What is a Carbide Plate?
Carbide plates are essential components in industries requiring extreme wear resistance, such as mining, metalworking, and construction. These plates, primarily composed of tungsten carbide (WC) or titanium carbide (TiC), provide unmatched durability and hardness, making them ideal for applications subjected to heavy abrasion and impact.
Think of carbide plates as the body armor of industrial machinery. They protect cutting tools, conveyor belts, and even high-wear components in excavation machinery. However, welding carbide plates isn’t as simple as regular steel welding. The unique material properties demand specialized techniques and procedures to ensure strong, long-lasting bonds.
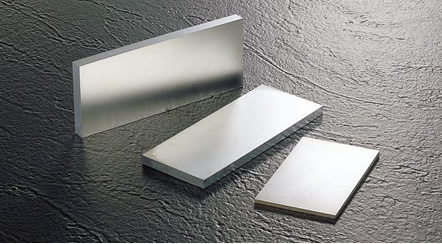
Common Welding Methods for Carbide Plates
1. Brazing
Brazing is one of the most common methods for joining carbide plates. It involves using a filler metal (like silver-copper alloys) with a lower melting point than the carbide itself. This method is ideal because it doesn’t weaken the carbide due to excessive heat exposure.
Pros:
- Produces strong joints with minimal thermal damage.
- Works well for small or intricate carbide components.
- Provides excellent resistance to mechanical stress.
Cons:
- Requires precise temperature control.
- Can be time-consuming compared to arc welding.
2. Tungsten Inert Gas (TIG) Welding
