Overview of Carbide Lathe Inserts
Carbide lathe inserts are crucial components in metalworking, especially in precision machining and cutting applications. These inserts, made from various grades of carbide, are designed to withstand high-speed operations, extreme temperatures, and the demands of repetitive machining tasks. Let’s dive deep into the world of carbide lathe inserts, explore their types, applications, material properties, and much more.
Types of Carbide Lathe Inserts
Carbide lathe inserts come in a variety of types, each suited for specific machining tasks and materials. Understanding these types is key to selecting the right insert for your needs.
Insert Type | Description |
---|---|
CNGP | CNGP inserts are double-sided with a positive rake angle, ideal for light finishing operations. |
DNMG | DNMG inserts feature a 55-degree diamond shape, versatile for both finishing and roughing applications. |
TNMG | TNMG inserts have a triangular shape with a negative rake, perfect for heavy-duty cutting. |
WNMG | WNMG inserts are trigon-shaped, offering six cutting edges for increased efficiency in both roughing and finishing. |
VNMG | VNMG inserts are 35-degree diamond-shaped, excellent for profiling and finishing. |
SNMG | SNMG inserts are square-shaped, commonly used for general-purpose turning and facing. |
RCMT | RCMT inserts are round-shaped, providing smooth finishes and ideal for interrupted cuts. |
SCMT | SCMT inserts have a square shape with a positive rake, suitable for light to medium machining. |
TCMT | TCMT inserts are triangular with a positive rake, used for light-duty cutting and fine finishing. |
CCMT | CCMT inserts have a 7-degree relief angle, used for finishing and medium machining tasks. |
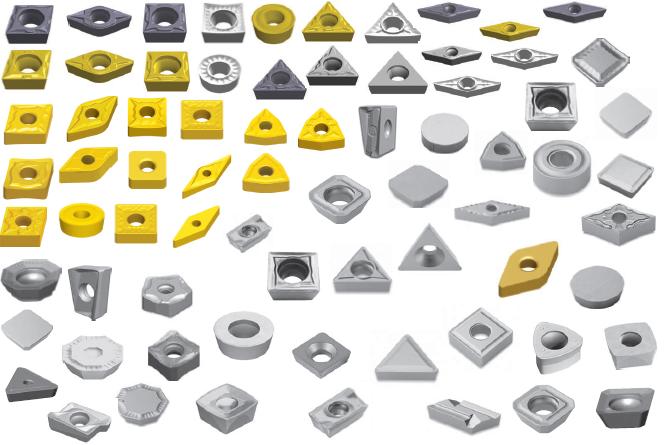
Applications of Carbide Lathe Inserts
Carbide lathe inserts are used across various industries, from automotive to aerospace, owing to their durability and precision. Here’s a look at the typical applications.
Application | Description |
---|---|
Automotive | Used for machining engine components, transmission parts, and other critical automotive parts. |
Aerospace | Essential for manufacturing aircraft components, ensuring precision and durability. |
Medical Devices | Used in producing high-precision medical instruments and implants. |
Oil and Gas | Employed in the production of drilling equipment and pipeline components. |
General Engineering | Suitable for a wide range of engineering applications, from small machine parts to large industrial equipment. |
Mold and Die | Ideal for creating molds and dies due to their high wear resistance and precision. |
Power Generation | Used in the manufacturing of turbines and other power generation equipment. |
Heavy Equipment | Essential for producing components used in heavy machinery and construction equipment. |
Railway | Utilized in the production of railway components, ensuring longevity and reliability. |
Electronics | Used for machining parts for electronic devices, requiring high precision and smooth finishes. |
Material Properties of Carbide Lathe Inserts
Understanding the material properties of carbide lathe inserts helps in selecting the right insert for the job. Let’s explore the key properties.
