What is a Carbide Plate?
Carbide plates are high-performance metal components made primarily from tungsten carbide (WC), often bonded with cobalt (Co) or other binders to enhance mechanical properties. These plates are widely used in industrial applications requiring extreme wear and corrosion resistance.
Factors Affecting Corrosion Resistance
Carbide plates are tough, but their corrosion resistance depends on multiple factors. Let’s break them down:
1. Binder Composition
The choice of binder plays a crucial role in corrosion resistance. For instance:
- Cobalt (Co): Enhances toughness but is more susceptible to corrosion in acidic environments.
- Nickel (Ni): Offers better corrosion resistance than cobalt, especially in marine and chemical processing applications.
- Chromium (Cr) Additions: Improve resistance against oxidation and acidic attacks.
2. Grain Size of Carbide Powder
Finer carbide grains lead to higher density and less porosity, making the material less prone to corrosion. Coarse grains may introduce weak points where corrosive agents can penetrate.
3. Environmental Factors
Exposure to extreme conditions like high humidity, acidic solutions, or saltwater can accelerate corrosion. Understanding the working environment helps in selecting the right carbide composition.
4. Surface Treatments & Coatings
Applying a protective coating, such as TiN (Titanium Nitride) or Al2O3 (Aluminum Oxide), can significantly enhance resistance to corrosion.
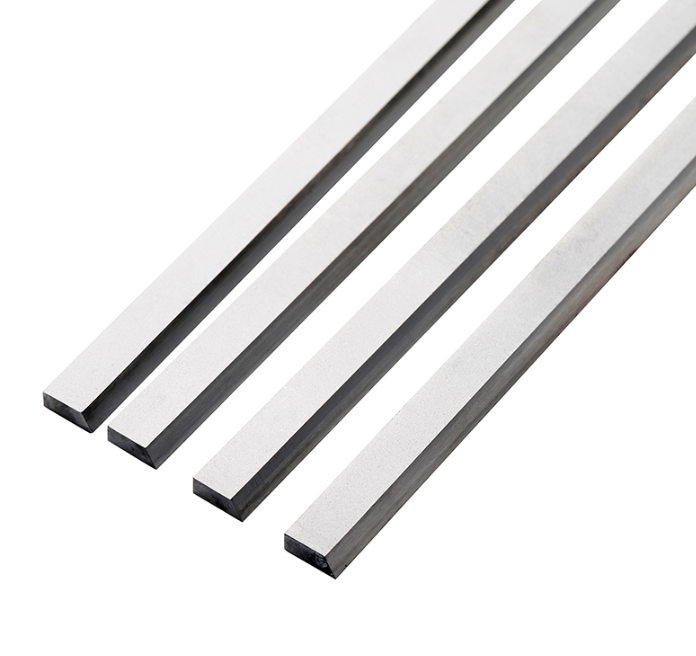
Advantages of Carbide Plates in Corrosive Environments
Why should industries choose carbide plates over conventional metals? Here are some compelling advantages:
- Superior Hardness & Strength: Unlike stainless steel, carbide plates maintain their integrity even under extreme stress and temperature fluctuations.
- Extended Lifespan: High resistance to both wear and corrosion means lower replacement costs and downtime.
- Chemical Stability: Ideal for harsh chemical processing applications where other metals may degrade quickly.
- High Temperature Tolerance: Carbide remains structurally sound at temperatures where steel and aluminum may weaken.
