Have you ever wondered how industries handle extreme wear and tear, high temperatures, and corrosive environments? The answer often lies in a material that’s quietly revolutionizing manufacturing and engineering: carbide plates.
These aren’t your everyday metal plates. Crafted from tungsten carbide, a material boasting incredible hardness, they’re the unsung heroes behind countless products and processes. Let’s dive into ten fascinating applications where carbide plates are making a real difference.
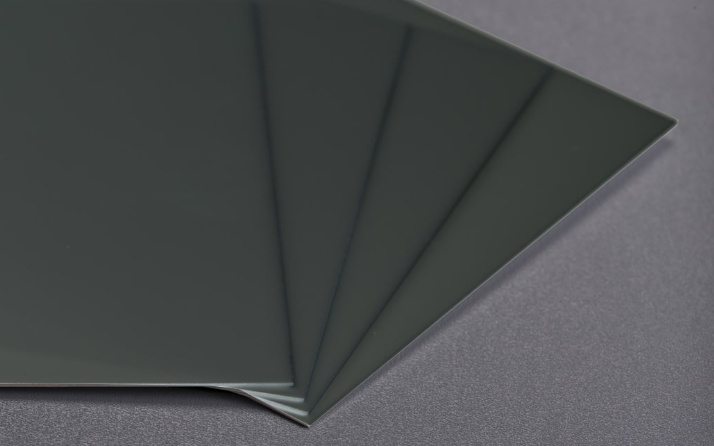
1. Metal Forming: Shaping the World Around Us
From car parts to kitchen appliances, metal forming is essential for countless everyday objects. Carbide plates, used in dies, punches, and wear plates, ensure these processes happen with precision and longevity. Their resistance to wear and deformation under pressure keeps production lines running smoothly and products meeting exacting standards.
2. Cutting and Machining: Tools That Last
Think of the sharpest tools you know – now imagine them even more durable. Carbide inserts in cutting tools, saw tips, and drill bits allow for faster cutting speeds, smoother finishes, and significantly longer tool life. This translates to cost savings and increased efficiency across industries like woodworking, metalworking, and construction.
3. Material Handling: Keeping Things Moving
Moving abrasive materials like coal, ore, or grain can take a toll on equipment. Carbide wear liners in chutes, hoppers, and conveyors act as protective armor, minimizing wear and tear. This ensures smooth material flow, reduces downtime for maintenance, and extends the lifespan of expensive equipment.
4. Oil and Gas Exploration: Venturing into Extreme Environments
Drilling for oil and gas presents unique challenges, including high pressures, abrasive formations, and corrosive substances. Carbide plates play a crucial role in downhole drilling tools, wear rings, and other components, ensuring reliability and performance in these demanding conditions.
5. Construction and Mining: Powering Through Tough Jobs
Construction and mining rely on heavy machinery that endures immense stress. Carbide wear parts in drilling equipment, crushing equipment, and excavators protect critical components from abrasion, impact, and wear, reducing maintenance needs and extending equipment lifespan.
6. Aerospace: Reaching New Heights
Lightweight yet incredibly strong, carbide plates find applications in aerospace components like bearings, seals, and fuel system parts. Their resistance to wear, heat, and corrosion ensures reliability and performance in the demanding conditions of flight.
7. Chemical Processing: Handling Corrosive Substances
Chemical processing often involves handling highly corrosive substances that can quickly degrade equipment. Carbide plates, with their exceptional corrosion resistance, are used in pumps, valves, and reactor linings, ensuring safety and extending the lifespan of critical components.
8. Food Processing: Ensuring Hygiene and Durability
Maintaining hygiene is paramount in food processing. Carbide blades and cutting tools offer superior wear resistance and corrosion resistance compared to steel, reducing the risk of contamination and ensuring cleaner cuts.
9. Medical Devices: Precision and Biocompatibility
Carbide’s hardness and biocompatibility make it suitable for use in medical devices like surgical instruments, dental burs, and implants. Its resistance to wear and corrosion ensures longevity and reliability in these critical applications.
10. Recycling and Waste Management: Closing the Loop
Even at the end of their lifecycle, carbide plates prove valuable. Due to the high value of tungsten, carbide scrap is often recycled, contributing to resource conservation and reducing environmental impact.
Carbide Plate Properties: A Closer Look
Property | Description | Benefit |
---|---|---|
Hardness | Measured on the Rockwell A scale (HRA), typically exceeding 85 HRA. | Exceptional resistance to wear, abrasion, and deformation. |
Compressive Strength | Can withstand extreme compressive forces. | Ideal for applications involving heavy loads and impacts. |
Heat Resistance | Maintains its properties at elevated temperatures. | Suitable for high-temperature applications. |
Corrosion Resistance | Highly resistant to corrosion from chemicals and harsh environments. | Excellent for use in demanding environments. |
Table 1: Key Properties of Carbide Plates
FAQs: Answering Your Questions About Carbide Plate Applications
1. What are the main advantages of using carbide plates over other materials?
Carbide plates offer superior hardness, wear resistance, heat resistance, and corrosion resistance compared to most other materials, making them ideal for demanding applications where longevity and performance are critical.
2. Are carbide plates only used in heavy industries?
While prevalent in heavy industries, carbide plates are also used in various other sectors like medical devices, food processing, and even high-end consumer products where durability and precision are essential.
3. Can carbide plates be machined or shaped to specific requirements?
Yes, although challenging due to their hardness, carbide plates can be machined using specialized techniques like EDM (Electrical Discharge Machining) and diamond grinding to achieve specific shapes and dimensions.
4. Are there different grades of carbide plates for different applications?
Yes, various grades of carbide plates are available, each with a specific combination of properties tailored for particular applications. Factors like required hardness, toughness, and wear resistance determine the optimal grade.
5. What is the lifespan of a typical carbide plate?
The lifespan of a carbide plate varies significantly depending on the application, operating conditions, and maintenance practices. However, due to their exceptional wear resistance, carbide plates often last significantly longer than components made from other materials, leading to reduced downtime and maintenance costs.
Want to buy a Carbide Plate of excellent quality at the right price? Click here.