Carbide mining buttons, also referred to as carbide buttons or tungsten carbide buttons, are an integral component in mining machinery and equipment. Constructed from tungsten carbide, these high-strength wear components protect drill bits and other ground-engaging tools from abrasion and impact stresses during demanding mining operations.
This guide provides a comprehensive overview of carbide mining buttons covering composition, properties, manufacturing standards, applications across mineral, metal, coal and aggregate sectors, global suppliers and costs. Technical comparisons enable informed selection while expert analysis lends engineering insights into optimizing button performance in varying rock conditions.
Carbide Button Composition
Tungsten carbide, often depicted by the chemical formula WC, forms the base composite material for carbide buttons. It comprises atoms of tungsten (W) alloyed with carbon atoms (C) via powder metallurgy techniques of milling, pressing and high-temperature sintering.
The precise proportion of carbon determines hardness, toughness and wear resistance values. Common industry standards require 5.5-6.5% carbon content in tungsten carbide grades for mining buttons.
Element | Composition by Weight % |
---|---|
Tungsten (W) | 94 – 95% |
Carbon (C) | 5.5 – 6.5% |
Table 1: Carbide button material composition
To augment certain properties like erosion resistance or thermal conductivity, small percentages of other refractory metals are blended:
- Titanium carbide (TiC) improves chemical inertness crucial for highly abrasive and corrosive conditions
- Tantalum carbide (TaC) enhances ductility and shock resistance at the cost of hardness
- Niobium carbide (NbC) aids grain size control during sintering
Alloying Element | Composition Range | Key Property Improved |
---|---|---|
Titanium Carbide (TiC) | 0 – 8% | Corrosion Resistance |
Tantalum Carbide (TaC) | 0 – 6% | Toughness |
Niobium Carbide (NbC) | 0 – 5% | Wear Resistance |
Properties of Carbide Buttons
Combining tungsten’s refractory attributes with carbon’s metal-hardening tendencies produces a unique grade of cemented carbide blend with exceptional physical properties well-suited for high-impact mining functions.
Property | Measurement |
---|---|
Density | 14.3 – 15.1 g/cc |
Compressive Strength | 5.5 – 6.1 GPa |
Hardness | 86 – 91 HRA |
Fracture Toughness | 9 – 15 MPa√m |
Maximum Service Temperature | 500°C |
Thermal Conductivity | 60 – 90 W/mK |
Coefficient of Thermal Expansion | 5.3 – 6.1 x 10<sup>-6</sup> /K |
Hardness figures approaching diamond make carbide supremely wear-resistant able to withstand highly abrasive ore handling. Toughness imparts damage tolerance against sudden impact loads. High temperature durability ensures consistent carbide button performance in hot operating environments when drilling or crushing rocks.
Thermal characteristics become vital when buttons undergo repeated friction-generated heat cycles from engaging tumbling material. Sufficient conductivity prevents overheating while expansion coefficients minimize thermal cracks.
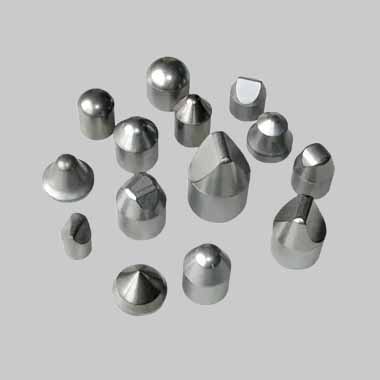
Carbide Button Standards
To guarantee grades have necessary quality attributes for heavy mining conditions, carbide buttons are manufactured and tested to conform with industry classifications below:
Standard | Description | Application |
---|---|---|
ISO 513:2004 | Technical specifications for tungsten carbide | Basis for all national and regional standards |
ASTM B777 | WC-Co composition analysis | North America reference |
GB/T 4861-2006 | Chinese standard | Widely adopted in Asia markets |
IS 6475:1971 | Indian standard | Buttons for subcontinental buyers |
BS EN ISO 513:2019 | British-European standard | Increasingly used alongside ISO |
These prescribe subsets of tungsten carbide (WC) tool material grouped into P/M-grades (powder metallurgy methods) primarily differentiated by cobalt (Co) binder content and grain size, for example:
Carbide grade P/M-01 contains average WC grain size 1 μm with Co binder percent < 6%
Operators select appropriate specification for regional procurement ensuring the buttons reliably withstand mining stresses.
Carbide Button Sizes
Carbide buttons for rock drills and crushing machinery come in specific dimensions measured by volume, rather than dimensions. Common sizes include:
- 16mm3
- 20mm3
- 25mm3
- 32mm3
Larger blocky inserts with 50mm3 volume also available for severely impacting applications like underground drilling of hardrock.
