Overview: Understanding Carbide Rods
Carbide rods, a critical material in various industrial applications, are known for their exceptional hardness, strength, and wear resistance. Made from tungsten carbide powder and cobalt, these rods are used primarily in the manufacturing of cutting tools, drilling equipment, and wear-resistant parts. The combination of tungsten carbide’s toughness and cobalt’s binding properties makes these rods an essential material in high-stress environments.
So, why are carbide rods so important? Well, think about it: in industries where precision and durability are key, the choice of material can make or break the efficiency of operations. Whether you’re involved in metalworking, mining, or even the aerospace sector, understanding the different types and applications of carbide rods can give you a significant edge.
Types of Carbide Rods
Carbide rods come in various forms, each tailored to specific applications. Here’s a look at some common types:
Type | Description | Common Applications |
---|---|---|
Solid Carbide Rods | Entirely made of tungsten carbide, offering superior rigidity and wear resistance. | Precision cutting tools, end mills, reamers. |
Single Hole Rods | Feature a central hole, reducing weight and improving chip evacuation. | Drills, step drills, and punch tools. |
Double Hole Rods | Have two central holes, offering improved cooling and chip flow. | Specialized drilling tools, advanced cutting tools. |
Blanks | Unshaped rods used as starting material for custom tool manufacturing. | Tool grinding, custom cutting tool production. |
Precision Ground Rods | Rods that have been ground to precise tolerances for high-accuracy applications. | High-precision cutting, finishing tools. |
Unground Rods | These are basic rods that have not been ground, allowing for further customization. | Machining, custom tool creation. |
Specialty Coated Rods | Coated with materials like titanium nitride (TiN) for enhanced performance. | High-wear environments, high-speed cutting. |
Straight Rods | Basic, straight cylindrical rods used in various machining operations. | General machining, tool holders. |
Tapered Rods | Feature a tapered design for specific applications. | Custom machining tasks, specialized cutting tools. |