Applications of Corrosion-Resistant Carbide Plates
Industry | Application | Corrosive Exposure |
---|---|---|
Oil & Gas | Drilling tools, valves, pump seals | Seawater, crude oil |
Chemical Processing | Heat exchangers, reactor linings | Acidic & alkaline chemicals |
Aerospace | Engine components, high-pressure nozzles | Extreme temperatures, moisture |
Marine | Propeller shafts, ship components | Saltwater corrosion |
Mining | Wear-resistant conveyor plates | Moisture, abrasives |
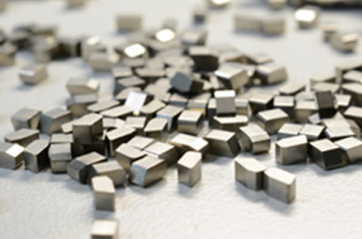
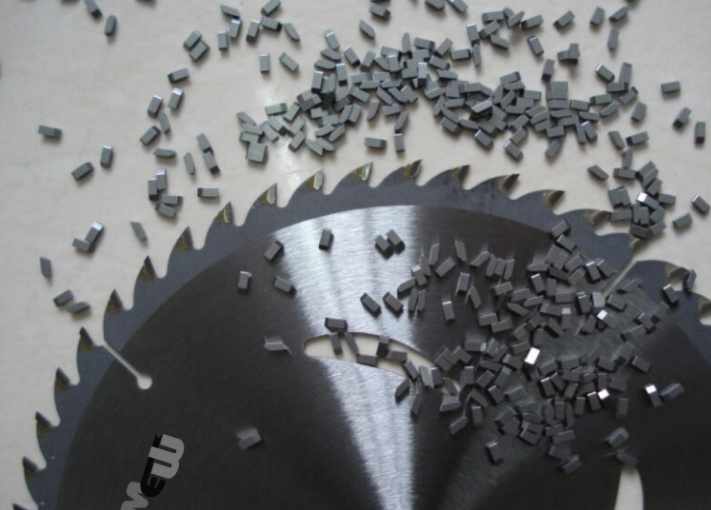
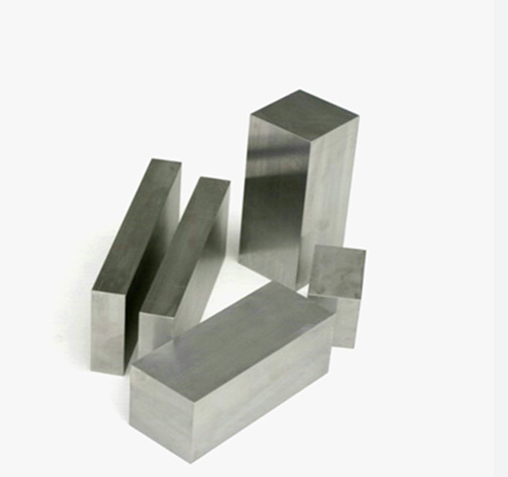

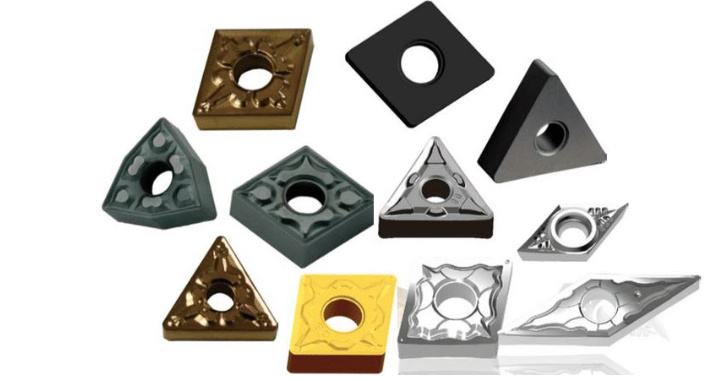
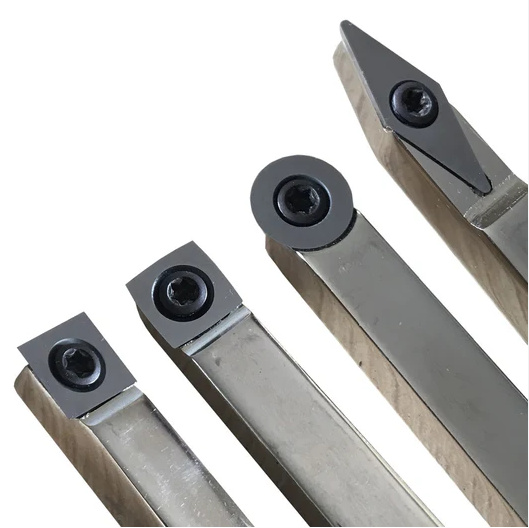
How to Enhance the Corrosion Resistance of Carbide Plates?
