Introduction
Definition of carbide inserts carbide rods
Carbide inserts and carbide rods are essential components in the field of metal machining. These tools are made from a combination of tungsten carbide and cobalt, resulting in a material that is incredibly hard and wear-resistant. Carbide inserts are small cutting tools that are used in milling, turning, and drilling applications. They are designed to withstand high temperatures and provide excellent cutting performance. Carbide rods, on the other hand, are solid cylindrical bars that are used as tool blanks for creating various cutting tools. They can be shaped and ground into different forms, such as end mills, drills, and reamers. Both carbide inserts and carbide rods play a crucial role in enhancing productivity and precision in metalworking industries.
Importance of Carbide Inserts and Carbide Rods in Manufacturing
Carbide inserts and carbide rods play a crucial role in the manufacturing industry. They are essential tools used in various machining processes, such as milling, turning, and drilling. These inserts and rods are made from a durable and wear-resistant material called carbide, which is a combination of tungsten carbide and cobalt. The importance of carbide inserts and carbide rods lies in their ability to provide high precision, efficiency, and longevity in machining operations. They are known for their exceptional hardness and resistance to heat, making them ideal for cutting, shaping, and forming materials like steel, cast iron, and aluminum. Additionally, carbide inserts and carbide rods offer superior cutting performance, resulting in improved productivity and reduced costs for manufacturers. With their versatility and reliability, carbide inserts and carbide rods have become indispensable components in the manufacturing process, contributing to the production of high-quality and precise products.
Overview of the Article
In the article titled ‘Carbide Inserts Carbide Rods’, the author provides an in-depth overview of the topic. The article explores the various applications and uses of carbide inserts and carbide rods in different industries. It delves into the manufacturing process, highlighting the materials used and the techniques employed to produce high-quality carbide inserts and rods. Additionally, the article discusses the advantages and benefits of using carbide inserts and rods, such as their exceptional hardness, durability, and resistance to wear and heat. The author also examines the different types and grades of carbide inserts and rods available in the market, providing insights into their specific features and applications. Overall, this article serves as a comprehensive guide for readers seeking to understand the significance and impact of carbide inserts and carbide rods in various industrial sectors.
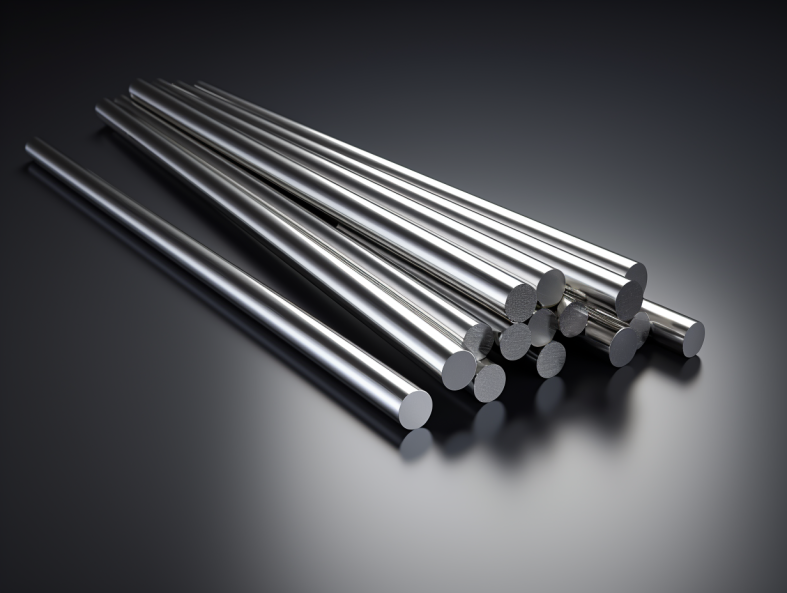
Properties of carbide inserts carbide rods
Hardness and Wear Resistance
Carbide inserts and carbide rods are known for their exceptional hardness and wear resistance. These materials are widely used in various industries, including machining, metalworking, and mining. The hardness of carbide inserts and rods is significantly higher than that of traditional steel materials, allowing them to withstand high temperatures and intense pressure. Additionally, their wear resistance properties make them ideal for applications that involve cutting, drilling, and milling. The use of carbide inserts and rods not only improves the efficiency and performance of cutting tools but also extends their lifespan, reducing the need for frequent replacements. Overall, the hardness and wear resistance of carbide inserts and carbide rods make them indispensable components in many industrial processes.