Spiral Coolant Hole Rods | Have spiral holes for improved coolant flow, enhancing tool life and performance. | High-speed drilling, advanced machining processes. |
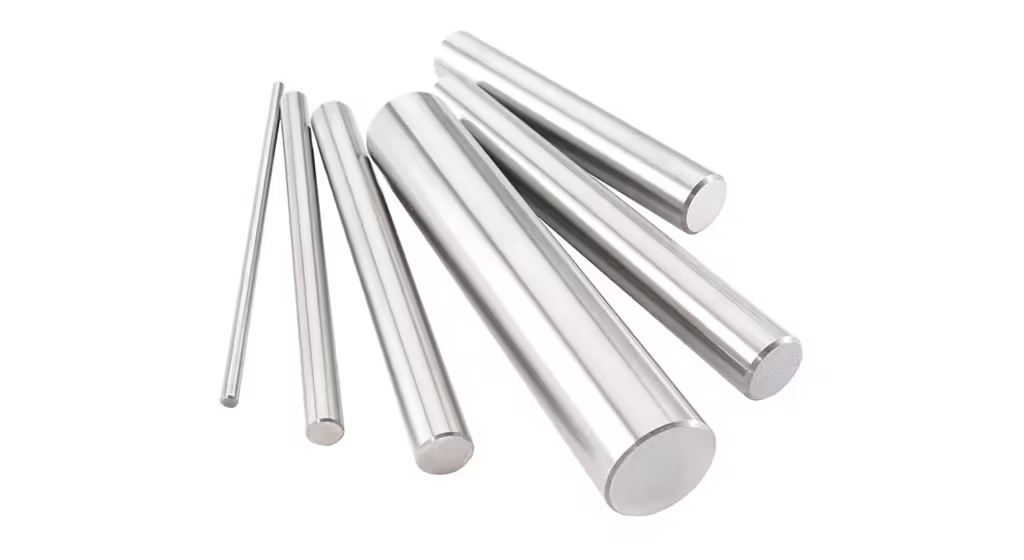
Applications of Carbide Rods
Carbide rods are versatile and find applications across a wide range of industries. Below is a breakdown of where these rods shine:
Industry | Application | Advantages |
---|---|---|
Metalworking | Used in cutting tools like end mills, drills, and reamers. | Offers excellent wear resistance, leading to longer tool life. |
Automotive | Essential in the production of precision components and engine parts. | Provides high accuracy and durability, critical in high-performance applications. |
Mining | Utilized in drill bits and other mining equipment. | Delivers superior toughness, necessary for the harsh mining environment. |
Aerospace | Used in machining high-strength materials like titanium and composites. | Ensures high precision and reliability in critical aerospace components. |
Woodworking | Applied in the creation of router bits and saw blades. | Allows for clean, precise cuts, even in hard woods. |
Medical Devices | Employed in the manufacturing of surgical instruments and implants. | Offers biocompatibility and precision, vital for medical applications. |
Energy Sector | Used in drilling tools for oil and gas exploration. | Withstands high temperatures and pressures, essential for energy exploration. |
Defense | Utilized in armor-piercing rounds and other military equipment. | Provides unmatched hardness and strength, critical in defense applications. |
Construction | Used in concrete drilling and cutting tools. | Enhances durability and efficiency in construction projects. |
Electronics | Applied in the production of precision components for electronic devices. | Ensures high accuracy and consistency, important for electronic manufacturing. |
Material Properties of Carbide Rods
Understanding the material properties of carbide rods is crucial for selecting the right type for your application. Let’s dive into some of the key properties:
Property | Description | Relevance |
---|---|---|
Hardness | Typically ranges from 85 to 92 HRA, depending on the composition. | Higher hardness means better wear resistance, crucial for cutting tools. |