Dimensional values roughly translate to:
- 16mm3 = 4.5mm diameter x 5.5mm thickness
- 32mm3 = 6mm diameter x 6.5mm thickness
Check manufacturers’ catalogues to identify exact button dimensions meeting required size specifications. Match with corresponding drill bit shank diameters.
Grades of Carbide Buttons
Carbide grades differentiate based on proportion of key augmenting elements blended into the WC-matrix tailored to enhance certain properties crucial for particular rock characteristics and mining conditions.
Grade | Description | Properties Improved |
---|---|---|
C1/C2 | Pure tungsten carbide | Hardness and wear resistance |
C3 | + Titanium carbide | Highly abrasion resistant with chemical inertness |
C5 | + Tantalum/Niobium carbide | Tougher grades for high shock loads |
C6/C7 | Grain growth inhibitors | Thermal shock resistance |
C8/C9 | Fine grained < 1μm | Strength and wear resistance |
There exist over a hundred registered WC grades for varying industrial uses. Consult suppliers to select optimal grade for each drilling location based on:
- Rock hardness: granite, basalt, limestone
- Mineral content: quartz, silicates
- Compressive/tensile strength
- Level of abrasiveness: non-abrasive, semi, highly-abrasive
- Dust and moisture levels
Matching the carbide grade to actual field conditions ensures cost-effective drilling and maximum button lifespan.
Mining Applications of Carbide Buttons
Surface Mining
Rotary and percussion drills equipped with hardened steel, polycrystalline diamond compact (PDC) or tricone roller bit studded with carbide button inserts penetrate through overburden to access buried mineral deposits. Carbide buttons in bit crowns also aid mechanical rock fragmentation improving crusher throughput.
Certain surface mining mills use semi-autogenous grinding (SAG) systems containing large internally studded alloy or steel grinding drums with cemented carbide buttons. As slurry fills the rotating chamber, solid rocks churning violently inside get pulverized into fine particles by the strategic placement of carbide buttons across drum walls.
Underground Mining
Tunnel boring machines (TBM) designed for underground excavation feature disc cutters consisting rotating steel rings or chisels reinforced with rectangular cemented carbide button inserts. The carbide strikes and chips away at tunnel faces with enormous point loads while providing wear protection to cutter bodies.
Longwall shearers cutting coal in narrow underground galleries rely on tungsten carbide button-tipped cutting picks to continuously mine away long facings. Intense friction and temperatures rapidly degrade exposed steel surfaces. Carbide inserts limit wearing of vital ground-engaging picks.
Carbide Mining Button Suppliers
China, India and the United States represent the top producers of cemented carbide components. Major manufacturers and OEM suppliers of carbide button inserts include:
China
- ZhuZhou JingGang Cemented Carbide Co.
- Zhuzhou Better Tungsten Carbide Co.
- Zhuzhou Kelite Tungsten Carbide Co.
- Chengdu Tool Research Institute
India
- Modi Carbide Tools
- Volzhsky Abrasive Works
- Midas Minmet
United States
- Rockmore Carbide Buttons
- CR Industries
- Western Drill Toolings
Many also retail through online stores on platforms like Alibaba and Made-in-China. Resellers offer small-batch trial samples before bulk orders.
Costs of Carbide Button Inserts
Carbide mining buttons approximately cost USD 5 to 9 based on:
- Size: bigger 32mm3 buttons nearly double in price versus smaller 16mm3 versions
- Grade: premium abrasion-resistant C3 grade 10-15% costlier than basic C1 grade
- Quantity ordered: bulk orders above 5000 pieces qualify for discounted rates
- Regional tariffs: China carbide prices remain very competitive compared to American and EU suppliers
Parameter | Price Range (USD per piece) |
---|---|
By Size → | |
16mm3 | 4.0 – 6.0 |
20mm3 | 5.5 – 8.0 |
25mm3 | 6.0 – 9.0 |
32mm3 | 7.5 – 12.0 |
50mm3 | 13.0 – 18.0 |
By Grade → | |
C1/C2 | 5.0 – 7.0 |
C3 | 6.5 – 9.0 |
C5 | 7.0 – 10.0 |
By Order Quantity → | |
< 1000 pieces | 8.0 – 15.0 |
1000 – 5000 pieces | 6.0 – 10.0 |
> 5000 pieces | 4.0 – 8.0 |
Table 6: Carbide mining button price estimates
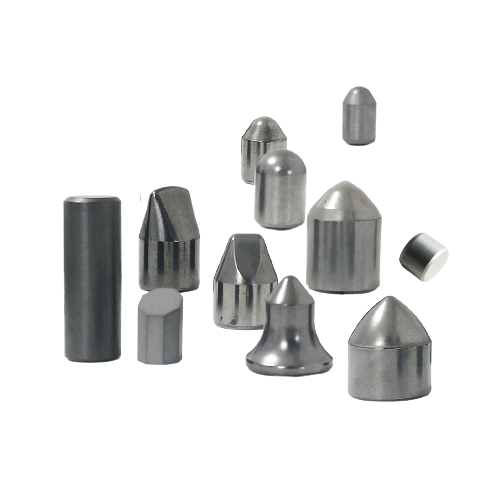
Pros and Cons of Carbide Buttons
Advantages | Disadvantages |
---|---|
Extreme hardness resists abrasive wear | Vulnerable to chemical corrosion |
Metal-to-rock contact minimizes drilling overheating | Brittle nature risks breakage and cracking |
High compressive strength sustains heavy loads | High tungsten content increases manufacturing costs |
Multiple grade options exist for varying conditions | Slightly lower temperature limit than other superalloys |
Recyclable composition via powder processing | No standard industry sizes unlike roller cone inserts |
Table 7: Comparison of carbide button pros and cons
Expert Tips for Maximizing Carbide Button Performance
Veteran mining engineers and drill operators provide field-based best practices for optimizing carbide button application:
Avoid sudden drilling overload
Gradually engage buttons into hard rock to avoid immediate stress-induced cracking leading to premature wear once underlying steel gets exposed. Let percussion hammers or roller cone teeth with carbide buttons gently nip the rock surface before increasing indentation pressure.
