When it comes to sourcing carbide rods, picking the right supplier is a game-changer. The right supplier ensures quality, consistency, and compatibility with your specific requirements. But how do you navigate this complex market? Let’s dive deep into the world of carbide rod suppliers and uncover all you need to know.
Why Choosing the Right Carbide Rod Supplier Matters
Imagine crafting precision tools or working on high-stakes industrial applications. A subpar carbide rod could ruin everything—from your production process to your reputation. The supplier you choose plays a pivotal role in determining whether you’re working with the finest tungsten carbide or struggling with inferior quality.
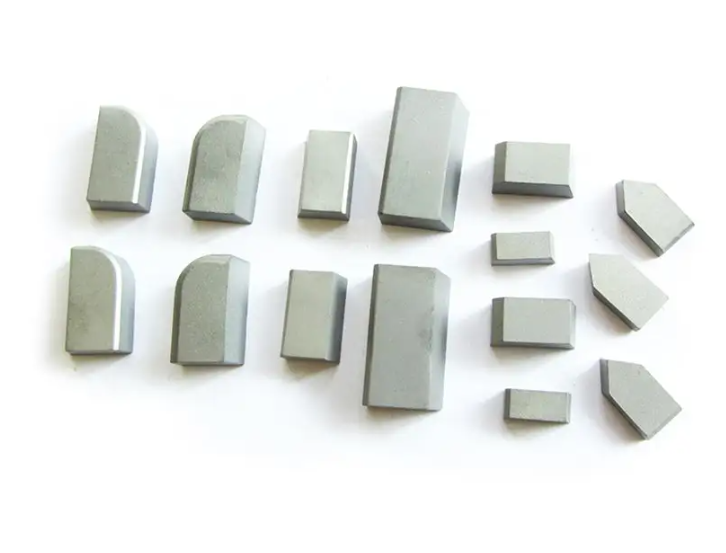
Key Factors in Choosing a Carbide Rod Supplier
Factor | Description |
---|---|
Raw Material Quality | Look for suppliers offering premium-grade tungsten and cobalt powders for consistent rod performance. |
Manufacturing Process | Suppliers using advanced sintering and extrusion processes typically deliver higher quality rods. |
Customization Options | Can the supplier meet specific sizes, tolerances, and finishes for your needs? |
Industry Standards | Ensure the supplier adheres to ISO or other international quality standards for reliability. |
Delivery & Logistics | A reliable supplier should ensure timely delivery and offer flexible shipping options to minimize downtime. |
Customer Support | Does the supplier offer technical assistance and post-purchase support? A strong support system adds tremendous value. |
Pricing Transparency | Avoid hidden fees; transparent pricing ensures you understand what you’re paying for. |
Raw Materials and Composition Analysis
Carbide rods are primarily composed of tungsten carbide (WC) and cobalt (Co). The ratio of these components significantly influences the rod’s performance. Let’s break it down:
Component | Role |
---|---|
Tungsten Carbide | Provides hardness, wear resistance, and durability. Typically forms 85-95% of the rod composition. |
Cobalt | Acts as a binder, lending toughness and ductility. |
Other Additives | Nickel, chromium, or tantalum may be added for specific properties like corrosion resistance or enhanced strength. |
Production Process Flow of Carbide Rods
Understanding the production process can help you evaluate a supplier’s capabilities. Here’s a simplified flow:
- Powder Preparation: Mixing tungsten carbide and cobalt powders to precise ratios.
- Compaction: Pressing the mixed powder into rod-shaped molds under high pressure.
- Pre-Sintering: Heating the compacted rods to remove binders and improve green strength.
- Sintering: Applying extreme heat (up to 1,500°C) to fuse the material and achieve desired hardness and density.
- Finishing: Grinding, polishing, or coating for final specifications.
- Quality Control: Inspecting for dimensional accuracy, hardness, and surface finish.