Toughness | Tungsten carbide offers excellent toughness, making it resistant to fracture. | Important for applications where tools are subjected to high stress. |
Density | Usually around 14.5 to 15.0 g/cm³. | Higher density indicates a more compact and durable material. |
Wear Resistance | Extremely high, due to the carbide’s hardness and toughness. | Essential for tools that undergo constant use and friction. |
Thermal Conductivity | Moderate, with values around 85 to 100 W/m·K. | Allows the rod to dissipate heat efficiently, preventing overheating during use. |
Compressive Strength | Typically exceeds 5000 MPa. | High compressive strength is important for applications involving heavy loads. |
Corrosion Resistance | Carbide rods are resistant to most forms of corrosion, especially when coated. | Critical for use in harsh environments where corrosion is a concern. |
Composition, Properties, and Characteristics of Carbide Rods
The unique properties of carbide rods stem from their composition and the processes used to manufacture them. Here’s a closer look:
Composition | Properties | Characteristics |
---|---|---|
Tungsten Carbide (WC) | Provides hardness and wear resistance. | Extremely hard, making it ideal for cutting tools. |
Cobalt (Co) | Acts as a binder, adding toughness and ductility. | Improves the rod’s toughness, preventing brittleness. |
Titanium Carbide (TiC) | Enhances wear resistance and reduces friction. | Often added to carbide rods for specialized applications. |
Tantalum Carbide (TaC) | Increases high-temperature strength. | Used in high-heat applications like aerospace tooling. |
Niobium Carbide (NbC) | Improves wear resistance and toughness. | Helps in enhancing the overall durability of the rod. |
Chromium Carbide (CrC) | Provides corrosion resistance and high-temperature stability. | Used in environments where corrosion is a significant concern. |
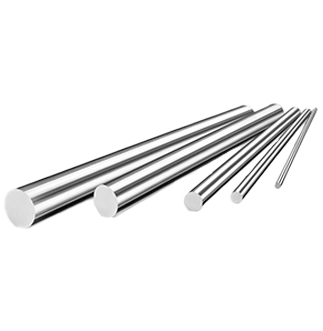
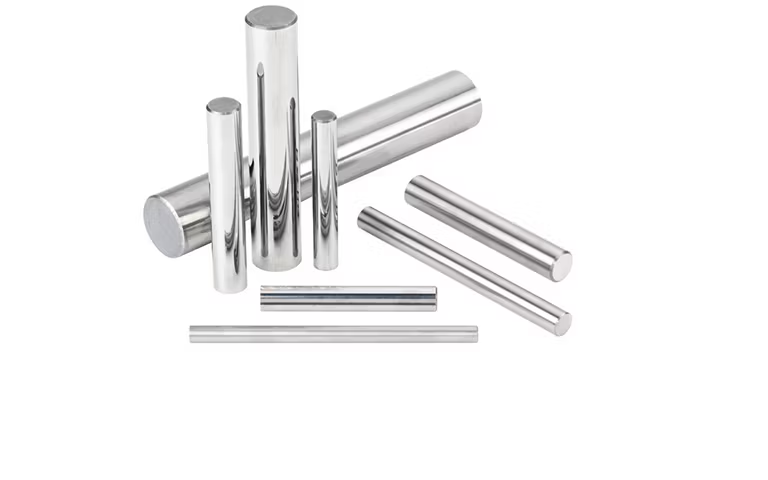
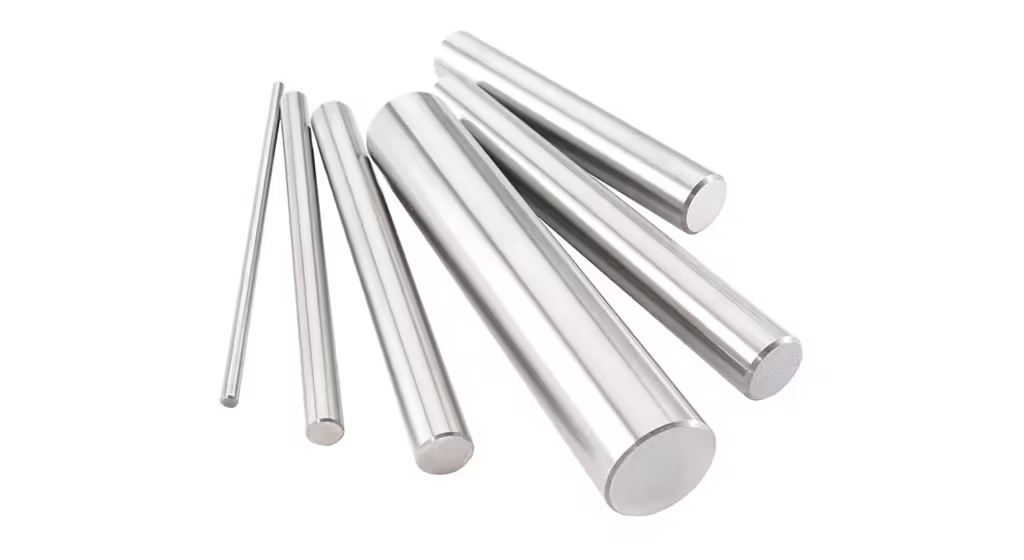
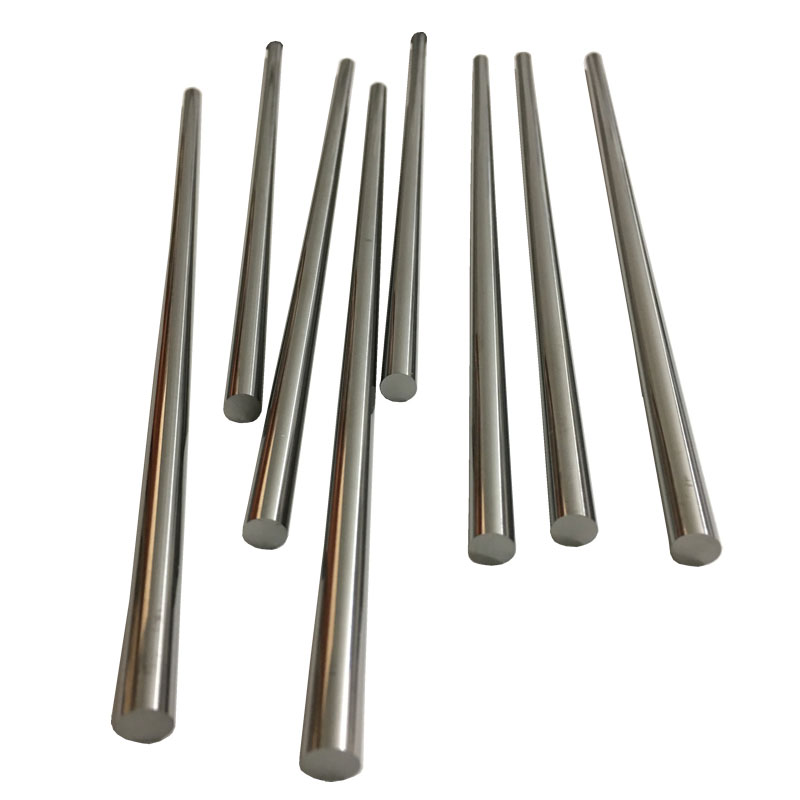
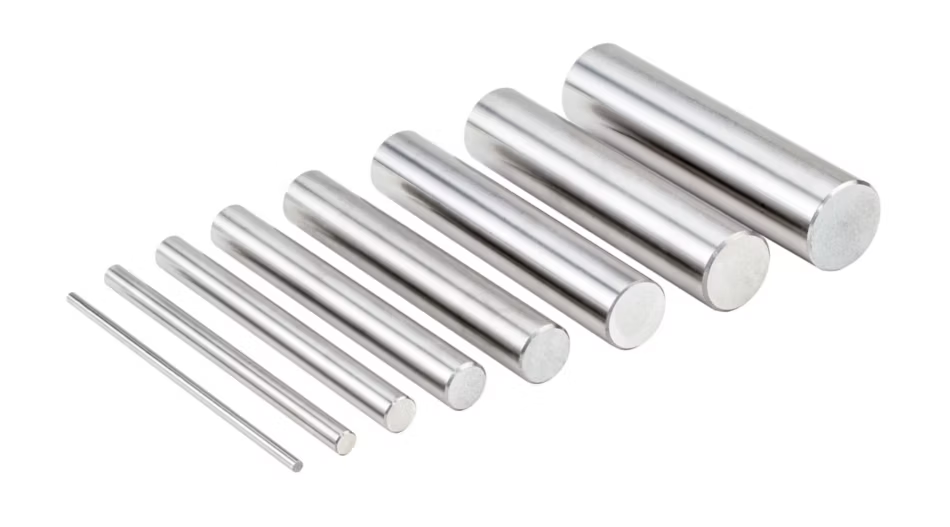
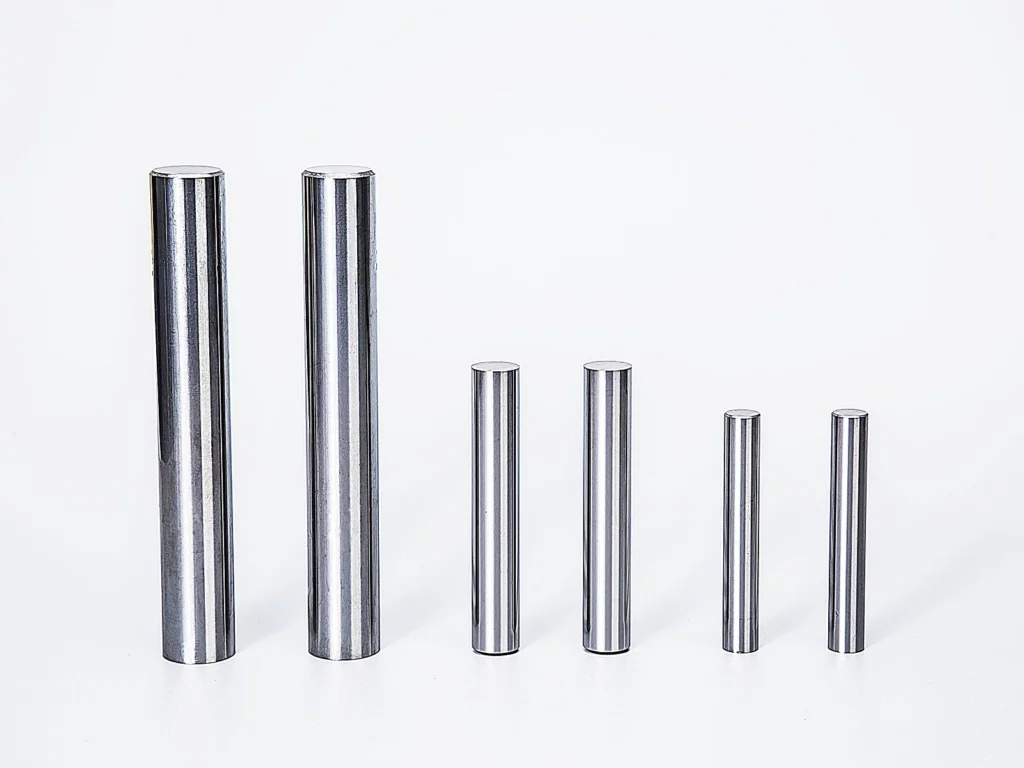
Hardness, Strength, and Wear Resistance of Carbide Rods
One of the main reasons carbide rods are so highly valued is their incredible hardness, strength, and wear resistance. Here’s how these properties compare:
Property | Description | Comparison |
---|---|---|
Hardness (HRA) | Generally between 85 and 92 HRA. | Compared to Steel: Carbide is significantly harder, offering better wear resistance. |
Compressive Strength (MPa) | Typically over 5000 MPa. | Compared to Ceramic: Carbide offers better toughness, reducing the risk of cracking under pressure. |
Wear Resistance | Extremely high due to the material’s inherent properties. | Compared to High-Speed Steel (HSS): Carbide lasts longer and performs better in high-stress applications. |
Fracture Toughness | Tungsten carbide is less brittle than ceramic, making it more reliable under sudden impacts. | Compared to Ceramics: Carbide offers a better balance between hardness and toughness. |
Specifications, Sizes, Shapes, and Standards for Carbide Rods
Carbide rods come in various sizes, shapes, and standards to meet the diverse needs of different industries. Here’s a breakdown:
Specification | Details | Applications |
---|---|---|
Diameter | Ranges from 1 mm to 40 mm. | Small Diameter: Precision tools, electronics. Large Diameter: Heavy-duty tools, construction. |
Length | Typically available from 50 mm to 500 mm. | Short Length: Drill bits, cutting tools. Long Length: Shafts, wear-resistant parts. |
Shapes | Cylindrical, tapered, or custom shapes. | Cylindrical: General machining. Tapered: Specialized tools, custom applications. |
Standards | ISO, DIN, ASTM standards. | Ensures compatibility and reliability across different industries. |
Tolerance | Precision-ground rods can have tolerances as low as ±0.001 mm. | Critical for applications requiring high precision. |
Surface Finish | Available in ground or unground finishes. | Ground: High precision, ready for use. Unground: For custom shaping and finishing. |
Suppliers and Pricing Details for Carbide Rods
Selecting the right supplier is crucial for ensuring the quality and performance of carbide rods. Here
’s a guide to some reputable suppliers and their pricing:
Supplier | Product Range | Pricing | Special Features |
---|---|---|---|
XYZ Carbide | Wide range of solid and coolant hole rods. | Starts at $50 per kg. | Offers custom rod manufacturing. |
ABC Tools | Specializes in precision-ground rods. | Starts at $75 per kg. | Provides fast delivery and bulk discounts. |