TIG welding, also known as Gas Tungsten Arc Welding (GTAW), is suitable for carbide plates when using a specialized filler metal, such as cobalt-based alloys.
Pros:
- Produces high-quality, precise welds.
- Offers excellent control over heat input.
- Reduces distortion in thin carbide plates.
Cons:
- Slower process compared to other welding methods.
- Requires highly skilled welders.
3. Plasma Transferred Arc (PTA) Welding
PTA welding is often used to deposit carbide powders onto a metal substrate, creating a wear-resistant coating.
Pros:
- Produces highly wear-resistant surfaces.
- Allows for customization of carbide layers.
Cons:
- Requires expensive equipment.
- More complex setup compared to MIG or TIG welding.
4. Laser Welding
Laser welding uses concentrated light beams to fuse carbide plates with other metals, offering precision and minimal heat-affected zones (HAZ).
Pros:
- Low heat input minimizes cracking.
- Provides precise and strong welds.
Cons:
- Requires advanced equipment.
- High initial investment cost.
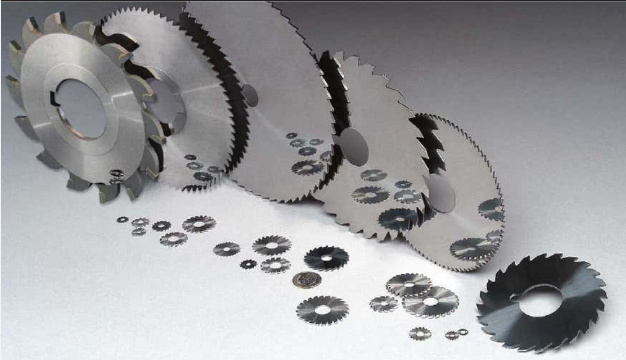
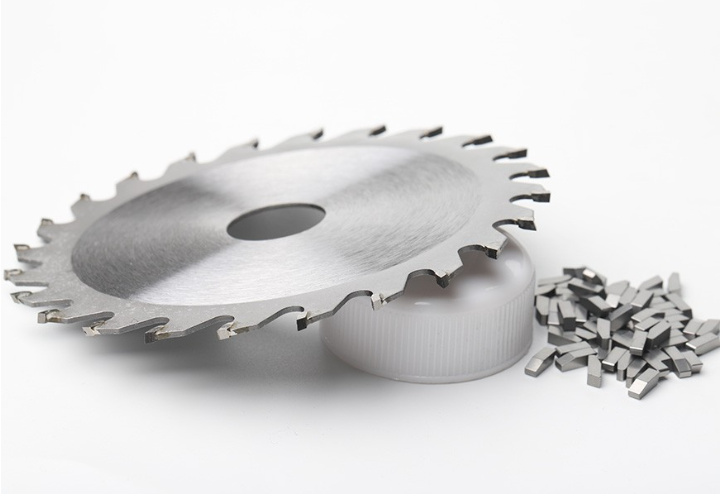
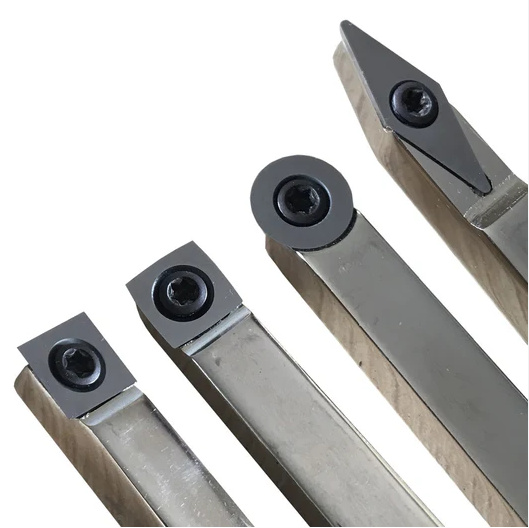
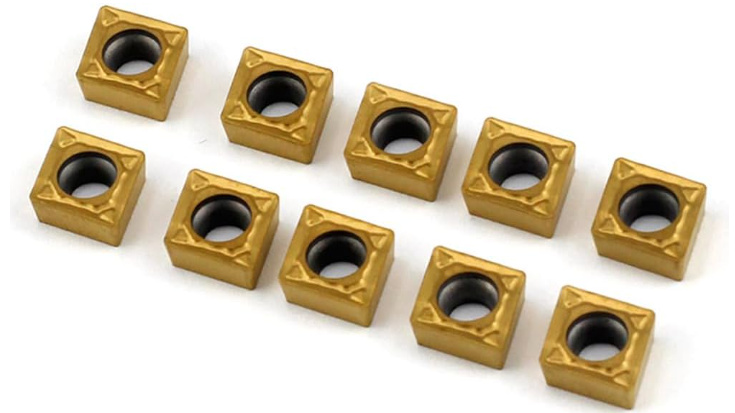
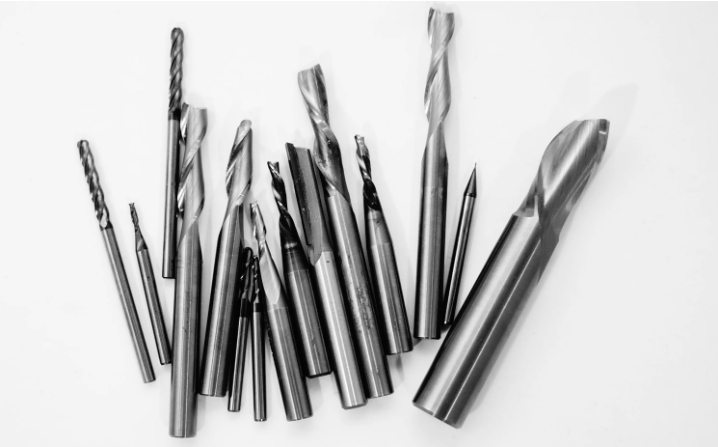
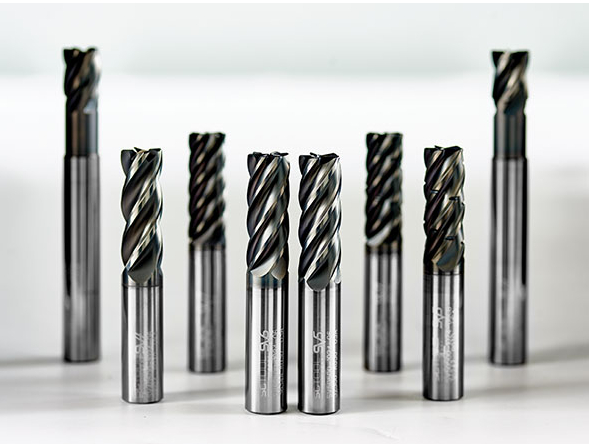
Best Welding Practices for Carbide Plates
Pre-Welding Preparation
- Surface Cleaning: Remove any oxidation, grease, or contaminants to ensure proper fusion.