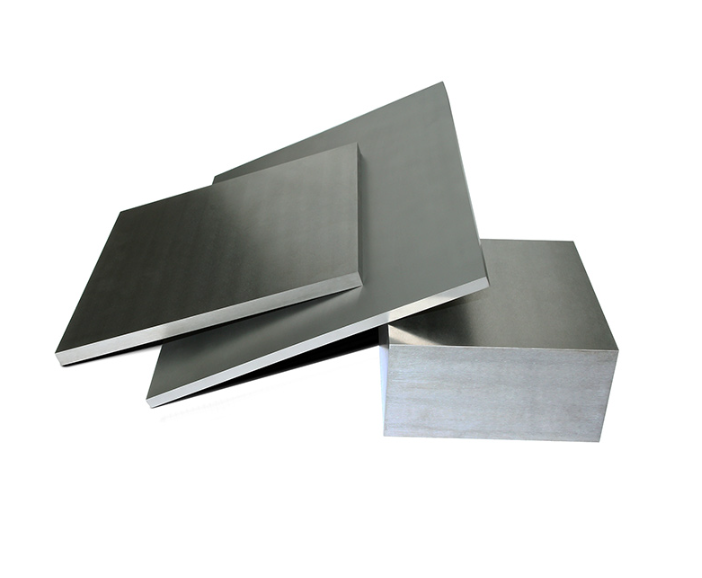
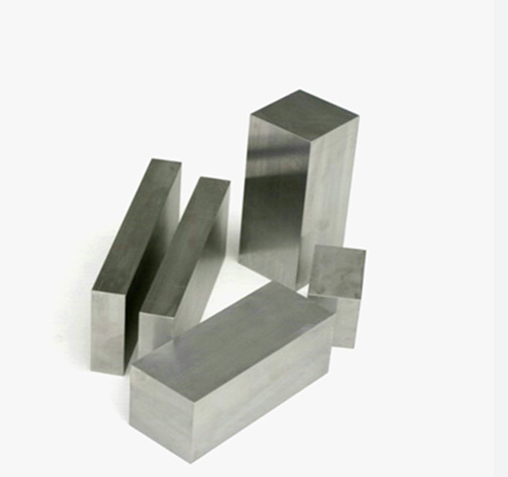
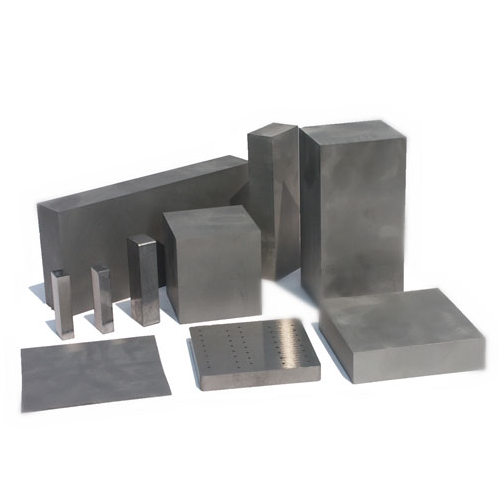
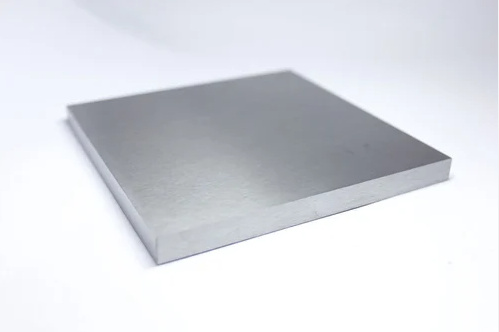
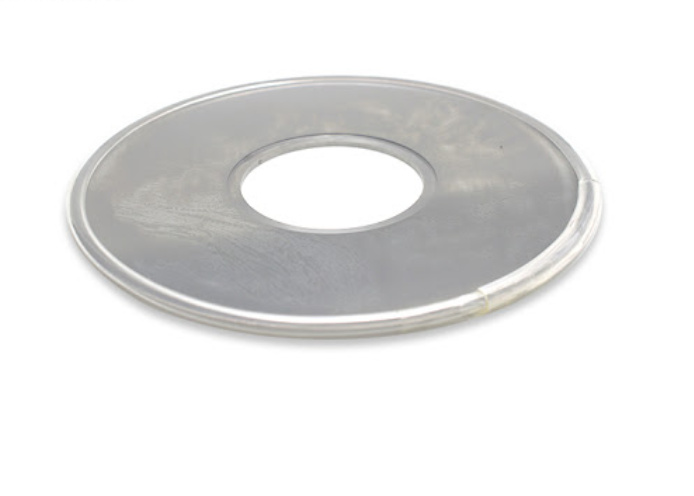
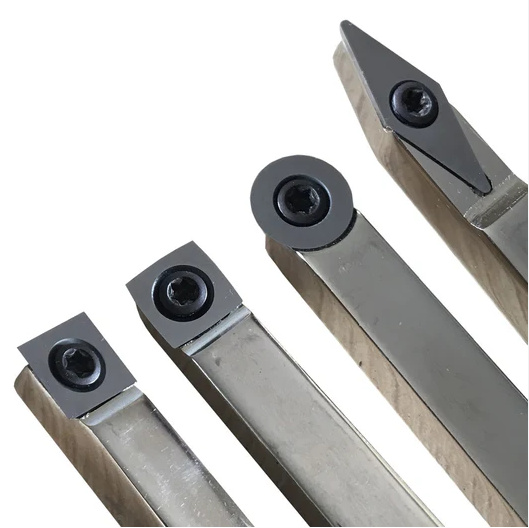
Applications of Carbide Rods
Application | Description |
---|---|
Cutting Tools | Used in drills, end mills, and lathe tools for precision machining of hard materials. |
Wear Parts | Ideal for components in industries where abrasion resistance is critical, such as mining and oil drilling. |
Metal Forming | Used in dies and punches for shaping metals under high pressure. |
Aerospace and Defense | Essential for manufacturing durable and heat-resistant parts. |
Automotive Industry | Commonly employed in producing engine parts and other high-performance components. |
Material Properties of Carbide Rods
Property | Range | Impact |
---|---|---|
Hardness (HRA) | 89-93 | Determines wear resistance and suitability for cutting applications. |
Transverse Strength | 2500-3500 N/mm² | Measures resistance to bending forces; higher values are ideal for heavy-duty tools. |
Density | 14.0-15.0 g/cm³ | Indicates material compactness; affects weight and strength. |
Thermal Conductivity | 50-100 W/m·K | Essential for applications requiring heat dissipation. |
Specifications, Sizes, Shapes, and Standards
Carbide rods come in various forms tailored to different applications. Here’s a snapshot:
Specification | Details |
---|---|
Sizes | Diameters range from 3mm to 30mm; lengths up to 330mm. |
Shapes | Round, square, or customized profiles. |
Standards | ISO 9001, DIN 6535, and other international benchmarks ensure compatibility and reliability. |
Choosing Carbide Rod Supplier: Pricing Details
Supplier | Pricing Range (per kg) | Value-Added Services |
---|---|---|
Supplier A | $50-$70 | Offers customization, fast delivery, and technical support. |
Supplier B | $45-$65 | Focuses on bulk orders with attractive discounts. |
Supplier C | $55-$80 | High precision rods with stringent quality control. |
Hardness, Strength, and Wear Resistance
