- Carbide Production Process
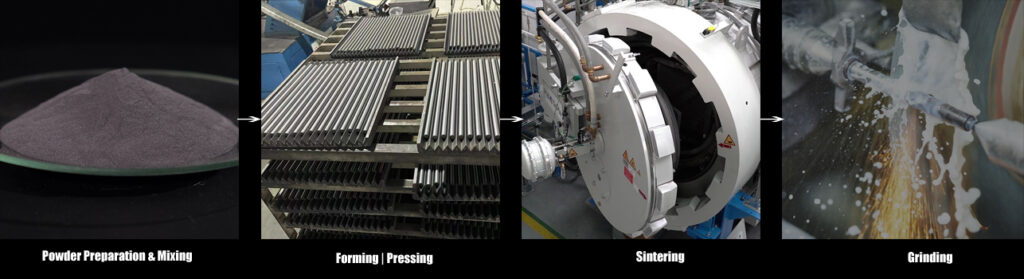
- Powder preparation
The tungsten carbide is mixed with the binder metal cobalt, nickel or iron, grain growth inhibitors and special alloys as well as materials which promote compaction by wet grinding to create a homogeneous suspension. Afterwards, the suspension is dried to produce a granulate with good flow characteristics. This granulate represents the basis for all forming processes.
- Forming / Pressing
The objective of the forming process is to obtain a compacted sample. There are several ways for the pressing of carbide blanks:

Cold isostatic pressing (CIP)
In which the powder is filled into shaped-bag and subjected to equal pressure from all directions using a liquid medium and pressed into a compacted form. Dimensional tolerances for parts produced by CIP are relatively larger than other pressing process.

Uniaxial pressing
the pressing tool consists of a die, an upper and lower punch. The carbide powder is filled into into the die and then compacted to create the near net shape geometry of the green compact by the upper and lower punch, which is then ejected from the pressing die.

Extrusion pressing
Mainly is used to produce rectangular bars or cylindrical rods with or without axial holes. A plastifier is added to the powder. The resulting paste is pressed through an extrusion nozzle. Before sintering, the plastifier must be evaporated in special drying furnaces.

Metal injection moulding (MIM)
is a process in which powdered metal is mixed with binder material to create a “feedstock” that is then shaped using injection moulding. It used to produce more complex forms which cannot be produced by direct pressing.
- Sintering
The sintering is the process which converts the blank after pressing into a homogeneous and dense cemented carbide with a high level of hardness by heat. The material is sintered at temperatures between 1300 and 1500°C (liquid phase sintering for tungsten carbide) and sometimes also at high pressure.
- Finishing-Grinding
In order to achieve the final requirements of surface finish and dimension tolerances, carbide parts can undergo a series of finishing processes such as grinding, polishing, spark erosion and coating.