Overview
Carbide punch strips are essential components in precision manufacturing, offering unmatched hardness, wear resistance, and durability. These strips play a crucial role in various industries, including automotive, aerospace, and metalworking. In this comprehensive guide, we will explore everything you need to know about carbide punch strips, including their definition, working principles, usage, manufacturing process, types, market trends, applications, comparisons, and advantages and disadvantages.
Detailed Introduction
What Are Carbide Punch Strips?
Carbide punch strips are elongated bars made from tungsten carbide, designed to be used in punching and stamping operations. Tungsten carbide is a composite material composed of tungsten and carbon, often bonded with a metal binder like cobalt or nickel. These strips are known for their exceptional hardness and wear resistance, making them ideal for applications that require precise and repetitive punching.
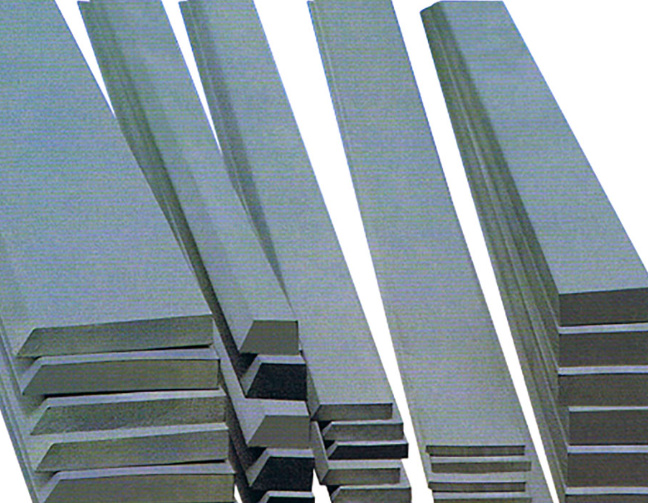
Working Principles of Carbide Punch Strips
Carbide punch strips operate on the principle of high-pressure impact. When a punch strip is pressed against a material, it delivers a concentrated force that cuts or shapes the material. The hardness of tungsten carbide ensures that the strip maintains its sharp edge and resists wear, even under intense pressure.
How to Use Carbide Punch Strips
Using carbide punch strips involves several steps:
- Selection: Choose the appropriate type and size of carbide punch strip based on the material and the desired punch shape.
- Installation: Secure the punch strip in the punching machine, ensuring it is aligned correctly.
- Operation: Operate the machine according to the manufacturer’s instructions, maintaining proper pressure and speed.
- Maintenance: Regularly inspect and sharpen the punch strip to maintain its performance.
Manufacturing Process of Carbide Punch Strips
The manufacturing process of carbide punch strips includes the following steps:
- Powder Mixing: Tungsten carbide powder is mixed with a binder, typically cobalt or nickel.
- Pressing: The powder mixture is pressed into the desired shape using a mold.
- Sintering: The pressed pieces are heated in a sintering furnace, causing the particles to bond and form a solid piece.
- Finishing: The sintered pieces are ground and polished to achieve the desired dimensions and surface finish.
Types of Carbide Punch Strips
There are several types of carbide punch strips, each designed for specific applications:
- Standard Carbide Punch Strips: Used for general punching applications.
- Micrograin Carbide Punch Strips: Made with smaller carbide particles for a sharper edge and better wear resistance.
- Sub-Micrograin Carbide Punch Strips: Feature even smaller particles for higher precision and durability.
- Coated Carbide Punch Strips: Have an additional coating to enhance wear resistance and reduce friction.
Market Trends
The market for carbide punch strips is growing due to their versatility and durability. Industries such as automotive, aerospace, and metalworking are increasingly adopting these strips for their precision and cost-effectiveness. The demand for advanced manufacturing processes and high-quality products is driving the growth of the carbide punch strip market.
Product Information
Basic Information of Carbide Punch Strips
Type | Composition | Properties | Features | Specifications | Typical Applications |
---|---|---|---|---|---|
Standard Carbide Punch Strips | WC + Co | High hardness, good toughness | Durable, reliable | Customizable sizes | General punching and stamping |
Micrograin Carbide Punch Strips | WC + Co | Higher hardness, better wear resistance | Sharp edge, precise | Customizable sizes | Precision punching, fine stamping |
Sub-Micrograin Punch Strips | WC + Co | Superior hardness, excellent wear resistance | Highly durable, low friction | Customizable sizes | High-speed punching, precision stamping |
Coated Carbide Punch Strips | WC + Co + Coating | Enhanced wear resistance, reduced friction | Longer lifespan, less maintenance | Customizable sizes | High-performance punching, abrasive materials |
Description: This table provides detailed information about different types of carbide punch strips, highlighting their composition, properties, features, specifications, and typical applications.
