When it comes to machining and metal cutting, the tools you choose can make all the difference in the efficiency, precision, and overall success of your project. Among these essential tools, carbide inserts stand out due to their incredible hardness, heat resistance, and wear resistance. If you’re diving into the world of carbide inserts, whether as a buyer, engineer, or simply someone interested in the intricacies of manufacturing, this guide is here to provide you with a deep understanding of the topic, including everything from the basics of what carbide inserts are to the specifics of manufacturers, types, and applications.
Overview of Carbide Inserts
Carbide inserts are cutting tools made from sintered carbide material, which typically consists of tungsten carbide and cobalt. These inserts are used in machining operations for cutting, shaping, and finishing metal and other materials. Due to their exceptional hardness and durability, carbide inserts offer significant advantages over traditional high-speed steel (HSS) tools, particularly in demanding industrial environments where precision and longevity are critical.
Carbide inserts are engineered to perform specific tasks in various machining operations, such as turning, milling, drilling, and threading. Their superior wear resistance and ability to maintain a sharp cutting edge for longer periods make them indispensable in industries such as automotive, aerospace, and heavy equipment manufacturing.
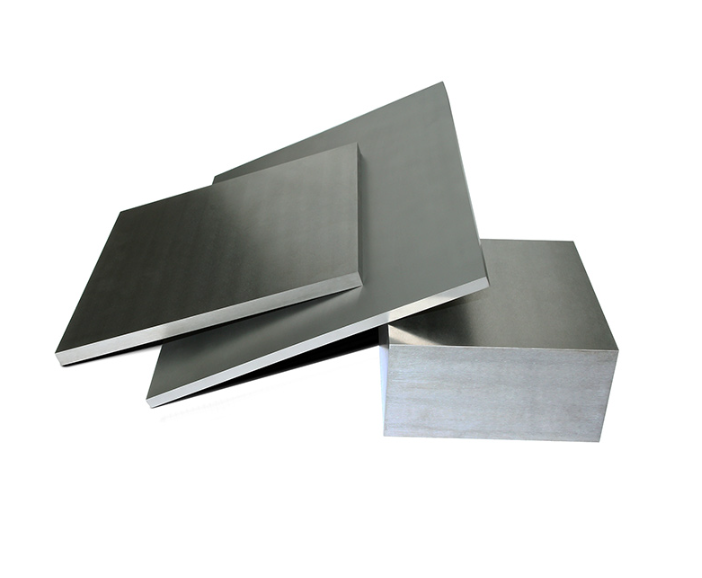
Function of Carbide Inserts
Carbide inserts serve as the primary cutting interface between the workpiece and the machine tool. Their primary functions include:
- Cutting and Shaping: Carbide inserts are used to remove material from a workpiece, shaping it into the desired form.
- Surface Finishing: They ensure a smooth finish on the machined part, reducing the need for secondary operations.
- Increased Tool Life: Compared to other materials, carbide inserts offer longer tool life due to their resistance to wear and high temperatures.
- Precision and Accuracy: They allow for tight tolerances and precise cuts, which are essential in industries that require high levels of accuracy.
Types of Carbide Inserts
Carbide inserts come in various shapes, sizes, and grades, each designed for specific applications. The choice of insert depends on factors like the material being machined, the type of operation, and the desired finish. Below, we present a table that outlines some of the most common types of carbide inserts.