Select buttons as per rock drillability
Softer sedimentary rocks like lignite coal and limestone require only basic C1 carbide grade to minimize costs. Harder igneous/metamorphic types containing higher silica/quartz demand premium ultra-fine grained carbide grades with inclusions of titanium and niobium carbides boosting wear performance.
Use larger buttons only when necessary
Larger diameter inserts undoubtedly demonstrate better impact resistance over smaller types. However the higher per piece price makes economic sense only in highly abrasive conditions that cause rapid wear-through of small buttons exposing the steel matrix. Appropriately grade the carbide instead of arbitrarily increasing size.
Preheat in extremely cold environments
Frictional heating from abrasive interaction with rocks somewhat compensates for freezing temperatures in regions like Alaska or Scandinavia. Still, experts recommend gentle preheating using propane torches for several minutes before engaging the bits at very high RPM, minimizing possibility of thermal shock cracks.
Clean regularly to prevent clogging
Dust mixed water forms abrasive slurry that sticks between button edges filling gaps in bit heads. Regular manual cleaning or high-pressure air jet washing prevents clogging ensuring smooth transfer of percussive loads and cooling liquids across drill bits.
Reuse despite slight wear Ideally swap out buttons once wear reaches 0.5mm depth. However given their high price, operators reuse inserts despite 1mm wear until overall diameter reduces by 2mm. Such extended usage possible only in stable homogeneous formations. Else rock drillability suffers severely.
FAQ
Q: Why carbide for mining buttons versus other materials?
- Carbide possesses ideal combination of hardness close to diamond plus metallic toughness necessary for drilling integrity under prolonged demanding use in heavy industries like mining. Ceramics like silicon nitride score higher on hardness but tend to be brittle. Stainless steel offers toughness at expense of strength.
Q: What causes carbide buttons to wear out?
- Abrasion from silica/quartz particles in rocks rub away binder cobalt first exposing porous tungsten carbide matrix that accelerates wear. High temperatures soften cobalt further. Stressful impact eventually causes cracks initiating breakage.
Q: How to check original carbide button quality?
- Procuring buttons directly from branded manufactures is recommended for assured material quality. For third-party sourced buttons, test microstructure for fine uniform WC grain size under electron microscope. Next use Rockwell indentation to verify hardness figures fall within expected range for the stated carbide grade. These checks certify minimal quality standards are met.
Q: What are renewable carbide button bits?
- Special drill bits where loose buttons sit recessed into cross holes along steel matrix. As exposed buttons erode with use, rotation uncovers fresh buttons. This renewal reduces downtimes associated with replacing entire bits. However loose button movement risks uneven wear. Price also remains higher.
Q: Can we reuse worn carbide buttons?
- Yes, recycling permits reuse. Worn inserts containing at least 30% carbon undergo dissolution methods separating tungsten intermediates like APT/ADT for powders while tungsten itself gets reduced and carburized back into fresh cemented carbide feedstock for producing new buttons via powder metallurgy route.
Q: Do carbide grades vary across mining sectors?
- Coal softer than metal mines which themselves drill less abrasive ores than non-metallic minerals or aggregate quarries. Hence basic grades with 6% cobalt binder like C1 or C2 commonly installed in shearer drums should suffice for coal whereas highest titanium-niobium reinforced ultrafine grades like C8 or C9 necessary for quarry work.