Property | Description |
---|---|
Hardness | Carbide inserts are extremely hard, with a hardness typically around 90 HRA, making them suitable for cutting hard materials. |
Toughness | Despite their hardness, carbide inserts also offer good toughness, allowing them to resist chipping and breaking under high-stress conditions. |
Wear Resistance | High wear resistance ensures long tool life and consistent performance over extended use. |
Thermal Stability | Carbide inserts can withstand high temperatures generated during cutting, maintaining their hardness and performance. |
Chemical Stability | Resistant to oxidation and other chemical reactions, ensuring durability in various working environments. |
Compressive Strength | High compressive strength allows carbide inserts to handle heavy cutting loads without deformation. |
Thermal Conductivity | Good thermal conductivity helps in dissipating heat quickly, reducing the risk of thermal damage to the workpiece and the insert itself. |
Composition, Properties, and Characteristics of Carbide Lathe Inserts
The composition of carbide lathe inserts greatly influences their properties and performance. Here’s a breakdown of common compositions and their characteristics.
Composition | Properties | Characteristics |
---|---|---|
Tungsten Carbide (WC) | High hardness, wear resistance | Most common material, excellent for a wide range of applications |
Cobalt (Co) Binder | Adds toughness to the insert, improves impact resistance | Commonly used as a binder with tungsten carbide for added toughness |
Titanium Carbide (TiC) | Enhances wear resistance, particularly at high temperatures | Used in combination with WC for high-temperature applications |
Tantalum Carbide (TaC) | Improves hardness and thermal resistance | Adds strength and heat resistance, used in specialized applications |
Niobium Carbide (NbC) | Increases hardness and corrosion resistance | Used for specialized applications requiring high corrosion resistance |
Chromium Carbide (CrC) | Provides excellent oxidation resistance | Enhances the performance in high-temperature and oxidizing environments |
Vanadium Carbide (VC) | Increases wear resistance and toughness | Used to improve overall durability and performance of the insert |
Nickel (Ni) Binder | Enhances corrosion resistance, adds toughness | Used in applications where high corrosion resistance is required |
Molybdenum Carbide (MoC) | Adds hardness and thermal stability | Improves wear resistance and performance at high temperatures |
Silicon Carbide (SiC) | Provides extreme hardness and high thermal conductivity | Used for cutting extremely hard materials like ceramics and hardened steels |