123 Industries | Offers a variety of coated and uncoated rods. | Starts at $60 per kg. | Focuses on high-performance coatings. |
Precision Metals | Large selection of sizes and shapes. | Starts at $55 per kg. | Known for high-quality, ISO-certified products. |
Global Carbides | Specializes in carbide blanks. | Starts at $45 per kg. | Offers competitive pricing for large orders. |
How to Select the Right Carbide Rod
Choosing the right carbide rod depends on several factors, including the intended application, material properties, and cost. Here’s a step-by-step guide:
Factor | Considerations | Tips |
---|---|---|
Application | What will the rod be used for? Cutting, drilling, or wear resistance? | Choose a rod with the appropriate hardness and toughness for the job. |
Material Properties | Does the application require high hardness, toughness, or wear resistance? | Consider coated rods for high-wear environments. |
Size and Shape | What size and shape will best suit your needs? | Opt for precision-ground rods for high-precision applications. |
Cost | What is your budget? | Compare prices from different suppliers and consider bulk purchasing for discounts. |
Supplier | Does the supplier offer the specific type of rod you need? | Choose a supplier known for quality and reliability, especially for critical applications. |
Standards | Does the rod meet industry standards like ISO or ASTM? | Always check for compliance with relevant standards to ensure compatibility and performance. |
Comparing Advantages and Limitations of Carbide Rods
When it comes to choosing between different materials or types of carbide rods, it’s essential to weigh the pros and cons. Here’s a comparative analysis:
Advantage | Limitation | Comparison |
---|---|---|
High Hardness | Can be brittle in some applications. | Compared to HSS: Carbide is harder but less tough. |
Wear Resistance | May be more expensive than other materials. | Compared to Steel: Carbide offers better wear resistance but at a higher cost. |
Thermal Stability | Requires specialized equipment for machining. | Compared to Ceramics: Carbide is more versatile but may need more careful handling. |
Precision | Higher initial cost but longer tool life. | Compared to Other Materials: Carbide offers better long-term value despite higher upfront costs. |