- Preheating: Reduces thermal shock and prevents cracking.
- Filler Metal Selection: Use cobalt, nickel, or silver-based fillers for optimal bonding.
During Welding
- Maintain a low heat input to prevent carbide degradation.
- Use controlled cooling to avoid residual stress and cracking.
- Apply slow travel speeds for uniform material deposition.
Post-Welding Treatment
- Implement stress relief heat treatment where necessary.
- Conduct non-destructive testing (NDT) to ensure bond integrity.
Common Mistakes and How to Avoid Them
Mistake | Why It Happens | How to Avoid It |
---|---|---|
Excessive Heat Input | Overheating causes carbide degradation. | Use lower amperage and controlled preheating. |
Improper Filler Selection | Incorrect filler metals result in weak joints. | Use cobalt, nickel, or silver-based alloys. |
No Preheating | Thermal shock can cause cracking. | Preheat carbide plates to the recommended temperature. |
Rapid Cooling | Sudden temperature changes lead to brittleness. | Allow slow, controlled cooling post-welding. |
Inadequate Surface Prep | Oxidation or contaminants weaken the bond. | Clean surfaces thoroughly before welding. |
Recommended Metal Powder Models for Carbide Welding
Metal Powder Model | Composition | Application |
---|---|---|
WC-10Co | 90% Tungsten Carbide, 10% Cobalt | High-impact resistance applications |
WC-12Ni | 88% Tungsten Carbide, 12% Nickel | Corrosion-resistant coatings |
TiC-15Co | 85% Titanium Carbide, 15% Cobalt | High-temperature applications |
CrC-10Ni | 90% Chromium Carbide, 10% Nickel | Extreme wear resistance |
WC-17Co | 83% Tungsten Carbide, 17% Cobalt | Mining and drilling tools |
WC-8Co | 92% Tungsten Carbide, 8% Cobalt | High-hardness wear coatings |
NbC-10Co | 90% Niobium Carbide, 10% Cobalt | Abrasion and heat resistance |
MoC-15Ni | 85% Molybdenum Carbide, 15% Nickel | Thermal spray applications |
VC-10Fe | 90% Vanadium Carbide, 10% Iron | Cutting tool reinforcement |
WC-5Co | 95% Tungsten Carbide, 5% Cobalt | Precision tools and wear parts |
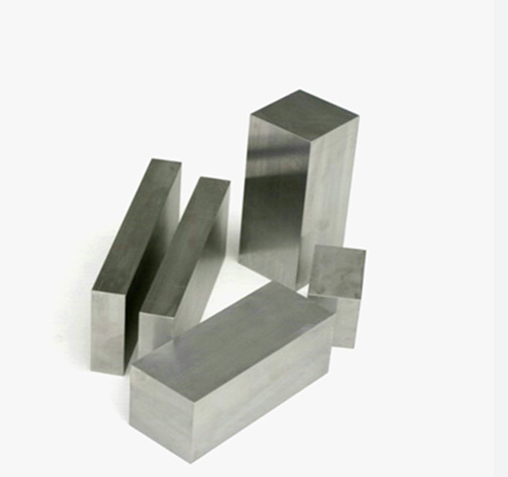
FAQ
Question | Answer |
---|---|
What is the best method for welding carbide plates? | Brazing is ideal for small components, while PTA and laser welding are preferred for industrial applications. |
Why do carbide plates crack during welding? | High heat input and rapid cooling can cause thermal stress and cracking. Preheating and controlled cooling help prevent this. |
Can I use standard MIG welding for carbide plates? | No, standard MIG welding lacks the necessary precision and heat control for carbide materials. |
What is the ideal preheating temperature for carbide welding? | Typically between 300°C and 600°C, depending on the alloy composition. |
What filler metals work best for carbide welding? | Cobalt-based and nickel-based fillers provide the best bonding with carbide plates. |