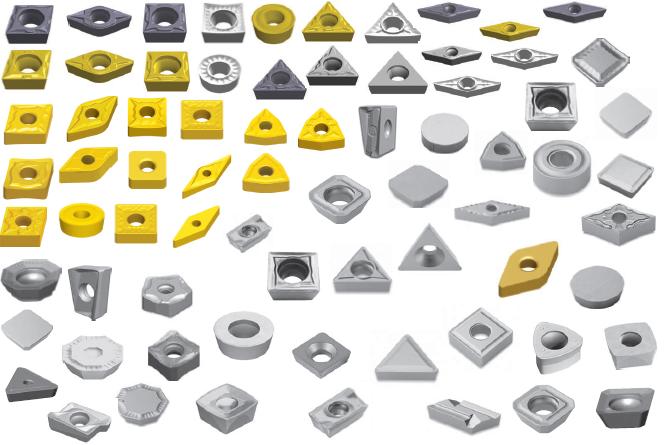
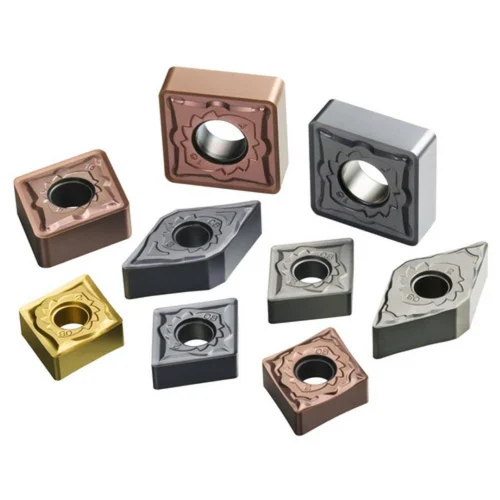
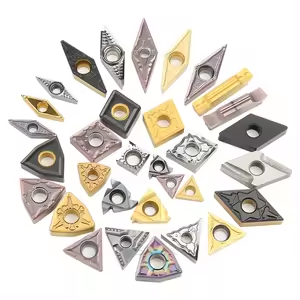
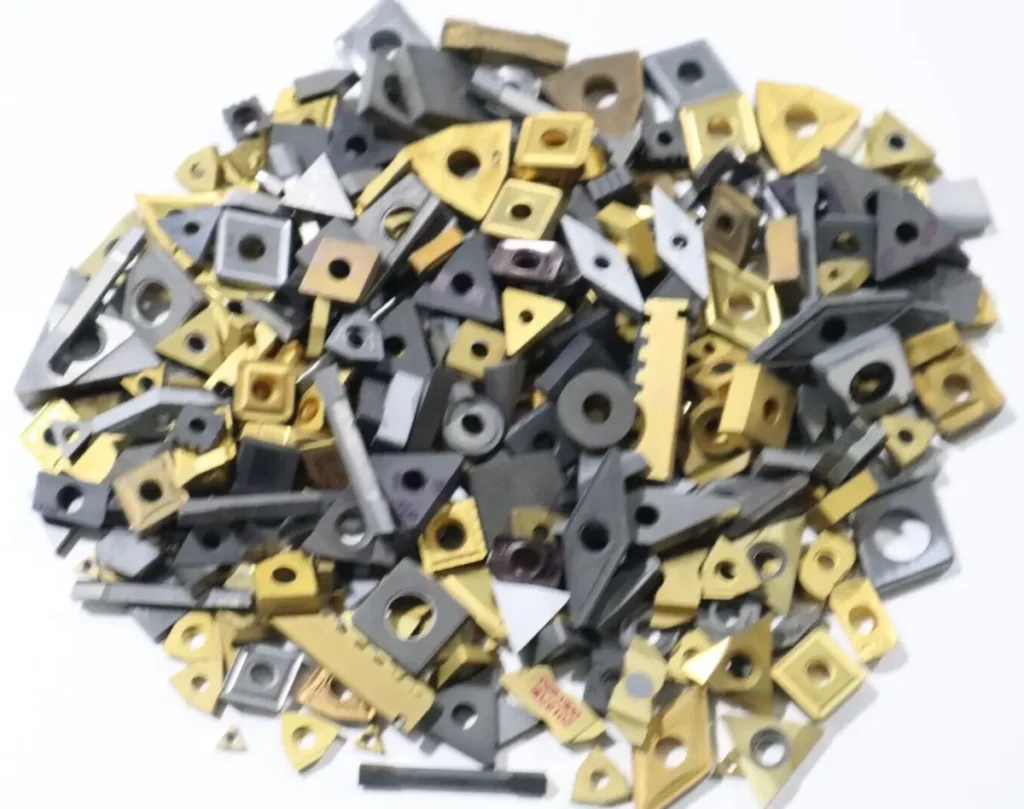
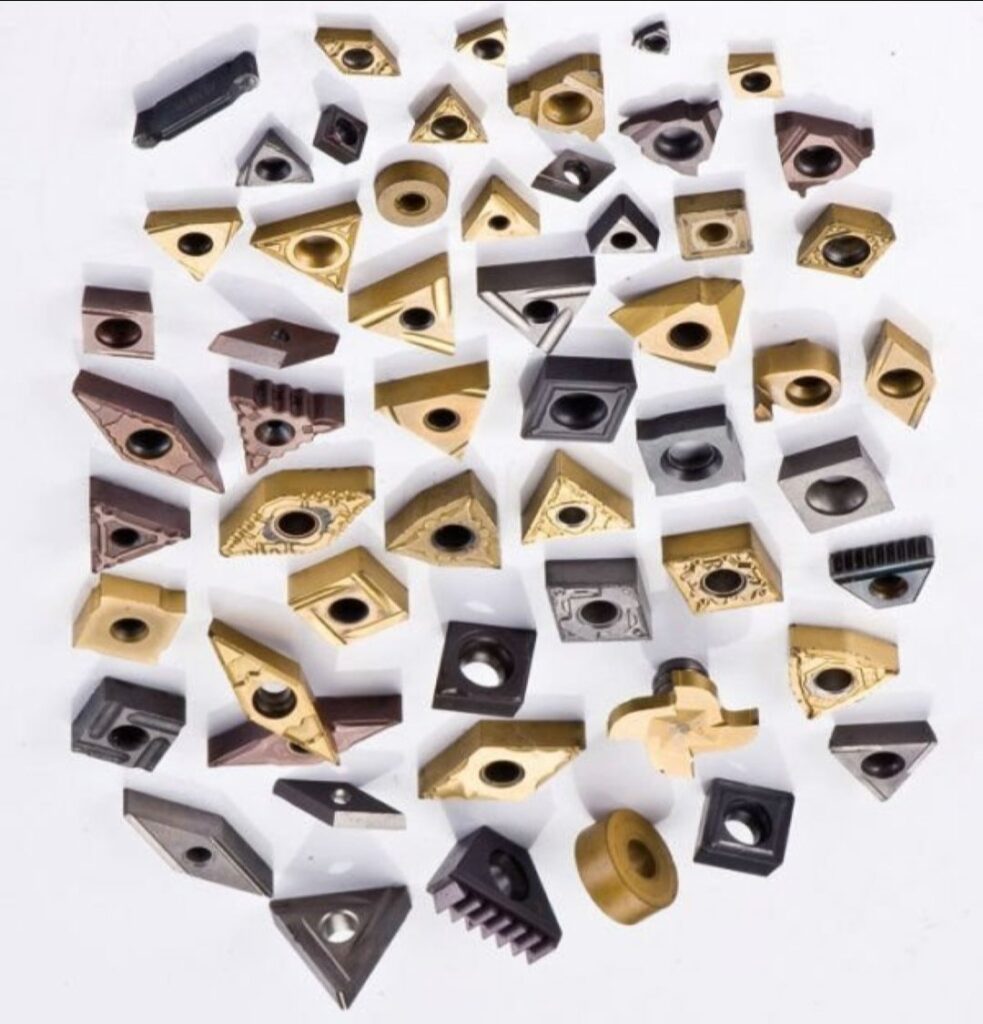
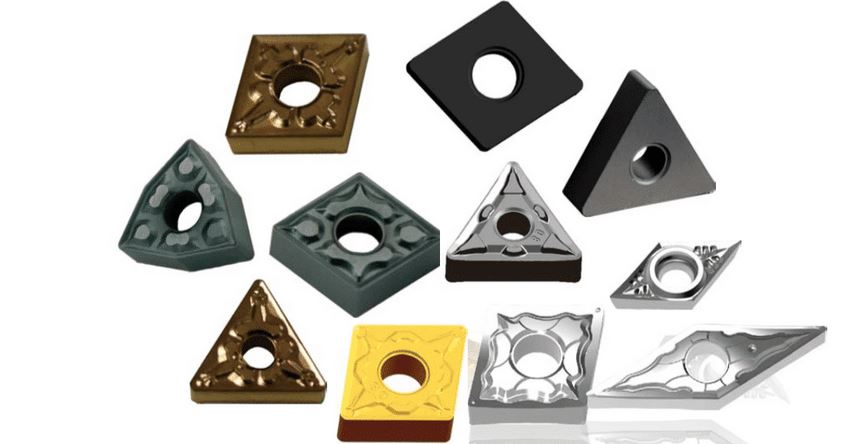
Hardness, Strength, and Wear Resistance
The performance of carbide lathe inserts is determined by their hardness, strength, and wear resistance. Here’s a detailed comparison.
Parameter | Description |
---|---|
Hardness (HRA) | Typically ranges from 85 to 93 HRA, ensuring the ability to cut through tough materials. |
Compressive Strength | High compressive strength allows inserts to handle heavy loads without deforming. |
Wear Resistance | Exceptional wear resistance ensures long tool life and consistent performance over time. |
Toughness | Balances hardness with the ability to resist chipping and breaking under high-stress conditions. |
Thermal Stability | Maintains performance even at high temperatures generated during cutting. |
Chemical Resistance | Resistant to oxidation and other chemical reactions, ensuring durability in various environments. |
Specifications, Sizes, Shapes, and Standards
Carbide lathe inserts come in various specifications, sizes, shapes, and standards. Here’s an overview to help you choose the right insert.