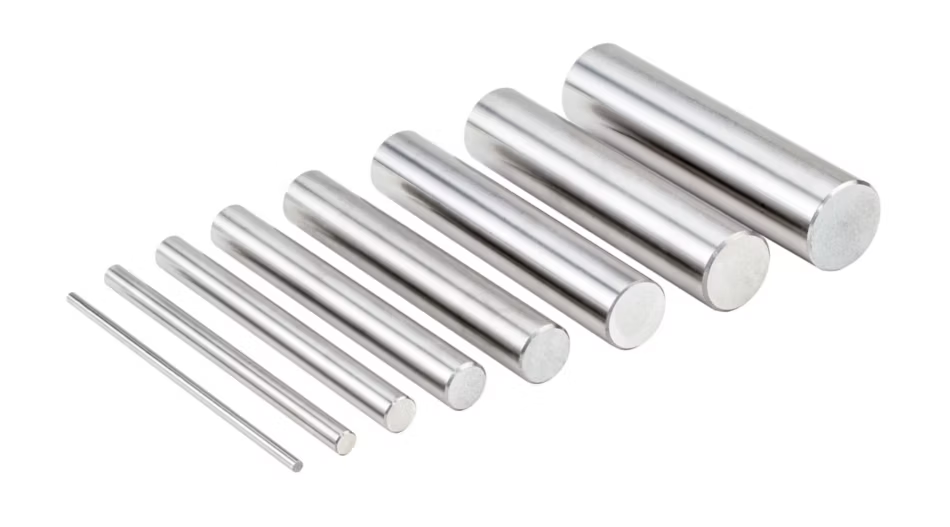
FAQ
Q: What are carbide rods primarily used for?
A: Carbide rods are primarily used in the manufacturing of cutting tools, such as drills, end mills, and reamers. They are also widely used in the automotive, aerospace, and mining industries for their hardness and wear resistance.
Q: How does the composition of carbide rods affect their performance?
A: The performance of carbide rods is heavily influenced by their composition. Tungsten carbide provides hardness, while cobalt adds toughness. Additional elements like titanium carbide or tantalum carbide can enhance wear resistance and high-temperature performance.
Q: Can carbide rods be customized for specific applications?
A: Yes, carbide rods can be customized in terms of size, shape, and coating to meet specific application requirements. Many suppliers offer precision-ground rods or rods with special coatings like titanium nitride for enhanced performance.
Q: What factors should be considered when selecting a carbide rod supplier?
A: When selecting a supplier, consider factors like product range, pricing, delivery times, and the quality of customer service. It’s also important to ensure that the supplier meets relevant industry standards.
Q: Are there any disadvantages to using carbide rods?
A: While carbide rods offer numerous advantages, such as high hardness and wear resistance, they can be more expensive than other materials and may require specialized equipment for machining.
Conclusion
Carbide rods are indispensable in many industries due to their exceptional hardness, strength, and versatility. Whether you’re in metalworking, aerospace, or mining, understanding the different types, applications, and material properties of carbide rods can help you make informed decisions that enhance your operations’ efficiency and effectiveness. By carefully selecting the right carbide rod and supplier, you can ensure optimal performance and longevity in even the most demanding applications.
This guide has covered everything from the basic types of carbide rods to detailed specifications, suppliers, and application tips. Armed with this knowledge, you’re well-equipped to navigate the world of carbide rods and make choices that best suit your specific needs.