- PVD (Physical Vapor Deposition) and CVD (Chemical Vapor Deposition) coatings improve wear resistance.
- TiAlN (Titanium Aluminum Nitride) and TiCN (Titanium Carbonitride) provide additional protection against extreme conditions.
How to Improve the Abrasion Resistance of Carbide Rods?
Looking to maximize the longevity of carbide rods? Here are some proven strategies:
1. Use Advanced Carbide Blends
- Opt for ultrafine-grain carbides to achieve higher hardness without brittleness.
- Custom-blended carbide compositions tailor performance to specific applications.
2. Optimize Cobalt Content
- Adjusting cobalt content balances toughness and wear resistance.
- Typically, 6-12% cobalt is used depending on the application.
3. Apply High-Performance Coatings
- Diamond-like coatings (DLC) significantly reduce friction and wear.
- TiN, TiCN, and AlTiN coatings enhance resistance to high temperatures.
4. Improve Manufacturing Techniques
- Hot Isostatic Pressing (HIP) ensures uniform carbide distribution.
- Cryogenic treatment enhances wear resistance by refining grain structures.
5. Proper Application & Maintenance
- Using carbide rods within their designed speed and feed rates prevents premature wear.
- Regular lubrication and cooling can prolong their lifespan significantly.
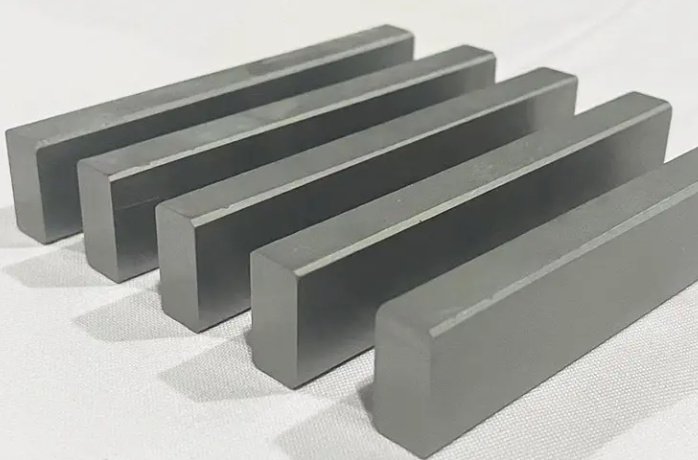
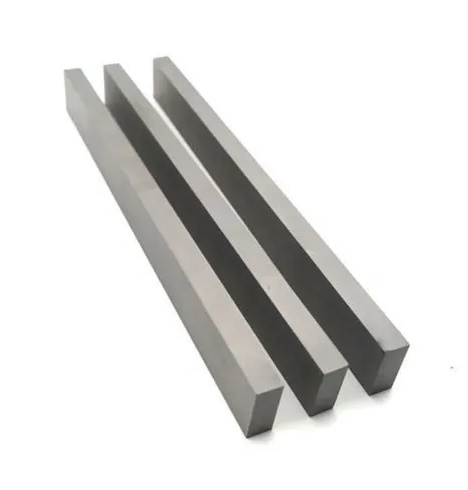
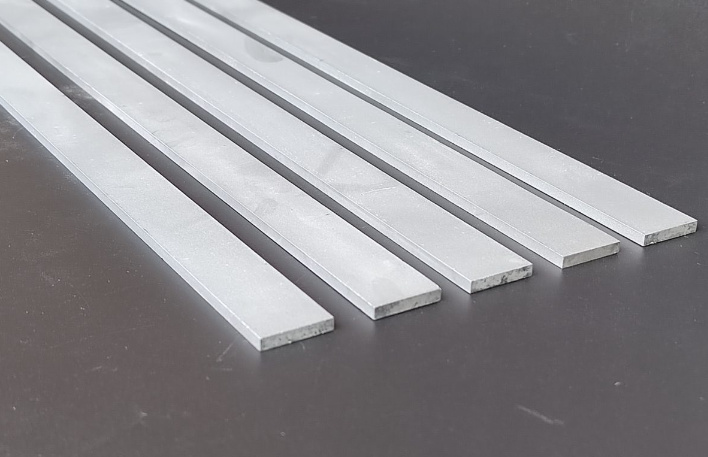
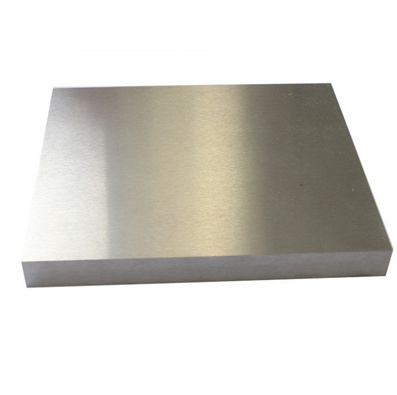
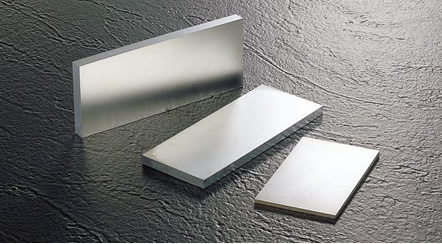
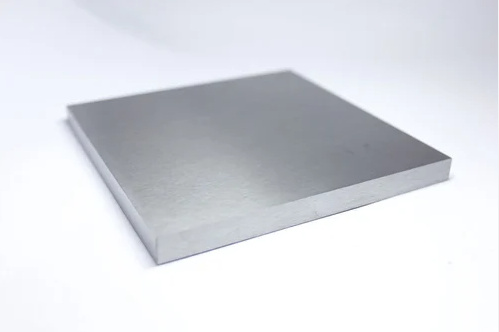
Applications of High Abrasion Resistance Carbide Rods
Industry | Application | Key Benefit |
---|---|---|
Aerospace | Jet engine components, turbine blades | Heat & wear resistance |