Specification | Description |
---|---|
ISO Standard | International standards for insert shapes, sizes, and tolerances, ensuring compatibility and interchangeability. |
ANSI Standard | American standards specifying insert dimensions, geometry, and application guidelines. |
Shape | Common shapes include square (S), triangular (T), diamond (D), round (R), and trigon (W), each suited for different applications. |
Size | Sizes vary to fit different tool holders and accommodate various cutting depths and feed rates. |
Thickness | Thickness options ensure inserts can handle different cutting forces and provide desired rigidity. |
Corner Radius | Available in various radii to influence the finish and strength of the cutting edge. |
Coating | Inserts may have coatings like TiN, TiAlN, or CVD for enhanced wear resistance and performance. |
Chipbreaker | Features designed into the insert to control chip formation and evacuation, improving cutting efficiency. |
Suppliers and Pricing Details
Several reputable suppliers provide high-quality carbide lathe inserts. Pricing varies based on the type, material, and quantity. Here’s a snapshot of some key suppliers and pricing details.
Supplier | Product Range | Average Pricing | Website |
Sandvik Coromant | Wide range of carbide inserts for various applications | $10 – $50 per insert | sandvik.coromant.com |
Kennametal | High-performance carbide inserts for industrial use | $15 – $60 per insert | kennametal.com |
Seco Tools | Versatile inserts with advanced coatings and geometries | $20 – $70 per insert | secotools.com |
Mitsubishi Materials | Innovative carbide inserts for various machining needs | $12 – $55 per insert | mitsubishicarbide.com |
Iscar | Comprehensive range of carbide inserts for multiple industries | $18 – $65 per insert | iscar.com |
Sumitomo Electric | High-quality inserts with advanced materials and coatings | $15 – $60 per insert | sumitomotool.com |
Taegutec | Cost-effective carbide inserts with reliable performance | $10 – $50 per insert | taegutec.com |
Walter Tools | Durable inserts for demanding machining operations | $20 – $70 per insert | walter-tools.com |
Tungaloy | Versatile and high-performance inserts for various applications | $18 – $65 per insert | tungaloy.com |
Kyocera | Innovative solutions with high-precision carbide inserts | $15 – $55 per insert | kyoceramicrotools.com |
Selecting the Right Carbide Lathe Inserts
Choosing the right carbide lathe insert can significantly impact your machining efficiency and output quality. Here’s how to make the right choice.
Factor | Consideration |
---|---|
Material to be Machined | Different materials require different insert properties. For example, hard steels need high wear resistance, while softer metals require high toughness. |
Machining Operation | Whether you’re roughing, finishing, or profiling, each operation has specific insert requirements for optimal performance. |
Insert Geometry | The shape and edge geometry of the insert affect the cutting forces, chip control, and surface finish. |
Tool Holder Compatibility | Ensure the insert fits your existing tool holders and machine setup. |
Cutting Parameters | Consider the cutting speed, feed rate, and depth of cut. Different inserts are designed to perform optimally under specific conditions. |
Coating | Coated inserts offer enhanced wear resistance and performance in challenging environments. |
Cost | Balance between the insert cost and its expected tool life and performance benefits. |
Supplier Reputation | Choose suppliers known for quality and reliability to ensure consistent performance. |
Comparing Advantages and Limitations
Different carbide lathe inserts offer various advantages and limitations. Understanding these can help you make an informed decision.