Model | Hardness (HRA) | Strength (N/mm²) | Wear Resistance |
---|---|---|---|
WC-92/Co-8 | 92 | 3000 | High; suitable for cutting tools and wear parts. |
WC-88/Co-12 | 88 | 3500 | Excellent; ideal for heavy-duty applications. |
WC-94/Co-6 | 94 | 2800 | Superior hardness for high-speed machining. |
Advantages and Limitations of Carbide Rods
Aspect | Advantages | Limitations |
---|---|---|
Durability | Long-lasting performance even under extreme conditions. | High initial cost compared to steel. |
Precision | Offers unmatched accuracy for machining tasks. | Requires specialized equipment for shaping and grinding. |
Versatility | Compatible with a wide range of applications, from tools to wear parts. | May not be suitable for extremely lightweight applications. |
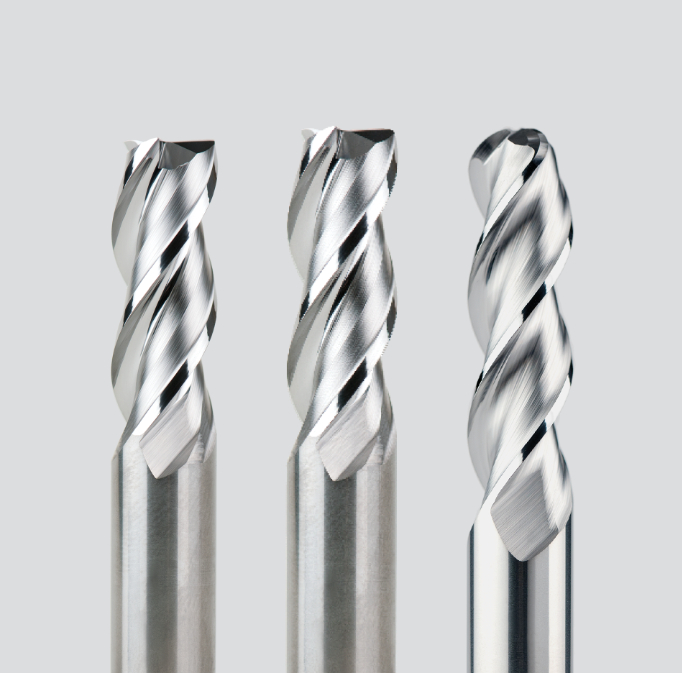
How to Select the Right Carbide Rod Supplier
Step | What to Do |
---|---|
Identify Requirements | Determine the grades, sizes, and finishes you need. |
Research Suppliers | Look for reviews, certifications, and past client testimonials. |
Request Samples | Test product quality before committing to large orders. |
Evaluate Pricing | Compare costs, ensuring no hidden charges. |
Assess Support | Check for technical assistance, customization, and post-sales services. |
FAQ
Question | Answer |
---|---|
What is the typical lifespan of carbide rods? | Depending on use, they can last several years in cutting or wear applications. |
Are all carbide rods the same? | No, differences in composition, size, and finishing make some more suited for specific tasks. |
How do I test carbide rod quality? | Hardness tests, surface inspections, and trial runs in your application are effective methods. |
Why are carbide rods expensive? | Their durability, precision, and resistance to wear justify the higher upfront cost. |
Choosing the right carbide rod supplier doesn’t have to be daunting. With the information in this guide, you’re well-equipped to make an informed decision. Remember: quality and reliability should always take precedence over cost alone!