Type of Carbide Inserts | Shape | Common Applications | Description |
---|---|---|---|
CNMG | Square | Turning, Roughing | Versatile, often used for rough turning and facing |
DNMG | Diamond | Finishing, Profiling | Ideal for profiling and finishing applications |
VNMG | Diamond | Light Machining, Finishing | Used for light cuts, excellent for finish turning |
WNMG | Trigon | Medium to Heavy Turning | Suitable for general-purpose machining |
CCMT | Square | Precision Turning, Boring | Best for small-diameter, fine machining tasks |
SCMT | Square | Medium Machining | Used in medium machining, offers good stability |
RCMT | Round | Heavy Roughing | Ideal for heavy-duty roughing and interrupted cuts |
APKT | Rectangle | Milling | Widely used in face milling, good chip control |
TPMT | Triangle | Finishing | Great for light finishing operations |
SNMG | Square | Roughing | Standard insert for general-purpose turning |
Carbide Inserts Applications
Carbide inserts are versatile and can be used across a range of industries and applications. The table below summarizes their typical uses in different machining operations:
Application | Description |
---|---|
Turning | Removing material from the outer diameter of a rotating workpiece. |
Milling | Removing material from a workpiece with a rotating tool, typically used for larger surfaces. |
Drilling | Creating round holes in a workpiece using a rotating tool. |
Boring | Enlarging existing holes with high precision. |
Threading | Creating threads on the internal or external surface of a workpiece. |
Grooving | Cutting narrow slots or grooves in a workpiece. |
Profiling | Machining complex contours or shapes on a workpiece. |
Parting | Cutting off sections of a workpiece. |
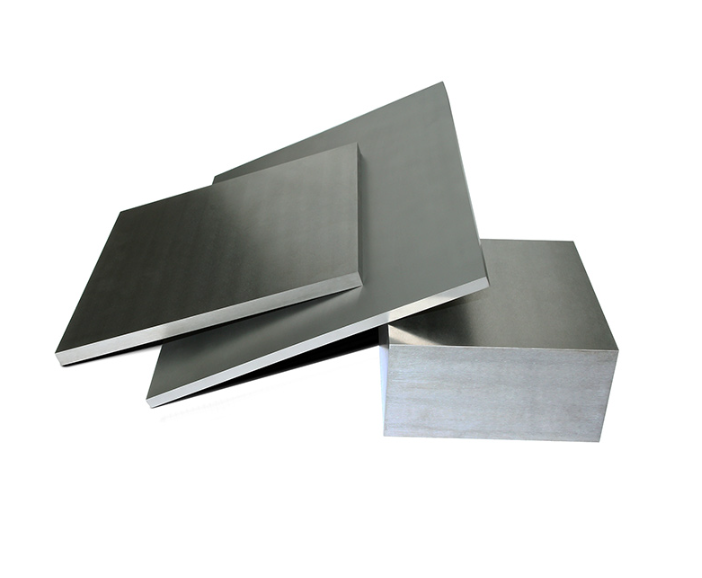
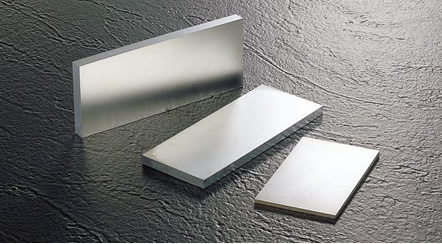
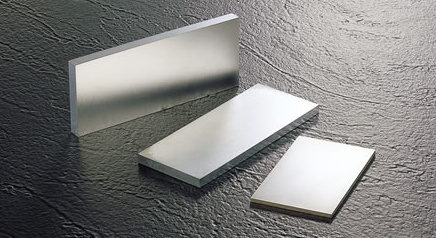
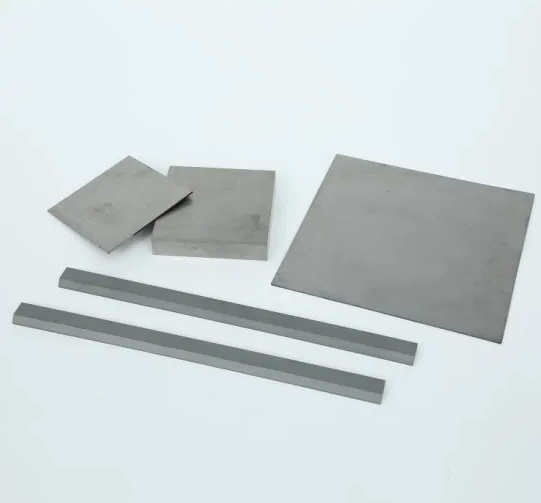
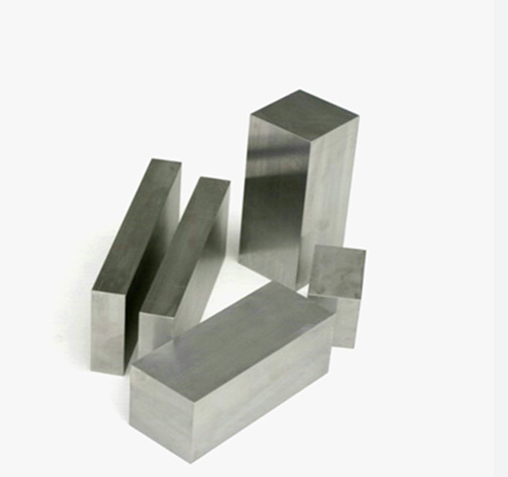
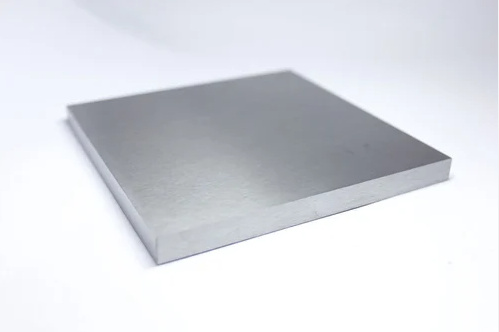
Material Properties of Carbide Inserts
Understanding the material properties of carbide inserts is crucial for selecting the right insert for your application. These properties determine the insert’s performance, durability, and suitability for different machining tasks.