Insert Type | Advantages | Limitations |
---|---|---|
CNGP | Excellent for fine finishing, good chip control | Limited to light cutting applications |
DNMG | Versatile, suitable for both roughing and finishing | May not be optimal for very heavy cuts |
TNMG | Durable, handles heavy-duty cutting, multiple cutting edges | Higher cutting forces, may require more powerful machines |
WNMG | High efficiency with multiple cutting edges, suitable for a range of applications | Complex geometry may lead to higher costs |
VNMG | Ideal for precision profiling and finishing | Limited to lighter cuts, higher risk of breakage |
SNMG | Good for general-purpose use, strong cutting edges | Less efficient chip control compared to specialized inserts |
RCMT | Provides smooth finishes, handles interrupted cuts well | Round shape limits cutting depth and precision |
SCMT | Suitable for light to medium machining, good surface finish | Not ideal for heavy cuts |
TCMT | Excellent for light-duty cutting, precise finishes | Limited to lighter applications, higher risk of breakage |
CCMT | Versatile, good for both finishing and medium machining | May not handle very heavy cuts effectively |
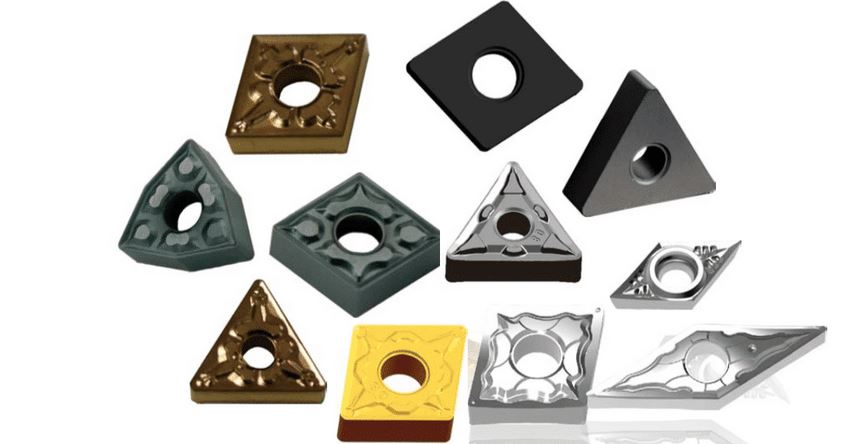
FAQ
What are carbide lathe inserts used for?
Carbide lathe inserts are used for precision machining tasks, including turning, facing, profiling, and finishing. They offer high wear resistance and can handle high-speed operations.
How do I choose the right carbide insert?
Consider factors like the material to be machined, the type of operation, insert geometry, tool holder compatibility, cutting parameters, coating, cost, and supplier reputation.
What are the common types of carbide lathe inserts?
Common types include CNGP, DNMG, TNMG, WNMG, VNMG, SNMG, RCMT, SCMT, TCMT, and CCMT, each suited for specific applications and materials.
Why are carbide inserts preferred in machining?
Carbide inserts are preferred for their high hardness, wear resistance, toughness, and thermal stability, making them suitable for a wide range of machining tasks.
How long do carbide inserts last?
The lifespan of carbide inserts depends on factors like the material being machined, cutting parameters, and the type of insert. They generally offer a longer tool life compared to other materials.
Can carbide inserts be re-sharpened?
Some carbide inserts can be re-sharpened, but it’s often more cost-effective to replace them due to the precision required in the sharpening process.
What coatings are available for carbide inserts?
Common coatings include Titanium Nitride (TiN), Titanium Aluminum Nitride (TiAlN), and Chemical Vapor Deposition (CVD) coatings, enhancing wear resistance and performance.
Are there standards for carbide inserts?
Yes, there are ISO and ANSI standards that define the dimensions, geometry, and application guidelines for carbide inserts, ensuring compatibility and interchangeability.
Where can I buy carbide inserts?
Reputable suppliers like Sandvik Coromant, Kennametal, Seco Tools, Mitsubishi Materials, Iscar, Sumitomo Electric, Taegutec, Walter Tools, Tungaloy, and Kyocera offer high-quality carbide inserts.
What are the advantages of coated carbide inserts?
Coated carbide inserts offer enhanced wear resistance, longer tool life, better heat dissipation, and improved performance in challenging machining environments.