Heat Resistance
Carbide inserts and carbide rods are known for their exceptional heat resistance properties. When subjected to high temperatures, these materials exhibit minimal deformation and maintain their structural integrity. This makes them ideal for applications that involve intense heat, such as metal cutting and machining processes. The heat resistance of carbide inserts and carbide rods not only ensures their durability but also enhances the performance and efficiency of the tools they are used in. With their ability to withstand extreme temperatures, these materials contribute significantly to the longevity and reliability of various industrial operations.
Chemical Stability
Chemical stability refers to the ability of a material to resist chemical reactions or changes when exposed to different substances or environments. In the case of carbide inserts and carbide rods, their chemical stability is a crucial factor in determining their performance and durability. These materials are designed to withstand harsh conditions and resist chemical corrosion, making them ideal for various industrial applications. The high chemical stability of carbide inserts and carbide rods ensures their longevity and reliability, even in demanding operating conditions. This attribute allows them to maintain their structural integrity and cutting efficiency, providing consistent and precise results. Overall, the exceptional chemical stability of carbide inserts and carbide rods makes them indispensable tools in the manufacturing and machining industries.
Types of Carbide Inserts
Turning Inserts
Turning inserts are an essential tool in the field of machining. These inserts are specifically designed to be used in turning operations, where a cutting tool is used to remove material from a workpiece. Carbide inserts, also known as carbide rods, are widely used in turning applications due to their exceptional hardness and durability. They are made from a combination of tungsten carbide and cobalt, which results in a material that can withstand high temperatures and maintain its cutting edge for a longer period of time. Carbide inserts offer superior performance and precision, making them the preferred choice for turning operations in various industries such as automotive, aerospace, and manufacturing. With their ability to provide excellent surface finish and extended tool life, carbide inserts play a crucial role in achieving efficient and cost-effective machining processes.
Milling Inserts
Milling inserts are essential tools used in machining operations to achieve precision and efficiency. These inserts, made of carbide, provide superior cutting performance and durability. Carbide inserts are widely used in milling applications due to their hardness and resistance to wear. They are designed to fit into milling cutters and are available in various shapes and sizes to suit different machining needs. With their sharp cutting edges and excellent heat resistance, carbide inserts enable smooth and accurate milling operations, resulting in high-quality finished products. Whether it’s roughing, finishing, or contouring, milling inserts play a crucial role in enhancing productivity and achieving optimal machining outcomes.
Drilling Inserts
Drilling inserts are an essential component in the field of machining. These inserts, made of carbide, are designed to be inserted into drilling tools to enhance their performance and durability. Carbide inserts are known for their superior hardness and wear resistance, making them ideal for drilling applications. With their sharp cutting edges and excellent heat resistance, these inserts can efficiently remove material and create precise holes. Whether it’s drilling through metal, wood, or other materials, carbide inserts offer a reliable and efficient solution. The use of carbide inserts in drilling operations ensures increased productivity and extended tool life, making them a popular choice among professionals in the industry.
Applications of Carbide Inserts
Metal Cutting
Metal Cutting is a crucial process in various industries, and carbide inserts and carbide rods play a significant role in this field. These cutting tools are made from high-quality carbide materials that offer exceptional hardness and wear resistance. With their sharp edges and precise cutting capabilities, carbide inserts and carbide rods are widely used in machining operations to cut through tough materials like steel, cast iron, and stainless steel. They provide excellent cutting performance, improved tool life, and higher productivity. Whether it’s turning, milling, or drilling, carbide inserts and carbide rods are essential tools for achieving accurate and efficient metal cutting operations.
Woodworking
Woodworking is a versatile craft that requires precision and quality tools. When it comes to cutting and shaping wood, carbide inserts and carbide rods are essential components. These durable and long-lasting materials are designed to withstand the demands of woodworking, providing clean and accurate cuts. Whether you’re crafting intricate designs or working on large-scale projects, carbide inserts and carbide rods offer the reliability and performance needed to achieve professional results. With their superior strength and hardness, they can handle the toughest of woods with ease. So, if you’re looking to enhance your woodworking skills and take your projects to the next level, consider incorporating carbide inserts and carbide rods into your toolkit.