Property | Description |
---|---|
Hardness | Typically measured in HRA or Vickers, indicating the resistance to deformation |
Toughness | The ability to absorb energy without fracturing, important for shock resistance |
Wear Resistance | Resistance to abrasion, crucial for tool longevity |
Thermal Stability | The ability to retain hardness and strength at elevated temperatures |
Chemical Stability | Resistance to chemical reactions with workpiece materials at high temperatures |
Composition, Properties, and Characteristics
Carbide inserts are composed of a matrix of tungsten carbide particles bound together by a metallic binder, usually cobalt. The ratio of tungsten carbide to cobalt, as well as the grain size of the carbide particles, significantly influences the properties of the inserts.
Composition | Properties | Characteristics |
---|---|---|
Tungsten Carbide (WC) | Hardness, Wear Resistance | Provides the primary cutting ability |
Cobalt (Co) | Toughness, Shock Resistance | Acts as a binder, adding toughness |
Titanium Carbide (TiC) | Chemical Stability, Hardness | Enhances wear resistance and reduces oxidation |
Tantalum Carbide (TaC) | Strength, Hardness | Improves high-temperature performance |
Nickel (Ni) or Molybdenum (Mo) | Corrosion Resistance | Used in special grades for corrosion resistance |
Specifications, Sizes, Shapes, and Standards
Carbide inserts are manufactured in various sizes, shapes, and specifications to cater to different machining needs. These specifications are standardized by organizations such as ISO, ANSI, and DIN to ensure compatibility and quality.
Specification | Available Sizes | Shapes | Standards |
---|---|---|---|
Thickness | 1.5mm – 7.9mm | Square, Diamond, Round | ISO 1832, ANSI B212.4, DIN 4987 |
Length and Width | 6mm – 25mm | Triangle, Rectangle | ISO 5610, ISO 13399 |
Corner Radius | 0.2mm – 2.4mm | Trigon, Parallelogram | Customizable based on application needs |
Coating Types | PVD, CVD, Uncoated | All shapes | ISO 2648, ISO 3735 |
Suppliers and Pricing Details
When it comes to purchasing carbide inserts, it’s essential to consider not just the price but also the reputation of the manufacturer, the quality of the inserts, and the level of customer support provided. Below is a comparison of several well-known carbide insert suppliers, including pricing details.
Supplier | Reputation | Pricing Range (per piece) | Key Products | Customer Support |
---|---|---|---|---|
Sandvik Coromant | High | $8 – $50 | Turning, Milling Inserts | Extensive global support |
Kennametal | High | $10 – $45 | Drilling, Threading Inserts | Dedicated technical support |
Mitsubishi Materials | High | $9 – $40 | Precision Inserts | Comprehensive service network |
Seco Tools | Medium to High | $7 – $35 | Grooving, Parting Inserts | Strong distributor network |
ISCAR | High | $11 – $55 | Heavy-Duty Inserts | Advanced machining solutions |
Kyocera | Medium | $6 – $30 | All-purpose Inserts | Competitive pricing strategy |
Walter Tools | Medium to High | $9 – $42 | Profile Turning Inserts | High-quality technical support |
Sumitomo Electric | Medium to High | $10 – $38 | Wear-resistant Inserts | Industry-specific solutions |
Tungaloy | Medium to High | $8 – $36 | General Machining Inserts | Good after-sales service |
Korloy | Medium | $5 – $28 | Cost-effective Inserts | Growing global presence |
Selecting the Right Carbide Inserts
Choosing the right carbide inserts can be challenging due to the numerous factors that need to be considered. Below is a table that highlights key considerations when selecting carbide inserts for specific applications
.