Automotive | Engine parts, fuel injector nozzles | Precision machining |
Mining | Drill bits, cutting tools | Extreme durability |
Metalworking | Lathe tools, milling cutters | High-speed performance |
Oil & Gas | Downhole drilling tools | Resistance to harsh conditions |
Medical | Surgical tools, orthopedic implants | Biocompatibility & precision |
Woodworking | Saw blades, router bits | Longer tool life |
Choosing the Right Carbide Rod for Your Needs
Not all carbide rods are created equal. Selecting the right one depends on:
- Application requirements: Do you need extreme hardness or a balance of toughness and wear resistance?
- Cutting environment: Will your tool be exposed to high temperatures or aggressive materials?
- Budget: While high-performance carbides offer better longevity, they come at a higher cost.
- Brand reputation: Trusted manufacturers like Sandvik, Kennametal, and Ceratizit produce high-quality carbide rods.
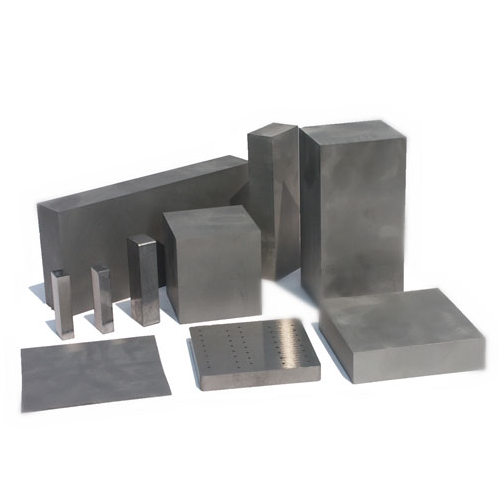
FAQ
Question | Answer |
---|---|
What is the best carbide rod for extreme wear conditions? | K44 and WC-12Co are excellent choices for highly abrasive environments. |
Does grain size affect carbide rod performance? | Yes! Smaller grain sizes enhance hardness and wear resistance. |
Are coated carbide rods better than uncoated ones? | Generally, yes! Coatings like TiAlN and DLC significantly improve wear resistance. |
How can I extend the life of my carbide rods? | Use proper speeds, apply lubrication, and avoid excessive force. |
What’s the best metal powder blend for carbide rods? | H10F, YF06, and MG18 are popular choices for different applications. |