Method | Description | Effectiveness |
---|---|---|
Binder Optimization | Using Ni or Cr-based binders instead of Co | High |
Nano-Grain Structure | Finer carbide grains reduce porosity | High |
Surface Coatings | TiN, Al2O3, or PVD coatings for protection | Very High |
Chemical Treatments | Passivation techniques to enhance surface stability | Moderate |
Alloy Additions | Incorporating elements like vanadium or chromium | High |
Corrosion Resistance Characteristics and Application Value of Carbide Plates
Carbide plates are invaluable in industries requiring extreme durability. With the right material composition and protective measures, their corrosion resistance can match or even exceed that of traditional stainless steel. When compared to alternatives like high-alloy steels, carbide plates offer superior longevity, cost-effectiveness, and performance in aggressive environments.
Top 10 Corrosion-Resistant Carbide Powder Models
Carbide Powder Model | Composition | Best for Applications |
---|---|---|
WC-Co (6%) | Tungsten Carbide, 6% Cobalt | Cutting tools, wear parts |
WC-Ni (8%) | Tungsten Carbide, 8% Nickel | Chemical processing, marine |
WC-CrC-Ni | Tungsten Carbide, Chromium Carbide, Nickel | Aerospace, high-temperature environments |
TiC-WC-Co | Titanium Carbide, Tungsten Carbide, Cobalt | High-speed machining |
WC-Co-Cr | Tungsten Carbide, Cobalt, Chromium | Corrosion-resistant coatings |
WC-NiMoCr | Tungsten Carbide, Nickel, Molybdenum, Chromium | Oil & gas industry |
WC-Co-V | Tungsten Carbide, Cobalt, Vanadium | Abrasive environments |
WC-FeNi | Tungsten Carbide, Iron, Nickel | Heavy-duty industrial applications |
WC-Cr3C2 | Tungsten Carbide, Chromium Carbide | Extreme wear resistance |
WC-Al2O3 | Tungsten Carbide, Aluminum Oxide | High thermal resistance |
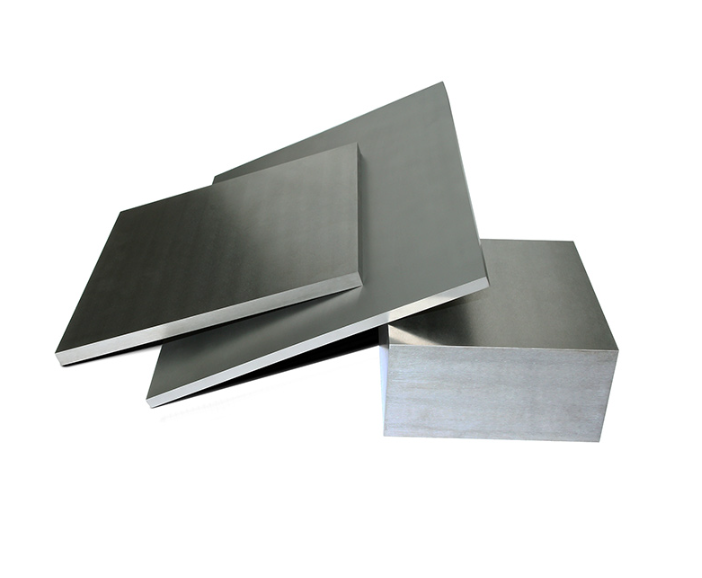
FAQ
Question | Answer |
---|---|
Are carbide plates completely corrosion-proof? | No, but they have high resistance depending on the binder and coating used. |
How do I choose the best carbide plate for my application? | Consider factors like environment, temperature, and chemical exposure. Nickel-based binders work best for corrosion resistance. |
Can carbide plates be used in seawater applications? | Yes, especially those with nickel binders and protective coatings like CrC. |
What coatings can improve carbide corrosion resistance? | TiN, Al2O3, and PVD coatings provide excellent protection. |
How do carbide plates compare to stainless steel? | Carbide is harder and more wear-resistant, but stainless steel may be preferable in some cases due to lower cost and greater flexibility. |