Consideration | Description |
---|---|
Material to be Machined | Different materials require inserts with specific properties, such as high toughness for steel |
Type of Operation | Milling, turning, and drilling each require different insert shapes and grades |
Surface Finish Requirements | For fine finishes, inserts with a sharp edge and fine grain are preferred |
Tool Life and Durability | Consider inserts with high wear resistance for longer tool life |
Machining Conditions | Inserts should be chosen based on whether the operation is continuous or involves interruptions |
Cost | Balancing cost with performance; sometimes more expensive inserts offer better value due to longevity |
Insert Geometry | The shape and size of the insert affect chip control, heat dissipation, and cutting forces |
Comparing Advantages and Limitations
When comparing carbide inserts with other cutting tools, it’s essential to understand both their advantages and limitations. This section provides a balanced comparison to help you make informed decisions.
Carbide Inserts | Advantages | Limitations |
---|---|---|
Compared to HSS Tools | Longer tool life, higher cutting speeds, better wear resistance | Higher initial cost, more brittle, requires careful handling |
Compared to Ceramic Inserts | Greater toughness, better for interrupted cuts, more versatile in materials | Lower heat resistance, less effective in very high-speed operations |
Compared to Diamond Inserts | More affordable, good for ferrous materials, versatile in applications | Less wear-resistant, not suitable for ultra-precision tasks or non-ferrous materials |
Compared to Coated Inserts | No coating wear-off, consistent performance throughout tool life | Generally lower heat resistance and wear protection compared to coated inserts |
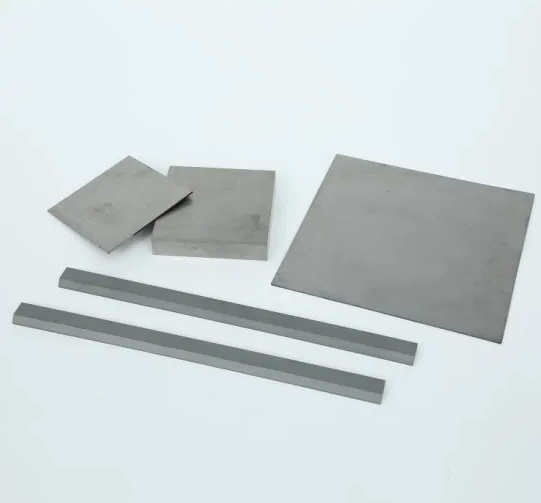
FAQ
Here’s a quick Q&A section to address common questions about carbide inserts:
Question | Answer |
---|---|
What are carbide inserts used for? | Carbide inserts are used for cutting, shaping, and finishing materials in various machining operations. |
Why choose carbide inserts over HSS? | Carbide inserts offer longer tool life, higher cutting speeds, and better wear resistance. |
How are carbide inserts made? | They are made by sintering tungsten carbide powder with a metallic binder like cobalt. |
Can carbide inserts be reused? | While they can be re-sharpened in some cases, it’s generally more cost-effective to replace them. |
What materials can carbide inserts cut? | They can cut a wide range of materials, including steel, cast iron, non-ferrous metals, and plastics. |
How do I choose the right insert? | Consider the material, operation type, surface finish, tool life, and machining conditions. |
Are coated carbide inserts better? | Coated inserts often provide better heat resistance and wear protection, but uncoated inserts can be better for specific applications. |
Conclusion
In conclusion, carbide inserts are a vital component in modern machining, offering unmatched hardness, durability, and precision. When selecting carbide inserts, it’s crucial to consider the specific needs of your operation, including the material being machined, the type of machining operation, and the desired finish. By understanding the different types of carbide inserts and their applications, you can make informed decisions that enhance the efficiency and effectiveness of your machining processes. Whether you’re an industry professional or just starting out, this guide provides the detailed insights needed to navigate the complex world of carbide inserts.
In a competitive marketplace, choosing the right manufacturer and understanding the properties, specifications, and applications of carbide inserts can make a significant difference in the quality and efficiency of your work. With the information provided in this comprehensive guide, you’re well-equipped to make informed decisions and achieve optimal results in your machining operations.