Mining and Construction
Mining and construction industries heavily rely on carbide inserts and carbide rods for their various applications. These high-performance tools are essential for drilling, cutting, and shaping hard materials such as rocks, concrete, and metals. Carbide inserts and rods offer superior hardness, wear resistance, and thermal stability, making them ideal for demanding mining and construction projects. With their exceptional strength and durability, these tools ensure efficient and precise operations, resulting in increased productivity and reduced downtime. Whether it’s excavating, tunneling, or building structures, carbide inserts and carbide rods play a crucial role in the success of mining and construction endeavors.
Manufacturing Process of Carbide Inserts
Powder Preparation
Powder preparation is a crucial step in the manufacturing of carbide inserts and carbide rods. It involves the careful selection and blending of various raw materials to create a uniform and high-quality powder mixture. The raw materials, such as tungsten carbide and cobalt, are processed and ground to specific particle sizes to ensure optimal performance and durability. This finely tuned powder mixture is then ready for the next stage of the manufacturing process, where it will be pressed, sintered, and shaped into the desired carbide inserts and carbide rods.
Mixing and Blending
Mixing and blending play a crucial role in the production of carbide inserts and carbide rods. These processes involve combining different materials and ensuring a uniform distribution of particles. By carefully controlling the mixing and blending parameters, manufacturers can achieve the desired composition and properties of the carbide products. Additionally, the mixing and blending processes help to eliminate any impurities and enhance the overall quality of the final products. With advanced equipment and expertise, companies can optimize the mixing and blending techniques to meet the specific requirements of their customers. Overall, the efficient mixing and blending of materials contribute to the production of high-quality carbide inserts and carbide rods.
Pressing and Sintering
Pressing and sintering are two important processes in the production of carbide inserts and carbide rods. Pressing involves compacting the powdered carbide material into a desired shape using high pressure. This process helps to ensure that the carbide inserts and rods have the necessary strength and durability. Sintering, on the other hand, involves heating the pressed carbide material to a high temperature in a controlled atmosphere. This causes the particles to bond together, resulting in a solid and dense product. The pressing and sintering processes play a crucial role in achieving the desired properties and performance of carbide inserts and carbide rods.
Advantages and Disadvantages of Carbide Inserts
Advantages
Carbide inserts and carbide rods offer numerous advantages in various industries. One of the key advantages is their exceptional hardness, which allows them to withstand high temperatures and heavy loads. This makes them ideal for applications that involve cutting, drilling, and milling. Additionally, carbide inserts and rods have excellent wear resistance, ensuring prolonged tool life and reducing the need for frequent replacements. Moreover, they provide superior precision and accuracy, resulting in high-quality finished products. Furthermore, carbide inserts and rods are known for their corrosion resistance, making them suitable for use in harsh environments. Overall, the advantages of carbide inserts and carbide rods make them indispensable tools for enhancing productivity and efficiency in industrial processes.
Disadvantages
Carbide inserts and carbide rods offer numerous advantages in various industrial applications. However, it is important to consider the potential disadvantages that come with their use. One major disadvantage of carbide inserts and carbide rods is their high cost. Compared to other cutting tools, carbide inserts and carbide rods can be significantly more expensive, making them less accessible for some businesses. Additionally, carbide inserts and carbide rods are brittle and can be prone to chipping or breakage under heavy loads or improper handling. This fragility can lead to increased maintenance and replacement costs. Despite these disadvantages, with proper care and usage, carbide inserts and carbide rods can still provide exceptional performance and longevity in cutting and machining operations.
Comparison with Other Cutting Tools
Carbide inserts and carbide rods are widely used in the manufacturing industry for cutting and machining applications. When compared to other cutting tools, carbide inserts and carbide rods offer several advantages. Firstly, they have a higher hardness and wear resistance, which allows for longer tool life and increased productivity. Additionally, carbide inserts and carbide rods have excellent heat resistance, enabling them to withstand high cutting speeds and temperatures. Moreover, they provide superior cutting performance and precision, resulting in improved surface finish and dimensional accuracy. Overall, the use of carbide inserts and carbide rods in cutting applications ensures efficient and cost-effective machining processes.