Applications of Carbide Punch Strips
Carbide punch strips are used in various industries due to their precision and durability. Here are some primary applications:
- Automotive Industry: Used in the manufacturing of car body panels, engine components, and other precision parts.
- Aerospace Industry: Employed in the production of aircraft components and structural parts.
- Metalworking: Utilized in punching and stamping operations for sheet metal fabrication.
- Electronics: Used in the manufacturing of electronic components and circuit boards.
- Packaging: Applied in the production of packaging materials and containers.
- Medical: Used in the creation of medical devices and surgical instruments.
- Construction: Employed in the fabrication of building components and tools.
Comparison of Suppliers
Comparison of TRUER with Different Suppliers
Supplier | Location | Price Range (per piece) | Specialties |
---|---|---|---|
TRUER | USA | $30 – $50 | High precision, custom sizes, quick delivery |
ABC Carbide Suppliers | Germany | $35 – $55 | Excellent wear resistance, extensive product range |
XYZ Tools | China | $25 – $45 | Cost-effective, large volume orders |
DEF Industrial | Japan | $40 – $60 | Advanced technology, premium quality |
Description: This table compares TRUER with different suppliers, focusing on location, price range per piece, and specialties. It provides a clear comparison to help you choose the right supplier for your needs.
Advantages and Limitations of Carbide Punch Strips
Advantages and Limitations of Carbide Punch Strip
Advantages | Limitations |
---|---|
High hardness and wear resistance | Higher cost compared to other materials |
Long lifespan, reducing tool replacement | Requires precise manufacturing processes |
Versatile applications across industries | Brittle nature can lead to chipping |
Customizable for specific needs | Limited to applications where brittleness is not a concern |
Description: This table highlights the benefits and drawbacks of using carbide punch strip, providing a balanced view of their performance and limitations.
Related Content
Innovations in Carbide Technology
Recent advancements in carbide technology have led to the development of new grades and coatings that enhance the performance of carbide punch strip. These innovations include nanostructured carbides and gradient materials that offer improved toughness and wear resistance.
Maintenance and Care for Carbide Punch Strips
Proper maintenance and care can significantly extend the lifespan of carbide punch strip. This includes regular cleaning, avoiding excessive heat, and ensuring correct usage to prevent chipping and wear.
Environmental Impact of Carbide Manufacturing
The manufacturing of carbide punch strip involves processes that can impact the environment. However, advancements in recycling and sustainable manufacturing practices are helping to minimize these effects.
Why Choose TRUER
Choosing TRUER for your carbide punch strip offers several advantages:
- High Precision: TRUER provides high-precision carbide punch strip that ensure accurate and consistent performance.
- Custom Sizes: TRUER offers customizable sizes to meet your specific requirements.
- Quick Delivery: With efficient production processes, TRUER ensures quick delivery times.
- Excellent Customer Support: TRUER provides exceptional customer support to help you select and maintain your carbide punch strip.
FAQ
Q1: What makes carbide punch strips superior to other punching materials?
A1: Carbide punch strip are superior due to their exceptional hardness, wear resistance, and ability to maintain a sharp edge under extreme conditions. This results in longer tool life and better performance in demanding applications.
Q2: How do I choose the right type of carbide punch strip for my application?
A2: The choice depends on the specific requirements of your application, such as the material being punched, the operating conditions, and the desired tool life. Consulting with a knowledgeable supplier can help you select the appropriate type.
Q3: Can carbide punch strips be customized for specific applications?
A3: Yes, carbide punch strip can be customized in terms of size, shape, and composition to meet the specific needs of different applications. This ensures optimal performance and efficiency.
Q4: What are the common applications of carbide punch strips in the automotive industry?
A4: In the automotive industry, carbide punch strip are commonly used in the manufacturing of car body panels, engine components, and other precision parts. They provide a sharp, durable edge that can punch through metal efficiently and with precision.
Q5: How does the cost of carbide punch strips compare to other punching materials?
A5: While carbide punch strip may have a higher initial cost compared to other materials, their long lifespan and superior performance often result in lower overall costs due to reduced tool replacement and maintenance needs.